Corrosion resistant plastics are essential materials in industries that face harsh chemical environments and exposure to moisture, acids, and bases, which can be detrimental to traditional materials. These plastics provide excellent durability, longer lifespans, and cost-effective solutions compared to metals. In this article, we will explore the key features that make plastics resistant to corrosion, provide a comprehensive list of corrosion-resistant plastics, and examine their industrial applications.
1. What Makes a Plastic Corrosion Resistant?
Plastics are naturally resistant to many corrosive substances, but not all plastics have the same level of corrosion resistance. This ability largely depends on the chemical structure of the plastic, particularly its resistance to reactions with acids, bases, salts, and other chemicals. Unlike metals, which corrode through oxidation or chemical reactions with their environment, plastics typically do not undergo these processes, making them highly suitable for harsh environments.
Several factors contribute to the corrosion resistance of plastics:
- Chemical Composition: Plastics made from certain polymers, such as fluoropolymers, are highly resistant to most chemicals. The specific arrangement of molecules in these plastics prevents chemical reactions that could degrade or weaken the material.
- Low Permeability: Some plastics, such as Polyvinylidene fluoride (PVDF), have low permeability, which means it does not allow gases or liquids to pass through easily. This characteristic helps prevent chemical reactions within the material.
- Non-reactivity: Many corrosion-resistant plastics are non-reactive, meaning they don’t interact chemically with the substances they come in contact with. This property is essential for applications in industries like chemical processing and oil and gas.
2. A Completed List of Corrosion Resistant Plastic
In this section, we will cover some of the most popular corrosion-resistant plastics used in various industries. These materials are valued for their ability to resist chemicals, moisture, and environmental degradation.
2.1. PVC and Chlorinated PVC
These two extremely popular plastics make plumbing and much of the industrial sector possible with ease and at an inexpensive price. PVC is the third most utilized polymer in the world and has earned its place in the construction and plumbing industries. As it can replace rubber in many aspects, it’s also used for jobs such as electrical cable insulation, flooring, leather, phonograph records, and signs.
By using plasticizers, PVC is made softer for these specific applications. CPVC is the chlorinated version of PVC known as thermoplastic. It has greater flexibility than PVC, which makes it more durable and allows it to withstand elevated temperatures better. These plastics are perfect for cold and hot delivery pipes and holding potable water, which is why they are commonly seen in the plumbing industry.
.jpg)
PVC pipes
2.2. UMHWPE
As a high-volume mass version of polyethylene, UMHWPE is the ideal solution for plastic parts that require corrosion resistance, high load or capacity abilities, or impact resistance. UHMWPE is often cited as the toughest thermoplastic currently available on the market as it features strength and abrasion-resistant properties that match or exceed carbon steel.
2.3. PTFE
This polymer is a jack of all trades. It’s hydrophobic, extremely dense in structure, and can tolerate high temperatures exceptionally well. Due to these properties, PTFE has a wide range of applications that it can take on. However, it’s infamously known for being unable to stick to surfaces. It will not rust or decompose, so it doesn’t age or become brittle. It works well for electrical insulation. It resists weathering, and it can be made for food-grade functions.
Lastly, it’s highly affordable as it has one of the best performance-to-price ratios. Most often, commercialized PTFE has been used as Teflon. This ideal material, with a high chemical, thermal, and electrical resistance, makes for excellent cookware where it is being used to a high degree. In fact, as it is one of the most durable substances to cook with, Teflon is very popular in cooking circles.
