I. What is FIBC bulk bags?
FIBC stands for flexible intermediate bulk containers designed to contain, store and transport products and materials such as sand, fertilizer, plastic granules, agricultural products, etc. FIBC can be bulk bags, jumbo bags, super sacks, big bags, or ton bags.
FIBCs are typically made from thick woven strands of oriented polypropylene, coated or uncoated. Its capacity usually ranges between 500 kg and 2500 kg. The most common use is the 1000kg bag. Because of this load, the bag size will be suitable for packaging equipment and vehicles, and inventory goods.
Related:
- What are Laminating Pouches Made of?
- Cement Plastic Bags Manufacturing Process - The Ultimate Guide
- What was bubble wrap invented for?
- How is HDPE pipe most commonly joined?
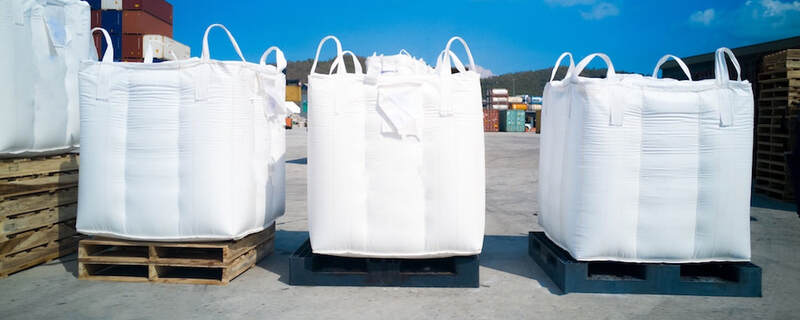
II. Pros and cons of FIBC
2.1 Pros of FIBC
- Used in many industries: The FIBC bulk bags are made of highly flexible materials, coated or uncoated, and come with different options such as type A, type B, type C, and type D, depending on your needs. These bulk bags can prevent moisture, electric charge, fire, etc. So they can be used to store everything from agricultural products to animal feed, chemicals, and pharmaceuticals.
- Lightweight yet durable: Another advantage of FIBC bags is that they are lightweight yet durable. Bulk bags can be used to store heavy items while retaining their shape and structure.
- Save storage space: With FIBC bulk container bags, you no longer have to use multiple containers with fixed shapes that tend to take up more space than necessary. When you don't need to use them, you can easily stow them.
- Save shipping cost: With their lightweight, bulk bags do not make the goods increase in weight and size compared to using fixed shape containers. This means you'll pay less for the entire load, saving you money on shipping costs.
- Easy transportation: With the current application of machinery, tons of products in bulk bags are moved very quickly by forklifts, making it convenient to arrange and transport goods. Thus, the work progress of the business will be greatly improved.
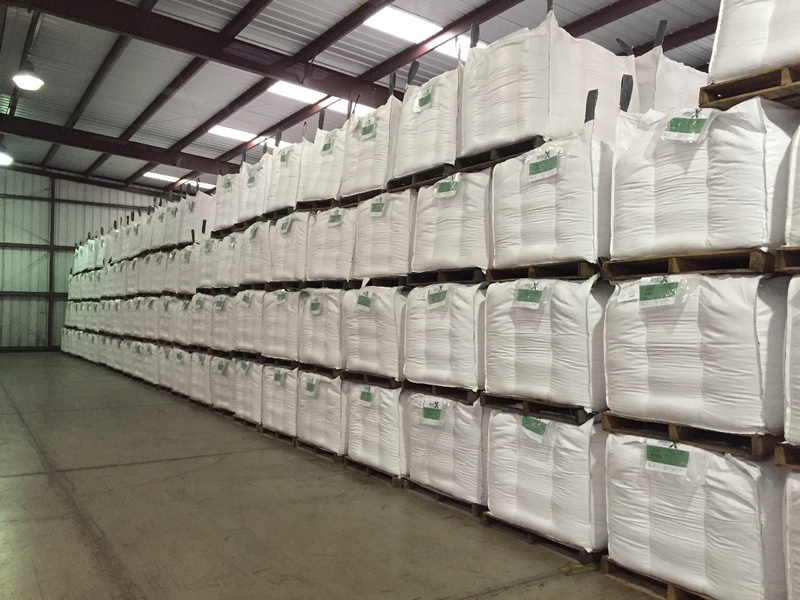
2.2 Cons of FIBC
Besides the advantages of using FIBCs, they have some disadvantages:
- Only forklifts can be used, other forms of loading and unloading are not suitable.
