In the world of plastics, thermoplastic and thermosetting plastic are the two most important categories, defining material properties, processability, and application scope. Choosing the right one not only affects product quality and durability but also has a direct impact on cost and production efficiency.
According to Grand View Research (2024), the global thermoplastic market is projected to grow at a 7.4% CAGR, reaching USD 40 billion by 2030—a clear sign of rising demand and broader adoption across industries. Also, thermosetting plastics also hold a significant share in sectors such as electronics, aerospace, and construction. Each material type has unique advantages, so understanding their differences and applications is the key to optimizing product performance.
This article will provide a detailed comparison of thermosetting vs thermoplastic, analyzing their characteristics, strengths and weaknesses, and real-world applications—ultimately helping you answer the question: “Which one should you choose?”
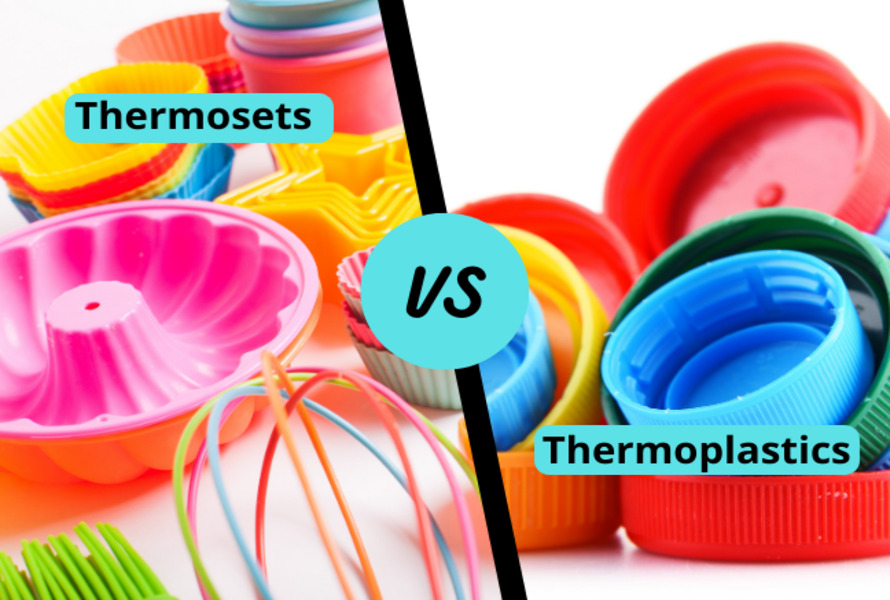
Thermosets vs Thermoplastics: Which one to choose?
1. Basic Concepts of Thermoplastic and Thermosetting Plastic
1.1. What is Thermoplastic?
Thermoplastic is a polymer that can soften when heated and harden when cooled, and this process can be repeated multiple times without significant changes to its chemical structure. This feature comes from its linear or branched molecular structure, where the chains are held together by weak secondary bonds (Van der Waals or hydrogen bonds) that are easily broken by heat.
Common examples include:
- Polyethylene (PE): plastic bags, packaging films.
- Polypropylene (PP): storage boxes, automotive parts.
- Polyvinyl Chloride (PVC): water pipes, building materials.
- Polyethylene Terephthalate (PET): beverage bottles.
- Polyamide (PA): mechanical parts, cables.
The main advantages of thermoplastic are ease of processing, recyclability, and design flexibility—making it suitable for mass production.
