When it comes to material selection, understanding the nuances between TPE (Thermoplastic Elastomer) and TPR (Thermoplastic Rubber) is essential. TPR vs TPE are widely used in various industries due to their exceptional flexibility and resilience.
In this comprehensive guide, we will explore the key similarities and differences between TPE vs TPR, including their composition, processing methods, physical properties, and application areas. By delving into the unique characteristics of TPR vs TPE, you'll gain valuable insights into which material is best suited for your specific project needs. Let’s get started!
Table of Contents
- What is TPE?
- What is TPR?
- TPE vs TPR: What are the similarities & differences?
- About EuroPlas masterbatch
1. What is TPE?
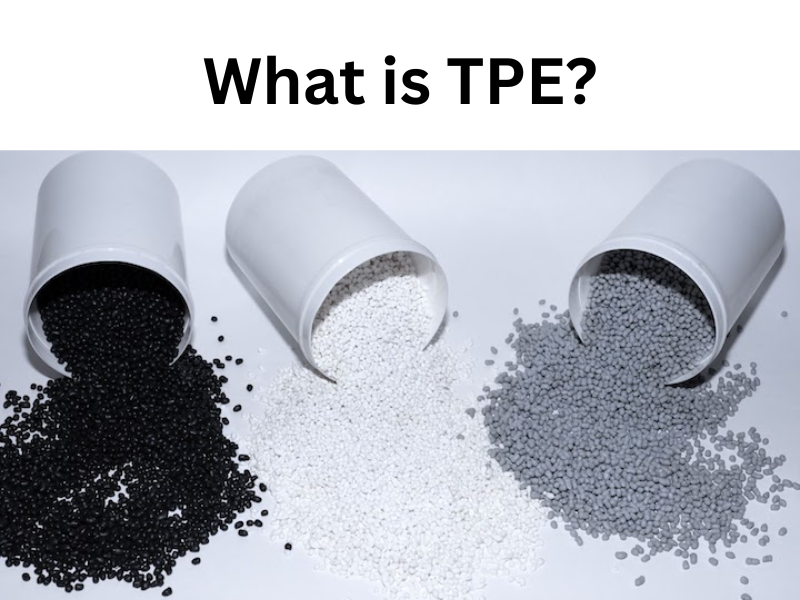
TPE
Thermoplastic Elastomers (TPE) are a class of materials that offer a remarkable combination of thermoplastic and elastomeric properties. They are versatile polymer blends that exhibit the elasticity and resilience of rubber while also providing the processability and shape retention of thermoplastics. TPEs have gained significant popularity and are widely used in various industries due to their unique characteristics and suitability for a wide range of applications.
1.1 Definition and Composition
TPEs are composed of two or more components, often a thermoplastic polymer and an elastomeric phase. The thermoplastic component contributes to the material's processability, allowing it to be melted, molded, and reshaped multiple times without undergoing any significant chemical change. The elastomeric phase, on the other hand, imparts the rubber-like properties, such as flexibility, resilience, and stretchability, to the TPE material.
1.2 Structure and Molecular Arrangement
The structure of TPEs can vary depending on the specific composition and manufacturing process. Generally, TPEs exhibit a phase-separated microstructure, where the elastomeric phase forms discrete domains dispersed within the thermoplastic matrix. This phase separation allows TPEs to combine the properties of both components effectively. The molecular arrangement within TPEs enables them to undergo deformation and return to their original shape, similar to traditional rubber materials.
1.3 Properties and Performance
TPEs possess a wide range of properties that make them highly desirable for numerous applications. These materials exhibit excellent elasticity, enabling them to stretch and recover without permanent deformation. They also display good resistance to chemicals, UV radiation, and weathering, making them suitable for outdoor applications. TPEs can be formulated to have specific levels of hardness, ranging from soft and flexible to hard and rigid, based on the intended application requirements. Additionally, TPEs exhibit low toxicity, good electrical insulation properties, and can be colored or molded into various shapes and sizes.
