Non woven fabrics are a category of textile products that are made without using any weaving or knitting processes but through a number of other processes. The steps involved in the manufacture of non woven fabrics are described below.
1. Process of Creating Non Woven Fabrics
Non woven fabrics are special types of fabrics that are manufactured by a number of processes but not through weaving or knitting as the other fabrics are.Depending on the intended application and the required characteristics of the end product, the specific technological processes may differ, although there are several general ones characteristics for non woven fabric production.
Read more: All Kinds Of Plastic Used To Make Nonwoven Fabrics
Read more: Producing nonwoven fabrics with PP filler masterbatch
Here are the steps to create non woven fabric:
Step 1. Processing of fiber (Man-made, natural or recycled)
The initial procedure of producing the non woven fabric is to prepare the fiber material that will be used in the non-woven production process. This involves removal of impurities and desired lengths of the fibers and further homogenization of the fibers.
- Some other man-made fibers include polyester, polypropylene, polyamide and rayon.
- The natural fibers: cotton, wool, silk, and linen are cleaned; Carded and Combed.
- Recycled fibers viewed as textile, plastic or paper scraps are collected, washed again, and separated or alternatively, are repelletized or reduced.
Step 2. Dyeing (If necessary)
If the fabric material used to develop the non woven fabric needs to be dyed then this is done before anything else. These are normally dyed using different dyeing methods in order to get the desired color of the fibers.
Step 3. Opening
The opened fibers are further mixed, either by hand or mechanically, to achieve the desired combination of fibers and corresponding properties.
Step 4. Blending
The opened fibers are then blended, either manually or using mechanical means, to create a homogenous mixture of the desired fiber types and properties.
Step 5. Oiling
The blended fibers are then oiled to enhance their flowability and ease of processing during the manufacturing process. This step is crucial as it helps to make the fibers more workable and less likely to degrade during other processing stages.
Step 6. Laying
The fibers are then laid out into a web or mat using one of three main techniques:
- Dry laying: The fibers are aligned mechanically with the help of air or mechanical means.
- Wet laying: The fibers are in water and then spread on a screen or mesh for drying.
- Spin laying: The fibers are extruded and directly deposited on a collecting substrate.
Step 7. Bonding
The laid web or mat is then bonded together using one of four main techniques:
- Mechanical bonding: The fibers are mechanically bonded by needling or water jet.
- Thermal bonding: Due to the heat and pressure the fibers are bonded at the point where they cross each other.
- Chemical bonding: The fibers themselves are combined with a binder or adhesive with the intention of covering the fibers with it.
- Stitch bonding: This web or mat is sewn with needles and threads.
Step 8. Raw non woven fabric
The bonded non woven fabric has become the unprocessed and unpolished material in the new processing cycle.
Step 9. Finishing
The raw non woven fabric may further be processed through various stages such as cutting, coloring, printing, or coating as the case may be depending on the final desired property and appearance of the final product.
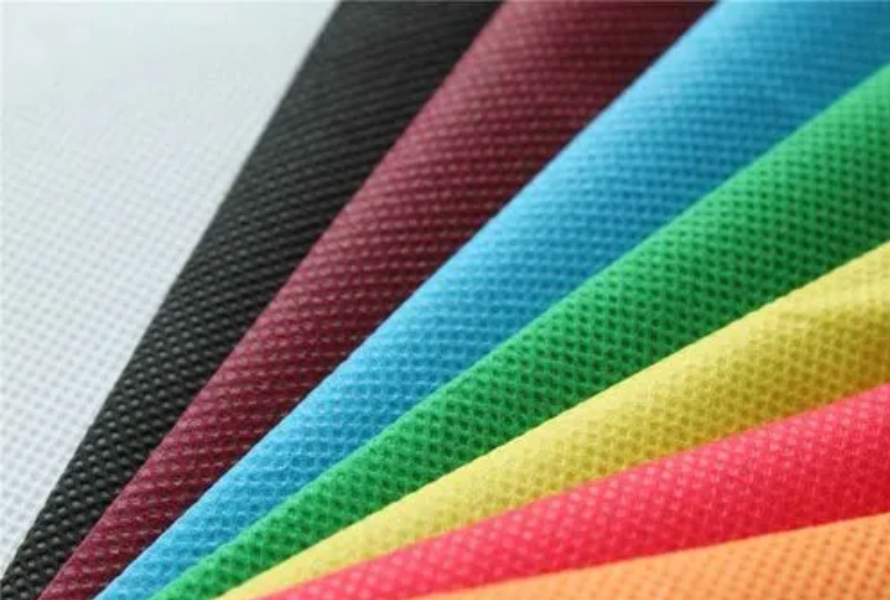
Depending on the final application of the product and its intended use, further processing of the raw non woven fabric may be necessary.
