Plastics are a common material in many industries, including electronic applications. The types of plastics used in electronics, especially electronic enclosures, are usually lightweight, durable, and resistant to heat and electricity.
Depending on the specific properties, pros, and cons of each plastic type, they are suitable for different applications. If you don’t know what to choose for your product, here is the guide to plastic used in electronics for your reference. Follow along for more!
Read more: What is plastic? Everything you need to know about plastic
1. Why should you choose plastics?
Plastic materials used in electronic gadgets usually have the following invaluable properties, making them a perfect material option.
1.1. Lightweight
Devices are now much lighter than their old generations due to the substantial weight reductions made by the use of plastic. Plastics are generally lightweight. Thus, they lighten the gadgets and use less electricity, reducing running costs and contributing to green environments.
1.2. Durable
Plastics are free of rot and corrosion. They are also acid and oil-resistant. Their toughness and hygienic ability (easy to clean and maintain) make them an ideal option for equipment.
1.3. Electrical insulation
It’s a crucial property of plastics. Since they don’t conduct electricity, they are widely used in various applications. For example, PVC is used to insulate electric wiring, and thermosets are used for handles, switches, and light lifting since they can withstand high temperatures. Plastics can protect users from electric shocks. That’s why they are suitable for housings of food mixers, hairdryers, and electric razors. 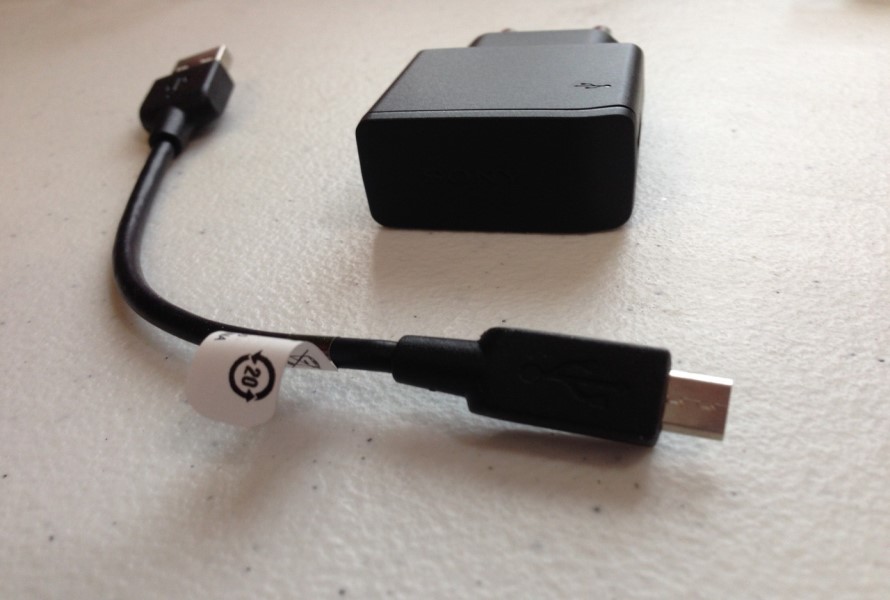
1.4. Heat insulation
Despite the relatively poor conductors of heat, plastics are modified to eliminate the risk of burns. You can see it through the applications of cool-touch toasters, kettles, and deep-fat fryers. Plastics can also be fire-resistant by adding special flame-retardant additives.
1.5. Easy to design
Plastics come in various colors (transparent, translucent, or opaque) and textures (matte or smooth), allowing them to be used in different products, from office tables to kitchen equipment. Plastics can satisfy all designs, including complicated ergodynamic curves. Thus, your tools with plastic designs are easy and safe to use.
1.6. Energy-efficient
Plastics take up only 4% of oil production. Compared to most traditional materials, they use less energy and fossil fuel. Therefore, their prices are cheaper, and they can also contribute to resource conservation.
1.7. Recyclable
Most plastics are recyclable. When they finish their life cycle, with a proper recycling process, they can be used for a second (or more) time. Thus, it can help save raw materials and energy. 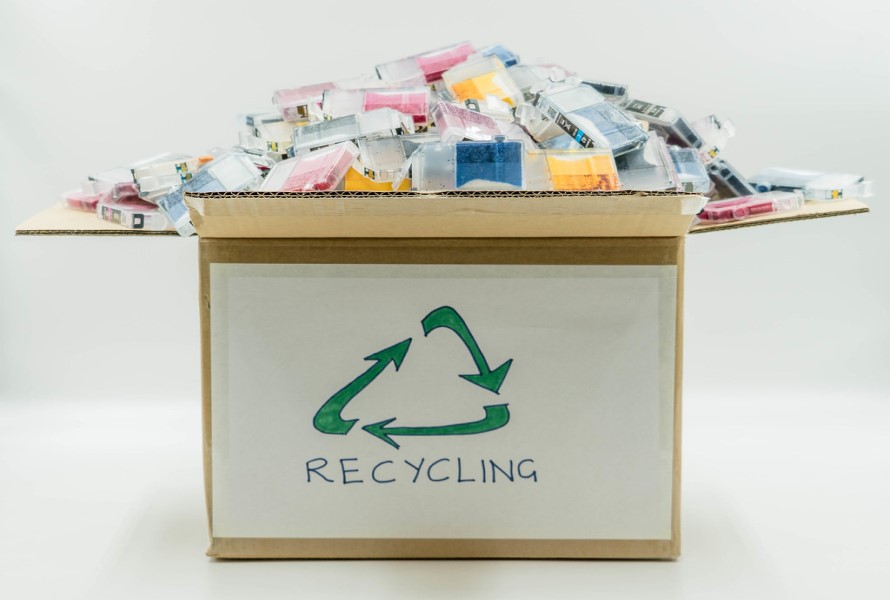
2. Types of plastics used in electronics
2.1. PC (Polycarbonate)
Polycarbonate is a common plastic used in electronics since they are tough, stable, and can be transparent or colored for aesthetic purposes. Since the material is UV light and wrapping resistant, it’s suitable for enclosures, including light pipes and housings, both indoors and outdoors.
