Polystyrene, commonly known as PS, is a transparent plastic that finds applications across various industries. Ranging from solid products to foam materials, the different types of polystyrene offer versatile solutions for a wide array of needs. Since its debut in 1941, polystyrene has become a staple in everyday life. In this article, we will explore the various types of polystyrene, empowering consumers to make informed choices for their future purchases.
Read more: Polystyrene vs Polypropylene: What Are The Differences?
1. Overview of Polystyrene
Polystyrene is a versatile and widely utilized amorphous plastic that plays a crucial role in the production of numerous consumer goods. Characterized by its lack of a distinct melting point, polystyrene exhibits a broad melting temperature range, allowing it to be easily blended with other similar polymers. This feature enhances its adaptability and enables the creation of innovative plastic components with superior properties.
Chemically, polystyrene is represented by the formula (C8H8)n, where "n" indicates the number of repeating styrene units in the polymer chain. It is synthesized through the polymerization of styrene monomers, resulting in long chains that give polystyrene its unique characteristics.
In its solid form, polystyrene is used to manufacture a variety of products, including automotive parts, household appliances, flower pots, and toys. When transformed into foam, commonly referred to as polystyrene foam, it serves critical functions in electrical insulation, protective packaging, and food containers. Its use in food packaging is particularly noteworthy, as it helps extend the shelf life of perishable items while remaining cost-effective compared to alternative materials.
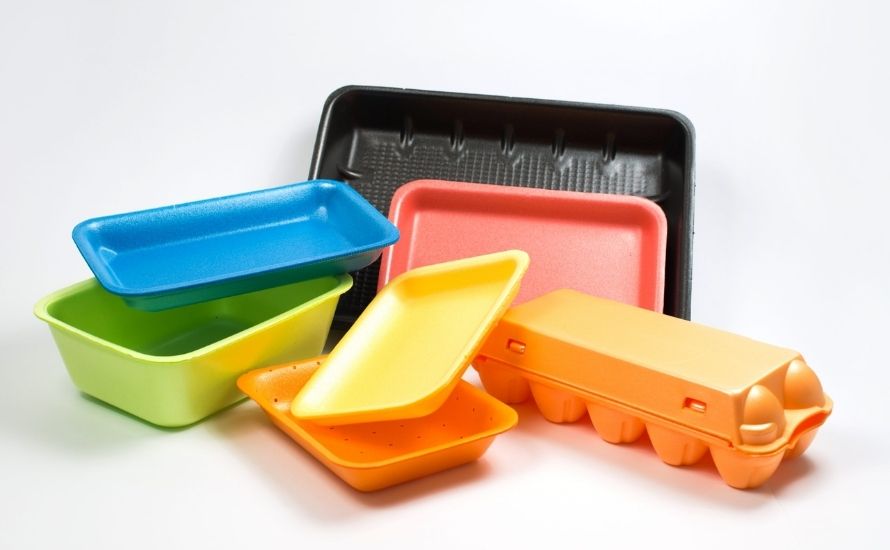
2. Main Types of Polystyrene
Polystyrene is a widely utilized polymer known for its versatility and adaptability across various applications. It exists in several distinct forms, each tailored to meet specific needs in manufacturing and production. The main types of polystyrene include:
- General Purpose Polystyrene (GPPS): This is a clear, rigid, and brittle form of polystyrene that is commonly used in applications requiring transparency, such as food packaging and disposable containers. GPPS is valued for its excellent clarity and ease of processing, making it a popular choice in the consumer goods sector.
- High Impact Polystyrene (HIPS): HIPS is a modified version of GPPS that incorporates rubber to enhance its impact resistance. This makes it suitable for applications where durability is essential, such as in the production of toys, appliances, and automotive parts. HIPS maintains good dimensional stability while offering improved toughness.
- Expanded Polystyrene (EPS): Known for its lightweight and insulating properties, EPS is created by expanding polystyrene beads. It is widely used in packaging, insulation, and construction due to its excellent shock absorption and thermal insulation capabilities. EPS is particularly effective in protecting fragile items during shipping.
- Extruded Polystyrene (XPS): Similar to EPS, XPS is produced through an extrusion process, resulting in a denser and more rigid foam. It is commonly used in insulation applications, particularly in building construction, where its moisture resistance and thermal performance are critical.
- Syndiotactic Polystyrene (SPS): This crystalline form of polystyrene is known for its superior heat resistance and mechanical properties. SPS is often used in high-performance applications, including automotive components and electronic housings, where durability and thermal stability are paramount.
Each type of polystyrene offers unique properties that cater to specific industrial needs, making it a fundamental material in various sectors, from packaging to construction and beyond. Understanding these types allows manufacturers to select the most appropriate form for their applications, optimizing performance and efficiency.