The performance of TPEs can be tailored by adjusting the composition, molecular weight, and processing conditions during manufacturing. This flexibility allows manufacturers to create TPEs with specific properties suitable for different industries, including automotives, consumer goods, medical devices, electronics, and more.
Overall, TPEs offer a unique combination of elastomeric and thermoplastic properties, making them highly versatile and suitable for a wide range of applications. Their ability to provide elasticity, processability, and customizable properties has contributed to their growing popularity in various industries.
2. What is TPR?
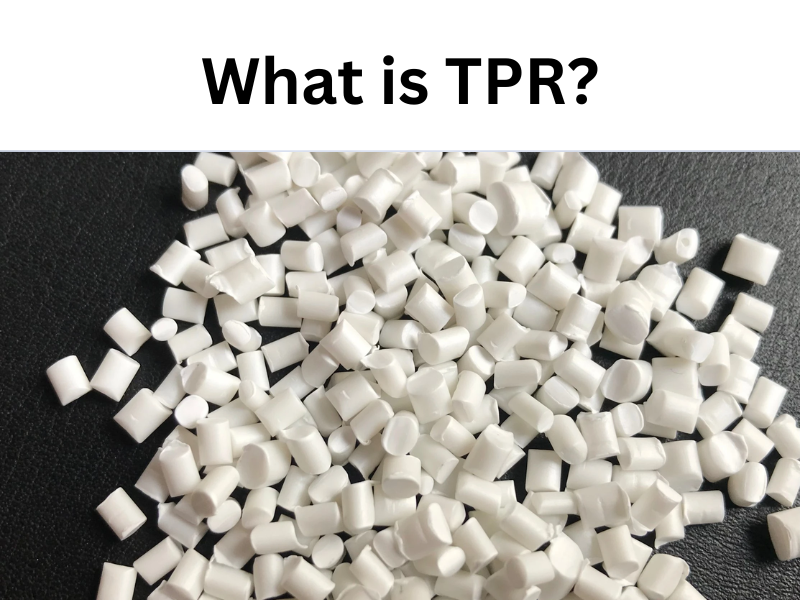
TPR
Thermoplastic Rubber (TPR) is a class of materials that falls under the broader category of thermoplastic elastomers (TPE). TPR combines the characteristics of thermoplastics and rubber, offering a balance between flexibility and processability. TPRs are widely used in various industries due to their versatile properties and cost-effectiveness.
2.1 Definition and Composition
TPR is a blend of polymers that includes a thermoplastic component and a rubber component. The thermoplastic component provides the material with the ability to be melted and reshaped multiple times without undergoing significant chemical change. The rubber component contributes to the TPR's elastic properties, allowing it to exhibit flexibility, resilience, and good impact resistance.
2.2 Structure and Molecular Arrangement
The structure of TPRs is similar to other thermoplastic elastomers, where the rubber phase is dispersed in a thermoplastic matrix. This phase separation gives TPR its rubber-like properties while maintaining the processability of a thermoplastic material. The molecular arrangement allows TPR to be easily molded into various shapes and sizes.
2.3 Properties and Performance
TPRs possess a range of properties that make them suitable for a wide array of applications. They offer excellent flexibility, allowing for easy bending, twisting, and stretching without permanent deformation. TPRs also exhibit good resistance to abrasion, chemicals, and weathering, making them durable and long-lasting. Additionally, TPRs can be formulated to have different levels of hardness, ranging from soft and gel-like to harder and more rigid, depending on the desired application requirements.
TPRs are widely used in industries such as footwear, automotive, toys, sports equipment, and household products. They are commonly found in shoe soles, handles, grips, seals, gaskets, and various molded parts. TPRs provide a cost-effective alternative to natural rubber while offering similar performance characteristics.
In conclusion, TPR is a type of thermoplastic elastomer that combines the properties of thermoplastics and rubber. It offers flexibility, processability, and durability, making it suitable for diverse applications. TPRs are widely utilized across industries, providing a cost-effective solution without compromising performance.
