PLA (Polylactic Acid) is a biodegradable thermoplastic polymer generated from renewable resources such as tapioca root, cornstarch, and sugarcane. Because of its simplicity of processing, minimal environmental effect, and versatility, it is well-liked in several industries.
Understanding PLA plastic melting point helps manufacturers decide if it's the right material for their products and what conditions they should follow to ensure a smooth manufacturing process.
This article will cover all you need to know about the topic. Follow along!
1. Overview Of PLA Plastic
Let's learn about this material before discussing the PLA plastic melting point!
PLA, or Polylactic Acid, is a brittle, high-strength plastic that can be used for many applications, including food packaging, prototyping, and medical components. It is environmentally beneficial since it's produced under regulated circumstances from fermented plant starch. Although PLA is biodegradable, composting calls for certain conditions. It breaks down into carbon dioxide, lactic acid, and water and needs to be kept at 60°C and 90% humidity for several weeks.
Read more: How Is PLA Plastic Made?
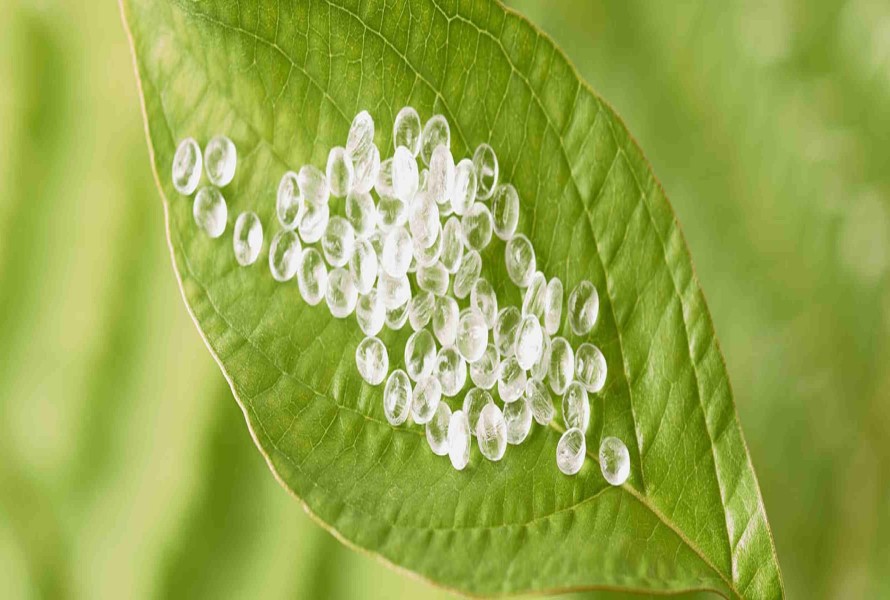
In more detail, lactic acid is created by fermenting plant materials under controlled conditions to provide repeating monomers, the chemical formula for polylactic acid. After the lactic acid oligomers are dehydrated and thermally broken down, they undergo ring-opening polymerization with the aid of a catalyst to form the lactide dimer.
PLA is created by 2 widely used synthesis methods: condensation polymerization and ring-opening polymerization. Ring-opening polymerization is the favored method for producing PLA since it can make a lower molecular weight version as well as a greater molecular weight PLA.
2. What Is The PLA's Melting Point? How does It influence products?
PLA plastic melting point is around 175°C. When reaching this point, the material's form changes from solid to liquid, allowing PLA to be extruded through the nozzle of a 3D printer.
Its intermolecular connections don't break when it melts, giving it a fluid-like consistency. PLA is heated in the hot end's "melt zone" during 3D printing to become molten and ready to be extruded and deposited onto the build plate.
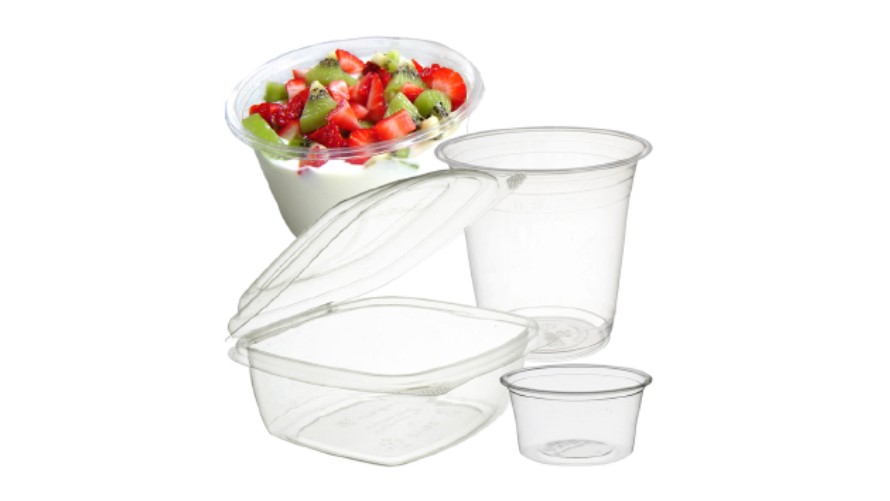
However, the PLA plastic melting point may differ significantly according to the properties of the PLA filament composition you're using. For example:
- The purity of PLA has a major impact on its melting point; a lower purity yields a more constant and predictable melting temperature, which is ideal for precision printing applications.