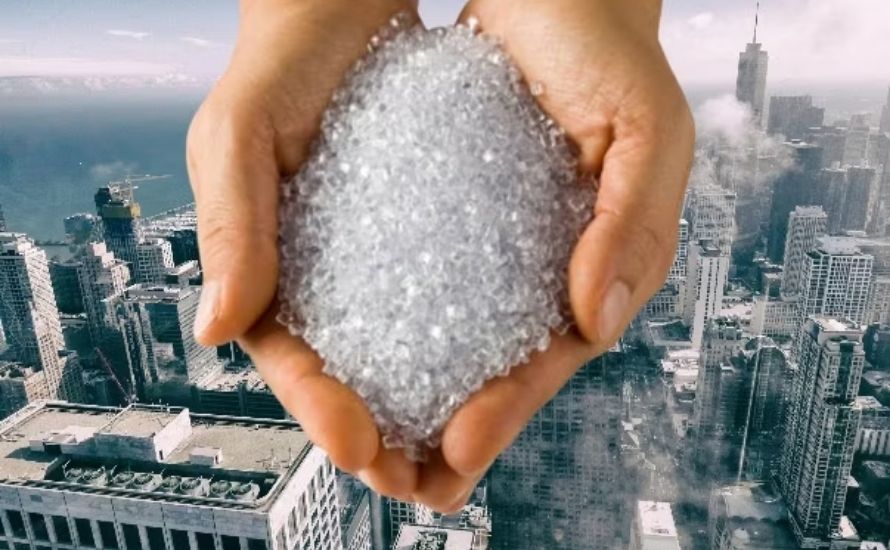
Read more: Polystyrene vs Polypropylene: Which one is stronger?
3. Differences and Key Characteristics of Each Type
Polystyrene is a versatile polymer that comes in various forms, each with unique chemical and physical properties. Understanding these differences is essential for selecting the right type for specific applications. Here’s a comparison of the main types of polystyrene:
Type of Polystyrene |
Chemical Properties |
Physical Properties |
General Purpose Polystyrene (GPPS) |
- Composed of linear chains of styrene monomers
- Non-crystalline structure |
- Clear and transparent - Brittle with low impact strength
- High glass transition temperature (Tg) of 80-105°C |
High Impact Polystyrene (HIPS) |
- Modified GPPS with rubber additives
- Improved toughness and impact resistance |
- Opaque and tougher than GPPS
- Good gloss finish
- Moderate flexibility with a Tg of 70-80°C |
Expanded Polystyrene (EPS) |
- Contains air-filled cells, created by expanding polystyrene beads
- Low density |
- Lightweight and buoyant
- Excellent thermal insulation
- Good shock absorption properties |
Extruded Polystyrene (XPS) |
- Similar to EPS but produced through an extrusion process
- Denser structure |
- Rigid and strong - Superior moisture resistance
- High compressive strength, ideal for insulation
|
Syndiotactic Polystyrene (SPS) |
- Syndiotactic Polystyrene (SPS)
- Crystalline form with a unique arrangement of polymer chains
- High thermal stability |
- High heat resistance (Tg of 100-120°C)
- Good chemical resistance
- Brittle but offers excellent mechanical properties |
4. Applications of Each Type
Understanding these applications is essential for manufacturers and consumers alike, as it allows for informed decisions regarding material selection based on performance requirements and environmental considerations. Below, we explore the diverse applications of each type of polystyrene:
General Purpose Polystyrene (GPPS):
- Widely used in the production of clear food containers and disposable cutlery due to its transparency and rigidity.
- Commonly found in packaging materials for consumer goods, providing a lightweight and cost-effective solution.
- Utilized in the manufacturing of stationery items, such as rulers and plastic folders, where clarity and ease of processing are essential.
High Impact Polystyrene (HIPS):
- Ideal for creating durable toys and household items that require enhanced toughness and impact resistance.
- Frequently used in the production of appliance housings and electronic device casings, where both aesthetics and durability are important.
- Employed in food packaging applications, particularly for items that need to withstand handling and transportation stresses.
Expanded Polystyrene (EPS):
- Commonly used in protective packaging for fragile items, such as electronics and glassware, due to its excellent shock-absorbing properties.
- Serves as an effective insulation material in construction, helping to improve energy efficiency in buildings.
- Utilized in the food service industry for takeout containers and disposable cups, providing thermal insulation for hot and cold items.
Extruded Polystyrene (XPS):
- Primarily used for insulation in building applications, offering superior moisture resistance and thermal performance.
- Employed in cold storage facilities to maintain temperature control and energy efficiency.
