Thermoplastic Elastomer, a material that possesses characteristic properties of thermoplastic and elastomer, is an acronym for TPE. TPE plastic is physically flexible, and extremely easy to process, which are all characteristics of an ideal material in many industries. Here are the details about its ingredients and how it is made.
1. Primary Ingredients to Make TPE Plastic
TPE plastic is an entire group of materials that are useful across many different industries. Normally, to produce TPE plastic, people usually combine the following components in a composition – SEBS, SBS, rubber oil, polypropylene, and zinc stearate. With a suitable formula, TPE plastic produced can be relatively inexpensive with high output.
Read more: All about TPE plastic: Definition, properties & applications
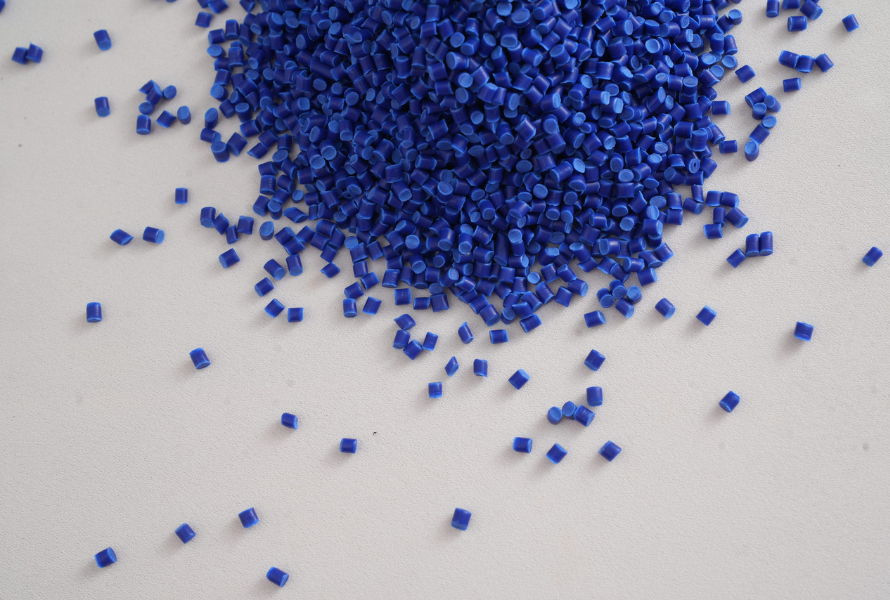
SEBS, SBS, rubber oil, polypropylene, and zinc stearate are the key ingredients to produce TPE plastic.
1.1. SEBS (styrene ethylene butylene styrene)
- SEBS is a thermoplastic elastomer with high mechanical properties, chemical and weathering resistance.
- It can be used as an impact modifier, to give flexibility and also to improve the tensile strength of the TPE plastic.
- The parts range from 10 to 20 of SEBS assist in attaining an average rigidness of the final product.
1.2. SBS (styrene butadiene styrene)
- SBS stands for Styrene Butadiene Styrene; it’s also an elastomeric thermoplastic that makes the TPE plastic more elongated and flexible.
- It gives it some of the inherent elasticity or rubber-like features of the TPE plastic.
- Likewise, the 10-30 parts of SBS are incorporated into the SEBS to enhance the elastomeric characteristics of the thermoplastic system.
1.3. Rubber oil
- 20-30 parts of rubber oil added into TPE plastic, perform the role of plasticizer thereby enhancing the processability and reducing the hardness of the TPE plastic.
- The rubber oil also revives the low-temperature property of the TPE plastic.
1.4. Polypropylene
- Originally, polypropylene with 30-50 parts contributed to the brittleness, hardness, and heat0resisting capacity of the TPE plastic.
- It assists in countering an overly soft nature contributed by the elastomeric parts.
- This also enhances the chemical and weathering characteristics of polypropylene in the total amount of TPE plastic produced.
1.5. Zinc stearate
- The small 0.1-0.3 of zinc stearate added into TPE production process have functions of lubricity and processing aid.
- The other roles of zinc stearate include stopping sticking or fouling of machinery during extrusion or injection molding.