- Goods may be contaminated because of the mesh structure of the bulk bag.
- High cost per large bag if ordered in small quantity.
- If you do not order according to your needs, but buy large bags available, sometimes the large bag shape will not be suitable for your industry.
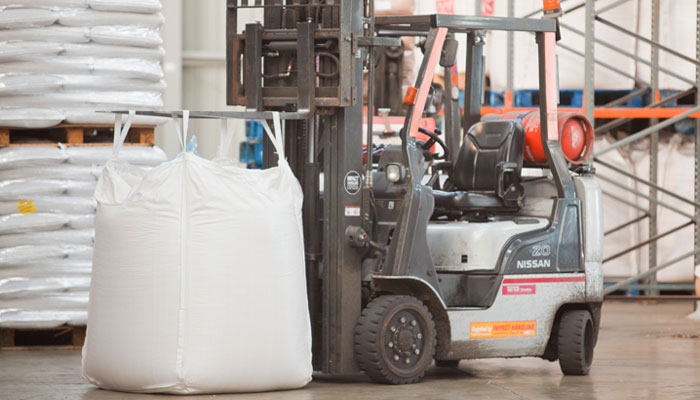
III. Types of FIBC bags
3.1 Type A FIBC bags
Type A FIBC is made of woven polypropylene (woven PP) and does not provide electrostatic protection. Static electricity is generated when materials rub the inner surface of bags as they are filled or emptied.
- Safe for:
+ Transportation of non-combustible products
+ No solvents or flammable gases around the bag
- Do not use for:
+ Transportation of flammable products
+ When there is solvent or flammable gas around the bag
+ Don’t use it in a place where there is a flammable atmosphere
3.2 Type B FIBC bags
Like type A, type B bulk bags do not have a mechanism to dissipate static electricity. Class B FIBCs are made from a plain woven polypropylene fabric with a low breakdown voltage to prevent the occurrence of high energy propagating brush discharges that can ignite dust-air mixtures.
- Safe for:
+ Transporting dry, flammable powders
+ Where there are no flammable solvents or gases
+ The dusty environment with low ignition energy
- Do not use for:
+ When transporting flammable or hazardous materials
3.3 Type C FIBC bags
Type C FIBCs, also known as conductive FIBCs or groundable FIBCs, are typically made from non-conductive polypropylene interwoven with conductive fibers, usually in the form of a mesh. The interconnection of conductive fibers and the connection to the ground during charging and discharging is required for the safe use of bulk C bags.
- Safe for:
+Transporting flammable powders
In the presence of flammable vapors, gases, or dust
- Do not use for:
+ When the ground connection is not available or has damaged
In the presence of a flammable atmosphere with a high ignition energy
3.4 Type D FIBC bags
Type D FIBCs are made from antistatic fabrics and safely dissipate static electricity into the atmosphere to prevent the appearance of sparks and propagating brush discharges.
