The Trend of Using No. 7 PC Plastic in Modern Medical Products
PC No. 7 plastic has been steadily gaining prominence in the modern medical industry due to its exceptional properties such as high transparency, heat resistance, and mechanical strength. As the healthcare sector continues to advance with cutting-edge technologies, PC No. 7 plastic has become a preferred choice for manufacturing a wide range of medical devices, from simple to complex. This article delves into the trend of using PC No. 7 plastic in the medical field, its outstanding advantages, and its potential for future development.
1. Overview of PC No. 7 plastic
PC No. 7 plastic is a type of transparent, colorless thermoplastic polymer. It is produced through the polymerization of Bisphenol A (BPA) and phosgene, resulting in long polycarbonate chains with superior properties.
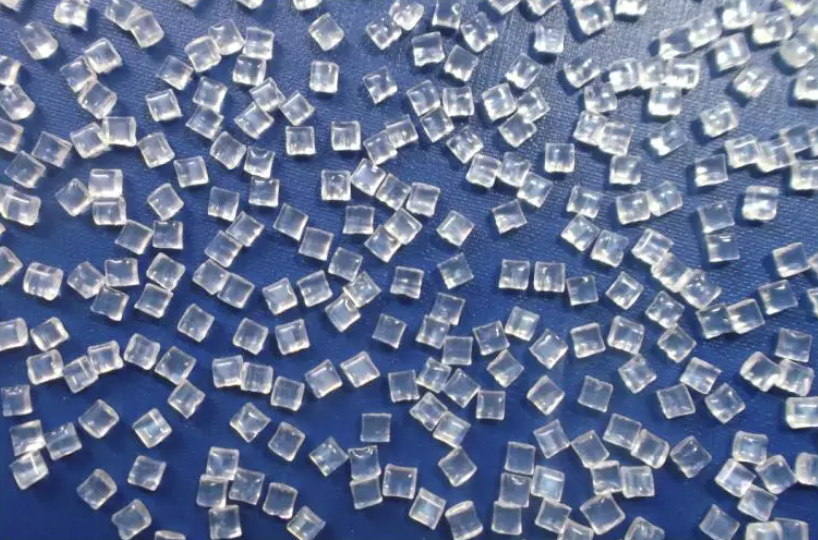
Notably, PC No. 7 plastic boasts a transparency level of up to 90%, exceptional impact resistance, and excellent heat resistance under harsh conditions. Moreover, this material exhibits inherent flame retardancy and high flexibility, facilitating the creation of complex shapes.
To identify PC No. 7 plastic products, consumers can look for the number 7 printed on the bottom, the number 58 (for products containing 58% polycarbonate), or the recycling symbol with a number 7 in the center. These markings help consumers accurately identify the type of plastic they are using.
1.1. Properties
PC No. 7 plastic exhibits exceptional toughness and ductility, enabling it to withstand significant impact forces without deforming. Its high transparency, allowing up to 90% light transmission, makes it an ideal choice for applications requiring visual clarity. Moreover, PC No. 7 plastic possesses outstanding dimensional stability, ensuring the precision and durability of products over extended periods.
PC No. 7 plastic's excellent thermal properties include a high heat deflection temperature, ensuring its dimensional stability even at elevated temperatures. Its broad processing window, ranging from a glass transition temperature of 145-150°C to a heat distortion temperature of 155°C, facilitates various manufacturing processes.
1.2. Advantages and Disadvantages
PC No. 7 plastic offers numerous advantages, such as high impact strength, heat resistance, and chemical resistance. These properties make it suitable for a wide range of applications, including automotive components, electrical equipment, and medical devices. Its transparency and dimensional stability also contribute to its popularity in the optical industry.
However, PC No. 7 plastic also has some drawbacks. Its surface is prone to scratches, requiring additional protective measures. Additionally, its compatibility with other polymers is limited, which can pose challenges in composite materials. Furthermore, the manufacturing process can be more expensive compared to other types of plastics. If not produced under strict quality control, PC No. 7 plastic may contain BPA, a substance that can pose health risks.
2. Why is Polycarbonate Widely Used in the Medical Industry?
PC plastic has become an indispensable material in the modern medical industry due to its exceptional properties. Firstly, PC offers exceptional transparency, comparable to glass, enabling healthcare professionals to easily observe procedures and monitor patient conditions.