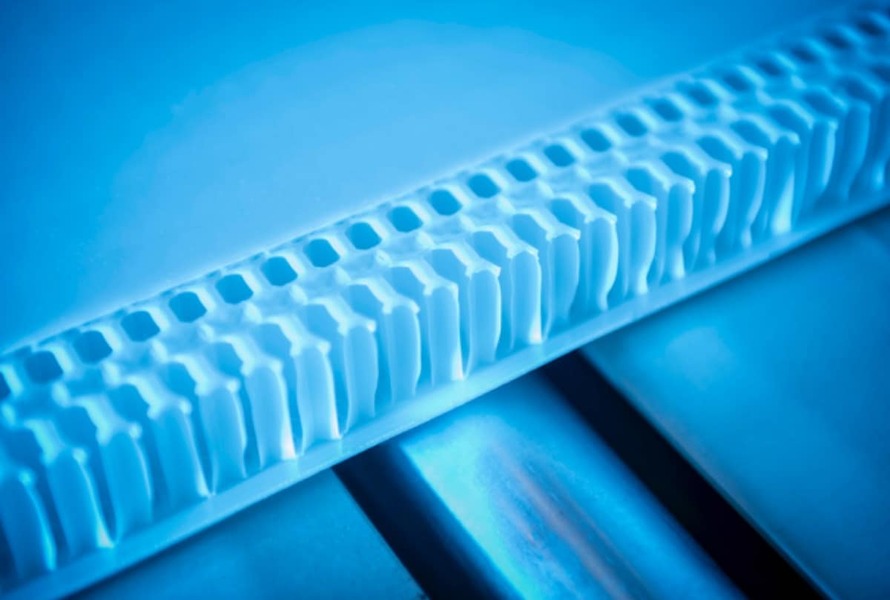
Thermoplastic is a type of polymer that undergo a phase transition from solid to liquid when exposed to elevated temperatures.
Moreover, the production of synthetic thermoplastic materials involves the polymerization process, which entails the connection of discrete particles (monomers) to form a chain-like structure. From just a single polymer chain, thousands of monomers can be created. Covalent solid bonds can link atoms together, while the forces between polymer chains are weak.
1.2. What is Thermosetting Plastic?
Thermosetting plastic is a polymer that, once cured through heat or chemical reaction, becomes permanently rigid. After setting, it cannot be remelted or reshaped. This is due to its three-dimensional cross-linked network structure, which provides excellent rigidity and dimensional stability.
Common examples include:
- Epoxy: industrial adhesives, printed circuit boards.
- Phenolic (PF): cookware handles, electrical insulators.
- Melamine Formaldehyde (MF): heat-resistant kitchenware, furniture.
- Urea Formaldehyde (UF): wood adhesives, molded parts.
Thermosetting plastics are widely used in applications requiring heat resistance, chemical resistance, and high rigidity, such as electrical equipment, construction materials, and aerospace components.
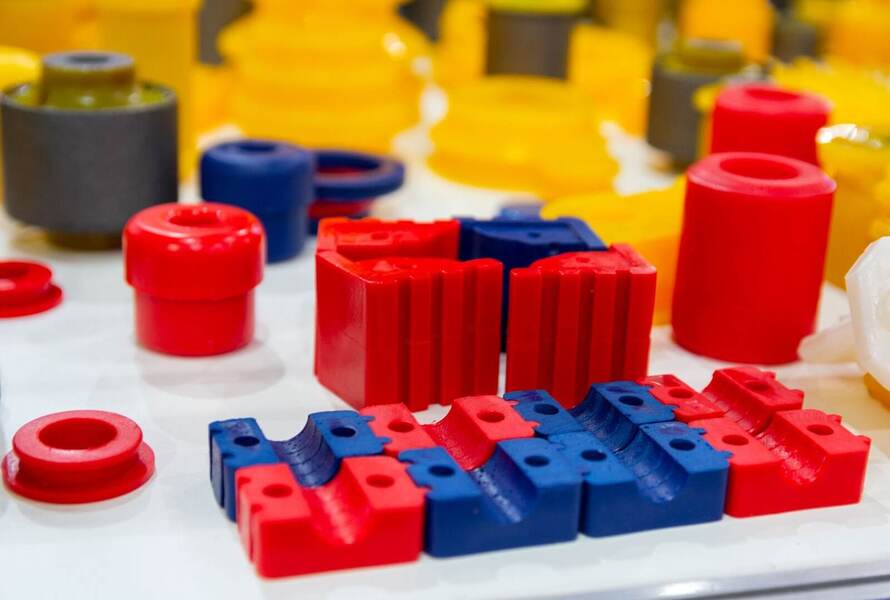
Thermosetting can undergo a three-dimensional transformation as a result of chemical processes
2. Properties of Thermoplastic
2.1. Mechanical Properties
Thermoplastics are well-known for their flexibility and impact resistance. Materials such as PP or PE can absorb shock effectively, making them suitable for products that need toughness. Tensile strength varies by polymer type—for example, PA has higher tensile strength than PE.
