Polyoxymethylene vs. Nylon: Which plastic should you choose?
Polyoxymethylene and nylon are often used in important industrial fields. They both have their own unique characteristics as well as complement each other. For example, polyoxymethylene is resistant to cracking, stretching, abrasion resistance, high hardness and self-lubrication. Meanwhile, nylon is not easily broken, has softness and stable temperature resistance. Currently, thermoplastics such as polyoxymethylene and nylon are used in many key industries such as: Consumer goods, 3D printing, packaging, automobiles, electrical equipment or sports, etc. In the article below, EuroPlas will analyze in detail the characteristics, applications, advantages & disadvantages as well as the differences between polyoxymethylene and nylon. Check it out now!
1. What is Polyoxymethylene?
Polyoxymethylene (POM), also known as acetal or polyacetal. Although they are classified as thermoplastics, polyoxymethylene products have very high requirements for low friction, high hardness and stable dimensions. Compared with other engineering thermoplastics, POM has superior mechanical properties, resulting in sustainable product performance and high practicality.
The outstanding features of polyoxymethylene (POM) are the durability and hardness in both the molecular structure and physical properties of the product. In particular, when the material is at low temperatures of about -40 degrees Celsius, these two characteristics are still maintained stably for a long time. Because the crystal content in the chemical structure of POM is quite high, they shape the color of the material to opaque white.
In addition, the density of polyoxymethylene ranges from 1.410 to 1.420 g/cm3. Thanks to the (CH2O)n structure, polyoxymethylene (POM) is not only hard but also has the ability to withstand temperatures of 175 degrees Celsius. This is one of the earliest thermoplastics discovered in 1953 by German chemist Hermann Staudinger. EuroPlas has introduced to customers basic information about polyoxymethylene thermoplastic.
-l%C3%A0-v%E1%BA%ADt-li%E1%BB%87u-nh%E1%BB%B1a-k%E1%BB%B9-thu%E1%BA%ADt-c%C3%B3-%C4%91%E1%BB%99-b%E1%BB%81n-c%E1%BB%A9ng-cao-(1).jpg)
Polyoxymethylene (POM) is an engineering plastic material with high rigidity and strength.
2. What is Nylon?
Nylon is the general name for synthetic polymers including polyamides. These repeating polymer patterns are formed by linking amide bonds. The chemical structure of Nylon is (C6H11NO)n.
Like polyoxymethylene, nylon is classified as a thermoplastic and is produced from petroleum combined with a melting process to form into many different shapes. Nylon plastic has two common forms: rigid or fibrous.
This nylon polymer can be used as a substrate to combine with different additives to obtain a variety of textures and properties to suit the specific requirements of the product. There are 5 common types of nylon including nylon 6,6, nylon 6, nylon 5 10, nylon 4,6 and nylon 1,6. All of them possess different levels of strength, elasticity, gloss, resilience and impact resistance.
In general, EuroPlas has sent customers the basic information & properties of two materials: polyoxymethylene and nylon. In the next part, EuroPlas will compare the characteristics of these two thermoplastic materials.
.jpg)
Nylon is classified as a popular thermoplastic with a reasonable price.
3. Comparison of characteristics of Polyoxymethylene and Nylon plastics
Polyoxymethylene plastic is assessed by experts and manufacturers to possess more impressive characteristics than Nylon plastic. If both materials are placed in a humid environment, polyoxymethylene will perform better than nylon because they have the ability to limit moisture absorption as well as surface hardness and a more durable physical structure than nylon.
Moreover, nylon has the ability to absorb moisture. However, this can be considered a weakness of this material when compared to polyoxymethylene because it will directly affect the durability and hardness of nylon. Meanwhile, POM shows impressive self-lubrication ability, so the material has the ability to reduce friction and wear.
However, those basic properties will directly affect the price of POM materials on the market. On the contrary, nylon is one of the popular materials as well as applied in industries that directly serve life such as: Household goods, packaging, ... so the price will be considered to be absolutely minimized. In particular, the cost factor will affect the entire cash flow of the manufacturing enterprise from input material costs, production costs, storage and transportation costs.
In terms of temperature resistance, nylon plastic can withstand about 85 - 90 degrees Celsius for a long time and nearly 190 degrees Celsius for a short time. Meanwhile, the short-term and long-term temperature resistance index of POM plastic is 140 degrees Celsius and 100 degrees Celsius, respectively. Therefore, polyoxymethylene plastic has higher technical requirements for production because units focus largely on the melting point over a long period of time. This is also the factor that has contributed to increasing the cost of POM materials.
