The Optimum Filler Loading in Raffia
- Unlike in numerous other PP/HDPE applications, expenses can be diminished by filler stacking in Raffia Tape. There is a compulsion to continue expanding filler loadings as business sectors turn out to be increasingly aggressive.
- Care ought to be taken not to exasperate the MFI picked by elevated amounts of Filler Masterbatch.
- Filler expansion levels for a specific application ought to act naturally administrative.
Self Regulatory contemplations for Filler loading
- The execution necessities of the end utilize ought to be obviously comprehended. Tests like Loaded Drop Test, Bursts quality, Stitch capacity ought to be set up to mirror the execution necessities.
- Filler Masterbatch levels ought to be precisely tried different things with to locate the ideal %.
- Ash tests like BIS-4985 could be detailed for basic applications like Bulk Sacks/Jumbo Bags.
Outline for Filler loading in Raffia
- The past computations and discoveries are similarly valid for PP Raffia. Comparative contemplations are substantial when Talc or mixes of Talc and CaCO3 are utilized.
- These investigations are hypothetical and take after the thinking of Volume Costs. It is fascinating to know how close these discoveries contrast with genuine Raffia industry encounter.
A few expressions of alert of Filler loading in Raffia
We, at EuP, comprehend that over the most recent couple of years, there have been purposeful advances taken to diminish the Filler expansion costs in Polyolefins. It is very certain that when contrasted with the PVC Industry, the high intensifying expenses is a noteworthy obstruction to filled Polyolefins from finding more extensive applications and piece of the overall industry. Just if Compounding costs descend radically and less expensive GCC is utilized is there any possibility of Volume expenses of
Filled PP/HDPE to be lower than the base Polymer
The course taken is very stressing. It is outstanding that Plasticised PVC Compounding is effectively done on single screw extruders, some of which are very unsophisticated, and accordingly exceptionally shabby. The capital expenses are a small amount of co-turning Twin Screw extruders and intensifying Rs/kg cost for Plasticised PVC is in the low single digits. It appears a comparative course is currently being utilized for filling Polyolefins, basically HDPE for the Raffia tape and Blown film industry.
One must comprehend that in Plasticised PVC, the filler is as of now very much scattered in the High Speed Mixer/Cooler Mixer before being encouraged to the Single Screw extruder. The extruder is basically to melt and drawing the PVC through the bite the dust for pelletising. The initiated blending activity of the single screw is sufficient to finish the homogenization.
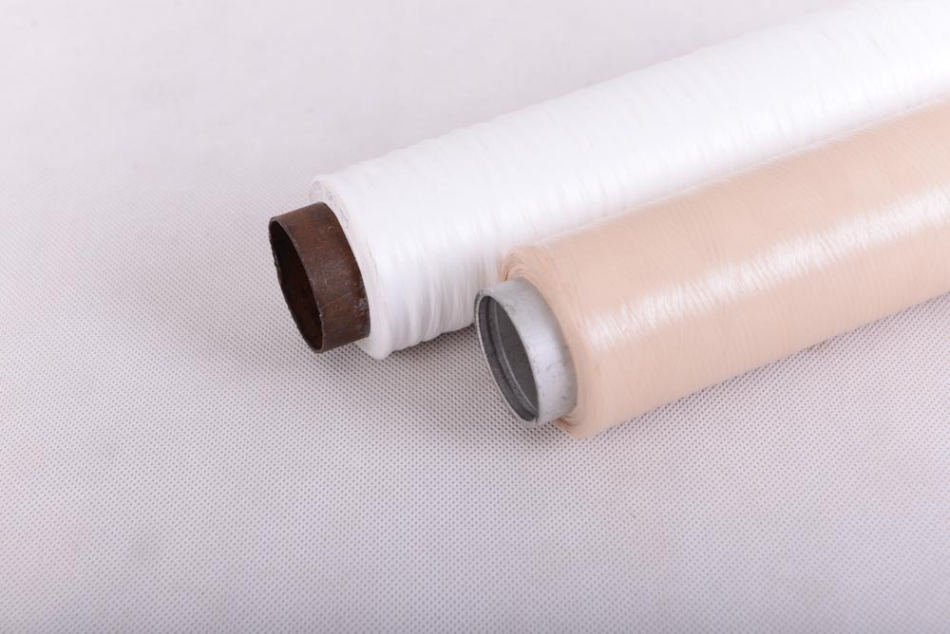
With HDPE and generally high filler loadings as required in a filler masterbatch, a solitary screw extruder, even with blending zones can never come even near the serious blending abilities of Co-turning multi-fragmented Twin Screw Compounders or Buss Ko-Kneaders.
As the single screw extruder is so considerably less expensive, many have been squeezed into administration to compound Polyolefins with high filler levels, while as yet holding the exacerbating expenses down to Rs 6-7/kg (US$130-150/MT). In the event that scattering isn't appropriate, numerous passes are turned to make up for the uncalled for blending. This is foolish as rehashed warm history eats into the Stabilizer and Antioxidant levels consolidated by the polymer maker. There is each shot that the filler masterbatch will lessen the life of the completed item it is utilized for.
Filler masterbatches are utilized at considerably larger amounts than Color Masterbatches, and nearness of debased polymer in the masterbatch will antagonistically influence item quality. I would ask the individuals who are exacerbating HDPE with filler on single fasten extruders different goes to add extra Antioxidants and stabilizers to make up for corruption. With Compounding costs on present day twin Screw lines plunging to Rs 10/kg, it doesn't appear to be advantageous to construct a filler masterbatch unit in light of single screw extruders only for another Rs.3-4/kg decrease. Maybe the main impetus with littler business people is the lower capital expenses of Single screw lines.
Indeed, even with higher Polymer costs, bring down Filler and Compounding costs, as indicated the volume cost are as yet not good when contrasted with unfilled polymer. There is an expanding pattern for utilizing Talc filled filler masterbatches for
HDPE and even LLDPE Blown film and it is hard to comprehend why this is going on.
I am persuaded that if the Film or the packs made thereof are sold by Volume, filler expansion would not decrease costs, even at higher Polymer and lower Filler costs. Accepting that the film rolls are sold in meters of a predefined measure, it is being sold by Volume. Sacks sold per bit of a settled check (thickness), again it is sold by Volume. We have seen that in Polyolefins, Volume cost does not go beneath the unfilled Polymer levels even at high filler loadings. In this way the processor might be hushed by the way that the filled compound he is expelling is of a lower cost in Rs/kg. terms, his item weight will go up for the settled volume units he offers. The extra material cost will exceed whatever investment funds he was expecting over unfilled item.
In the event that the film is being sold by weight premise, it is another issue. Here the client endures. He gets less meters for a similar measure film as thickness runs up with filler. The meterage lessening % will be more than the value markdown offered with Talc filled movies. I would ask for the business pioneers to check this pattern from developing in any way and instruct their clients on the Volume Cost idea with the goal that they are not misused by corrupt rivalry.