- PLA comes in two varieties: semi-crystalline and amorphous. The former has a distinct melting point and well-organized polymer chains. Amorphous PLA is easier to print and has a wider melting range than semi-crystalline PLA because of its more randomly placed chains.
- In PLA, the term "molecular weight" describes the length of the polymer chains: the greater the molecular weights, the higher the melting temperatures. Longer chains are more resilient and appropriate for demanding applications since changing from a solid to a liquid state requires more energy.
- Additives are added to PLA to change its melting point and enhance its qualities. Plasticizers can raise or decrease flexibility. Colorants, such as dyes and pigments can somewhat change the melting point. PLA's heat characteristics may also be altered by fillers and reinforcements like metal particles, wood, or carbon fiber material.
Properly processing according to the PLA plastic melting point affects many production aspects.
- Manufacturing temperature: The melting point identifies the temperature range for PLA processing in 3D printing or injection molding. The surface smoothness and layer adhesion depend heavily on efficient temperature control.
For example, for long-lasting prints with low delamination risk, melted plastic layers must adhere to one another (layer adhesion). This strong bond is ensured by proper temperature settings, including cooling, print, and bed temperatures. Low temperature can affect the layer adhesion and overall quality of the products.
Plus, the PLA plastic melting point can affect the 3D printing process. High printing temperatures can cause oozing and stringing, while low printing temperatures may lead to nozzle clogs.
- Thermal stability: The PLA plastic melting point is not really ideal for high-temperature applications. For example, if automotive components or kitchenware from PLA are not designed properly, wrapping or deformation may occur.
- Material compatibility: When mixing PLA with other materials, such as in multi-material prints or support structures, it is important to understand its melting temperature. It will help to guarantee effective printing and eliminate problems like warping or poor layer adhesion, improving the quality of the finished products.
- Biodegradability: The thermal characteristics of PLA affect how rapidly it degrades in comparison to other plastics since it has a lower melting point when composted.
3. Applications Of PLA Plastic
The PLA plastic melting point makes it suitable for different applications, including:
- Containers and packaging: PLA is food-safe; thus, food containers, drinking cups, bottles, trays, and bags made from PLA are commonly seen.
- Healthcare and medical equipment: Due to its biocompatibility and biodegradability, the material has been used in the industry for more than 10 years. Common applications include bioabsorbable medical implants, covering membranes, and scaffolds for tissue engineering.
- Textile products: PLA offers low moisture absorption and good resistance to UV light, allowing it to be suitable for shirts, sportswear, bedding, mattresses, and carpets.
- 3D printing: The material is used to produce film for 3D printing.
Automotive, electrical, and electronics applications: Though PLA material is new for these industries, the material has enhanced tensile strength and impact capabilities and is suitable for front panels, door trim, pillar coverings, floor mats, and ceiling materials.
Read more: Applications Of PLA Plastic In Human Life
4. Conclusion
The PLA plastic melting point plays an important role in designing and producing products. Understanding this issue helps manufacturers make a proper decision, design effectively, and create suitable and durable products.
5. About EuroPlas
As a specialist in the masterbatch sector, EuroPlas is aware of the need for biodegradable plastic for environmental protection and sustainable growth. Therefore, we've developed Bioplastic Compounds and Bio Fillers with many advantages.
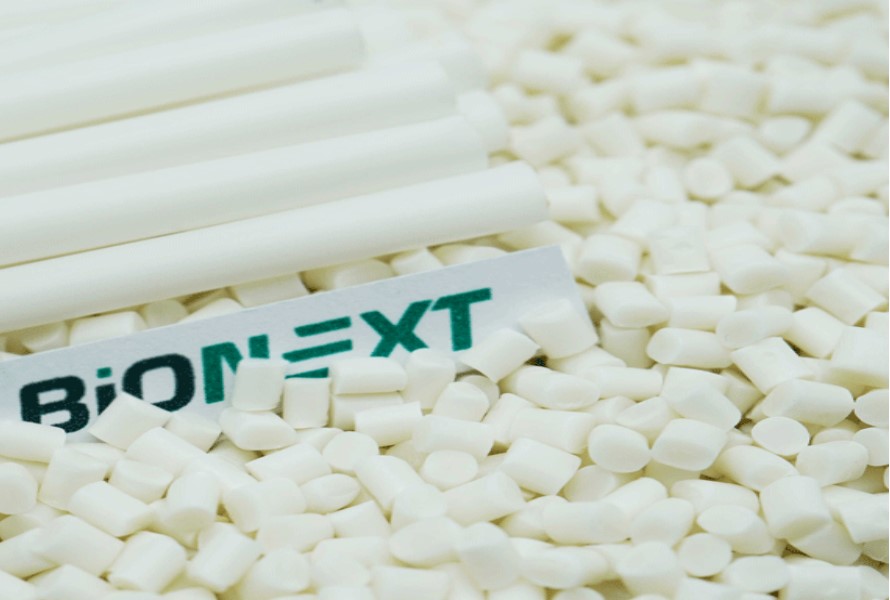
BioNEXT is a bio compound that can break down within a year after use. Our products have several exceptional characteristics and are beneficial to the environment. We've successfully navigated rigorous quality control management to fulfill every prerequisite.
On the other hand, Bio Filler from EuroPlas is an affordable material option. It's a biodegradable substance that enhances several final product properties, including gloss and rigidity. In blown film, it can function as an anti-block and sliding agent.
Contact EuroPlas for more information.