However, Polycarbonate can’t resist oil and alcohol-based chemicals. Plus, the BPA element restricts its usage in some applications.
2.2. ABS (Acrylonitrile Butadiene Styrene)
ABS is a polymer blend offering a good and all-around performance for electronic enclosures. It has many advantages, such as flexibility and a great ability to withstand impact, electrical, and several chemicals. Plus, manufacturers can easily combine it with other plastics for better capabilities.
The disadvantage of ABS is it’s less strong when made with thin walls and unsuitable for outdoor applications since its resilience can’t be preserved after long periods of sun exposure.
2.3. PC and ABS Blend (Polycarbonate + Acrylonitrile Butadiene Styrene)
Combining the positive qualities of both PC and ABS, the blend offers the great strength and heat resistance of PC and the flexibility of ABS. You can easily color or tint the material to meet the aesthetic requirements of the final products.
This combination can also be modified by adding impact modifiers or flame retardants, making it suitable for indoor or limited outdoor plastic electrical enclosures that require regular maintenance with a cleaning agent.
2.4. PBT (Polybutylene Terephthalate)
Another plastic used in electronics is PBT or Polybutylene Terephthalate. It has many outstanding features, such as resistance to physical, electrical, and chemical elements. It’s durable and can withstand types of stress, making it an ideal option for high-temperature applications.
One minus of this material is its crystalline structure with the shrink rate that prevents the manufacturers from switching classes easily.
2.5. PPO (Polyphenylene Oxide)
This crystalline thermoplastic is resistant well to high heat, preventing it from distortion while exposing it to a wide range of temperatures. Thus, it provides good dimensional stability and relative toughness.
Besides, the heat, water, and electrical resistance make it a suitable material for housings with frequent water contact or devices that often get hot easily. However, PPO’s ability to resist UV light and oxidation is weak.
2.6. Polyphenylene Ether (PPE)
PPE blends PS and PPO with improved mechanical, thermal, and electrical properties. It’s often used for sturdy and resistant housings, including transformers or relays. The material is corrosion-free and difficult to melt.
Its advantages show up when overexposed to UV light. The product’s color will be faded; thus, using it for outdoor enclosures is not a good choice. Plus, PPE is quite expensive and is not the preferable option in some cases.
2.7. PA (Polyamide)
PA is tough and wear-resistant. This great electrical insulator can slide well, making it a perfect choice for sliding and moving parts of the enclosures, such as power tool housings.
However, PA can’t be used for enclosures that need waterproofing because it does not have this ability and can even absorb moisture. Plus, it’s affected by alcohol and acids, so you should not use it for enclosures requiring regular cleaning.
2.8. SEBS (Styrene Ethylene Butadiene Styrene)
This thermoplastic elastomer is elastic, smooth, and comfortable to touch. Therefore, SEBS is suitable for handheld electronic cases. It also can replace PVS in small applications, such as small toys.
The material does not absorb water and heat and can protect electronics from chemical substances, including cleaning agents and alcohol. However, SEBS is quite expensive and can be rare to find in some regions.
2.9. PMMA (Polymethyl Methacrylate, Plexiglas)
The infrared transparency makes PMMA one of the types of plastics used in electronics, such as remote control handsets or scanners. The thing is, this material is brittle and can’t withstand friction and impact.
Thus, to make the material usable and enhance its quality, some injection molders tend to combine PMMA with other materials, such as ABS.
2.10. Acrylic
Acrylic is an alternative for PC due to its transparent attribute. However, its usage is selective as the material does not withstand impact well. Thus, manufacturers always need to add additives and modifiers to enhance it.
If you insist on using Acrylic, you can still improve its performance with modifiers and additives since the material interacts well with them.
3. EuroPlas - Plastic manufacturers and suppliers for electronic applications
As the leader in the masterbatch field, EuroPlas offers a full-function-in-one-material solution for your electronic end-products. Our engineering compounds are high-quality, flexible, and can satisfy all safety requirements for electronic applications. Some of our highlighted products include ABS Antistatic compound and PP conductive compound.
3.1. ABS Antistatic compound
It’s a combination of ABS resin and an antistatic additive and has the ability to dissipate static electricity. The blend can provide electrical conductivity and, at the same time, maintain ABS’s mechanical and processing properties, such as excellent dimensional stability and high impact resistance. ABS Antistatic compound is suitable for electronic applications such as electronic components, pallets, mobile chargers, power sockets, and earphones.
3.2. PP conductive compound
The blend mixes PP resin and carbon black conductive. Conductive polypropylene pellets are lightweight and simple to work with throughout the injection molding process. Our compound has higher stability compared to standard PP and improved electrical conductivity. Therefore, it has many applications, such as manufacturing electronic components, cable jackets, and electrical equipment housing.
If you’re still not sure what types of plastics you should choose, contact EuroPlas. Our professional consulting team is always ready to help.