Polyimide is known as a high-performance polymer commonly used under elevated temperatures. Thanks to its great thermal stability, it can replace glass, steel, and metals. The material's excellent dielectric property allows it to be used in electronics, automobiles, and aerospace.
Let's delve into the article below for more interesting information about this high-performance plastic!
Read more: The Ultimate Guide to High Plastics
1. What is Polyimide?
Polyimide, or PI, is classified as a thermosetting polymer formed through a chemical process called condensation polymerization. The material has high versatility, thermal stability, mechanical strength, and electrical insulation properties. Therefore, it's widely used in various industries and applications, such as the electronics industry, aerospace applications, and automotive sectors.
2. How is Polyimide Processed?
Polyimides were first synthesized and developed in the mid-20th century. The American chemist Paul J. Flory is known to have contributed significantly to the discovery and advancement of this thermosetting polymer in the 1950s. The plastic was then researched, produced, and enhanced properties to achieve more usage.
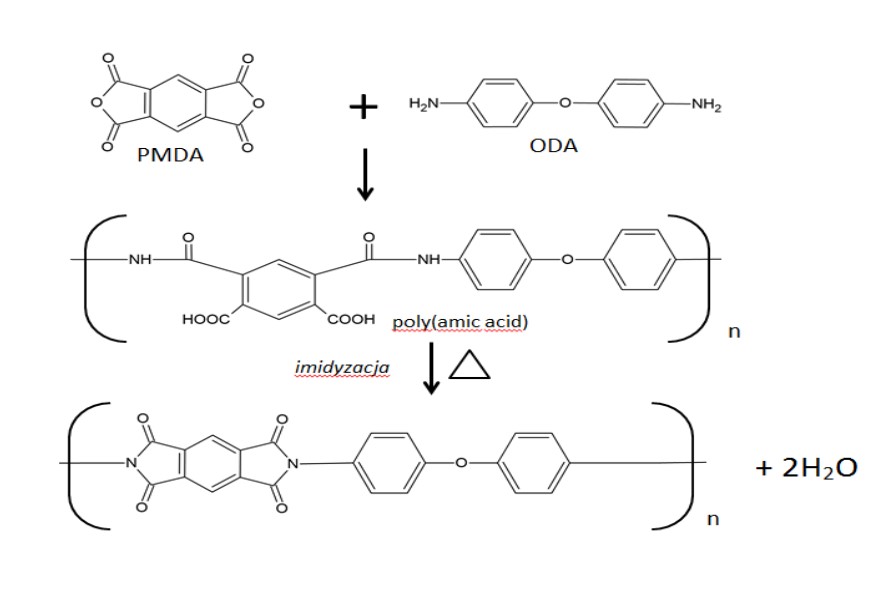
The production process includes 2 stages. Stage 1 is the reaction of a dianhydride with a diamine to produce a polyamic acid. This polyamic acid can be processed into various forms, such as films or coatings. It will then go through stage 2, called imidization. In this process, the acid groups combine to form amide linkages, a functional group comprising two acyl groups bound to nitrogen. Since imides are highly polar, they have good solubility in polar media, resulting in a highly stable, crosslinked polyimide structure.
3. Outstanding Features of Polyimide
Polyimide has many exceptional properties, including:
- High strength and toughness: The material is well-known for its strength and toughness, as it has a high modulus of elasticity and great impact resistance.
- Heat resistance: Thanks to its high melting temperature and resistance to thermal degradation, polyimides are an ideal option for high-temperature applications.
- Low coefficient of friction: This outstanding feature makes Polyimide suitable for applications with common friction requirements.
- Good chemical resistance: The material can tolerate various types of chemicals, such as bases, acids, and organic solvents. Thus, it's one of the top choices for applications in harsh environments.
- Good weather and UV resistance: The ability to withstand weather and UV radiation is necessary for the plastic to be used in outdoor applications.
4. Polyimide Applications
Polyimide is an ideal choice in aerospace, automotive, electronic, and microwave industries because of its excellent mechanical strength, chemical resistance, and electrical insulation properties.
In the aerospace industry, this plastic is used to produce components exposed to harsh environments. Thanks to its ability to withstand extreme temperatures and pressures, it's often used to make aircraft components, including structural parts, gaskets, and seals. Polyimide composites can replace metals in engine components, including ductwork and insulation. Polyimide foams are ideal for lightweight, highly efficient thermal and acoustic insulation in aircraft.