Moreover, thermoplastics can be reinforced with glass fibers or inorganic fillers to improve stiffness and dimensional stability, expanding their use in engineering applications.
2.2. Heat Resistance
A major limitation of thermoplastics is their lower maximum service temperature compared to thermosetting plastics. The heat deflection temperature (HDT) for most thermoplastics is in the range of 60–120°C, except for high-performance grades like PEEK or PSU, which can exceed 200°C.
This means thermoplastics may soften or deform under prolonged exposure to high temperatures, so material selection must be carefully considered.
2.3. Recyclability and Processability
One of the most important advantages of thermoplastics is their recyclability. They can be melted and reshaped multiple times, reducing waste and making them more environmentally friendly.
Thermoplastics are compatible with many processing techniques, including:
- Injection molding
- Extrusion
- Blow molding
- Thermoforming
Thanks to this versatility, thermoplastics dominate industries such as packaging, household goods, and automotive parts.
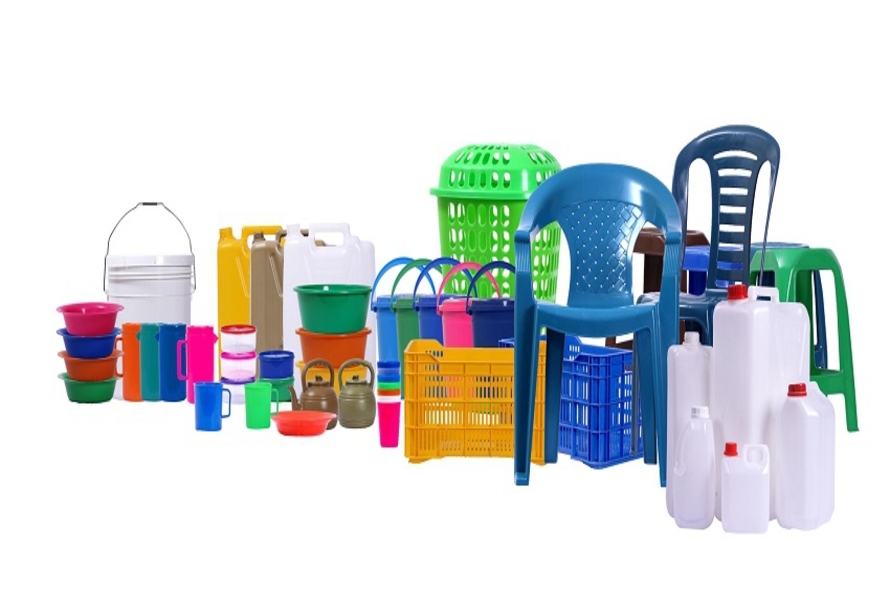
Thermoplastics are used in the production of popular plastic products such as tables and chairs
3. Properties of Thermosetting Plastic
3.1. Mechanical Properties
Thermosetting plastics have higher rigidity and tensile strength than thermoplastics. Their cross-linked network structure ensures dimensional stability under long-term loads, with little to no plastic deformation.
For instance, carbon fiber-reinforced epoxy can reach a tensile strength of 1,500 MPa, far exceeding most thermoplastics.
3.2. Heat Resistance
Unlike thermoplastics, thermosetting plastics do not soften when reheated after curing. Many can withstand working temperatures above 200°C without losing mechanical strength. This makes them indispensable in electronics, insulation, and aerospace applications.
