Nylon injection molding is a technique commonly used to manufacture parts for different industries. Therefore, the distinguishing features of different nylons, the factors affecting the choice of material, and the consideration of injection molding process with nylon should be understood in detail to receive the best outcomes.
Read more: What is nylon? All about its properties and common uses
1. Types of Nylon for Injection Molding
1.1 Nylon 6
Nylon 6 is one of the most popular nylon injection molding types that is characterized by high levels of hardness, elasticity and wear resistance.
It has a relatively lower melting point when compared to other varieties of nylons, attributes that make it easier to work with in injection molding. Moreover, it also offers itself well in resisting chemicals and has good mechanical properties that are suitable for various applications.
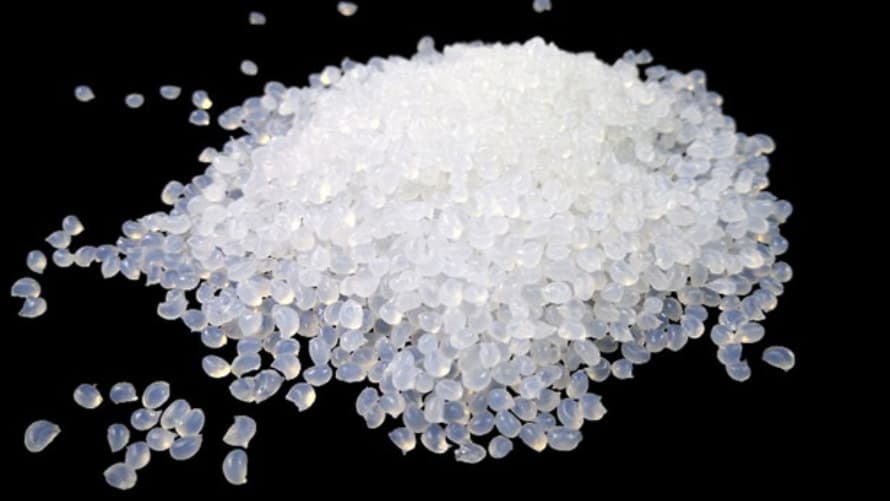
One of the most widely used varieties of nylon injection molding is nylon 6.
1.2 Nylon 66
In nylon injection molding, nylon 66 is characterized by its superior strength, thermal stability, and chemical resistance, making it suitable for high-performance applications. With a higher melting point than nylon 6, it can withstand elevated temperatures and provides better dimensional stability.
This type of nylon is used in example electric connections, automotive and industrial parts and components which have to be strong and flexible.
1.3 Nylon 11
In nylon injection molding, nylon 11 is notable for its toughness and good resistance to both moisture and chemicals. Made from renewable resources, it is a far better prospect than other nylons in terms of being environmentally friendly.
These properties make it ideal for use in diverse industries, especially in functions that require operating in environments with humidity and other forms of moisture.
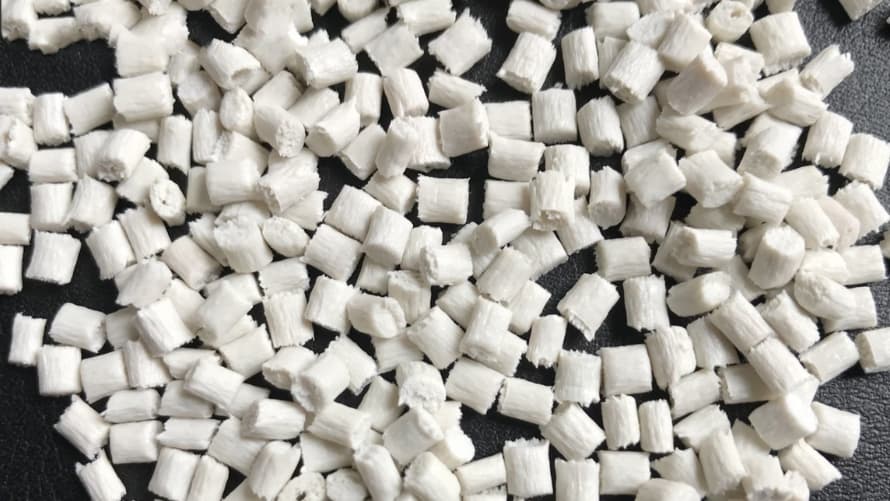
Nylon 11 stands out for its durability and strong resistance in nylon injection molding.