3. TPE vs TPR: What are the similarities & differences?
3.1. Similarities between TPE vs TPR
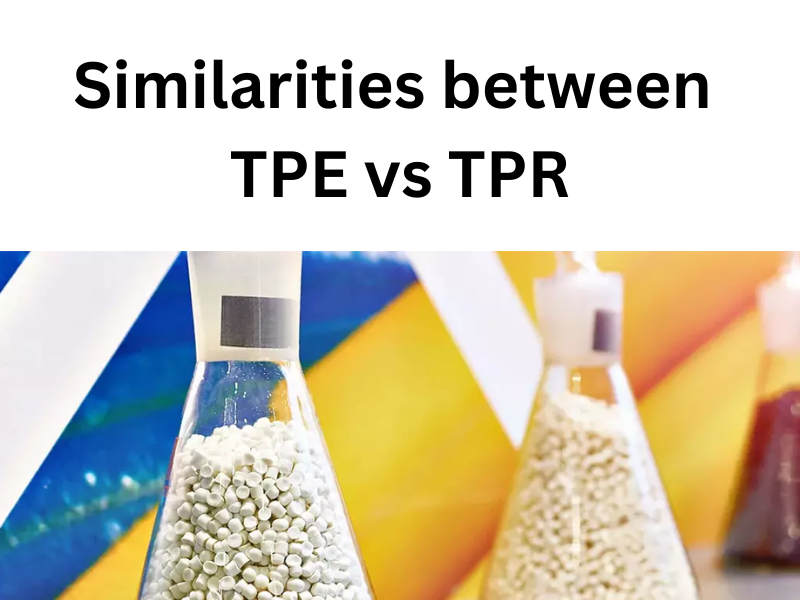
Similarities between TPE vs TPR
Thermoplastic Elastomers (TPE) and Thermoplastic Rubber (TPR) share several similarities due to their common classification as thermoplastic elastomers. While they have distinct characteristics, there are certain properties and features that are common to both TPR vs TPE materials.
- Elasticity and Flexibility: Both TPE vs TPR exhibit excellent elasticity and flexibility, allowing them to stretch and recover without undergoing permanent deformation. This property makes them suitable for applications that require materials with resilience and the ability to endure repeated movements or stresses.
- Processability: TPR vs TPE materials are thermoplastic, meaning they can be melted and reshaped multiple times without significant chemical change. This characteristic enables them to undergo various processing techniques such as injection molding, extrusion, and blow molding. The ability to process these materials efficiently and cost-effectively contributes to their widespread use in manufacturing industries.
- Versatility: Both TPE vs TPR offer versatility in terms of their composition and formulation. They can be engineered to possess a wide range of properties, including different levels of hardness, flexibility, and resistance to chemicals or weathering. This versatility allows manufacturers to tailor the materials to specific application requirements, expanding their potential uses across diverse industries.
- Cost-effectiveness: TPR vs TPE materials often provide cost-effective alternatives to traditional rubber materials. Their manufacturing processes are generally less complex, resulting in reduced production costs. Moreover, their durability and long-lasting properties contribute to lower maintenance and replacement expenses over time.
- Wide Range of Applications: Both TPE vs TPR find applications in various industries due to their combination of elastomeric and thermoplastic properties. They are utilized in sectors such as automotives, footwear, consumer goods, electronics, medical devices, and more. These materials are commonly employed in the production of seals, gaskets, grips, handles, and molded components.
In conclusion, TPE vs TPR share several similarities as thermoplastic elastomers. They both offer elasticity, flexibility, processability, versatility, cost-effectiveness, and find applications in diverse industries. However, it is essential to recognize that they also have distinct characteristics and properties, which will be discussed further in the subsequent sections.
