PP vs. PE Plastic: Which One To Choose?
1. Introduction
PP (polypropylene) and PE (polyethylene) are two of the most common types of plastic globally. Even though they both come from petroleum, their characteristics and uses differ. Different types of plastic have distinct properties. By choosing the right for your needs, you can ensure that your product or packaging is safe, performs as expected, cost-effective, and has a minimal environmental impact.
This article is your one-stop shop for all things PE vs. PP plastic. Learn right now!
2. Understand the basis of PP vs PE Plastic
2.1. Properties of PP vs PE plastic
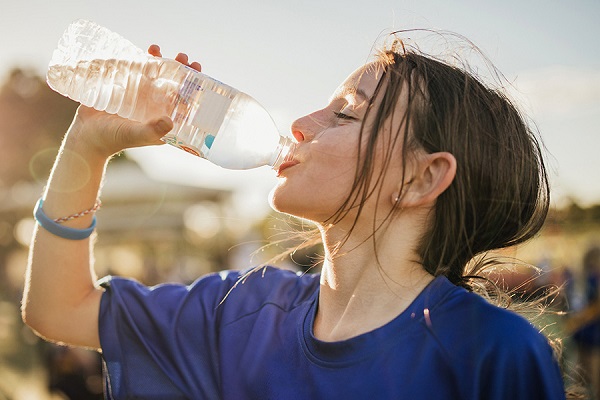
PP water bottle is a general choice because they are durable, reusable, and BPA-free.
The properties of PP and PE depend on their chemical structure.
PP is a semi-crystalline polymer, meaning that it has a more ordered structure than PE. This shows PP better strength and durability. On the other hand, PE is a fully amorphous polymer, indicating that it has a less ordered structure. By this, PE is more flexible and easier to process.
Imagine a pile of gum. If you chew it for a long time, it will become soft and pliable, like PE. But if you leave it out to dry and harden, it will become brittle and break easily, like PP.
Some key factors to differentiate polypropylene (PP) and polyethylene (PE):
- Molecular weight: Polymers with higher molecular weights tend to be more sturdier and durable.
- Crystallinity: Semi-crystalline polymers, such as PP, have a more ordered structure than amorphous polymers, such as PE. This makes semi-crystalline polymers stronger and more durable than amorphous polymers.
- Branching: Branched polymers are more flexible and process with ease than linear polymers.
- Molecular orientation: Oriented polymers have their molecules aligned in a specific direction, which gives them better strength and stiffness.
These factors can be optimized during the manufacturing process of PP and PE with the desired properties. For example, PP can be blended with other polymers, such as PE, to improve its flexibility and processability. PE can be cross-linked to improve its strength and durability.
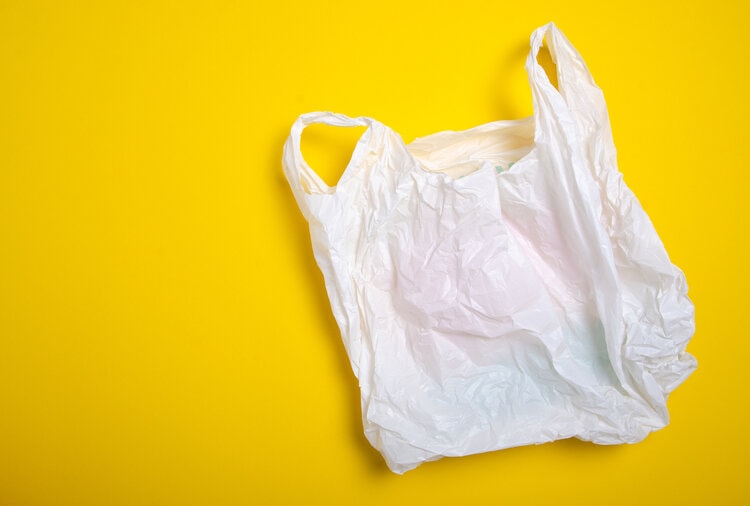
PE grocery bags are lightweight and inexpensive but not durable as PP bags.
Check out more technical property details at:
PE plastic: Everything you need to know
PP Plastic: Everything you need to know
2.2. Applications of PP vs PE plastic
PP is often used for strength and durability, while PE is for flexibility and ease of processing.
Food packaging: PE and PP are both food-safe and can preserve freshness. PE is often used for flexible packaging, while PP is for rigid packaging.
