Bubble wrap may currently be the most common packing medium, second only to cardboard boxes. Did you realize, though, that bubble wrap wasn't even created for packaging? What was bubble wrap invented for? In actuality, it was designed for a purpose that has nothing to do with shipping.
In today’s article, we shall look at the story behind bubble wrap. From who created bubble wrap to the bubble wrap manufacturing process, here’s all you need to know about this excellent creation!
Related:
- What are Laminating Pouches Made of?
- Types of FIBC bags and their manufacturing process
- Cement Plastic Bags Manufacturing Process - The Ultimate Guide
I. What was bubble wrap invented for
1. Origins of bubble wrap
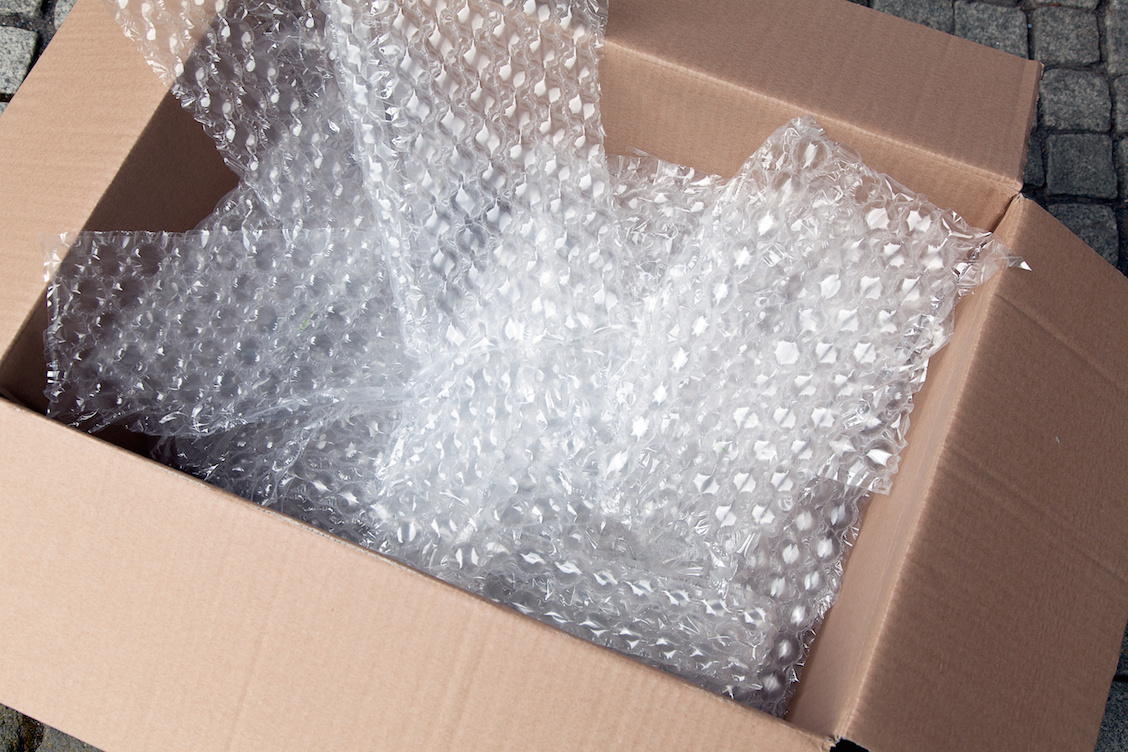
In 1957, Alfred Fielding and a Swiss inventor, Marc Chavannes are the two people who created bubble wrap in Hawthorne, New Jersey. But neither was attempting to create a thing that would serve as packaging. Instead, they sought to produce textured wallpaper.
The initial bubble wrap manufacturing process was done by tacking two shower curtains together in a way that would trap air bubbles, giving their wallpaper a textured appearance. This wallpaper concept wasn't very successful.
They then started looking for a different use for their product, unfazed. Three years after bubble wrap's invention, Frederick W. Bowers, a marketer for the company that creates bubble wrap, Sealed Air, finally came up with the ideal use.