Polyimide plays an important role in the automotive sector as a material for engine components and a protective coating for sensors. Meanwhile, in the electronics industry, you can find Polyimide present in wire insulation, flexible printed circuit boards (PCBs), and protective coating for electronic components.
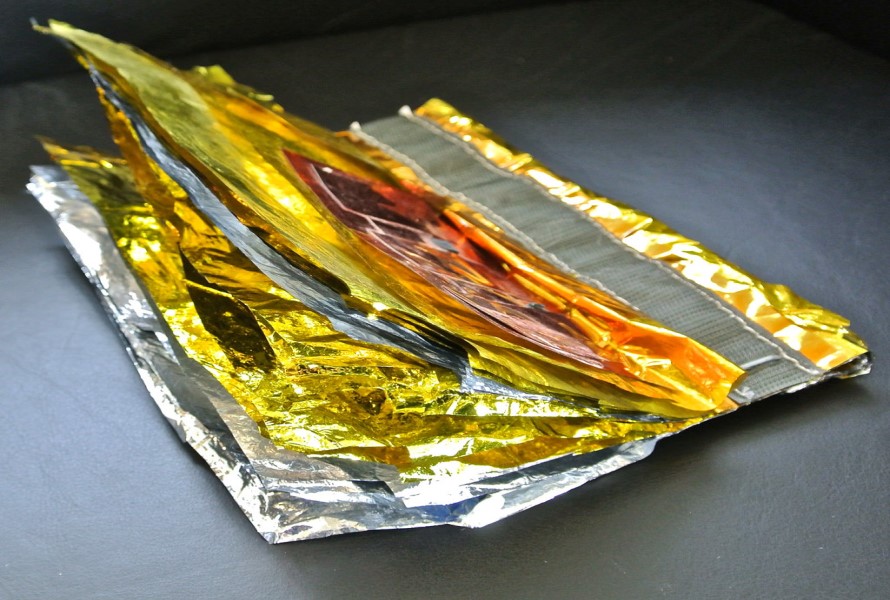
This thermosetting polymer also has various uses in producing semiconductors and flexible printed circuits. It acts as a mechanical stress buffer, a high-temperature adhesive, a film for micronized circuity, and an insulating film on the magnet wire for electronic cables.
Polyimide is an excellent choice in the microwave industry. The material can withstand high temperatures and high-frequency electromagnetic radiation, which is a must-have property for microwave ovens, microwave filters, and other microwave components.
In addition, Polyimide fibers are woven into protective clothing for firefighters and bags for hot gas filtration in power plants and cement kilns.
5. EuroPlas - A World Leading Company For Engineering Plastic Compound
EuroPlas is known as a leader in the masterbatch field since the company satisfies a wide range of requirements for unique plastic raw material solutions to optimize production costs and improve the competitiveness of the customers.
EuroPlas engineering plastic compound is full-function-in-one-material to save time and production costs. The combination is made of resin, additives, and reinforcements (based on the end-product requirements).
All EuroPlas products are various, including PA6, PA66 blend compound, PBT GF-FR compound, ABS Glass fiber compound, ABS Antistatic compound, PC flame retardant compound, and ABS. All are of high quality and flexibility. If you're looking for a material for automobile, electronics manufacturing, interior decoration, and renewable energy, you should not miss these products from EuroPlas.
Look at our list of Engineering Plastic Compounds below!

PP engineering plastic compound is a blend of PP resin and special reinforcing agents such as flame retardant additives, conductive black carbon, talc mineral, fiber/glass beads, etc. Depending on the requirements of the final product's characteristics, manufacturers will choose what reinforcements to combine.
