Polypropylene vs. nylon: A comprehensive comparison and suggestions
The debate of polypropylene vs. nylon is often a hot topic among manufacturers and designs regarding choosing which is suitable for final products. Both materials are common thermoplastics used for industrial and household applications.
They share some similarities, yet the key differences make one can be used for a particular appliance but not others. Let’s dig into the topic of nylon vs. pp right below!
1. What is polypropylene?
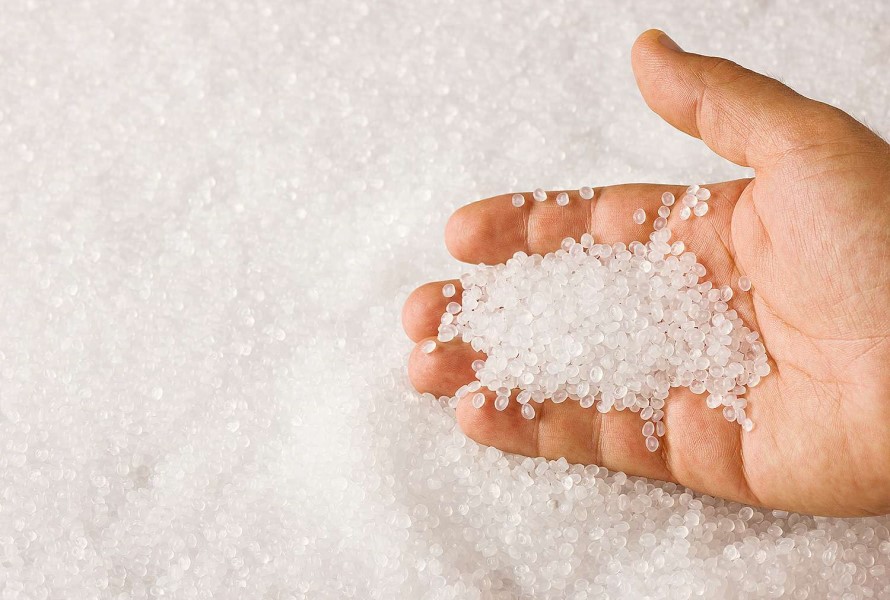
Polypropylene
Polypropylene, a mixture of propylene monomers, or other names polypropene or PP, is a polyolefin or saturated polymer with the chemical formula (C3H6)n. It’s usually opaque or turns translucent or colored by applying pigments.
This low-density thermoplastic has many outstanding features, such as toughness, elasticity, fatigue resistance, heat resistance, chemical resistance, and electrical insulation. It also possesses dual functionality: plastic and fiber. Thus, the material is commonly used in many fields.
2. What is nylon?
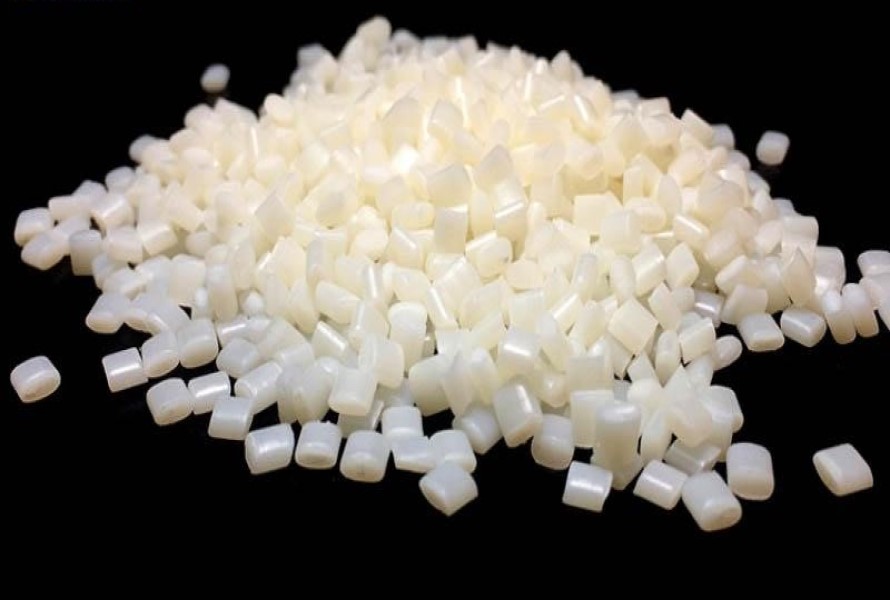
Nylon
Nylon is a particular synthetic polyamide thermoplastic made from the reaction of a diamine and a dicarboxylic acid. There are 4 main grades of polyamide nylon: 66, 11, 12, and 46, deriving from the lengths of the polymeric chains.
The material can look shiny, semi-shiny, or dull. This synthetic polymer is highly machinable. It tolerates numerous chemicals, abrasion, fungi, and insects, withstands significant elongation, and can reduce noise. Its applications include gloves, guitar strings, wheels, electric connectors, medical devices, etc.
