In the realm of advanced manufacturing, understanding the properties and processing techniques of PA6 material is crucial for optimizing production efficiency and product quality. PA6, or Polyamide 6, is renowned for its excellent mechanical strength, impact resistance, and versatility, making it a preferred choice in various applications, from automotive components to consumer goods. This article delves into the key processing techniques for PA6 material, essential factors to consider during processing, and an overview of its unique characteristics to help manufacturers achieve superior results.
Read more: PA6 vs. PA66: The Differences Between Two Engineering Giants
1. Overview of PA6 Material
PA6 material, also known as Polyamide 6, is a semi-crystalline thermoplastic widely recognized for its excellent mechanical properties and versatility in various applications. This material is particularly valued in the woodworking and manufacturing industries due to its low friction coefficient, high thermal resistance, and outstanding electrical insulation capabilities. PA6 material is commonly utilized in the production of gears, bearings, and fittings, making it an ideal choice for technical components that require durability and reliability.
Additionally, its compatibility with various processing techniques, including injection molding and 3D printing, further enhances its appeal in modern manufacturing processes. As industries continue to seek innovative solutions, PA6 material stands out as a robust option for high-performance applications.
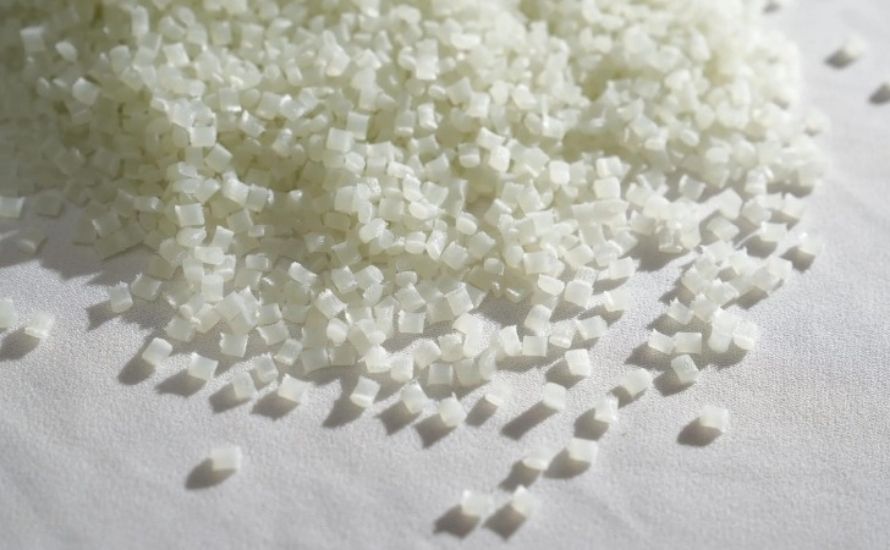
2. Key Processing Techniques
When it comes to the key processing techniques of PA6 material, several critical steps ensure optimal performance and quality in various applications, particularly in woodworking and manufacturing. Here are the essential techniques:
- Drying: Due to PA6's high moisture absorption capacity, drying the material before processing is crucial. The recommended drying temperature is above 80°C for at least 16 hours to prevent defects during molding. Proper drying helps eliminate moisture that can lead to issues such as bubbles and dimensional instability in the final product.
- Injection Molding: The melting temperature for PA6 material typically ranges from 230°C to 280°C. Maintaining a mold temperature between 80°C and 90°C is essential to enhance crystallinity, which significantly affects the mechanical properties of the final product.
- Reinforcement: Incorporating glass fiber into PA6 material can improve its mechanical strength and reduce shrinkage rates. This modification is particularly beneficial for applications requiring high durability and dimensional stability.
- Injection Speed and Pressure: Proper control of injection speed and pressure is vital to ensure uniform filling of molds and to minimize internal stresses in the molded parts. Generally, injection pressures should be maintained between 750 and 1250 bar, depending on the specific application.
- Cooling and Post-Processing: After molding, a controlled cooling process is necessary to prevent warping and ensure dimensional accuracy. Additionally, post-processing methods may enhance the material's properties, making it suitable for high-performance applications in wood processing. Effective cooling and post-processing strategies are critical for achieving the desired performance characteristics in the final products.