We have:
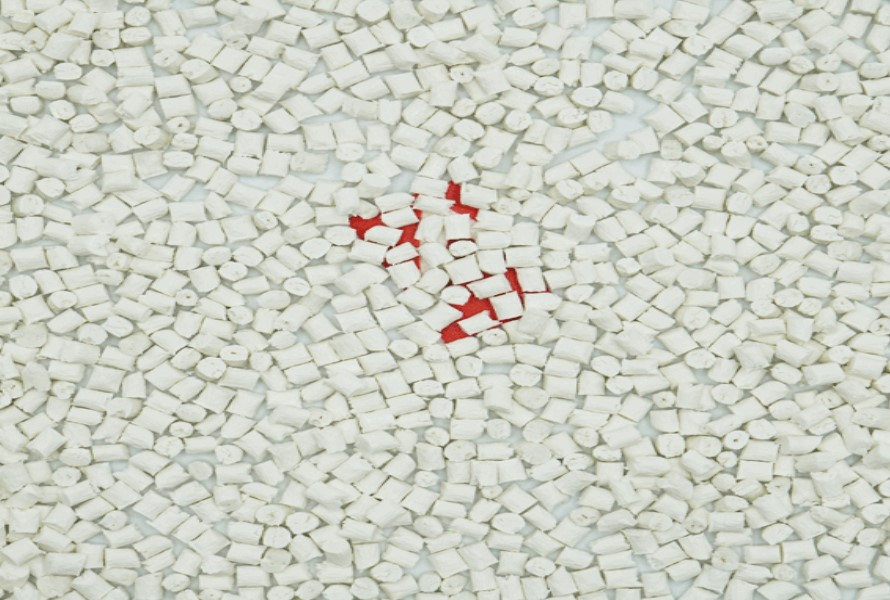
It's an engineering plastic comprising PBT plastic with glass fiber reinforcements, color, and flame retardant additives. Our material also obtains glass fiber ratios and fire resistance levels that meet the UL94 standards, including 5VA, 5VB, V0, V1, and V2. Therefore, EuroPlas is confident to be your reliable supplier for PBT GF-FR Compound and other products.
5.3. PA (Nylon) engineering plastic compound
Polyamide-6 (PA6) and Polyamide-66 (PA66) are among the top choices for manufacturing, thanks to their outstanding properties. The former is cheaper, easier to process, and distorts less, while the latter is stiffer and has higher temperature resistance and better abrasion resistance. EuroPlas has added other additives to the PA6 and PA66 resin to increase their performance.
- PA6, PA66 blend compound: PA6, PA66 Blend compound combines PA6/PA66 resin, elastomer, and impact strength modifiers, giving it resiliency and strong mechanical properties. This material from EuroPlas will help you produce mechanically strong and highly precise final products. Its application includes roller bearings, carburetors, control valves, exhaust gas, and other gear-related components.
- PA66, PA6 Glass fiber compound: PA resin is mixed with glass fiber reinforced, providing the PA66 and PA6 Glass fiber compound with toughness, mechanical strength, high heat deflection temperature, chemical resistance, and wear resistance. With 30-50% of glass fiber, EuroPlas PA66, PA6 Glass fiber compound is ideal for producing drive belts, bearings, gears, carburetor components, household electrical components, and computer details.
5.4. HIPS
It's the blend of HIPS resin and other additives such as flame retardant carbon black conductive. It's known to improve the performance of final products. Their application includes Mobile chargers, Power sockets, Electronic Components, earphones, Electronic component pallets, Consumer goods, Packaging, and Toys. We have:
5.5. ABS Plastic Products
ABS (Acrylonitrile Butadiene Styrene) is a thermoplastic polymer known for its toughness, heat resistance, and impact resistance. ABS is commonly used in a wide range of applications, such as electronic housings, automotive parts, and toys, due to its mechanical properties and ease of processing.
- ABS Antistatic compound: It's the combination of ABS resin and antistatic additive. It helps prevent surface static, thus minimizing the risk of electrostatic discharge and ensuring safety during processing and product use.
- ABS Glass Fiber Compound: It's a combination of ABS resin, glass fiber, and suitable additives. It can increase the stiffness, heat deflection temperature (HDT), and softening point (VICAT) of end-products.
- ABS flame retardant compound: It is made of ABS resin and flame retardant additives, which are in different fire resistance levels according to UL94 standards: V0, V1, and V2. It's well-known for its ability to prevent fire spread on plastic surfaces.
5.6. Polycarbonate Engineering Plastic Compound
Polycarbonate engineering plastic compound is mixed between the polycarbonate base, reinforcing agents, and additives. Its purpose is to create a material meeting the property requirements of the final products. The end products can achieve special properties thanks to the compound. Engineering plastic is commonly seen in electronics and automobile manufacturing, interior design, and renewable energy.
EuroPlas Polycarbonate engineering plastic compound includes:
- PC glass fiber compound: a mixture of polycarbonate resin and glass fiber with rigidity, heat, and impact resistance.
- PC flame retardant compound perfectly combines polycarbonate resin and halogen flame retardant. It's lightweight, transparent, durable, impact-resistant, and high-temperature resistant.