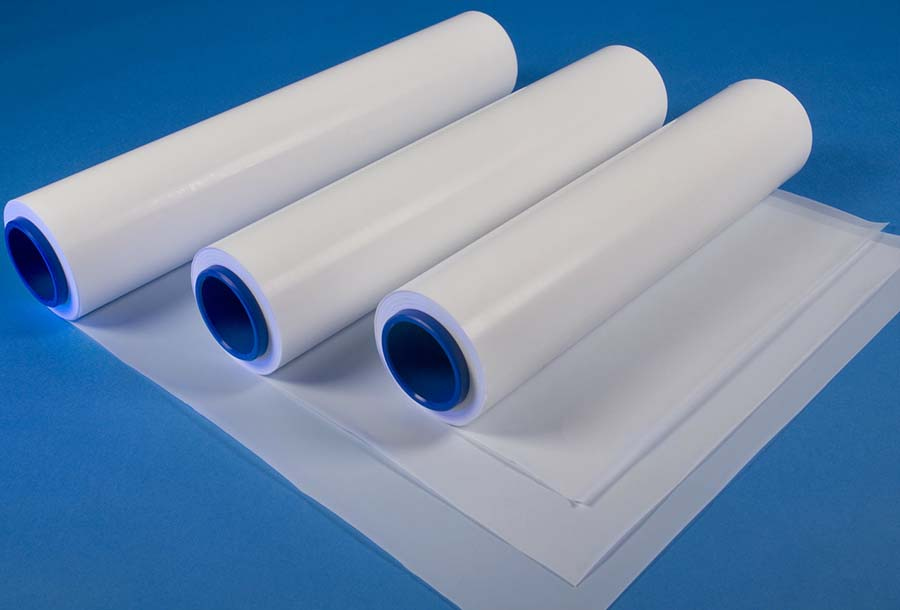
PTFE Plastics
2.4. High-Density Polyethylene
Moving into more complex polymers, we have HDPE, another thermoplastic like PVC and CPVC. Due to its high corrosion resistance properties, this polymer, also referred to as alkathene or polythene, is used for producing plastic bottling, piping, plastic lumber, and geomembranes. You will often see a recycling symbol containing the number two on HDPE plastic products. This marking, known as a resin identification code, signifies that the product is recyclable up to two times in its life. As one of the most consumable plastics, everyday household plastic items are created using this particular polymer. Anything from cleaning material containers to food-grade storage and food-grade wrapping items consists of polyethylene.
.jpg)
HDPE Pipes
2.5. PVDF
PVDF, or polyvinylidene fluoride, is an excellent choice for any high-corrosion application as it resists chemicals, electrostatic, UV and other radiation, flames, and smoke. PVDF parts are weldable, making them versatile inclusions in your final assembly, and these components are used in projects across industries. It is available as a homopolymer for high-strength capabilities and improved heat deflection or as a copolymer for greater impact and stress crack resistance.
3. Applications of Corrosion-Resistant Plastics
Corrosion-resistant plastics are utilized across various industries, including chemical processing and healthcare, due to their durability, chemical inertness, and cost-effectiveness. Here’s a closer examination of their applications in different sectors:
3.1. Chemical Processing
The chemical industry is one of the largest consumers of corrosion-resistant plastics. In environments where strong acids, bases, solvents, and other chemicals are present, plastics such as PTFE, PVC, and PP are used to manufacture pipes, tanks, and seals. These plastics offer excellent resistance to chemical attacks, extending the lifespan of equipment and reducing maintenance costs.
3.2. Water Treatment
Corrosion-resistant plastics like HDPE and PVC are widely used in water treatment facilities for piping, valves, and tanks. These materials resist the corrosive effects of chemicals used in water purification, such as chlorine and ozone, ensuring long-term durability.
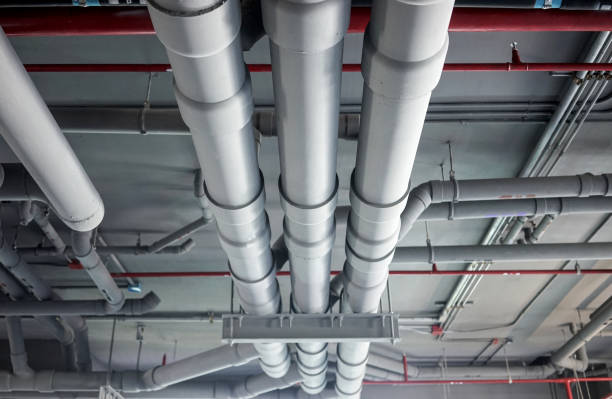
PVC Piping Systems
3.3. Oil and Gas
In the oil and gas industry, materials are exposed to harsh chemicals, extreme temperatures, and abrasive conditions. Plastics such as PEEK and PVDF are used in various applications, including pumps, seals, and pipe linings, due to their resistance to corrosive chemicals and mechanical stress.
3.4. Healthcare
In the healthcare industry, corrosion-resistant plastics are critical for maintaining the cleanliness and durability of equipment. Materials like ABS and PP are used to manufacture medical devices, trays, and containers that need to withstand sterilization processes and chemical exposure.
3.5. Automotive
In the automotive industry, corrosion-resistant plastics play a crucial role in ensuring the longevity and durability of vehicle components. Materials like Nylon, ABS, and PEEK are widely used for parts exposed to harsh chemicals, oils, and fuels. These plastics offer excellent resistance to corrosion, ensuring that critical components such as fuel system parts, bearings, gears, and electrical connectors remain durable and reliable.