Moreover, PCs can withstand temperatures up to 135°C without deformation, meeting the rigorous sterilization requirements of the medical field.
Another significant advantage of a PC is its superior mechanical strength, with impact resistance 250 times that of ordinary glass. This ensures utmost safety in hospital environments, especially during emergencies. Additionally, PC possesses inherent antibacterial properties and strong antioxidant capabilities, preventing the growth of bacteria and protecting medical equipment from environmental damage.
Furthermore, PC exhibits excellent biocompatibility, causing no adverse reactions with the human body or medical solutions. This characteristic makes PC an ideal choice for medical devices that come into direct contact with patients, such as breathing tubes, oxygen masks, and infusion devices.
3. Trends in Using PC plastic in Modern Medical Products
With the escalating global healthcare crisis, especially during the COVID-19 pandemic, the demand for PC plastic in medical applications has surged. PC plastic has found widespread use in the production of various medical devices, including ventilators, infusion pumps, test tubes, and diagnostic imaging equipment. Its exceptional properties, such as transparency, durability, and chemical resistance, make it an ideal material for these applications.

The trend of using PC plastic in the medical sector is further driven by its potential for customization and sterilization. Advanced manufacturing techniques allow for the creation of highly precise PC components, meeting the stringent requirements of medical devices. Moreover, PC plastic can be easily sterilized, ensuring the safety of medical procedures.
In the field of surgery, PC plastic is increasingly used in the production of endoscopic instruments, vital sign monitoring devices, and temporary implants. This trend is expected to accelerate in the coming years, particularly with the advancements in 3D printing and smart manufacturing.
4. The Future of Polycarbonate plastic in the Medical Industry
The future of PC plastic in the medical industry appears promising. Researchers are actively developing new PC formulations with enhanced antimicrobial properties and durability.
In the realm of personalized medicine, PC plastic is being explored for 3D printing applications to create customized implants and medical devices. This technology is particularly beneficial for reconstructive and orthopedic surgeries where precision and biocompatibility are paramount.
The growing trend of smart medical devices presents new opportunities for PC plastic. In the next five to ten years, PCs are expected to be integrated with biosensors and microelectronics to create intelligent health monitoring devices capable of real-time data collection and analysis.
Furthermore, research is focused on developing biodegradable PC plastic to address environmental concerns related to medical waste. Such advancements could usher in a new era of sustainable medical applications, balancing efficacy with environmental friendliness.
5. Conclusion
PC plastic has become a cornerstone of the medical industry thanks to its outstanding properties. As PC manufacturing technology advances and the demand for advanced medical equipment rises, the use of PC is set to expand further. Nevertheless, more research is required to understand its environmental impact and develop efficient recycling solutions to ensure its sustainable use. With its exceptional qualities, PC plastic is destined to remain a vital component in the production of medical devices for years to come.
6. About EuroPlas PC compound products
With extensive experience in the industry, EuroPlas has established itself as a leading manufacturer of filler masterbatches in Vietnam. Leveraging its deep industry knowledge, EuroPlas has developed two specialized PC compound product lines to cater to a wide range of applications.