2. The Benefits of Using Non Woven Fabric
Within the last few years demand for non woven fabrics has tremendously increased in various sectors as they overshadow the utilities of woven or knitted fabrics.
Read more: Using nonwovens in packaging is great for your business
2.1. Versatility
In non woven fabrics properties and characteristics can be altered and developed to suit diverse specifications. Based on the materials used in its production as well as the processes of manufacturing as well as finishing techniques, non woven fabrics can be made to have various properties such as high strength, high absorbency, breathability, water repellent, and antimicrobial among others. Due to this flexibility, they can be easily incorporated into a wide spectrum of uses, including cosmetics and industrial filtering.
2.2. Durability
Non woven fabrics can be engineered to have excellent tear and tensile strength and are generally and mechanically stronger than woven or knit fabrics. This is even more important in usage areas where the fabric would be under heavy utilization including car interiors, building and structure materials, or industrial use in filtration.
2.3. Sustainability
Non woven fabrics are known to be innovative fabrics and most of them can be produced from renewable or recycled materials to enhance environmental conservation compared to textiles. Also, the specific processes for non woven fabrics production take less water and energy and produce less waste compared to other varieties of fabric.
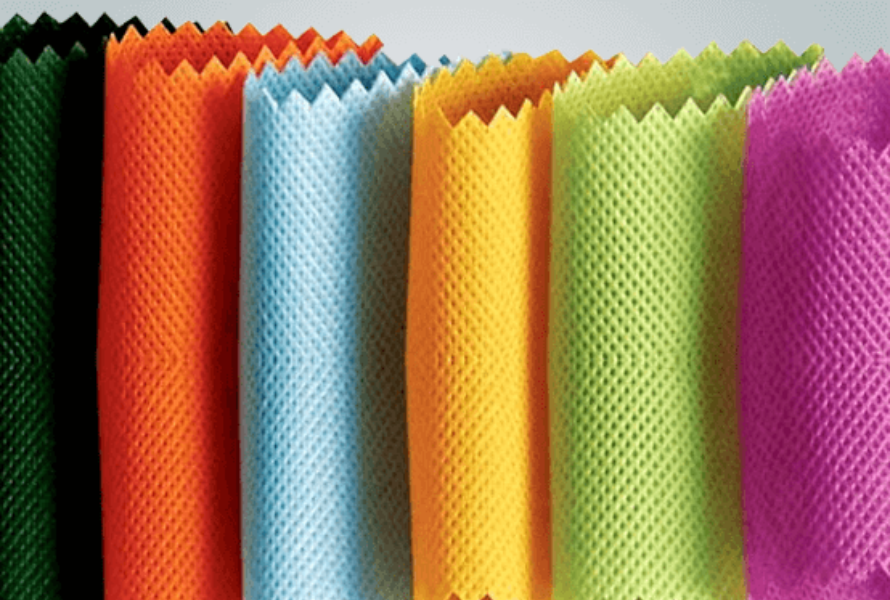
Non woven fabrics are environmentally friendly, which are made from renewable or recycled material.
3. The Importance of Non Woven Fabric in Production
Today, they are the primary material used in production processes of various production IV Non woven fabrics industries. Due to their special characteristics, these engineered textiles are beneficial in many ways which make them important in use.
3.1. Versatility and adaptability
Indeed, one of the reasons why the non woven fabrics are so vital in production is their versatility. These materials can be designed to have specified characteristics that include high strength, absorbency, filtration, and many others. This versatility lets manufacturers utilize the non woven fabrics to fit the precise requirements of its usage in production and the final products.
3.2. Cost effectiveness
The manufacturing of non woven fabrics is less expensive than usual textile trading processes. The integrated processes inherent in manufacturing, conservation of materials, and opportunities for automation lead to lower production costs. This places non woven fabrics as quite a cost-effective and reasonable opportunity for businesses who would want to cut down their material cost without actually having to compromise on quality and durability.
