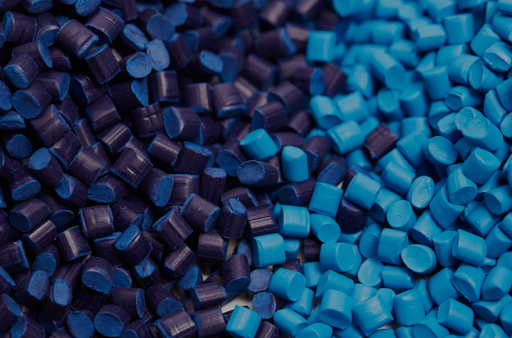
Choosing a suitable material between Polystyrene and Polypropylene will be extremely easy when you clearly understand their properties
Polystyrene and Polypropylene are considered two extremely popular plastics on the market today. They are always popular and widely used because each type has its own unique superior properties. Polystyrene and Polypropylene meet the different needs of both the engineering industry and the consumer goods industry.
Polystyrene is known for its high transparency, hardness and excellent insulation. This is one of the ideal materials for applications such as food packaging, disposable products, and insulation systems. On the other hand, Polypropylene is highly appreciated for its flexibility, durability and chemical resistance. The fields where they are favored include automotive technology, textiles and medical equipment.
Choosing a suitable material between Polystyrene and Polypropylene will be extremely easy when you clearly understand the properties, advantages, disadvantages and specific applications of each type. The following article will be the most detailed perspective for all the important aspects above. Let's find out now!
1. Polystyrene vs Polypropylene: Comparing Physical And Mechanical Properties
Polystyrene vs Polypropylene are both thermoplastic materials and are widely used in many different industries. However, Polystyrene vs Polypropylene both have their own unique characteristics. Here are some comparisons of the typical properties of Polystyrene vs Polypropylene:
1.1. Density
Polystyrene: This material has a density of about 1.04-1.06 g/cm³. This shows that Polystyrene has a higher density than polypropylene. Due to its high density, Polystyrene is often heavier and has higher stiffness than Polypropylene in certain applications.
Polypropylene: For this material, their density is about 0.90-0.92 g/cm³, slightly lower than Polystyrene. Therefore, when comparing Polystyrene vs Polypropylene, we can conclude that they have an advantage in terms of weight.
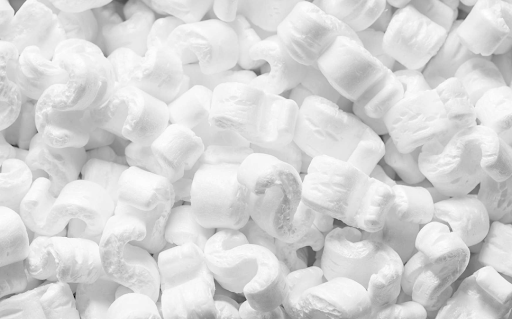
In terms of tensile strength, Polystyrene is usually in the range of 30-70 MPa
Read more: Everything you need to know about polystyrene
Read more: PP Plastic: Everything you need to know
1.2. Tensile strength
Polystyrene: In terms of tensile strength, Polystyrene is usually in the range of 30-70 MPa. This is considered one of the high tensile strength indexes. This advantage helps them possess the ideal hardness for applications that require rigidity.
Polypropylene: When comparing Polystyrene vs Polypropylene, we see that Polypropylene has a lower tensile strength. They only fall in the range of 25-40 MPa. However, to compensate for the tensile strength, they possess the ability to be tough and flexible. This makes them suitable for applications that require durability and fatigue resistance.
1.3. Impact resistance
Polystyrene: Between Polystyrene vs Polypropylene, Polystyrene is more susceptible to cracking and breaking when impacted. The reason is because they are known to have good hardness but high brittleness and low impact resistance.
Polypropylene: On the other hand, polypropylene is known to have excellent impact resistance even in various impact situations. So, between Polystyrene vs Polypropylene, they have a higher advantage in impact resistance.