- Safe for:
+ Transporting flammable powders
+ In the presence of flammable vapors, gases, or dust
- Do not use for:
+ When the surface of the FIBC is contaminated or covered with conductive or combustible materials
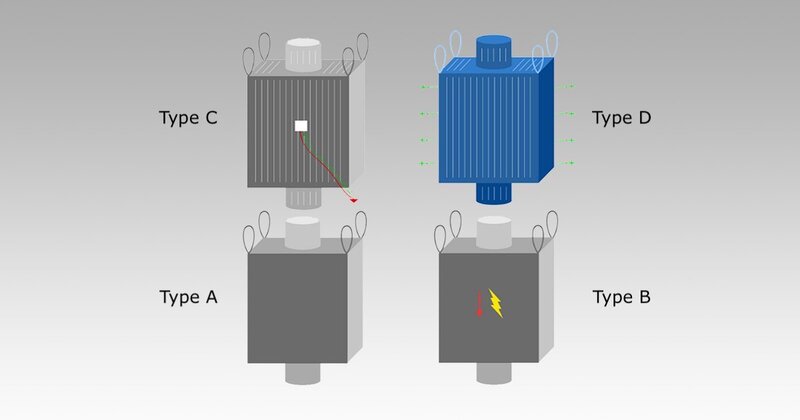
IV. FIBC bulk bags price
4.1 Specifications
The more details you require on FIBC bulk bags, the higher the cost will be. For example, a bag with a fully open top will cost significantly less than a bag with a spout top. And an uncoated bag will cost less than a coated bag.
4.2 Quantity
A large number of bags per order will significantly determine their cost. Ask the supplier about the quantity discount to balance the order quantity. If you plan on using how many bulk bags in a fixed time, you can buy in bulk to get the best price. In addition, buying a large number of bulk bags at once reduces the shipping cost per bag.
4.3 Material cost
The main material for the production of FIBC bulk container bags is polypropylene yarn. And material to make PP yarn is raw plastic. As the cost of plastic increases, so does the cost of PP FIBC bags increase. Therefore, the price of bulk bags depends on the price of raw plastic.
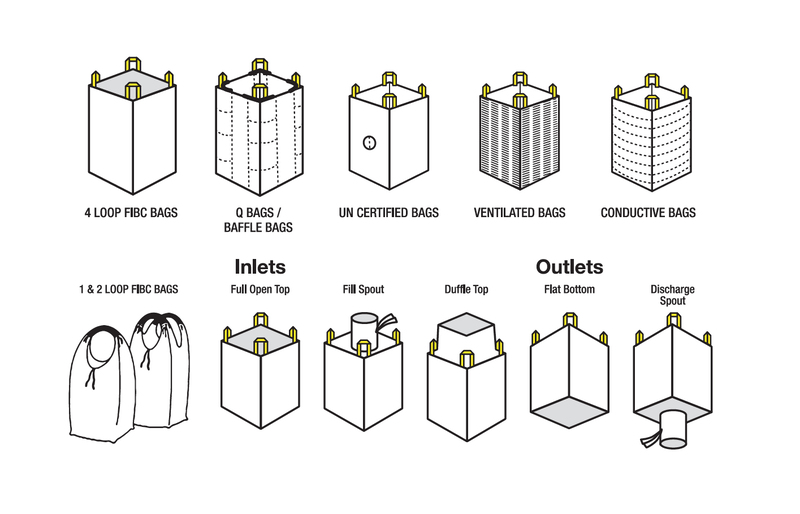
Many forms of FIBC bags
IV. What material is FIBC made of?
FIBC bags are most often made of thick woven strands oriented polypropylene (OPP), coated or uncoated. As a result, FIBC bags have many advantages of polypropylene such as high strength, lightness, and safety, and can be reused.
Nowadays, FIBC manufacturers tend to use PP filler masterbatch as a solution to optimize both cost and properties for woven PP as below:
- Cost-effective: PP filler masterbatch replaces about 40% of the resin in the production of woven PP, and the price of PP filler masterbatch is much cheaper than that of the resin. As a result, the cost of FIBC bags will decrease accordingly, which means that FIBC manufacturers using PP filler masterbatch can sell their products at a more competitive price.
- Improve productivity: The property of PP filler masterbatch is good thermal conductivity. Therefore, it helps to make the machining time of PP woven yarn faster, thereby shortening the production cycle of FIBC bulk bags. In addition, good thermal conductivity also saves energy in the production process.