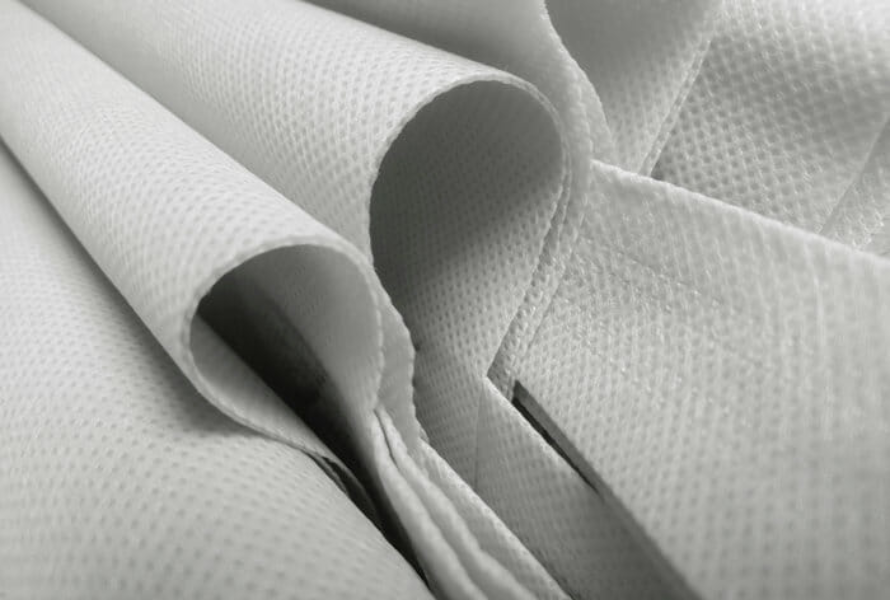
The cost of producing non woven fabrics is lower than that of standard textile trading procedures.
3.3. Improved efficiency
In many cases, non woven fabrics can be incorporated into production processes with relative ease against all other textile materials. Some of the advantages include high surface smoothness, homogeneity of cross-section, fewer blemishes, seamless edges, and fewer recourse to additional processing. These benefits can manifest themselves in the form of a faster product assembly line and a reduced total cost of operations.
3.4. Enhanced product performance
The unique characteristics of non woven fabrics can come in direct contact with the targeted use products to improve their performance and effectiveness. For example, in the automobile industry, non woven materials are used in interiors as sound insulation and thermal insulating properties. For the medical industry, non woven fabric is crucial in forming highly absorbent and permeable wound dressings.
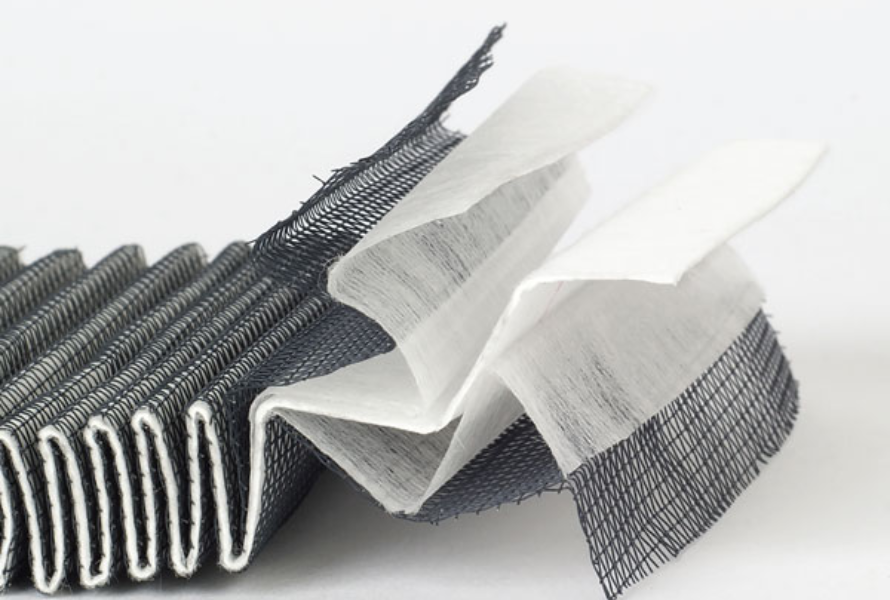
Non woven fabrics can help the applied products improve their performance and effectiveness.
4. Conclusion
To sum up, making non woven fabrics involves the choice and treatment of fibers, bonding techniques, and finishing steps, providing an opportunity to develop a great number of varieties of the long-sellurable fabrics with various characteristics that allow their use in different fields. Also, continuous improvement and the quest for perfectibility in the methods of production make non woven fabrics more important in today’s manufacturing.
5. About EuroPlas
Whether you are in the process of selecting the right plastics that can be used in manufacturing non woven fabrics, you can turn to EuroPlas for the products.
Our polypropylene (PP) material is one of the finest available out there for its quality and its performance as well. Feel free to contact us to get your non woven fabric manufacturing to meet our optimum plastic solutions.