.jpeg)
POM has higher stiffness and less moisture absorption than Nylon
Moreover, the hardness and durability of polyoxymethylene are also better than conventional nylon lines because the specific gravity in the molecular structure density of polyoxymethylene is heavier than that of nylon (1.41 g/cm3 > 1.15 g/cm3). However, this characteristic of the two material lines is not too different and manufacturers can adjust it through plastic additives. In general, polyoxymethylene and nylon are both used in products with high durability requirements. In particular, nylon will be superior to polyoxymethylene in terms of tensile strength and elongation at break. If polyoxymethylene can only withstand a tensile strength of 70N/mm2 and not exceed 40% of the elongation coefficient at break, nylon can withstand up to 82.7 MPa of force with an elongation coefficient at break of about 50%. Therefore, nylon is more suitable than polyoxymethylene in the fashion, fabric and packaging industries.
Although polyoxymethylene is more highly regarded than nylon, both have their own distinct advantages. EuroPlas will discuss them in the next section.
4. Advantages of each type of plastic
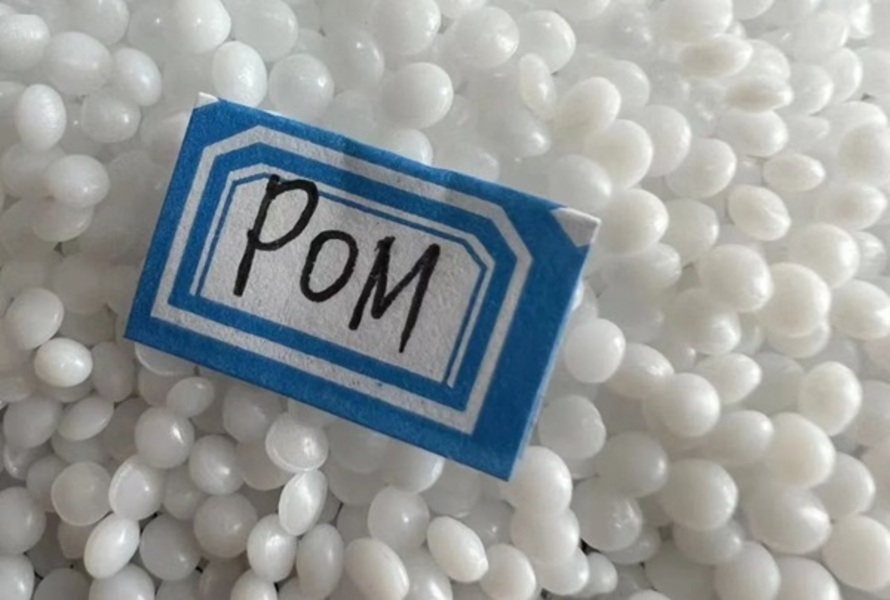
The stiffness of POM is determined by the molecular weight.
Both polyoxymethylene and nylon are considered high-quality engineering plastics. Therefore, their advantages are fully utilized in a variety of key economic sectors. Specifically as follows:
Polyoxymethylene plastic |
Nylon |
- Low coefficient of friction: The coefficient is only about 0.32 combined with self-lubrication ability, helping polyoxymethylene plastic products have a longer life cycle and more durable quality. Therefore, they are used to produce gears, automobile engines, sliding bearings, etc.
|
- Flexural strength: Nylon has much higher flexibility in shape and ductility than polyoxymethylene plastic because this material has a flexural strength of 45 - 90 MPa. Therefore, nylon is widely used in the fields of fashion, fabric, and packaging
|
- Chemical resistance: Polyoxymethylene plastic is not only easily combined with different types of plastic and plastic additives to enhance basic properties, but also resists the effects of solvents and strong chemicals to ensure product durability in natural conditions. Therefore, POM is an ideal material for industries that are exposed to many chemicals such as medicine, biotechnology, etc.
|
- UV resistance: This is one of the characteristics that makes nylon popular in life applications. Each type of nylon will have different UV resistance, for example: Nylon 6 or Nylon 12 is more resistant to UV radiation than Nylon 6,6.
|
- Elasticity: The molecular structure of POM has a mechanism of operation like a spring. They will absorb external impact force and quickly react to restore to their original state without affecting the shape of the product. This factor combined with the durability and hardness of the surface further enhances the quality of polyoxymethylene plastic
|
- Chemical compatibility: Like polyoxymethylene, most nylons are not compatible with acids and ozone. In addition, nylon is compatible with strong alcohols, some types of alcohol, gasoline, oil and fuel. In addition, nylon resins such as PA6, PA66 can be combined well with plastic additives to improve product properties.
|
- Temperature stability: If the temperature fluctuates from -50°C to 120°C, polyoxymethylene plastic is still capable of maintaining its physical and mechanical properties. Thermal stability will help polyoxymethylene work well in a variety of different conditions without affecting the quality of the product. Thanks to that, POM is suitable for parts exposed to different temperatures, such as car engine parts, hot water valves and other high temperature applications that require stable performance.