2. Characteristics of bubble wrap
A packaging material known as "bubble wrap" is made up of tiny air bubbles that are intended to cushion and safeguard delicate items.
Many individuals are curious about the science behind bubble wrap. In a nutshell, the air pockets that form bubble wrap are sandwiched between two layers of polyethylene film. Fragile products are shielded from harm by the air bubbles during shipping or relocation. Bubble wrap is available in sheets, rolls, and even integrated into postal envelopes.
They are highly recommended for packaging thanks to their excellent properties:
- Lightweight
- Transparent
- Resistant to moisture
- Prevents abrasion on surfaces
- Simple to use
- Excellent insulating qualities
- Flexible and powerful
- Many uses
- Resistant to water
- Simple to trim using hand tool
There are a few common questions for people when bubble wrap is used for packaging.
- Is bubble wrap anti-static?
When using conventional bubble wrap, it can produce static, which can harm electronics such as motherboards and computer chips. For this reason, selecting anti-static bubble wrap is crucial when shipping electrical goods.
- Is bubble wrap a conductor or insulator?
Natural insulator bubble wrap. The layer of trapped air within the bubbles creates a shield that keeps warm air within and keeps out the unwelcome cold.
II. What material is bubble wrap made of?
1. Main raw material
So what material is bubble wrap made of? The main components of bubble wrap are thin plastic sheets or films manufactured from polyethylene and polypropylene resins.
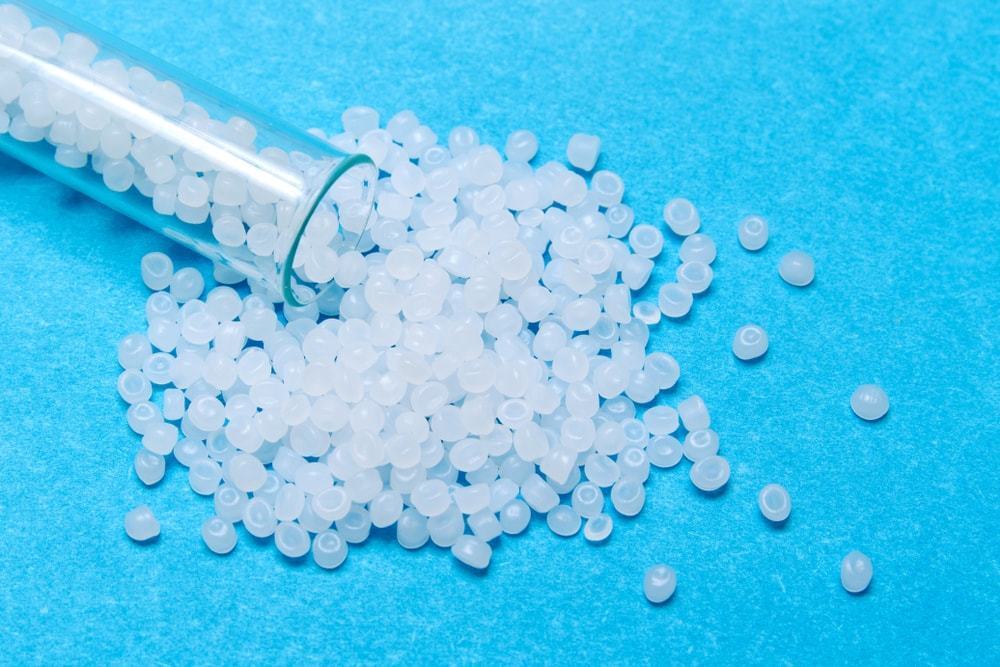
Because they function effectively and are reasonably priced, these resins are frequently utilized. They may be molded into durable, pliable films having the capacity to contain air without leaking. These resins are also thermoplastic materials, making it simple to melt and shape them.
Given that the plastic sheets could be warmed during manufacturing, this characteristic is crucial. The top and bottom sheets of the cushioning laminate may be made from several types of resins to give it unique qualities. For instance, one layer may be built of a stiffer material to improve the rigidity of the final product.
2. Additives
The basic polymers are blended with a range of additives to change their characteristics and make processing easier for creating the polypropylene or polyethylene films.