EuroPlas' PC-GF compound is an exceptional blend of polycarbonate plastic (PC) and glass fibers, resulting in a material with superior properties:
- Excellent impact resistance and dimensional stability
- Enhanced mechanical properties
- Improved flexural strength
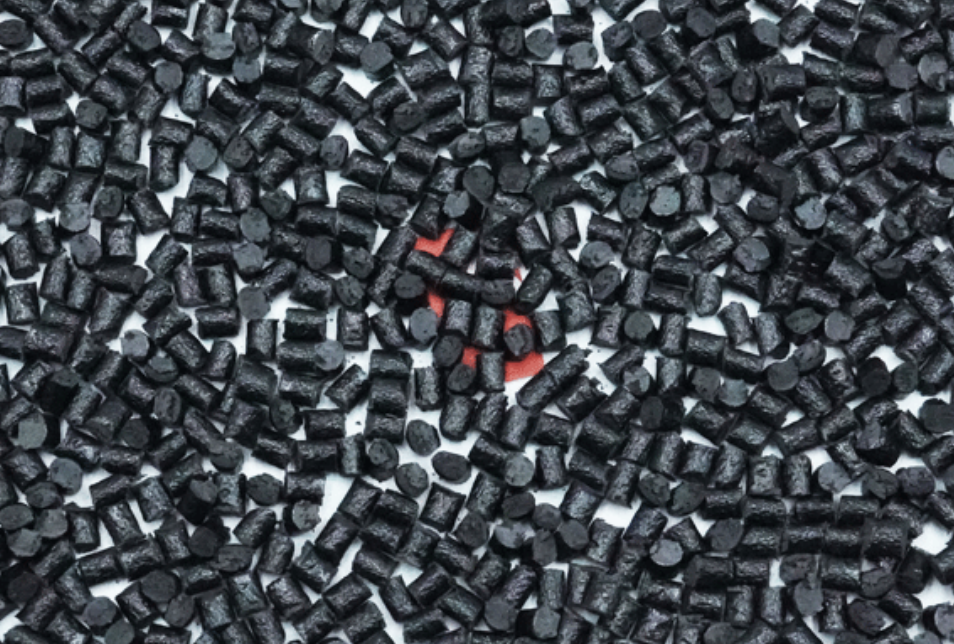
EuroPlas also introduces PC-FR, an advanced version of PC plastic that is specially formulated with enhanced flame retardancy. This product:
- Meets UL94 V-0, V-1, or V-2 ratings
- Maintains high transparency
- Offers excellent electrical insulation
- Effectively limits flame spread
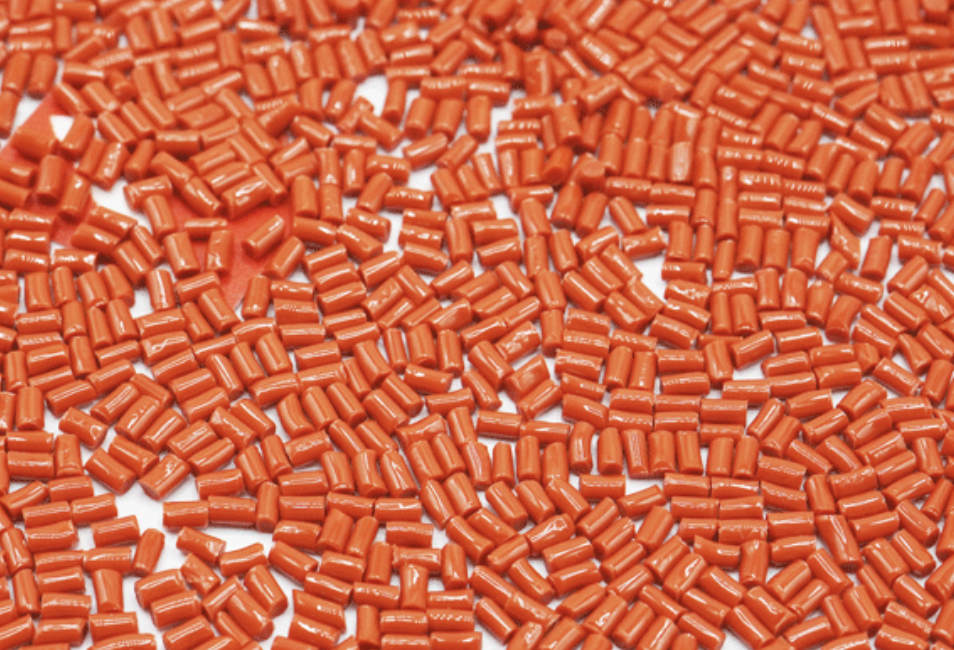
6.3. Outstanding Advantages
EuroPlas has successfully developed various PC plastic products with exceptional advantages, including:
- All-in-one material: Combining multiple properties in a single material.
- Simplified manufacturing process: Eliminating the need for additional blending.
- Customizable design: Tailored to specific customer requirements.
- Optimal durability and performance: Delivering superior performance.
6.4. Storage and Handling
To ensure the best quality of EuroPlas PC compounds, the following guidelines are recommended:
- Storage: Store in a cool, dry place.
- Transportation: Transport by land or sea as per agreement.
EuroPlas PC compounds are widely used in various industries. For detailed advice on PC compounds and the most suitable solution for your business, please contact our experts for prompt and accurate support.