|
- Durability: Although the durability of nylon cannot be compared with polyoxymethylene, the estimated density of about 1.14g/cm3 also helps nylon possess a certain firmness. Therefore, they are often used to produce gears, machine parts, machine parts or industrial machine parts.
|
- Low water absorption: This advantage helps polyoxymethylene plastic maintain a durable and hard surface state. Besides, they also keep the mechanical properties and dimensional state stable for a long time. Therefore, polyoxymethylene plastic is often used to make water pipes in large factory systems to ensure safety.
|
|
.jpg)
Nylon has high tensile strength and flexibility in terms of product shape change.
5. Applications of polyoxymethylene and nylon
The properties of polyoxymethylene and nylon are both beneficial, such as high hardness, low friction, dimensional stability and good chemical resistance. Thanks to their flexibility and advantages, both materials are fully utilized in many different fields. Some common applications, specifically as follows:
-
Automotive industry: Polyoxymethylene has a fairly low coefficient of friction and is suitable for the production of gears and sliding bearings in automobile engines to ensure safety during fast and strong operation. Meanwhile, nylon is also used to produce screws, bolts, and bearings in machine systems because they have high heat resistance and tensile strength.
-
Health & medical: Both polyoxymethylene and nylon can resist strong chemical groups such as acids, solvents, and bacteria. Therefore, they are used to produce surgical sutures, catheters, and medical fabrics. In addition, the biocompatibility of both materials is also highly appreciated by experts, so they will not affect the health of consumers.
.jpg)
polyoxymethylene is used in many fields
-
Consumer goods: Nylon is almost one of the most popular materials for daily fast-moving consumer products. Specifically, they are used to produce packaging and nylon bags. Because of their heat resistance, UV resistance and chemical resistance, they fully meet the standards for use in daily food preservation activities. In addition, polyoxymethylene has a low friction index, high hardness, and reusability. Therefore, they are used to produce zippers, locks, handles, buttons, lanyards and toys.
-
Sports field: With impact resistance and elasticity, polyoxymethylene and nylon are used to produce ski bindings, bow parts, gears, bicycle spokes. In addition, both materials are also used to make camping equipment such as tents and ropes for outdoor recreational activities.
-
Industrial equipment & machinery: Thanks to its durable mechanical properties, low coefficient of friction and wear resistance, polyoxymethylene plastic is used to manufacture gears, bearings, conveyor system components, valve parts and mechanical parts. These are parts that require high technical requirements as well as stability under high pressure during long-term operation of heavy industrial machinery.
-
Electronic equipment & components: Polyoxymethylene and nylon plastics both have the ability to eliminate resistive currents, so they are ideal materials for the production of electrical cables, connectors, switches, sockets, strong breakers, connectors, switches, relay housings. In particular, polyoxymethylene plastics will be more dominant in this field because of their very high resistance to heat.
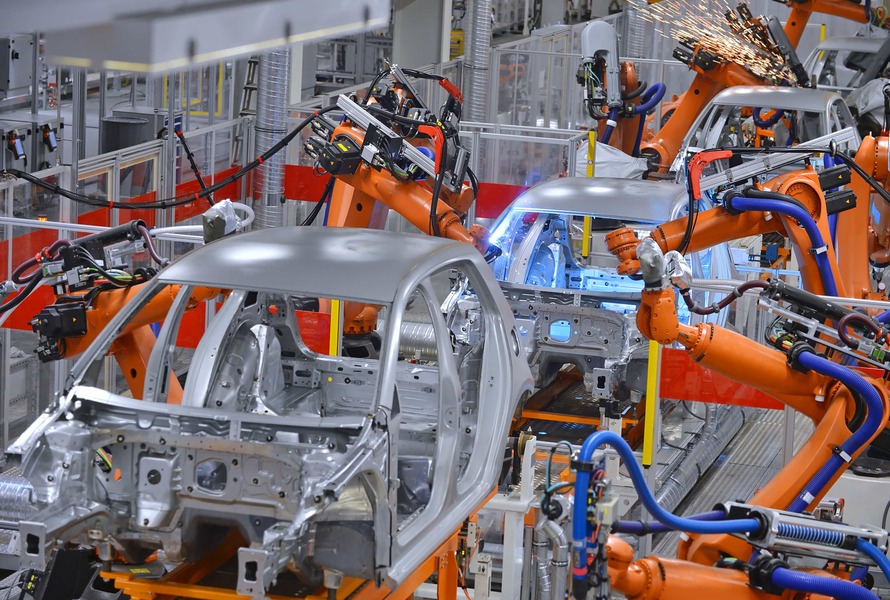
Nylon is used in the automotive industry.