3.2. Differences between TPE vs TPR
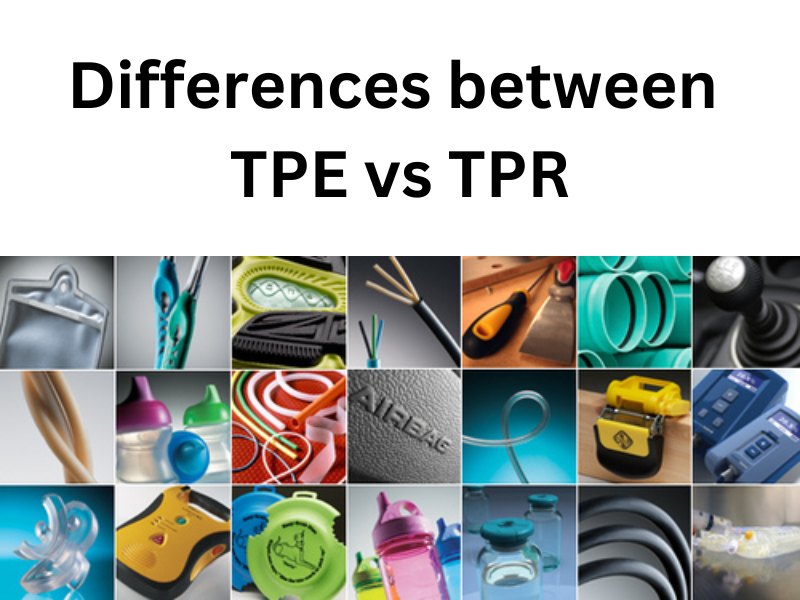
Differences between TPE vs TPR
While Thermoplastic Elastomers (TPE) and Thermoplastic Rubber (TPR) belong to the same category of thermoplastic elastomers, they have some notable differences in terms of composition, properties, and applications. Understanding these differences is crucial for selecting the most suitable material for specific needs.
- Composition: TPEs are typically composed of a blend of two or more components, including a thermoplastic polymer and an elastomeric phase. This composition allows for a fine-tuning of properties, such as hardness, flexibility, and chemical resistance. On the other hand, TPRs are specifically formulated to incorporate a thermoplastic component and a rubber component, which gives them a more rubber-like nature.
- Hardness Range: One significant difference between TPR vs TPE is the range of hardness they can achieve. TPEs can be formulated to cover a broader hardness range, from very soft and flexible (such as gel-like materials) to harder and more rigid materials. TPRs, on the other hand, generally have a narrower hardness range, typically offering softer and more rubber-like hardness levels.
- Processability: TPEs are known for their excellent processability, allowing them to be easily molded, extruded, or blow-molded using conventional thermoplastic processing techniques. They can be processed efficiently at lower temperatures, making them energy-efficient. TPRs, while still thermoplastic, may have slightly different processing requirements due to their rubber component. They may require higher processing temperatures and specific processing techniques to achieve optimal results.
- Properties and Performance: TPEs and TPRs may exhibit differences in terms of their overall properties and performance. TPEs often offer a balanced combination of elasticity, flexibility, and processability. They can provide good chemical resistance, UV stability, and weathering resistance depending on the specific formulation. TPRs, with their higher rubber content, tend to offer enhanced elasticity, resilience, and impact resistance, which can be beneficial in certain applications.
- Applications: TPEs and TPRs find application in various industries; however, the specific applications may differ due to their distinct properties. TPEs are commonly used in automotive parts, consumer goods, electrical cables, medical devices, and more. TPRs, with their more rubber-like properties, are often utilized in footwear soles, grips, handles, and other applications that require higher elasticity and impact resistance.
In conclusion, while TPR vs TPE share similarities as thermoplastic elastomers, they have differences in terms of composition, hardness range, processability, properties, and applications. These differences should be carefully considered when selecting the most appropriate material for a particular application, taking into account the desired properties, processing requirements, and performance characteristics needed.
4. About EuroPlas masterbatch
At EuroPlas, we take pride in being a top-tier masterbatch manufacturer based in Vietnam, committed to delivering exceptional solutions for a wide range of industries. With our extensive experience, cutting-edge technology, and a strong focus on innovation, we offer an extensive portfolio of high-quality masterbatch products tailored to meet diverse applications and requirements.