3.3. Chemical Resistance and Durability
Thermosetting plastics offer excellent resistance to solvents, acids, and alkalis, and they are less prone to aging under environmental stress. Many types can last over 20 years in normal conditions.
Because of this, they are ideal for outdoor applications, chemical-resistant equipment, and harsh industrial environments.
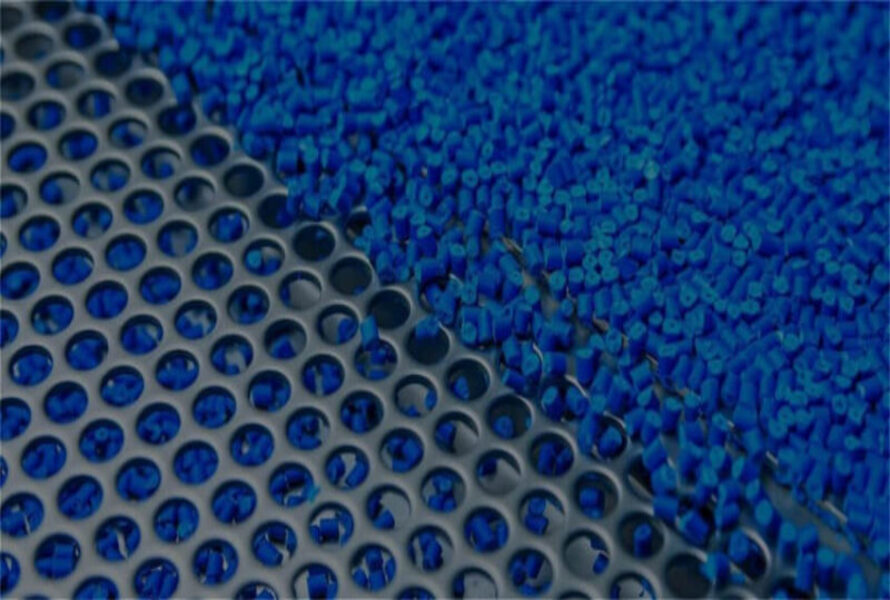
Thermosetting's physical properties do not change under the influence of high temperatures
4. Common applications of thermoplastic
Each thermoplastic will have its advantages and characteristics. Therefore, they will also be optimized in each different product and field. You can differentiate based on the types of symbols engraved on the base of the plastic product. For instances:
- PET plastic (Polyethylene Terephthalate): They are used in the bottling and textile industries. PET thermoplastic is tested to be safe for consumer health and is suitable for products that come into direct contact with food.
- PS (Polystyrene) Thermoplastic: Polymerized styrene thermoplastic is manufactured using the stiten process and is recyclable several times, even after prolonged consumption. This type of plastic usually exists in a complex form, has no unpleasant odor, and is transparent in color under normal conditions. Specifically, polystyrene (PS) plastic is very affordable due to its ease of blending and ability to undergo various molding techniques. Because of its notable water resistance, this material finds application in producing plastic eating utensils, children's toys, and plastic covers for CDs or DVDs.
- PVC (Polyvinyl Chloride) Thermoplastic: Depending on the composition, this type of plastic can withstand extreme temperatures ranging from -55 degrees Celsius to 100 degrees Celsius. Therefore, flexibility and durability are two fundamental attributes. They are commonly used in the construction and medical fields, such as: cables, metal cladding, water pipes, dialysis equipment, intravenous bags, or respiratory tubes.
- PP - Polypropylene Thermoplastic: The material stands out for its low price and is colorless and odorless. However, PP thermoplastic cannot withstand temperatures for too long; the average temperature this material can meet is 130 - 170 degrees Celsius. Besides, PP thermoplastic is also waterproof with high hardness, making it very difficult to stretch or deform under significant impact. Therefore, PP plastic is used in the printing, food, medical and fast-moving consumer goods industries.