-
Fashion: Nylon is more commonly used than polyoxymethylene in the fashion industry because of its flexibility, UV resistance, moisture resistance, and chemical resistance. In addition, nylon can also adapt well to each specific condition of the surrounding environment, providing the best experience for consumers.
Most essential fields have the presence of polyoxymethylene and nylon. Therefore, it will be really difficult if customers hesitate between choosing polyoxymethylene or nylon. In the next part, EuroPlas will answer that question in the next part. Refer now!
6. Polyoxymethylene and nylon, which material should you choose?
Overall, both materials have outstanding advantages, so manufacturers need to consider carefully before choosing. EuroPlas recommends that you consider the business sector, production costs and products of the enterprise to decide on the source of input materials.
If your business is small and operating in the field of regular consumer goods, nylon plastic is the right choice. On the other hand, for businesses that produce high-quality household appliances with technical requirements to meet export needs, polyoxymethylene plastics have a certain position in the market.
Not only that, both types of materials have outstanding advantages and properties such as: Stable moisture resistance, insulation, low coefficient of friction, high durability & hardness, strong chemical resistance, easy processing and combination with other groups of materials or additives. In addition to deciding on the right source of raw materials, customers also need to find reputable suppliers to ensure product quality as well as save costs for large-scale production.
That is the reason why EuroPlas is always proud to be one of the leading filler masterbatch manufacturers in the Vietnamese market.
7. Introduction to EuroPlas
Currently, EuroPlas owns 7 factories with a scale of tens of hectares in 6 economic regions of Vietnam and 1 factory in the Egyptian market. In particular, the enterprise has been and is a comprehensive strategic partner of many plastic manufacturing companies and corporations in more than 95 different countries. Therefore, the EuroPlas team is confident in meeting about 0.8 million tons / year, always having a full source of goods available for partners.
In terms of nylon materials, EuroPlas currently provides 2 product lines: PA6 and PA66 compound mixtures. This is a nylon material combined with glass fiber to further enhance the rigidity of the material structure. With a glass fiber content of up to 65%, almost all the weaknesses in the durability and rigidity of nylon materials at EuroPlas are resolved. Not only improving the impact resistance and material life, the combination of nylon and glass fiber of EuroPlas helps the material increase its ability to resist UV rays, moisture as well as heat for a long time. These changes are aimed at narrowing the comparison gap between conventional nylon plastic and polyoxymethylene in practice.
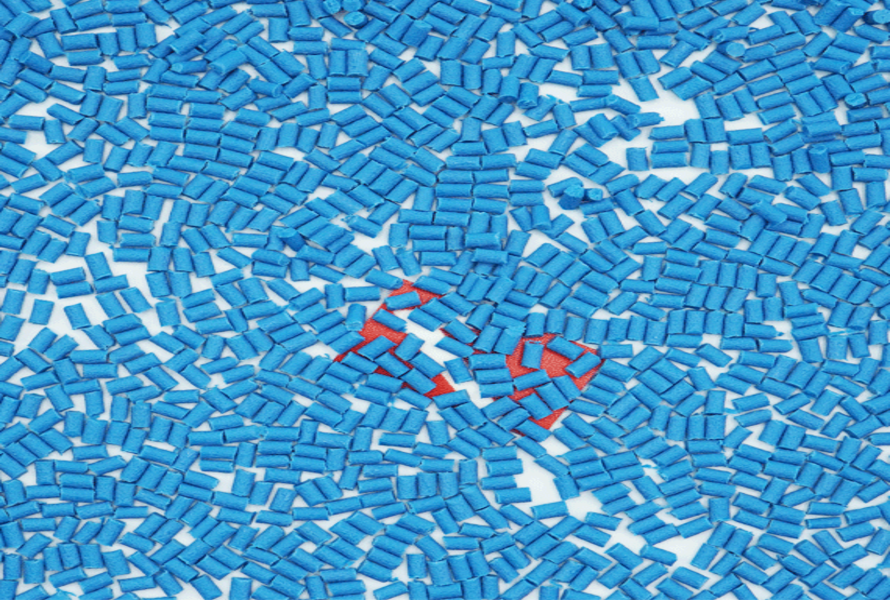
EuroPlas PA66 and PA6 nylon resin compound
EuroPlas has introduced detailed information about the characteristics, applications, advantages, and disadvantages of polyoxymethylene and nylon plastic in practice. We also help customers solve the question of choosing between polyoxymethylene and nylon in each specific field. In addition, EuroPlas is also proud to introduce to the market standard plastic materials such as: PA66 and PA6. Please continue to accompany EuroPlas to learn more....