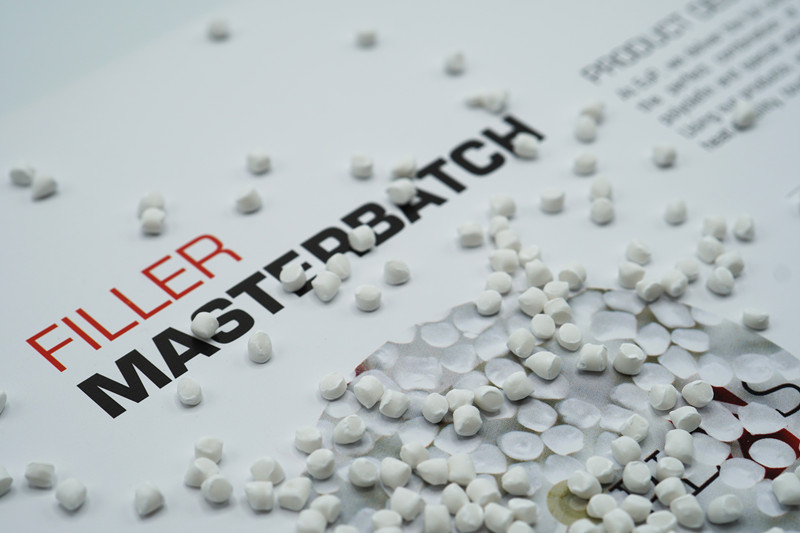
PP filler masterbatch from EuP
- Reduce environmental pollution: As mentioned above, PP filler masterbatch will replace a large amount of primary plastic plus save energy in the production process. All of this helps to reduce the amount of carbon released into the environment.
- Printability: Sometimes FIBC bags need to be printed with the company name and logo depending on customer requirements. Therefore, manufacturers mix PP filler masterbatch into FIBC bags material to enhance the printing ability on the surface of them.
Europe Plastics Joint Stock Company (EuP) is the world's largest filler masterbatch manufacturer providing quality-tested PP filler masterbatch. This product is a solution to help PP woven yarn manufacturers to optimize costs and improve many characteristics of FIBC bags such as brightness, opacity, durability, and printability.
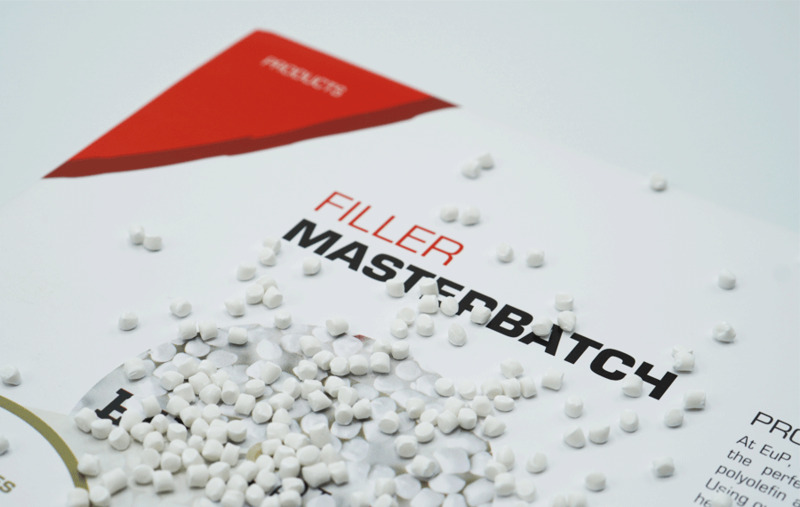
V. FIBC bags manufacturing process
Step 1: Extrusion
The primary PP plastic particles are melted and formed into a tape.
Step2: Weaving
The extruded tape rolls will be loaded into the weaving machine. Here the tapes will be woven into the fabric of the required specifications and will be in rolls.