In general, thermoplastics make products close to human life and are indispensable materials in many fields.
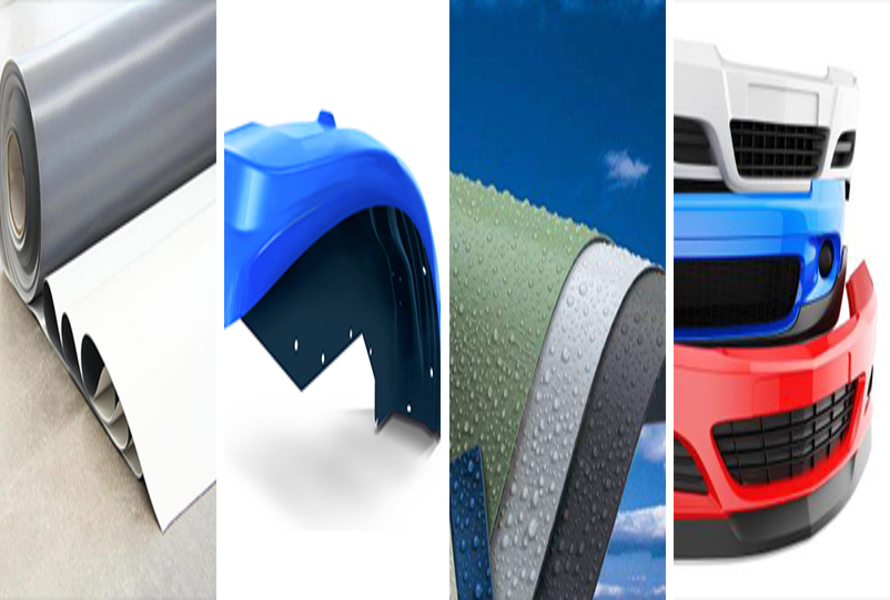
Thermoplastic is used in the production of car materials
5. Applications of thermosetting
Several thermosetting polymers that are widely used in various industries are Polycarbonate (PC) plastic, Polyamide (PA) plastic, Epoxy plastic or Epoxy Resin, and Acrylonitrile Butadiene Styrene (ABS) plastic. Each type will be utilized across several production sectors, encompassing various businesses. For example:
- PC - Polycarbonate Plastic: The polymer reveals a high level of transparency and provides superior air permeability compared to PVC or PE. Consequently, polycarbonate (PC) is employed in the manufacturing process of automotive glass. The PC material has high thermal stability, overcoming temperatures up to 100 degrees Celsius. Additionally, it demonstrates commendable resistance to corrosion and remains inert when exposed to various chemical constituents found in food.
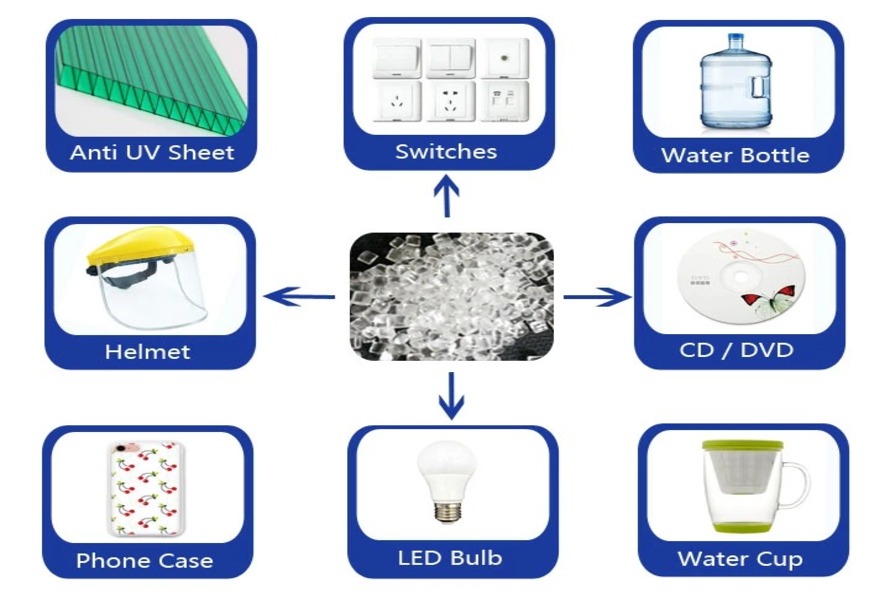
The applications of PC Thermoplastic
- PA - Polyamide Thermosetting: The material is commonly used in the marine and automotive sectors or the production of accessories such as friction bearings and gears because it has low friction, high hardness, and the ability to withstand lubricating oils and heat insulation stable electricity.