1.4 Nylon 12
Nylon 12 is appreciated in nylon injection molding for low water absorption, flexibility and impact strength. This material has its mechanical properties preserved even in moist environments, making it suitable for applications where moisture resistance is critical.
Nylon 12 is typically utilized in automotive applications such as fuel lines, automotive components, and other industrial applications.
2. Factors to Consider When Choosing the Right Nylon Material
Choosing this nylon material for nylon injection molding entails some very important characteristics that determine its performance, durability, and cost of the final product. Here are the key considerations:
- Mechanical properties: Determine how the tensile strength, impact resistance and flexibility nylon needs for your intended application. Make certain that the material will comprehensively accommodate all the stress it is likely to encounter in its use.
- Environmental resistance: Consider the conditions the product will have to endure, including chemical, moisture, UV and heat or cold. Select a nylon that affords enough protection to these factors so as to have a long and worthy performance.
- Processing conditions: Based on type, nylons have different processing parameters as melting temperature and cooling time. Match your choice in resins well to your injection molding equipment to enhance molding and also minimize defects.
- Cost considerations: Balance performance needs with budget constraints by evaluating both the cost of the material and processing expenses. Aim for a nylon that meets performance requirements without exceeding your budget.
3. Injection Molding Process Considerations for Nylon
When working with nylon in the injection molding process, several key considerations are essential to ensure optimal results and high-quality final products:
- Temperature control: It is important to keep the correct melt temperature for nylon while in use to allow free flow and not reach its degradation temperature. Lower temperatures cause underfilling while high temperatures compromise the mechanical properties of semiconductors.
- Cooling time: Rather than extending the time for cooling until components fully cool, adjust the time according to the thickness and geometry of the part to allow for dimension stability. Lack of cooling also brings in internal stresses and defects on the final product.
- Mold design: Concentrate the concept of mold with some of the specific sub-aspects such as the gates’ location, vents, or part forms. Proper venting helps to exhaust defects as well as the well-positioned gates help in the better filling of the mold.
- Injection speed and pressure: Change the injection speed and pressure to get the right filling of the product to reduce defects. Increasing velocities decreases fill times but may increase shear heating so it must be moderated.
- Material drying: Avoid any chance of moisture on nylon and ensure that you take time and dry it before you process it so that you can avoid the formation of such things as bubbles or splay. To get almost all possible moisture out, a desiccant dryer is used and helps get the pore moisture content level right.
- Quality control: Quality control can also be extended by controlling important factors like temperature or cycle times. Increased inspection of finish parts controls for adherence to specifications and performance requirements.
4. Applications of Nylon Injection Molding
4.1. Automotive Components
Nylon has a significant application in the automotive industry where it is used to produce lightweight parts which are tough.
Some of the nylon injection molding applications may include fuel tanks that need chemical endurance and sturdiness, connectors that have to be electrically insulated by nylon, and inside trims and panels that need both mechanical strength and elegance.
Moreover, the high heat resistance of nylon enables the application of under-the-cover parts so as to improve the efficiency and performance of vehicles in general.
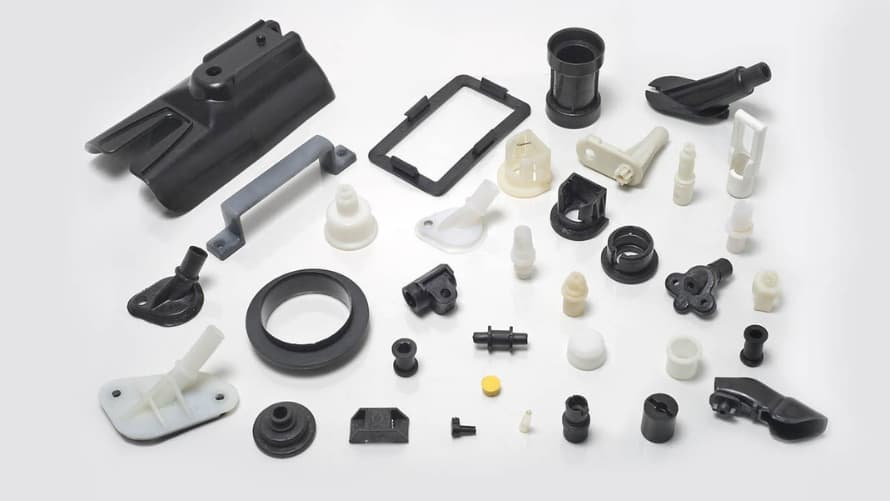
Nylon injection molding finds its applications in automotive parts.