These additives include plasticizers, heat stabilizers, UV light absorbers, coupling agents, and strength modifiers that strengthen the binding between the polymer and the filler, as well as lubricants and plasticizers that regulate the flexibility of the resin mix.
Additionally, antistatic chemicals are provided to lessen static electricity accumulation, and biocides may be added to prevent microbiological development.
III. Bubble wrap manufacturing process
Three basic phases make up the process for bubble wrap production: plastic compounding and sheet extrusion, lamination, and finishing processes.
Step 1: Plastic compounding and sheet extrusion
Compounding
Bulk plastic resin is bought from a supplier that has compounded it to the manufacturer's specifications. The heated polyethylene resin is combined with the aforementioned ingredients during this compounding procedure.
The mixture is then melted and shaped into tiny pellets with a diameter of 0.125 in (0.3175 cm). These pellets are first added to an extruder, a molding equipment used in the production process.
The pellets are dropped into a hopper at one end of the extruder. The pellets are fed into a long, heated barrel from this hopper. The plastic is propelled forward by a screw mechanism built inside this barrel. A stainless steel sheeting die that can create sheets up to 10 feet (3 meters) wide is located at the opposite end of the barrel.
Extrusion
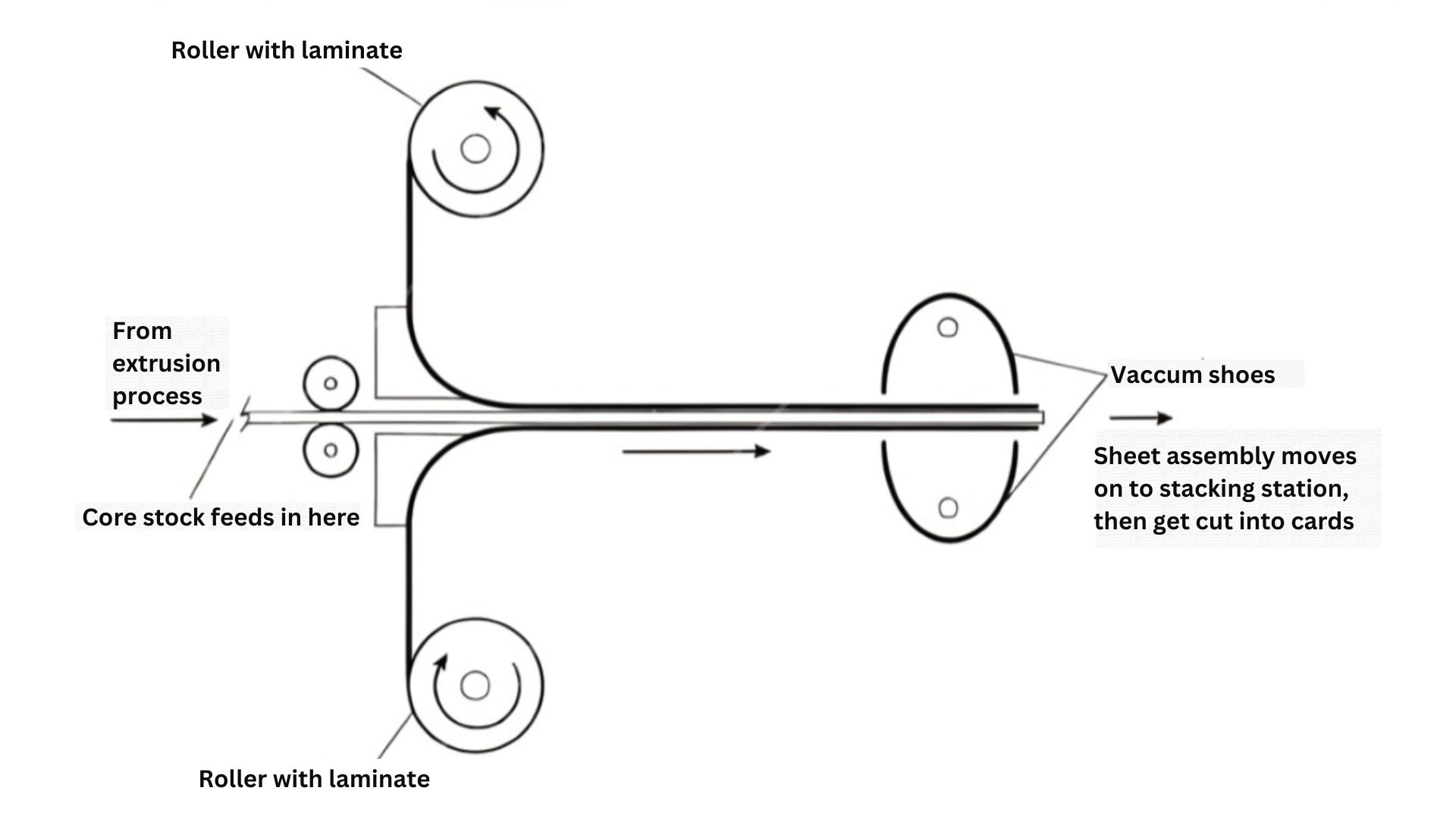
As the resin travels down the heated barrel, it begins to melt; by the time it reaches the end, it is readily pushed through the die's aperture. The molten resin is molded into a sheet as it is forced through the die and is then treated further.