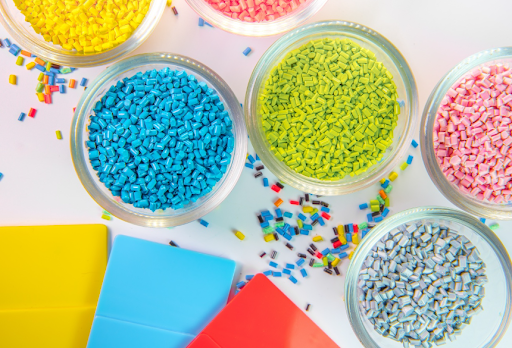
Polypropylene are resistant to many types of acids, bases, salts and even organic solvents
1.4. Chemical resistance
Polystyrene: Research has shown that this material is capable of performing well in environments containing acids, bases and salts. However, they will be easily affected by organic solvents such as acetone, benzene and many different types of oils.
Polypropylene: As for Polypropylene, they are resistant to many types of acids, bases, salts and even organic solvents. So, it can be concluded that between Polystyrene vs Polypropylene, Polypropylene has better chemical resistance.
1.5. Transparency
Polystyrene: This material is always the ideal choice for applications that require high transparency. Their transparency can be rated as excellent and their optical properties are also very good.
Polypropylene: Although they are also transparent, to achieve the best transparency, certain additives are needed. However, they are usually not as transparent as polystyrene. This makes them less advantageous in terms of transparency when it comes to Polystyrene vs Polypropylene.
2. Polystyrene vs Polypropylene: Thermal Properties
Polystyrene vs Polypropylene always have their own specific temperature properties. There are a few important aspects when comparing Polystyrene vs Polypropylene that we need to consider to choose the right material for each specific application.
Read more: Temperature ranges for different plastic materials
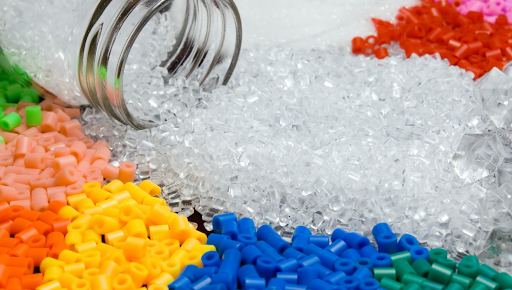
Between Polystyrene vs Polypropylene, Polypropylene will have a lower melting point
2.1. Melting point
Polystyrene: This material has a fairly high melting point of around 240°C (464°F). However, before reaching the melting point, they will tend to soften significantly. This limits their ability to operate or be exposed to high temperature environments.
Polypropylene: Between Polystyrene vs Polypropylene, Polypropylene will have a lower melting point. Specifically, their melting point is rated to fall around 160-170°C (320-338°F). Although their heat resistance is lower, they still work well in high temperature environments and limit softening before reaching the melting temperature.
2.2. Glass Transition Temperature (Tg)
Polystyrene: The glass transition will cause Polystyrene to change from a hard state to a rubbery state. The temperature that causes this phenomenon in them is around 100°C (212°F). This makes them more limited when comparing Polystyrene vs Polypropylene.
Polypropylene: Polypropylene has a much lower glass transition temperature. It falls between -10°C to 0°C (14°F to 32°F). This makes them still work well at room temperature. When comparing Polystyrene vs Polypropylene, it can be concluded that at low temperatures Polystyrene will be more brittle and Polypropylene will be more flexible.
2.3. Thermal stability
Polystyrene: This material is stable under normal conditions but can decompose when exposed to high temperatures for a long time. It tends to turn yellow and brittle when exposed to UV rays and high temperatures.
Polypropylene: Between Polystyrene vs Polypropylene, this material has the advantage in terms of thermal stability especially in low temperature environments. However, like Polystyrene, they can also degrade when exposed to UV rays and may require additives for outdoor use.
2.4. Heat Deflection (HDT)
Polystyrene: Depending on the type, they will have a specific index. In fact, the heat deflection temperature of polystyrene is usually around 70-100°C (158-212°F). This property indicates the temperature at which Polystyrene begins to deform under a specific load. The HDT of Polystyrene is relatively high, so they perform well in both operating in an environment exposed to heat and bearing loads at the same time.
Polypropylene: The heat deflection of this type is lower. Depending on the specific level, they will fluctuate between 50-110°C (122-230°F). It can be seen that, between Polystyrene vs Polypropylene, this material has a lower thermal displacement.
2.5. Thermal conductivity
Polystyrene: This material is considered an excellent insulator. The reason for this is because they have a fairly low thermal conductivity of about 0.033-0.036 W/m·K.