Additionally, corrosion-resistant plastics help reduce vehicle weight, improving fuel efficiency while maintaining structural integrity. Their ability to withstand extreme temperatures and chemical exposure makes them an essential choice for modern automotive manufacturing.
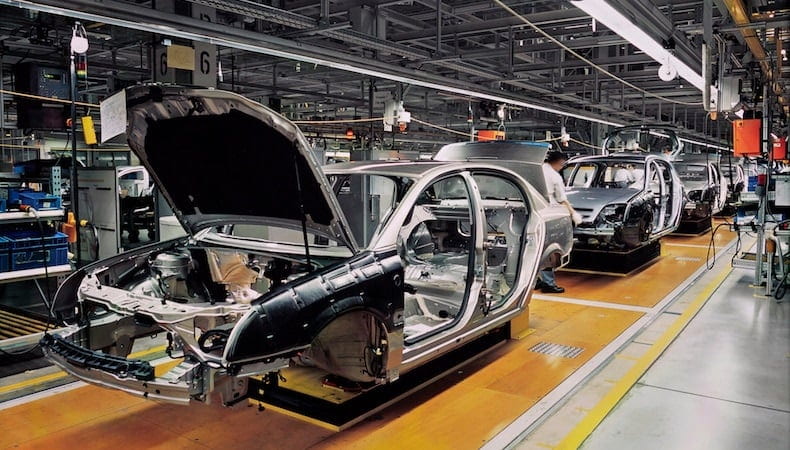
Using Corrosion-Resistant Plastics In Making Car Covers
3.6. Aerospace
In the aerospace industry, corrosion-resistant plastics are essential for reducing weight and ensuring durability in extreme environments. Materials like PEEK and PTFE are commonly used in various aircraft components, including insulation, gaskets, and structural parts. These plastics offer high resistance to corrosion from chemicals, moisture, and temperature fluctuations, which is crucial in aerospace applications.
Their lightweight nature helps reduce overall aircraft weight, improving fuel efficiency and performance. Additionally, the high strength and reliability of these plastics ensure they can withstand the intense pressures and demanding conditions experienced during flight, making them vital in modern aerospace engineering.
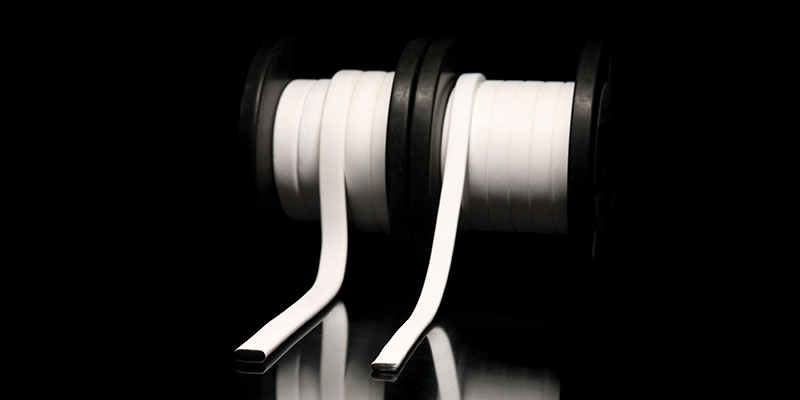
PTFE Tapes In Aerospace
4. Conclusion
In short, corrosion-resistant plastics are essential in modern manufacturing and industrial processes. Their chemical resistance and ability to withstand harsh environments make them versatile solutions across various industries. As technology progresses, new plastics and enhanced corrosion-resistant formulations will further expand their applications.
Choosing the right corrosion-resistant plastic is crucial for durability, efficiency, and cost savings, whether you're in chemical processing, oil and gas, automotive, or healthcare. These plastics present an attractive alternative to metals, offering longevity, resistance, and flexibility in challenging environments.
5. About EuroPlas
EuroPlas is a leading manufacturer of high-quality plastic materials, including a wide range of corrosion-resistant plastics for industrial applications. With a commitment to innovation and sustainability, EuroPlas provides customized plastic solutions that meet the unique needs of various industries. Our company has the expertise and technology to deliver top-quality products that exceed industry standards. Some products of EuroPlas include: bioplastic compounds, color masterbatch, plastic additives, engineering plastic compounds, filler masterbatch and bio filler.
For more information and samples, please contact us HERE!