Step 3: Coating (optional)
PP fabric is coated to make the fabric moisture-resistant. This process is optional according to customer requirements.
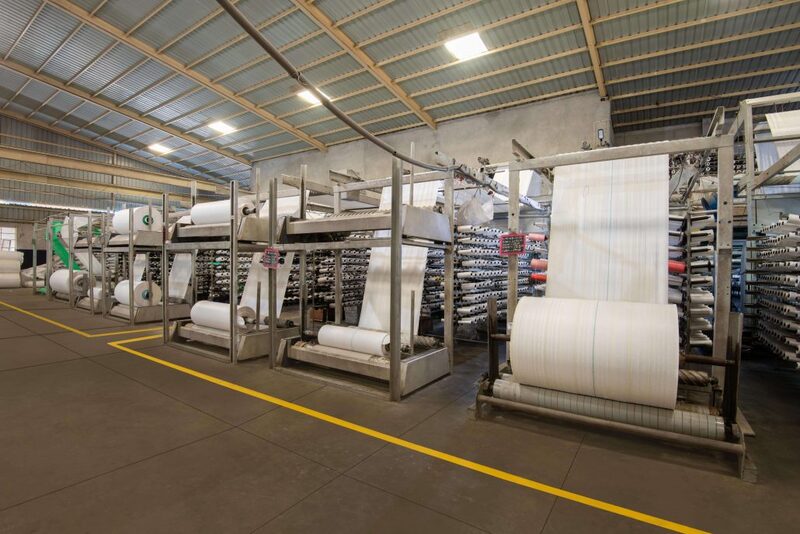
Step 4: Cutting
Woven PP fabric in rolls will be fed into an automatic cutting machine and will be cut into segments according to the required size.
Step 5: Printing
The cut bits will be fed into the heavy-duty printing machine to make the printing on the fabric.
Step 6: Webbing
Heavier PP tapes are woven into webbing which forms the lifting loop of the FIBC bags.
Step 7: Sewing unit
In this step, all components are assembled into a large bag.
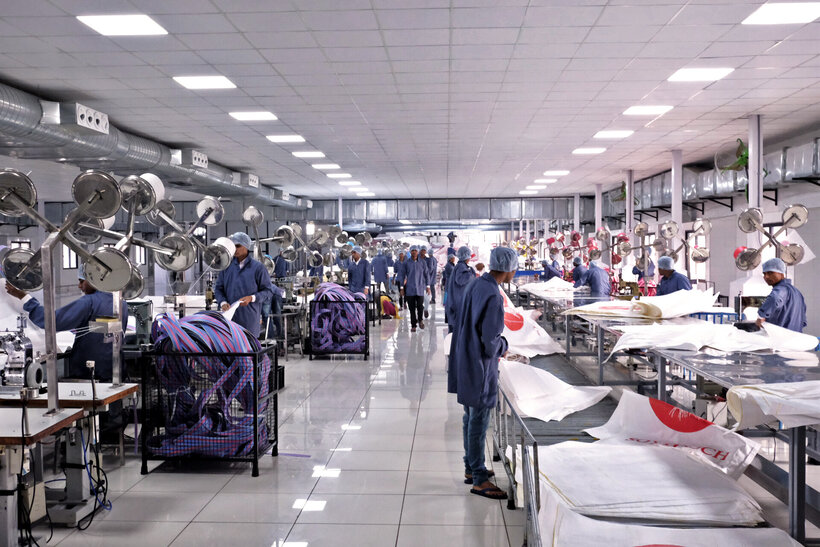
Step 8: Checking
Each large bag after sewing will be checked by technicians to ensure that each bag is of good quality. Also, random FIBC bulk bags will be selected from a specific batch and tested to ensure safe working loads are achieved.
Step 9: Packing and Storage
Here the bags that have been produced will be compressed with the help of a baler, neatly packed, and stored.