By following these key processing techniques, manufacturers can maximize the potential of PA6 material, ensuring high-quality products that meet industry standards.
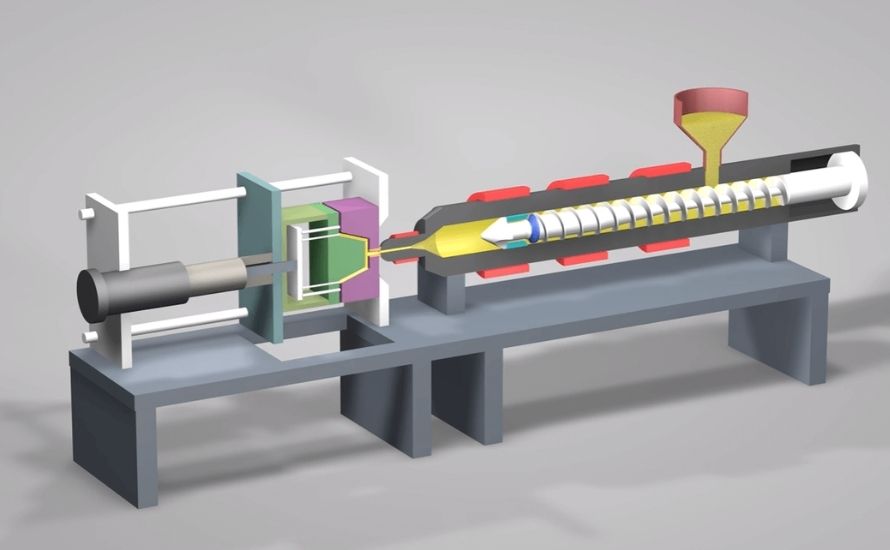
3. Factors to Consider During Processing
When processing PA6 material, several critical factors must be considered to ensure optimal performance and product quality. Here are the key factors to keep in mind:
- Moisture Content: PA6 is hygroscopic and can absorb moisture from the environment, which can negatively affect its processing characteristics and final properties. Therefore, regularly monitoring moisture levels is crucial to maintain the integrity of the material throughout the production process.
- Thermal Stability: PA6 can withstand temperatures up to 310°C without decomposing; however, processing temperatures should be kept below this threshold to prevent thermal degradation. Exceeding this temperature can compromise the material's properties, leading to discoloration and loss of mechanical strength. Careful temperature management during processing is essential to preserve the quality of PA6.
- Mold Design: The design of the mold plays a significant role in the processing of PA6. Factors such as gate size, venting, and wall thickness should be optimized to ensure proper flow and minimize defects during injection molding. A well-designed mold facilitates efficient material flow, reduces cycle times, and enhances the overall quality of the molded parts. Attention to mold design can significantly impact the success of the injection molding process.
- Recycling Considerations: If recycled PA6 is used, the proportion should not exceed 25% of the total material to maintain mechanical properties and processing stability. Additionally, recycled materials must be dried before mixing with virgin PA6 to avoid moisture-related issues. Proper handling and processing of recycled PA6 can contribute to sustainability efforts while ensuring that the final products meet quality standards.
- Post-Processing Treatments: After molding, PA6 parts may require post-processing treatments, such as humidity control, to enhance their mechanical properties and ensure dimensional stability. These treatments can include annealing or controlled storage conditions to mitigate the effects of moisture absorption. Implementing effective post-processing strategies is essential for achieving the desired performance characteristics in the final products.
By considering these factors during the processing of PA6 material, manufacturers can optimize their production processes and achieve high-quality results suitable for various applications in the woodworking and manufacturing industries.