Polypropylene: Although they also have excellent thermal insulation (about 0.1-0.22 W/m·K), when comparing Polystyrene vs Polypropylene, they are still behind Polystyrene. However, this index still helps them perform excellently as insulators in many different applications.
3. Polystyrene vs Polypropylene: Common Applications
3.1. Applications of Polystyrene
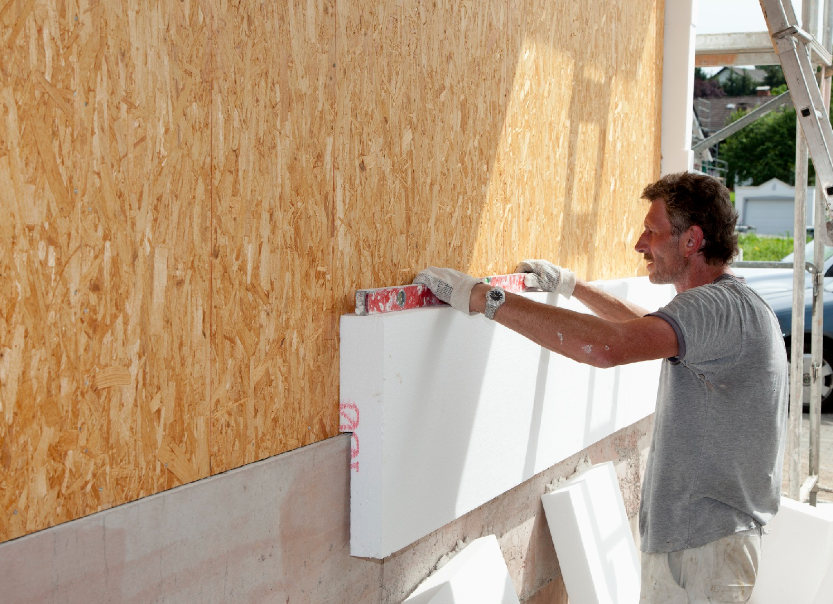
Due to their low thermal conductivity, they are always the ideal choice for insulation applications in homes and some other engineering works
Packaging: Between Polystyrene vs Polypropylene, Polystyrene is naturally lightweight, insulating, and has excellent impact resistance, making it suitable for the production of high-quality packaging. Furthermore, it has the ability to expand into a foam form, which makes it a good choice for protecting fragile items during transportation.
Transparent containers: Some container applications such as blister packs, plastic cups, zip bags, and some display containers can also be made from Polystyrene. They provide the application with both display and protection of the items they contain.
Disposable eating utensils: Some common applications include disposable cutlery, plates, and cups, etc. They are easy to mold, lightweight, thin, and cost-effective, making them suitable for mass production.
Insulation equipment: Due to their low thermal conductivity, they are always the ideal choice for insulation applications in homes and some other engineering works. They give the insulation product the ability to reduce temperature conduction excellently, are lightweight, easy to install and construct.
Laboratory equipment: They are always the first choice for laboratory equipment designs.
This is because they possess good chemical resistance, transparency and are easy to sterilize. Some common applications include petri dishes, test tubes and microplates, etc.
3.2. Applications of Polypropylene
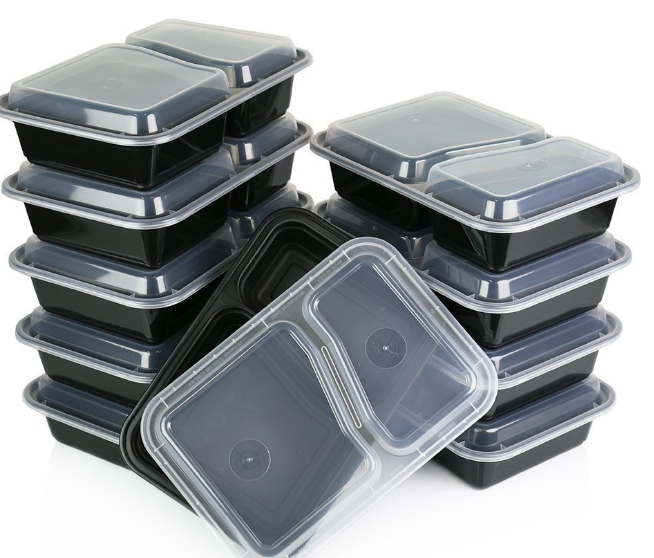
Some of the products that Polypropylene contributes to include yogurt cups, bottle caps, food storage containers, microwave food warmers, etc
Food Packaging and Containers: Between Polystyrene vs Polypropylene, this material possesses excellent heat resistance, moisture resistance and good chemical resistance, making it very suitable for applications related to food packaging and containers. Some of the products that Polypropylene contributes to include yogurt cups, bottle caps, food storage containers, microwave food warmers, etc. Besides, they can also produce packaging for snacks, confectionery and other consumer goods.