Medical devices: PE and PP are both sterile and biocompatible. PE is often used for disposable devices, while PP is best for reusable devices.
Automotive parts: PP is strong, durable, lightweight, and resistant to chemicals and corrosion. Automotive manufacturers use it for components, including bumpers, dashboards, and interior trim.
Construction materials: PE and PP are both durable and resistant to weathering. PE is often used for pipes and tubing, while PP is for roofing shingles and other exterior building materials.
Consumer goods: PE and PP are widely used in consumer goods, such as toys, furniture, and household products.
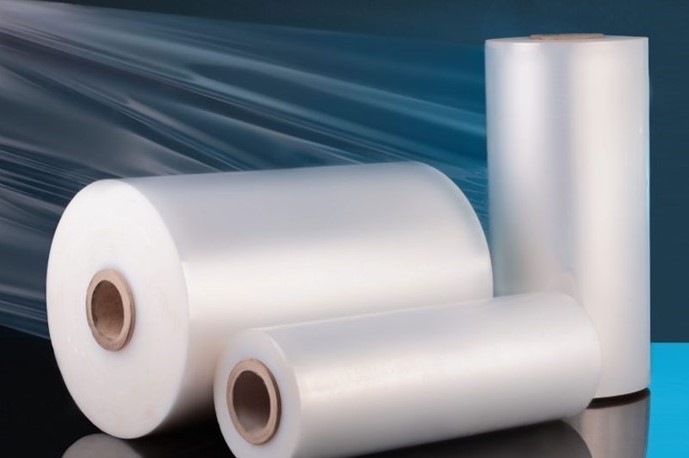
PE stretch film is used to wrap and protect products during shipping and storage
Products made from PE:
- Flexible packaging: Plastic bags, wraps, pouches, and liners
- Bottles and containers: Milk jugs, water bottles, detergent bottles, and food storage containers
- Toys and sporting goods: Balls, frisbees, sleds
- Electrical insulation: Wires and cables, electrical tape
- Other products: Pipes, tubing, films, and nets
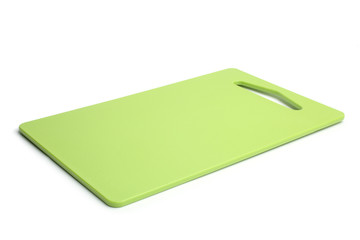
PP cutting boards are non-porous and easy to clean, making them a good choice for food preparation
Products made from PP:
- Food packaging: Yogurt cups, margarine tubs, and other food containers
- Medical devices: Syringes, surgical implants
- Automotive parts: Bumpers, dashboards, and other car parts
- Construction materials: Pipes, roofing shingles
- Consumer goods: Toys, furniture, household products
2.3. Advantages and disadvantages of PP vs PE material
Advantages of PP:
- Sturdy and durable: PP is one of the excellent and most durable materials. It is resistant to tearing, impact, and abrasion.
- Lightweight: PP is a lightweight plastic, which makes it ideal for applications where weight is a concern.
- Resistant to heat, chemicals, and moisture: PP is resistant to various chemicals, solvents, and damp. It is also heat-resistant, making it suitable for high-temperature applications.
- Food-safe and biocompatible: PP is a food-safe and biocompatible material, saying that it is non-toxic and does not irritate the skin or body tissues.
- Easy to process and recycle: PP is easy to process and recycle, making it a sustainable choice for many applications.
Disadvantages of PP:
- Not flexible: By structure, PP is not as flexible as PE, which is difficult to use in some applications.
- Can be susceptible to UV degradation: PP is receptive to UV degradation, which can cause it to become brittle and break over time.
- Difficult to bond to other materials: This limits its use in some applications.
Advantages of PE:
- Flexible and easy-to-process: PE is an easy-to-process material. You can mold it into various shapes and sizes.
- Waterproof and resistant to chemicals: PE is waterproof and resistant to chemicals. It is also non-toxic and odorless.
- Lightweight and inexpensive: This property makes it ideal for many applications.
- Food-safe and biocompatible: PE is a food-safe and biocompatible material, indicating that it is non-toxic and does not irritate the skin or body tissues.
Disadvantages of PE:
- Not as strong and durable as PP: PE is not as strong and durable as PP. It is more susceptible to tearing, impact, and abrasion.