2. TPE Plastic’s Manufacturing Process
The main production processes applicable for TPE plastic include extrusion and injection molding. It has also received progressive developments in 3D printing for product distribution in manufacturing. Meanwhile, compression molding is extremely rare in TPE plastics production.
2.1. Extrusion
Extrusion is acknowledged as one of the most frequently effective processing methods for TPE plastic. Such a process as extrusion provides high or high rates of production and it is used when producing TPE products with similar cross-sections.
The extrusion process involves the following key steps and equipment:
Step 1. Extruder: The main machinery required is an extruder since it is the equipment responsible for melting and mixing the TPE compound and forcing it through the die.
Step 2. Feeding: The TPE compound is in the form of pellets or granules after which they are loaded in the hopper of the extruder.
Step 3. Melting and Mixing: Melting the TPE plastic and blending it to achieve a homogeneous consistency.
Step 4. Die Extrusion: When the TPE plastic is in its molten form and it is uniform, it is forced through the die.
Step 5. Cooling: The extruded product of TPE plastic goes directly to the cooling water tank after coming out from the die. After this, the mixture gets cooled at a very fast pace in order to solidify the overall structure of the TPE.
Step 6. Stretching Zones: the extruded TPE material goes through 3 different stages, which are called stretching zones. These zones provide controlled stress and strain to the TPE plastic; these will align the polymer chain and enhance the mechanical properties of the material.
Step 7. Relaxation Zones: There are two rest zones between each stretching area to allow the muscles to rest and prepare for the next stretching area. These enable the TPE plastic to go through adequate control of stress relief and enhance the stability of the material.
Step 8. Inspection: After the part is manufactured using TPE plastic material, the TPE plastic part is examined to ensure it meets the established specifications and quality.
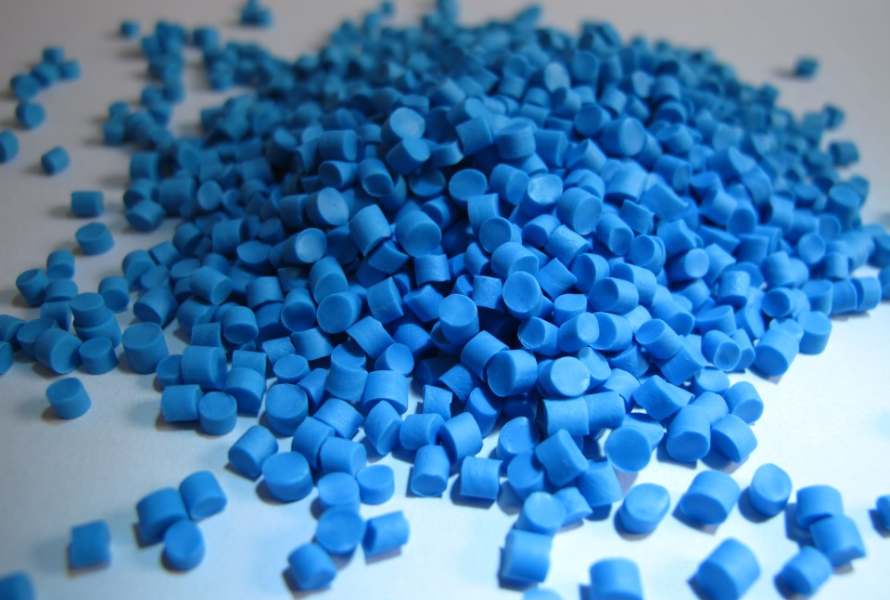
Extrusion is one of the most common processing methods for TPE plastic.
2.2. Injection molding
The second significant process of manufacturing TPE plastic is injection molding. In addition, injection molding is one of the fastest and the least expensive techniques for fabricating TPE plastic.
The injection molding process involves the following steps:
Step 1. Material preparation: TPE plastic pellets or granules are placed into the feed hopper of an injection molding machine.
Step 2. Heating: TPE plastic is put in the barrel of the injection molding machine and has its temperature increased to a level that is above its melting point.
Step 3. Injection: This liquid material, which was once the TPE, is then forced under pressure into the mold.