The sheet may be laminated to another layer right away while it is still heated, depending on the procedure, or it may be cooled first and laminated afterward. In both cases, the sheet is extruded and then goes through a three-roll finisher or three-roll stack of stainless steel rollers.
These water-cooled rollers have a diameter of 10-16 in (25.4-41 cm) and are internally cooled. The top two rollers' meeting place, the nip, is where the plastic sheet enters when it leaves the die. The rollers' action draws the sheet in as it is fed through the top, middle, and bottom rollers.
The sheet is kept at the proper size and form while being cooled by these rollers. The sheet enters the second set of rollers known as pull rolls after passing through the three-roll stack, dragging the sheet through the remaining steps of processing..
Step 2: Lamination
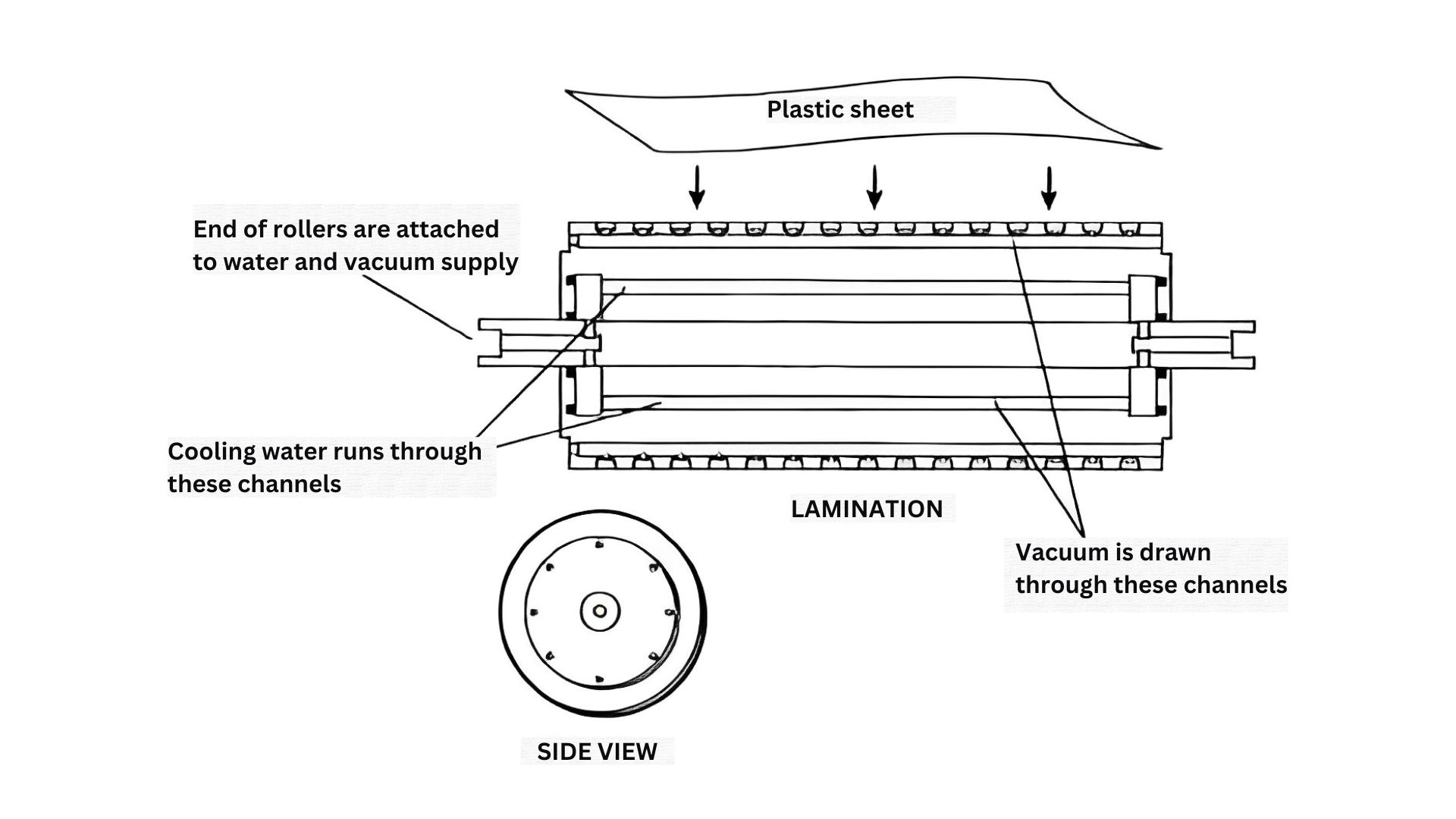
Laminating
The method used to bond the two sheets together and capture air bubbles is called lamination. By stretching or perforating the substrate sheet in a certain manner, you may arrange these bubbles uniformly throughout the sheet's face. The sheet will hold air and develop distinct pockets as a result of these uniformly distributed deformations.
Heat is necessary to soften the plastic during the deforming of the substrate sheet. As said, this procedure can be carried out while the sheet is still warm after extrusion, or it can be done later after it has been warmed and molded.
The softened sheet can then be shaped with bubbles by placing it in contact with a forming surface. This surface might be a plate or a roller with protrusions distributed in the desired ways. The plastic is molded into the required shape when the molten sheet comes into contact with the forming surface.
Creating air pockets