- Can be susceptible to UV degradation: PE can be susceptible to UV degradation, which can cause it to become brittle and break over time.
- Not as heat-resistant as PP: PE is not as heat-resistant as PP, which limits its use in high-temperature applications.
- Hard-to-recycle: PE can be difficult to recycle, which makes it less sustainable than PP.
2.4. Choosing between PP vs PE plastic
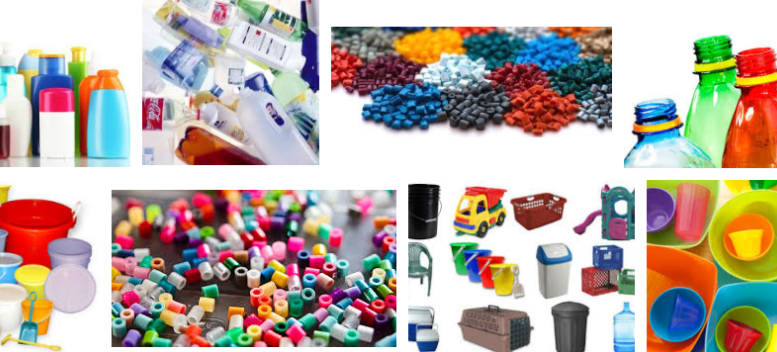
PP and PE plastic are used to make a wide variety of products
To choose the right PP or PE plastic for your needs, you should consider many factors, including:
Strength and durability: PP is partially stronger and more durable than PE. Food packaging, medical devices, and automotive parts will be the best using PP.
Flexibility: PE is more flexible than PP. Its flexibility makes it ideal for applications such as bags and wraps, bottles and containers, and toys and sporting goods.
Heat resistance: PP and PE have similar heat resistance. However, PP is slightly more heat-resistant than PE.
Chemical resistance: PP and PE have similar chemical resistance. However, PP is slightly more resistant to some chemicals than PE. This makes a good choice for applications where chemical resistance is vital, such as food packaging and medical devices.
Cost: PE is generally less expensive than PP, explained by the simple production of PE.
Recyclability: PP and PE are both recyclable. However, PP is more difficult to recycle than PE because of its higher melting point.
Appearance: PP is translucent, while PE can be translucent or opaque. If you want your product to have specified appearance, take this as a necessary factor.
Environmental impact: PP and PE are both petroleum-based plastics. They are not biodegradable and can contribute to environmental pollution. However, PE is generally more environmentally friendly than PP since it's easier to recycle and has a lower melting point.
3. About EuroPlas
PP filler masterbatch, made from calcium carbonate (CaCO3), polypropylene (PP) resin, and other additives, is a cost-effective and productive solution for the plastics industry.
EuroPlas commits to supplying versatile and customizable PP filler masterbatch solutions for improving the quality and performance of PP products in a wide range of applications.
PP resin, glass beads, and additional ingredients are combined to create PP glass bead compound. Due to their spherical form, glass beads have the benefits of transparency, compressive resistance, and good thermal stability.
Strengthening with glass beads can help reduce mechanical stress under load.
By these qualities, this material is frequently utilized in home furnishings, appliances, and automobile interiors
PP base resin, glass fiber, and additional additives are incorporated to produce PP glass fiber compounds. It increases the flexibility and tensile strength of the finished products. Glass fiber-reinforced polypropylene offers greater durability for applications such as furnishings, electric appliances, and automobiles because of its outstanding performance.
The PP glass fiber compounds offered by EuroPlas come in a variety of densities, notably ECP PP 10GF, ECP PP 20GF, ECP PP 30GF, ECP PP 40GF, and ECP PP 50GF.
PE resin, CaCO3, and other substances are incorporated to generate PE filler masterbatch. Manufacturers have a more affordable choice using PE filler masterbatch, which additionally boosts the stiffness, flexibility, and thermal insulation of the result.
With 16 years of experience working with worldwide companies, the No. 1 filler masterbatch manufacturer in the world, EuroPlas, is dedicated to giving its clients the best goods and services, including its premium solutions.
4. Conclusion
Overall, PP is generally a better choice for applications where strength, durability, heat resistance, and chemical resistance are essential. PE would be better for applications when flexibility, cost, and environmental impact are required.
Looking for a wide range of PP and PE plastic products? EuroPlas, with a team of experienced and professional staff, is committed to providing customers with high-quality products and services. Visit our website to learn more.