Let's explore our comprehensive range of masterbatch products in greater detail:
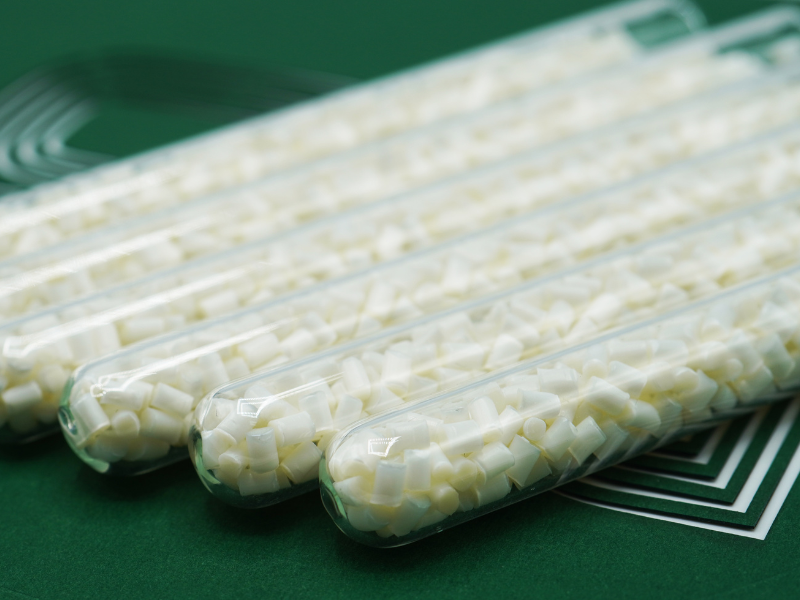
EuroPlas Bioplastic Compound
EuroPlas specializes in developing bioplastic compounds that address the growing demand for sustainable materials. Our bioplastic compounds are derived from renewable sources and offer exceptional biodegradability while maintaining the required mechanical properties. They are an ideal choice for applications where eco-friendliness is paramount.
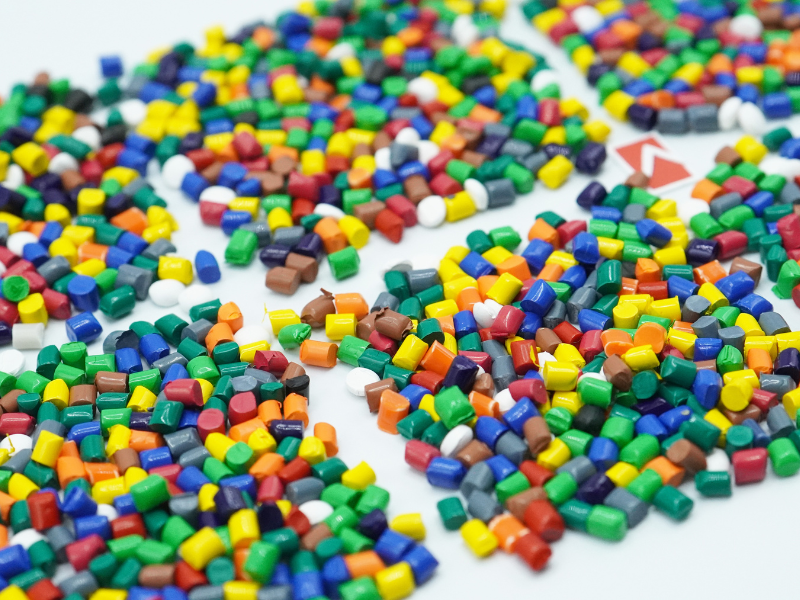
EuroPlas Color Masterbatch
We offer a wide selection of color masterbatch solutions that enable manufacturers to achieve vibrant and consistent colors in their plastic products. Our color masterbatches are meticulously formulated to ensure excellent dispersion, color accuracy, and UV stability, enhancing the visual appeal and brand recognition of the end products.