One technique employs a revolving belt as the forming surface to produce these air pockets. There are several holes all around this belt. Suction is delivered from a vacuum source to the gaps in the belt as the substrate sheet travels along it. The plastic stretches into the belt's perforations as a result of the air pressure difference, forming a number of pockets.
A molding plate is used as the forming surface in a different technique. The plastic sheet, through which a vacuum is drawn, is placed into position beneath this plate. A molded sheet with the appropriate uneven surface is created when the sheet is forced to conform to the bumps in the mold plate by the suction.
In a third technique, the air pockets in the plastic are created using a revolving molding cylinder.
Sealing
The substrate sheet and a second sheet are fed together through a set of laminating rollers after the air pockets have been created using one of the processes mentioned above. To guarantee that bonding will take place, at least one of the sheets needs to be at the right temperature. The sheets are sealed together by pressure and heat, and any air bubbles are kept in place.
Step 3: Finishing
Additional operations
The sheets are chilled, if necessary, using open or forced air systems once lamination is finished. Air may blow over the sheet from above and below. Water cooling is occasionally used, although this can lead to cleaning issues and needs more drying time. Other specialized procedures can be needed, depending on the type of cushioning laminate being produced.
For instance, certain cushioning laminates have an adhesive coating applied to one side. Others are cut into envelope shapes to protect delicate tiny things. These extra procedures may be carried out either before or after the lamination process, depending on the processing involved.