Automotive Components: Some of their common applications in the automotive industry are bumpers, interior trims, dashboards and battery boxes, etc. They bring significant benefits to the equipment such as weight reduction, durability, chemical resistance and good heat resistance.
Textile Industry: They are one of the ideal materials to use in the design of products such as diapers, surgical masks and disposable gowns. They provide users with a soft, flexible feel and excellent moisture resistance. In addition, they are also used to produce carpets, doormats, upholstery, etc. These fibers are stain-resistant, moisture-resistant and durable, making them suitable for both residential and commercial use.
Medical equipment: This material also possesses chemical resistance and the ability to sterilize without degrading. They are applied in the production of syringes, trays, sample containers and medical containers, etc. Moreover, thanks to their excellent flexibility, they are also used for the production of sutures and surgical mesh.
Household items: They are considered an extremely versatile material in production. It is easy to find Polypropylene in many common household items such as living hinges, integrated hinges, household storage boxes, bins and drawers, kitchen utensils, etc. They provide consumers with products that last over time.
4. Advantages And Disadvantages Of PS And PP
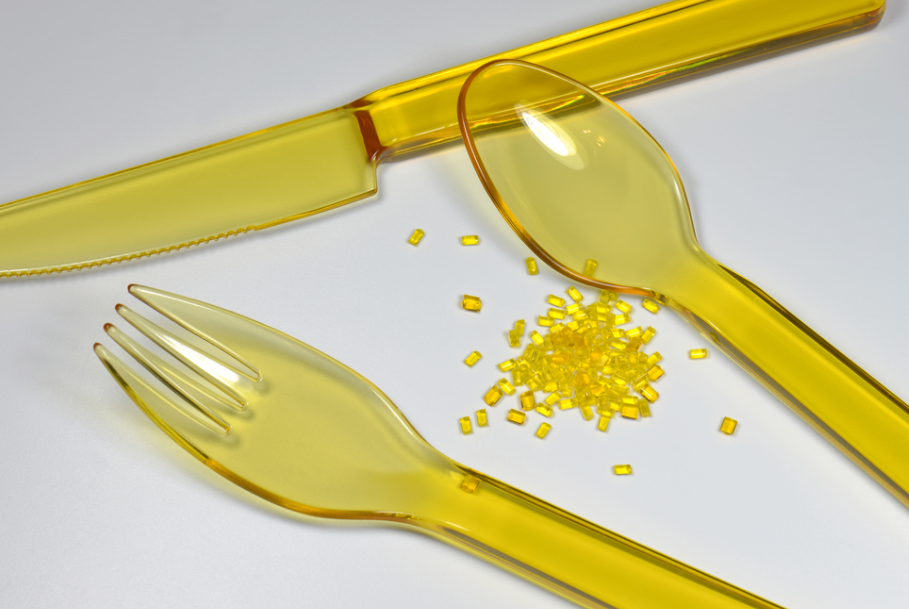
This material is known to be highly resistant to a wide range of chemicals, including acids, bases, and organic solvents
Polystyrene vs Polypropylene |
Polystyrene |
Polypropylene |
Advantages |
Transparency and Clarity: Polystyrene can be produced with high optical clarity. Thanks to this ideal property, they perform well in applications that require display and product visibility
Rigidity and Strength: Polystyrene is a hard material with high tensile strength, which helps ensure structural integrity of the product.
Easy to process: This is one of the materials that is considered very flexible in production. They are suitable for many methods such as extrusion, injection molding, blow molding, etc.
Low thermal conductivity: Thanks to their low thermal conductivity, they have great advantages for insulation applications in life. |
Flexibility and durability: They are known for their excellent flexibility and durability. This makes them ideal for products that require durability and fatigue resistance.
Chemical resistance: This material is known to be highly resistant to a wide range of chemicals, including acids, bases, and organic solvents.