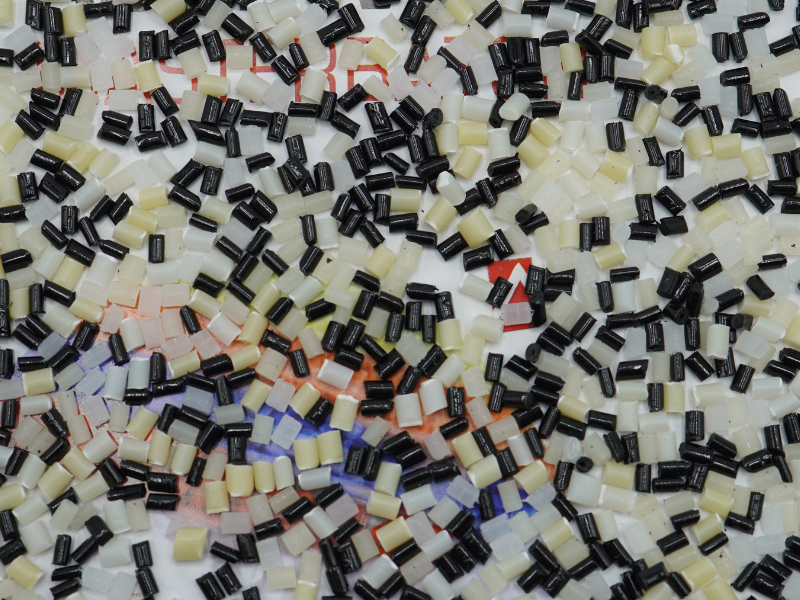
EuroPlas Plastic Additives
EuroPlas provides an extensive range of plastic additives to enhance the performance and functionality of plastic materials. Our additives include UV stabilizers, antistatic agents, flame retardants, processing aids, and more. These additives improve the durability, processability, and end-use properties of plastic products, enabling manufacturers to meet specific requirements and industry standards.
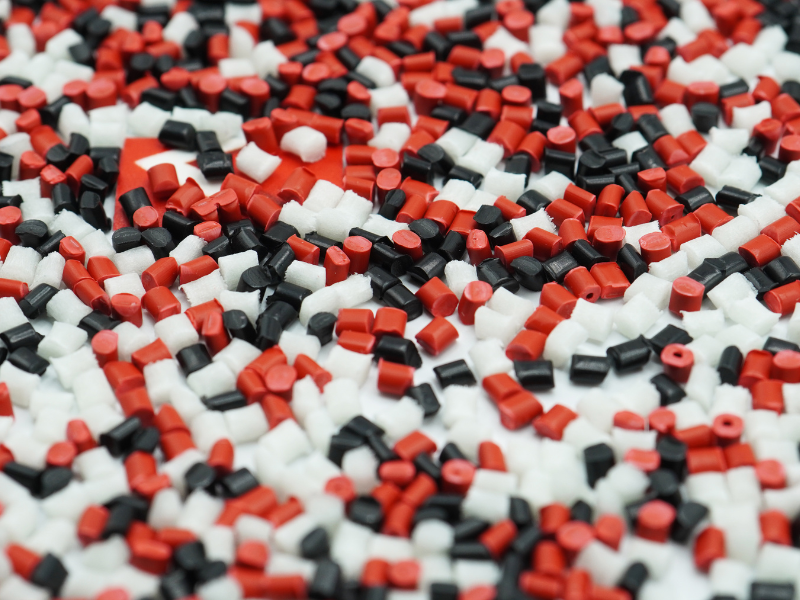
EuroPlas Engineering Plastic Compound
EuroPlas offers high-performance engineering plastic compounds that cater to the stringent demands of various industries. Our compounds are engineered to exhibit exceptional strength, impact resistance, chemical resistance, and heat resistance, making them ideal for applications such as automotive components, electrical appliances, and industrial parts.