- Epoxy or Epoxy Resin: When placed under freezing temperatures, this particular plastic exhibits a remarkable ability to establish a highly resilient and nearly impervious connection. Epoxy thermosetting resin can be readily combined with various pigments to create three-dimensional artworks, jewelry embellishments, or adhesive compounds. Furthermore, plastics are frequently employed in adhesive applications, including their use in the manufacturing of skateboards.
- ABS - Acrylonitrile Butadiene Styrene Thermosetting: Thermosetting plastics stand out for their toughness and impact resistance, as well as not changing shape significantly when exposed to high temperatures. Water resistance and electrical insulation are also strong points of ABS material. Therefore, it makes electrical panels, water pipes, phone cases, refrigeration equipment, or packaging.
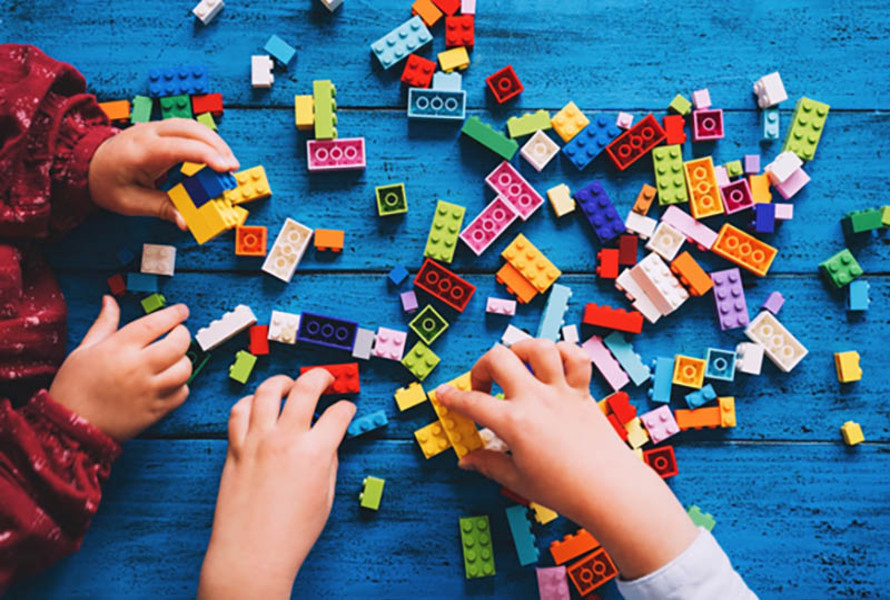
The ABS Thermosetting is used to product children's toys such as Lego.