4.2. Consumer Goods
In the consumer goods sector, nylon injection molding gives a broad range of products we use in our day to day lives.
For instance, spatula and measuring cups both employ nylon’s thermal stability in that they will not degrade with frequent use in the kitchen.
Some of clothes that use nylon include sporting activities apparels, protective gear and sporting equipment, this is because nylon materials provide lightness combined with strength, which, when used in sporting gear and equipment, will not only provide the strength that is needed but also without the extra bulk commonly seen in other material types.
4.3. Industrial Equipment
Nylon plays an important role in various industrial applications particularly where high strength and abrasion resistance are desired for the component.
Materials used in gears made from nylon injection molding are smooth to operate and hence self-lubricating with long working durations due to their wear resistance. Nylon bearings and rollers eliminate friction hence making it possible for the manufacturing companies to design most of their machinery to use them.
Furthermore, the shock and vibration-absorbing properties of nylon are appropriate for applications in conveyors, mechanics and automated equipment, increasing the dependability of the mechanisms.
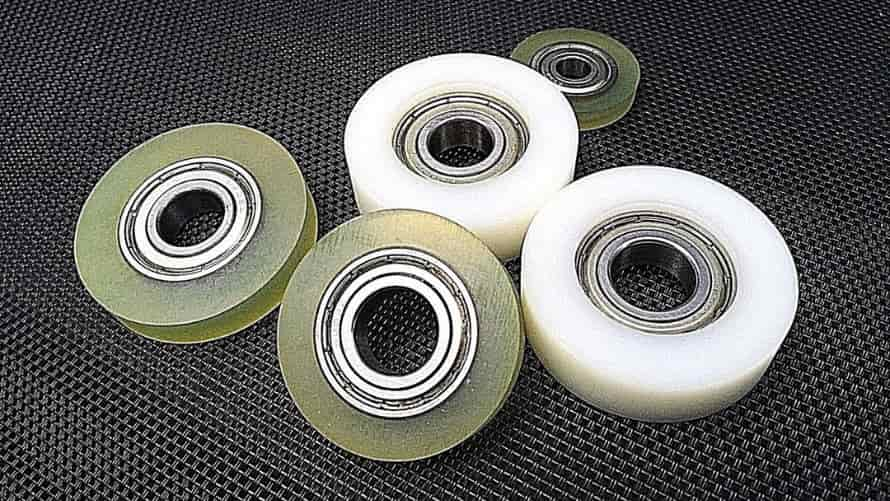
Nylon injection molding is used in bearings and rollers.
4.4. Electrical and Electronics
The electrical and electronics industries benefit significantly from nylon injection molding’s insulating properties and resistance to heat and chemicals.
Nylon is commonly used in the production of connectors, housings, and circuit boards where electrical insulation is critical. Its durability ensures that components can withstand environmental stresses, such as moisture and temperature fluctuations.
Furthermore, nylon’s lightweight nature aids in reducing the overall weight of electronic devices, making it a preferred choice for portable electronics, telecommunications equipment, and automotive electrical systems.
4.5. Medical Devices
Nylon’s biocompatibility and stabilizability make it an ideal choice for various medical applications. It is commonly used in manufacturing syringes, where precision and hygiene are essential.
Surgical instruments made from nylon injection molding offer a combination of strength and flexibility, ensuring they can perform effectively during procedures. Additionally, nylon is used in drug delivery systems, catheters, and implantable devices.
5. Conclusion
Choosing the right nylon material and considerations for the injection molding process is vital for the application's success. By understanding the various types of nylon, the factors influencing material selection, and the specific considerations for injection molding, you can ensure high-quality, cost-effective results with nylon injection molding.
6. About EuroPlas’ PA Products
EuroPlas is a leading manufacturer and distributor of high-quality plastic products, specializing in PA materials such as nylon.
High-quality PA products at EuroPlas are designed to meet the diverse needs of various industries. Our commitment to innovation and excellence ensures that we provide materials that not only meet but exceed industry standards. Here our PA Products:
Contact us now for more support!