Step 4. Cooling: The mold is cooled through a core of cooling channels or through an external cooling system. The cooling time depends on the size, shape, the structural design of the part, and the type of molded TPE plastic.
Step 5. Ejection: After TPE plastic has attained a solid state, the mold is opened and the completed part is either ejected or disconnected from the mold.
Step 6. Inspection: After completely manufactured, the TPE plastic part is examined to ensure it meets the established specifications and quality.
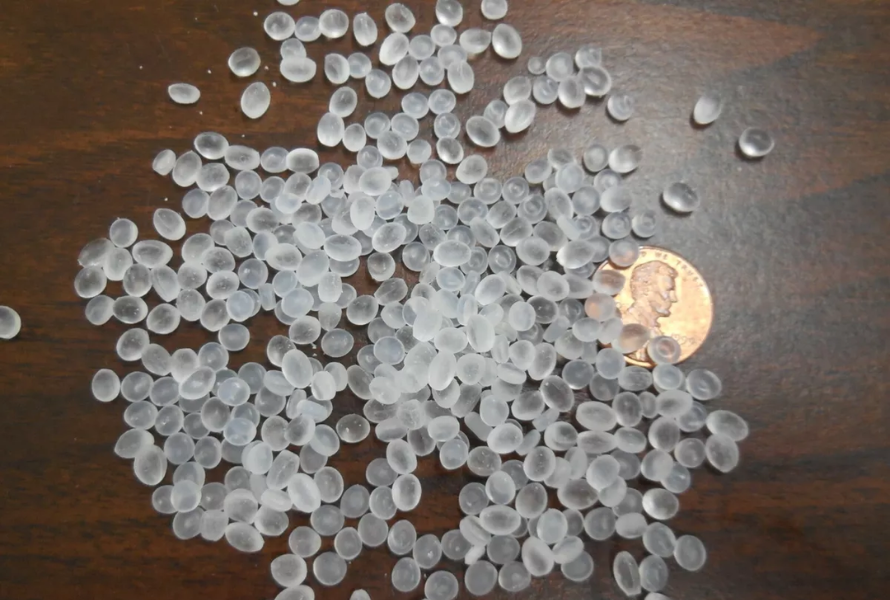
Injection molding is considered as one of the most rapid and least costly methods of creating TPE plastic.
3. Importance of Quality Control on TPE Plastic
Quality control is especially important in the manufacture of TPE plastic, whereby certain qualities have to be met to meet the general standards of the product. Thanks to good quality control, the manufacturers could develop a good reputation, reduce cost failures, and the benefits of which they can improve constantly.
3.1. Consistent performance
It is important that the output be consistent in its quality in TPE plastic production. This is important for TPE plastic that is used in various industries, and therefore their performance requirements are quite important. This is evidenced by systems put in place in order to provide quality assurance of TPE parts and ensure they meet the quality standard and perform in a stable manner. That is why maintaining consistency is of great importance since failure in product deliverables could have expensive consequences and might be risky for the safety of people.
3.2. Regulatory compliance
Food contact, medical, toys, and childcare articles are the most significant markets of TPE, and TPE plastic has to meet various sector-specific standards. It is important to ensure that TPE plastic products meet the provisions on safety, the environment, and labeling before being released into the market. If certain essential standards/requirements are not met then there can be legal challenges, and brand image problems.