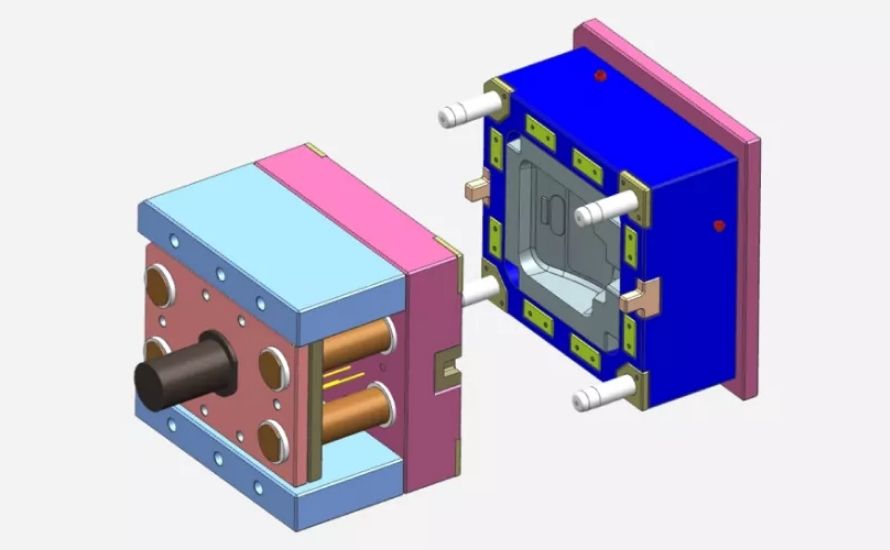
4. Conclusion
Mastering processing techniques for PA6 is crucial for manufacturers to leverage its exceptional properties. Understanding PA6's mechanical strength and thermal stability allows companies to optimize production for efficiency and quality. Key methods like injection molding and extrusion are vital for creating complex components. Additionally, managing moisture content and processing temperatures is essential to prevent defects. Embracing these techniques enables manufacturers to fully harness PA6's potential.
5. About EuroPlas’ PA Products
EuroPlas offers a range of advanced PA products, including PA6 and PA66 blend compounds, designed to meet the diverse needs of various industries. PA6 is known for its ease of processing, lower melting temperature, and cost-effectiveness, while PA66 provides superior temperature resistance, stiffness, and abrasion resistance. The blend of PA6 and PA66 combines the best properties of both materials, resulting in a resilient compound with strong mechanical characteristics. These compounds are widely utilized in the automotive and motorcycle sectors, finding applications in components such as roller bearings, carburetors, and fuel tank lids.
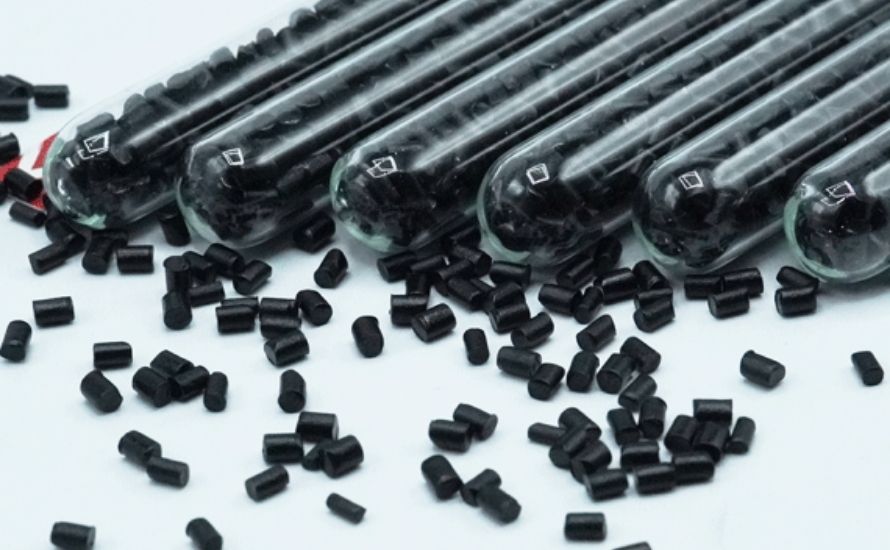
EuroPlas stands out with its commitment to quality, offering tailor-made solutions that enhance the usability and durability of end products. For businesses seeking reliable and advanced plastic compounds, EuroPlas is your go-to partner. Contact us today to learn more about how our PA products can elevate your manufacturing processes.