Impact resistance: Polypropylene has superior impact resistance even in low temperature environments.
Cost-effective: They are known to be one of the most cost-effective thermoplastics on the market. This is also one of the great advantages that contributes to their popularity in many industries.
Heat Resistance: Their ability to operate in high temperature environments makes them an ideal choice for applications that involve repeated heating.
|
Disadvantages |
Brittleness: Polystyrene is brittle and can crack or break on impact, especially at low temperatures.
UV sensitivity: They can degrade when exposed to ultraviolet (UV) light, which can cause yellowing, brittleness, and reduced mechanical properties.
|
Limited Transparency: This material is naturally transparent and cannot achieve the transparency of polystyrene.
UV Degradation: Like polystyrene, polypropylene can degrade when exposed to UV light. |
5. Conclusion
In conclusion, to thoroughly evaluate Polystyrene vs Polypropylene, it is necessary to understand their properties, advantages and disadvantages. When comparing Polystyrene vs Polypropylene, both materials have unique properties that make them suitable for different applications. Understanding these differences will ensure that product performance and manufacturing costs are optimized.
6. About EuroPlas’ PP Products
EuroPlas is proud to be the world's leading PP Filler Masterbatch supplier. PP filler masterbatch is one of EuroPlas main products. With over 17 years of experience, we are proud to provide top quality, reputable and reliable PP Filler Masterbatch to our customers.
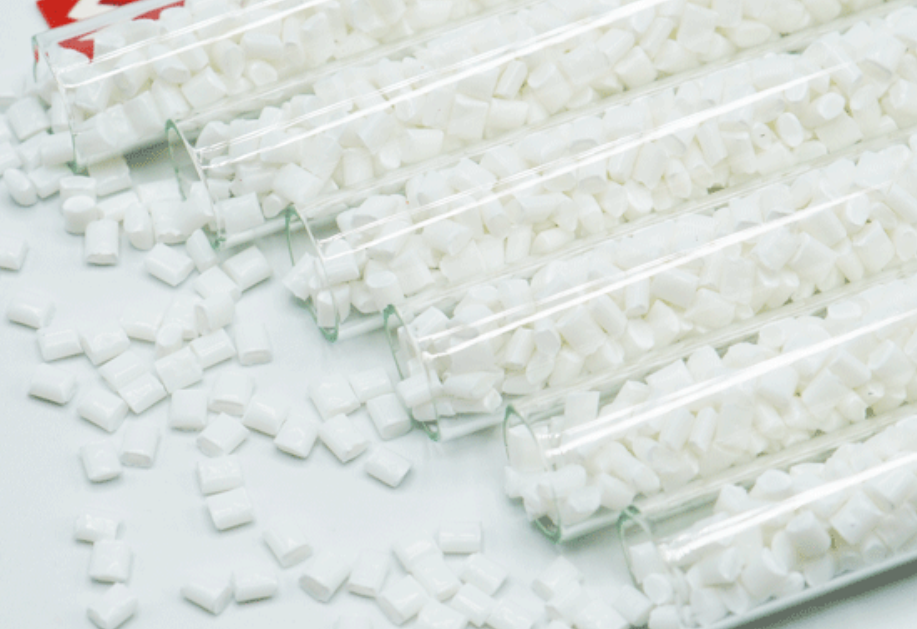
PP Filler Masterbatch helps improve the stiffness and tensile strength of products
PP Filler Masterbatch is one of the most popular plastic materials in production today. They are a concentrated mixture of calcium carbonate (CaCO₃) or other mineral fillers, dispersed in polypropylene carrier resin. Incorporating PP Filler Masterbatch into the production process will help bring countless great benefits:
Cost savings: Incorporating PP Filler Masterbatch into the production process will help reduce the amount of virgin polypropylene required. This helps manufacturers save a significant amount of cost.
Improved mechanical properties: PP Filler Masterbatch helps improve the stiffness and tensile strength of polypropylene bags. This ensures that the polypropylene bag will always maintain its shape and integrity when subjected to high pressure or load.
Improvements in manufacturing: PP Filler Masterbatch is an important factor in improving the forming process in terms of reduced shrinkage, more uniform bag thickness, smoother surface finish and improved product stability.
Improved printability: This material improves the surface properties of PP bags, making them easier to print with high quality.
Let's visit EuroPlas blog today! We will accompany you in your upcoming big projects!