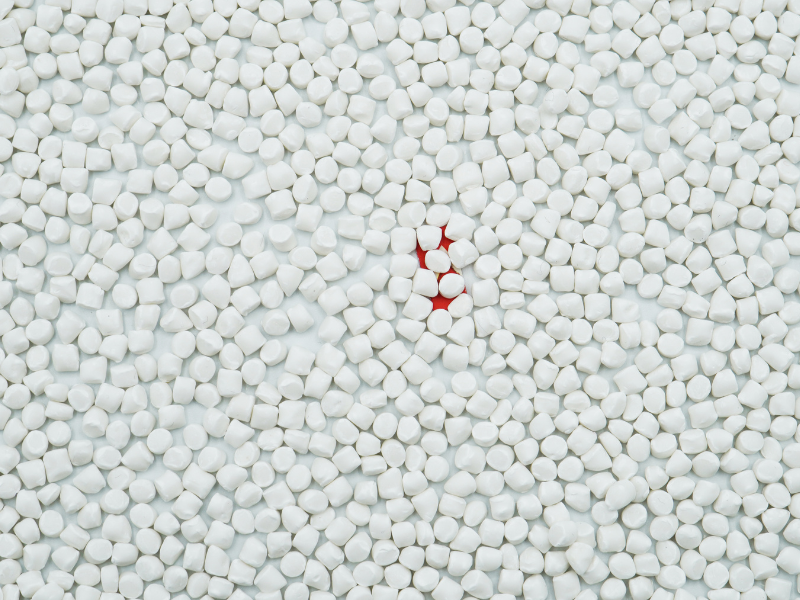
EuroPlas Filler Masterbatch
EuroPlas's filler masterbatch comprises PE or PP resin blended with calcium carbonate (CaCO3) and additives like wax and oil. It enhances mechanical properties, dimensional stability, and achieves desired weight reduction in plastic materials, optimizing cost-efficiency without compromising quality.
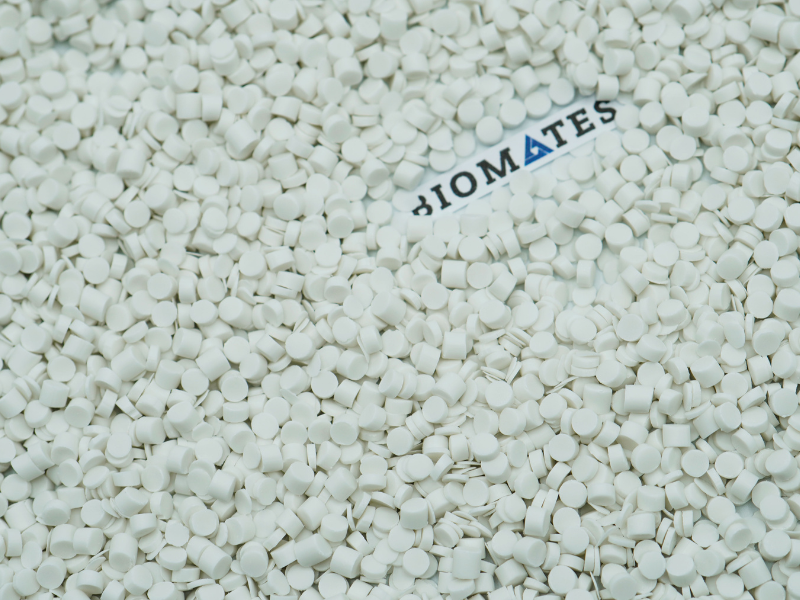
EuroPlas Bio Filler
EuroPlas bio filler products are derived from renewable resources, offering an eco-friendly alternative for enhancing the properties of plastic materials. These bio fillers effectively improve tensile strength, impact resistance, and stiffness, allowing manufacturers to create sustainable products without compromising on performance or functionality.
At EuroPlas, we are committed to providing the highest level of quality and customer satisfaction. Our team of experienced professionals works closely with clients to understand their specific needs and deliver customized masterbatch solutions. With state-of-the-art manufacturing facilities, advanced quality control measures, and a strong focus on research and development, we ensure that our masterbatch products consistently meet and exceed industry standards.
So what are you waiting for? Contact us now and to explore our comprehensive range of masterbatch solutions or discuss your specific needs for your next project!