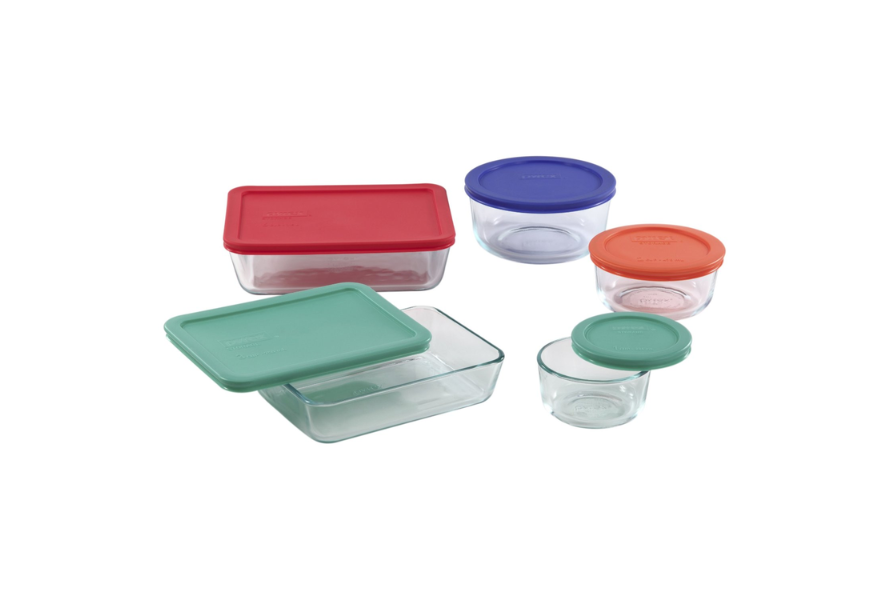
Food contact is the dominating market for TPE plastic and must satisfy several sector-specific requirements.
3.3. Waste reduction and efficiency
Quality control in TPE plastic manufacturing involves examining the material and sometimes manufacturing processes to ensure that all the products produced meet the standard required of them; this way, the company controls the amount of scrap, amount of time spent on rework, among others. This also decreases the number of inspections required in the production after completion as well as other costs associated with customers’ returns in TPE plastics manufacture.
3.4. Customer satisfaction and brand reputation
The customer satisfaction factor hence becomes a priority since the products are produced from TPE plastic of acceptable quality and consistent with the set standards. This quality focus adds value to the brand which puts the product in a better position within the market competition.
4. Conclusion
TPE plastic is generally produced from SEBS, SBS, rubber oil, polypropylene, and zinc stearate. The common methods used in its production are extrusion and injection molding. Therein, injection molding is the one suitable for distributed manufacturing at the lowest cost.
Quality conscious when it comes to manufacturing TPE materials, to get topnotch performance and durability, and not to have a repeat of the accidents that occurred as a result of failure of these materials.
5. About EuroPlas
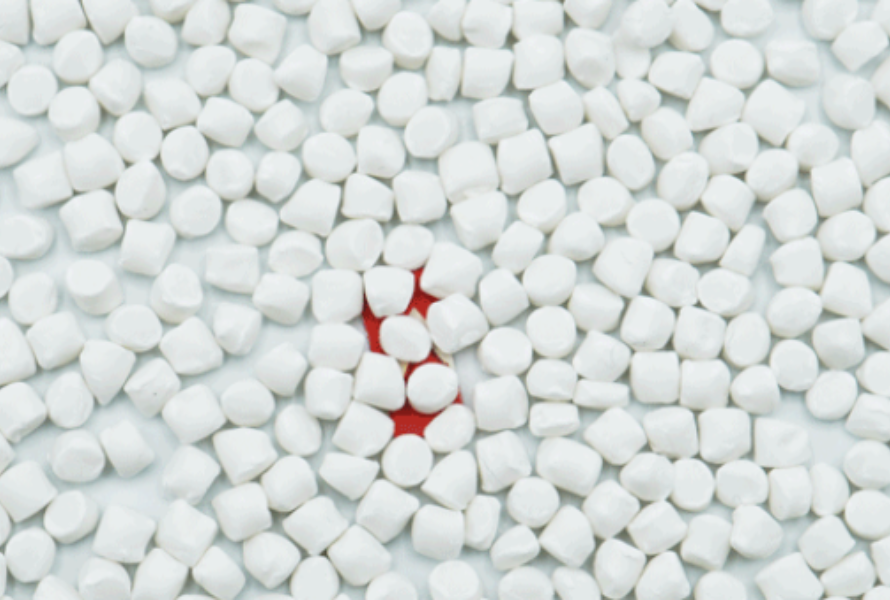
If you are looking for TPE plastic ingredients such as polypropylene, EuroPlas could be a reliable provider. At EuroPlas, we offer a wide range of high-quality PP products, including:
For more information, please contact us right now.