Completing
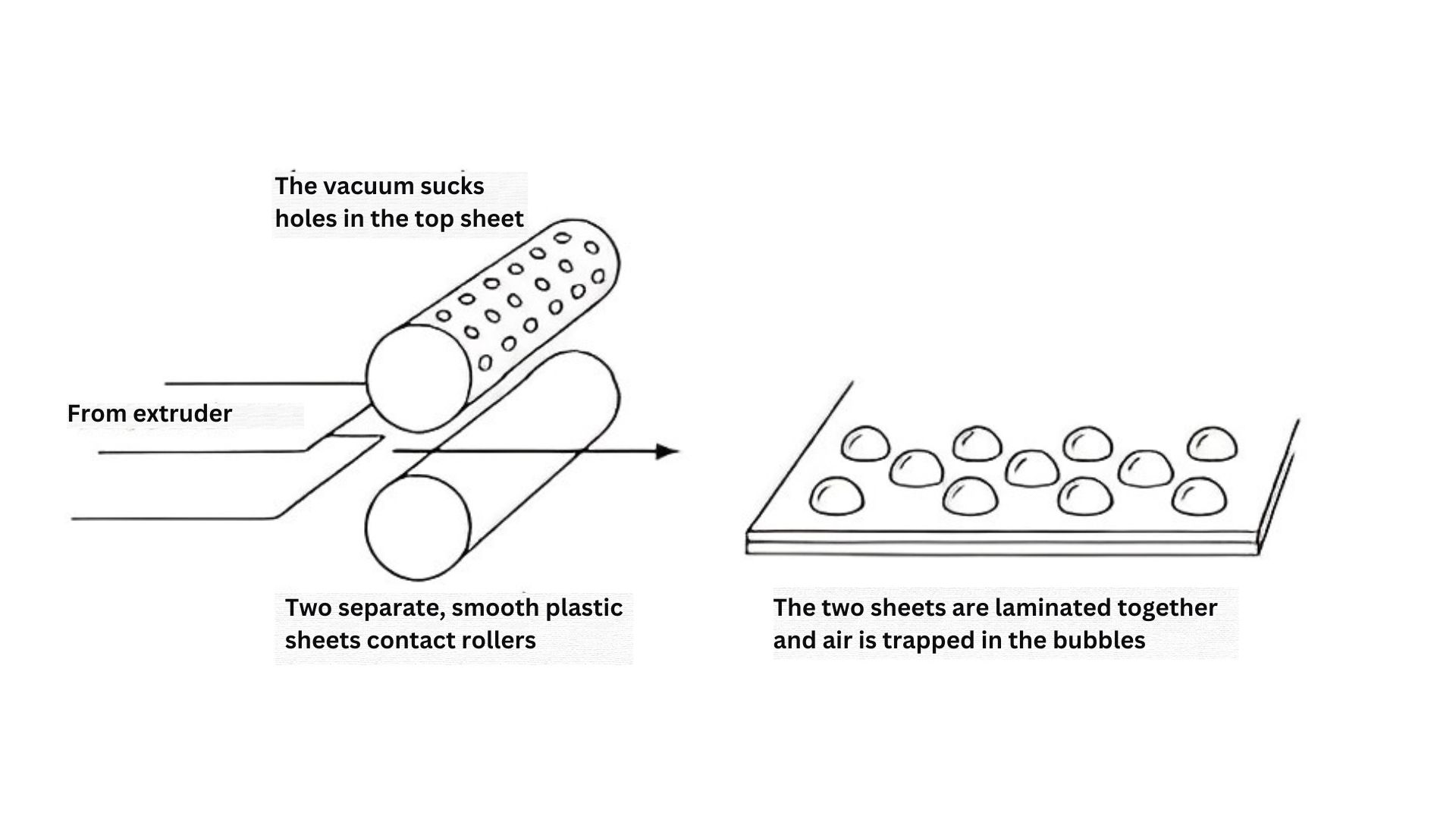
The sheet material is trimmed to the required size when the cushioning laminate is finished. The uncut wrap may be processed in this manner as part of the first processing, or it may be kept in giant rolls and cut to size afterward. Slitting, also known as cutting, is carried out using specialized blades that can slit through thick layers of plastic. The laminate may be packaged and marketed in sheets or rolls.