Read more: What is nylon? All about its properties and common uses
3. Polypropylene vs. nylon: A comprehensive comparison
3.1 Polypropylene vs. nylon - Properties
Property |
Polypropylene |
Nylon |
Tensile Strength |
25-40 MPa |
50-90 MPa |
Surface Hardness |
92 HRR (Rockwell R) |
100 - 120 (Rockwell R) |
Operating Temperature |
<180 °F |
-70 to 250 °F |
Melting Temperature |
327 °F |
374 - 460 °F |
Impact Tolerance |
High impact resistance |
High impact resistance (10 times more than ABS) |
Chemical Resistance |
Great chemical resistance - able to tolerate diluted bases and acids |
Good chemical resistance - including resistance to oils, gasoline, fuels, mineral spirits, and some alcohols. |
Water Absorption |
Almost water resistance. It absorbs only 0.01% of its weight in water after a 24-hour soaking |
0.30 - 7.0% by weight |
Recyclability |
Yes. It takes 20-30 years for PP to biodegrade. |
Yes. Nylon is not biodegradable. |
3.2 Polypropylene vs. nylon - Applications
Thanks to its water and solvent resistance, PP is widely used in producing automotive batteries and semiconductor components. Plus, since the material is elastic and durable, people utilize it in plating, chemical tanks, and laboratory settings.
Though polypropylene is less flexible than nylon, it can be bent without cracking, making it an ideal choice for hinges, gears, and other moving parts. Besides, PP’s light and chemical and UV light-resistant properties allow it to be the popular choice for plastic components (such as lightweight buckles) and outdoor applications.
In general, nylon is more durable and abrasion resistant than PP; thus, manufacturers like to use it for products that require high tensile strength levels and buckles that require good wear and tear tolerance.
Nylon appliances
Moreover, as a good insulator, nylon is used to insulate electrical cables and as an alternative to aluminum in engine parts. Because the material is malleable, allowing it to be reheated and remolded, it’s a great option for design prototyping. In addition, the low friction coefficient of nylon is super suitable for some parts such as wheels, rollers, and seals.
We can use injection molding to manufacture parts from these two materials. However, the process with polypropylene may be simpler as the raw PP pellets have a lower melt viscosity than nylon ones. Since nylon (especially nylon 12) possesses strong heat resistance, it’s useful in injection molding and additive manufacturing.
There are types of polypropylene and nylon that are certified in FDA-compliant grades. So, both can be used in the medical and food and beverage industries.
3.3 Polypropylene vs. nylon - Our suggestions
As mentioned above, both materials have their own advantages, making them the favorable choices in different cases. Depending on the requirements of the final products, the unique properties and benefits of one material may fit better than that of the other.
Plus, you should consider the cost of the two materials. In general, PP is cheaper than nylon. So if you prefer a more cost-effective option, go for polypropylene. It’s a good choice for products without many strength requirements or for outdoor applications. Meanwhile, although nylon is more expensive, if your products require higher strength and better durability, stretch our budget a little more for the option of nylon.
4. Introduction of EuroPlas polypropylene engineering plastic compound
Polypropylene engineering plastic compound from EuroPlas is a time-saving and cost-efficient method as the company provides you with a full-function-in-one-material solution for your final products. Polypropylene is combined with other additives and reinforcements to optimize its special properties.
PP compound
Here is the list of our best Polypropylene engineering plastic compounds:
It’s a combination of PP resin, glass fiber, and other specific additives, increasing its flexural modulus and tensile strength. Therefore, it provides additional strength to automobile applications, electric appliances, and furniture. EuroPlas PP glass fiber compound comes with different densities of glass fiber, such as ECP PP 10GF (10% GF), ECP PP 20GF (20% GF), ECP PP 30GF (30% GF), ECP PP 40GF (40% GF), and ECP PP 50GF (50% GF).
With this compound, polypropylene is mixed with glass beads and other additives, making it more compressive resistant and thermally stable and improving the mechanical stress under load. Besides, since the compound can deliver more stiffness and transparent shaping, it’s an ideal choice in home interiors, home appliances, and car interiors.
PP conductive compound, a perfect combination of PP resin and carbon black conductive, is another highlighted product from EuroPlas. The material is lightweight and machinable with the injection molding process. Thus, it’s applied in many applications, such as cable jackets, electrical equipment housing, and electronic components.
EuroPlas PP flame retardant compound consists of PP resin and halogen/non-halogen flame retardant, creating a material with good flame resistance and high performance. The products have different levels of UL94-standard flame retardants: 5VA, 5VB, V0, V1, V2. PP flame retardant compound is widely used in supplies, including insulation, roofing, and flooring. It’s also a popular option in the electrical and electronic sectors to produce circuit boards, cables, and plastic coverings for appliances.
The compound combines PP resin with BaSO4 and suitable additives, lending the material the ability to reduce shrinkage and deformation in high-temperature settings and resist heat, chemicals, and impact. EuroPlas PP BaSO4 compound is suitable for producing sanitary equipment, house appliances, or water filter equipment.
EuroPlas produces PP talc compound based on the PP resin talc powder and appropriate additives. The material has better stiffness, flexural modulus, and strength. Plus, it lessens the tendency to be creep in increasing temperature environments and improves heat distortion temperature and dimensional stability. Thus, it’s ideal for products with the requirements of good durability and high heat resistance (120-130oC) for a long time.
5. Conclusion
We hope our article about polypropylene vs. nylon will help you understand more about these two popular materials in the manufacturing industry. Once again, each has its own unique properties and advantages to be applied in specific applications than others. So, thoroughly consider the final product’s requirements and decide which material to choose.