Utilized in various craft and DIY projects due to its rigidity and ease of cutting.
Syndiotactic Polystyrene (SPS):
- Applied in high-performance automotive components, where heat resistance and mechanical strength are critical.
- Used in electronic housings and insulation materials, providing durability and protection against environmental factors.
- Ideal for engineering applications that require materials with excellent thermal stability and chemical resistance.
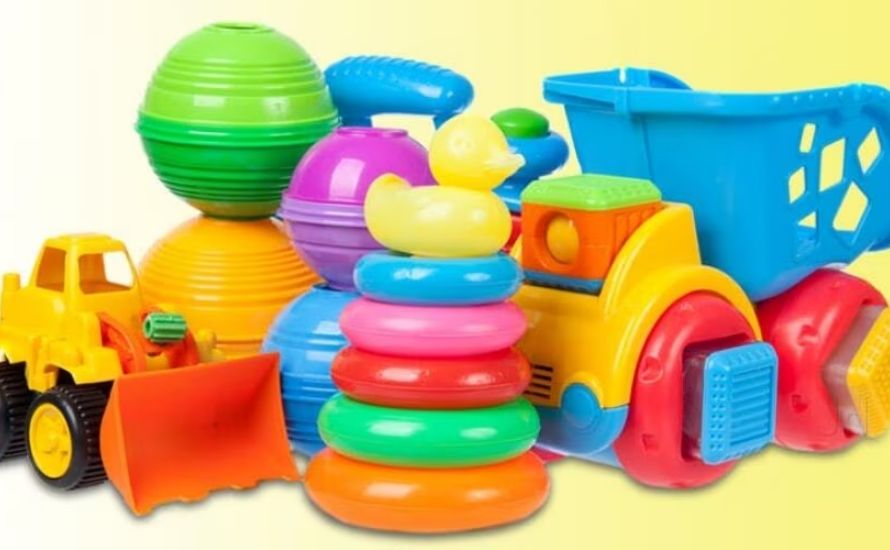
5. Conclusion
In conclusion, understanding the various types of polystyrene is essential for making informed decisions in both personal and professional contexts. Each type offers unique properties and applications, catering to diverse needs across industries. By recognizing these differences, consumers can select the most suitable polystyrene products for their specific requirements. Embracing the right types of polystyrene not only enhances functionality but also promotes sustainability in our choices.
6. About EuroPlas’ HIPS Products
EuroPlas proudly presents its innovative
HIPS filler masterbatch, engineered to optimize performance in the plastic manufacturing sector. Our masterbatch combines high-quality CaCO3 with HIPS resin and specialized additives, ensuring exceptional whiteness and superior dispersion. This formulation not only enhances the aesthetic qualities of your products but also significantly reduces production costs. By leveraging Vietnam's rich deposits of high-calcium limestone, we provide a sustainable and cost-effective solution that boosts productivity while saving energy through excellent thermal conductivity.
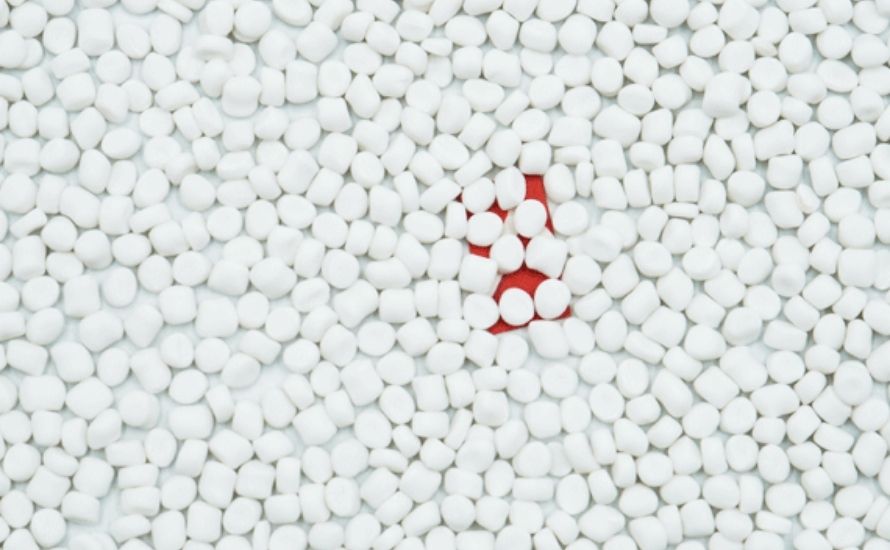
Discover the advantages of EuroPlas’ HIPS filler masterbatch for your business. For more details and to explore how our products can benefit your manufacturing process,
contact us today!