6. Thermosetting vs Thermoplastic: A Detailed Comparison
Criteria |
Thermoplastic |
Thermosetting Plastic |
Molecular structure |
Linear or branched chains |
Three-dimensional cross-linked network |
Reprocessability |
Can be remelted and reshaped |
Cannot be remelted after curing |
Recyclability |
High |
Low |
Heat resistance |
Moderate (60–120°C) |
High (>200°C) |
Mechanical strength |
Flexible, good impact resistance |
Rigid, strong under long-term loads |
Chemical resistance |
Moderate |
Excellent |
Applications |
Packaging, consumer goods, auto parts |
Electronics, aerospace, construction |
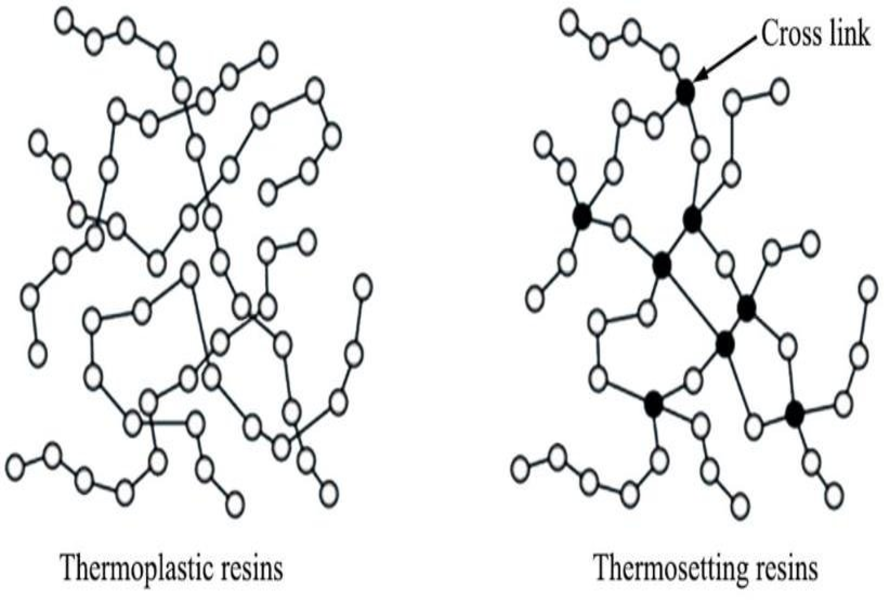
The differences in chemical structure between Thermoplastic and Thermosetting
7. Which One Should You Choose?
7.1. Key Selection Criteria
When deciding between thermosetting vs thermoplastic, consider:
- Operating temperature: >150°C → thermosetting is usually better.
- Mechanical requirements: rigid, long-term load → thermosetting; flexible, impact resistance → thermoplastic.
- Recyclability & sustainability: thermoplastic is more eco-friendly.
- Production cost: thermoplastic generally cheaper and faster to process.
7.2. Recommendations by Application
Mass consumer goods (packaging, household items, general components) → Thermoplastic is preferred for cost efficiency and design flexibility.
High-performance applications (electronics, high-temperature equipment, composites) → Thermosetting plastic ensures strength and durability.
8. Conclusion
Both thermoplastic and thermosetting plastic are essential in modern industries. There is no single “best” option—only the most suitable choice depending on performance requirements, cost, and working environment.
If you’re unsure which material fits your production needs, carefully evaluate working conditions, cost efficiency, and sustainability goals. For expert consultation and high-quality plastic solutions, EuroPlas is ready to support your business with tailored recommendations.
EuroPlas has sent readers the most useful and detailed information about two popular industrial plastic materials, thermoplastic and thermosetting plastic. We hope that the article will provide interesting and useful knowledge in everyday life. Please continue to follow EuroPlas to update the latest news about "Plastic World"!
9. FAQ – Frequently Asked Questions
9.1. Is thermoplastic as strong as thermosetting plastic?
→ Not exactly. Thermoplastics are more flexible and impact-resistant, while thermosets are more rigid and heat-resistant.
9.2. Can thermosetting plastics be recycled?
→ Yes, but only through mechanical or chemical recycling, which is more complex and costly than thermoplastic recycling.
9.3. Which thermoplastic has the best heat resistance?
→ High-performance grades such as PEEK, PSU, and PPS can withstand over 200°C, approaching thermoset performance.
9.4. Are there plastics that combine both properties?
→ Yes, for example glass fiber-reinforced thermoplastics or high-heat thermoplastics that offer improved stiffness and heat resistance similar to thermosets.