Vacuum forming is sometimes considered ineffective and out of date compared to pressure forming and injection molding methods. However, it's still an economical and efficient process to produce plastic that is utilized in a variety of goods.
Our article will discuss highlighted applications of the method and provide useful tips to be successful with vacuum forming with clear plastics. Let's scroll down for more detail!
Read more: Vacuum forming plastic - The ultimate guide
1. A List Of 7 Applications Of Vacuum Forming Plastic
Vacuum forming is affordable, flexible in design, and has the capacity to create many similar parts at once in a short time. It is extensively implemented in the fields in which the parts and products produced are needed to be lightweight, durable, and in overall custom shapes. Its highlighted applications include:
- Packaging
- Blister Packs: Vacuum forming is applied to the packaging of small end products in pharmaceuticals, electronics, and consumer goods.
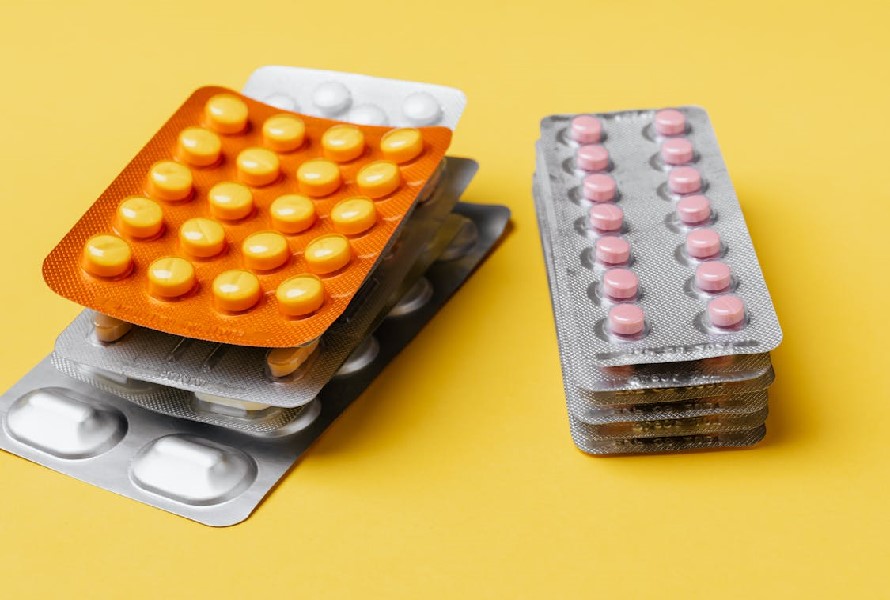
- Clamshells: The method is useful for product protective packaging, such as for hardware, cosmetics, and toys.
- Plastic Food Containers and Trays: In the food and packaging industries, vacuum forming is an extensively utilized process, especially for producing plastic trays and storage containers.
- Thermoformed Parts
- Automotive Interiors: Vacuum forming provides the automotive industry with long-lasting solutions and design freedom, thanks to its characteristics. The most common applications are interior parts such as dashboard, door panels, and trim.
- Medical Devices: Since manufacturers can tailor the shape and size during vacuum forming, it's employed in making prosthetics, orthotics, and different parts of medical tools.
- Protective Equipment
- Industrial Safety Equipment: Vacuum forming is specialized for sheltering molded plastic parts in protective gear such as shields, glasses, and covers.
- Sports Equipment: The method is applied to produce protective gear like helmets, shin guards, and chest protectors in sporting activities.
- Signage and Display Components
- Trade Show Display: Custom-shaped displays are made for retail settings using vacuum forming, which improves marketing and product exposure.
- Signage: Vacuum forming is widely used to create strong, lightweight signs, including lettering and logos, that may be used both indoors and outdoors.
- Toys: Since vacuum forming can duplicate intricate patterns and characteristics, it is frequently employed in the manufacture of toys, action figures, and model kits.
- Agriculture: In farming and the manufacture of agricultural vehicles and products, vacuum forming is used to create low-cost, weather-resistant, and long-lasting parts and components. Products like greenhouse glass, tractors, and seed trays all employ this technology.
- Household Goods: Manufacturers of home goods employ vacuum forming because of their efficiency and low cost. Large-scale appliances like shower enclosures, bathtubs, refrigerator trays, and some plastic cooking utensils fall within this category. In order to save expenses, vacuum forming is also frequently used to make product packaging.
2. Tips for Successful Vacuum Forming with Clear Plastics
Here are some tips to improve the quality and consistency of vacuum-formed clear plastic parts. They will guarantee that the parts fulfill the required standards for clarity, toughness, and aesthetic appeal.
- Selection of materials: Select transparent polymers that are meant to be vacuum-formed, such as polycarbonate, acrylic, and PETG (polyethylene terephthalate glycol). These materials have good thermoforming properties, impact resistance, and clarity.
- Thickness of sheet: Choose a thickness where formability and clarity are balanced. Although thinner sheets—roughly 0.010 to 0.060 inches—generally have greater clarity, managing them carefully throughout the forming process is necessary to avoid ripping or deformation.
- Preheating process: Before forming, make sure the plastic sheet has been preheated evenly. This facilitates better material flow and stress reduction during the vacuum forming process. Usually, an oven or infrared heater is used to warm the sheet to the suggested temperature range given by the manufacturer, which is often between 250 and 320°F or 120 and 160°C.
- Mold setting up: To guarantee that the mold surface is clean and clear of contaminants, carefully prepare it. The produced object can have a clear finish more easily if the mold surface is smooth. Sticking can be avoided, and part removal can be aided by using a mold release agent.
- Consistent heating while forming: To prevent the plastic sheet from stretching or thinning unevenly, keep the temperature consistent throughout the forming process. Heating must be managed to avoid uneven material thickness and clarity caused by overheating or under heating particular areas.
- Time and vacuum pressure: Employ the proper vacuum pressure and time settings based on the particular plastic substance and shape of the component. Sufficient vacuum pressure should allow for a consistent draw without unwanted stretching or tearing. Timing guarantees that the plastic fits the mold perfectly without overstretching or cooling down too soon.
- Cooling process: After forming, give the component enough time to cool down to establish its shape. Stress from rapid cooling might result in warping or surface flaws. Part integrity and clarity are preserved by controlled cooling with the use of cooling fans or ambient air.
- Management after forming: Take extra care while handling formed components to prevent scratching or harming the clear surface. To preserve optical clarity and avoid surface flaws during storage and transit, wear protective gear such as handling gloves or packaging gears.
3. Conclusion
Vacuum forming is a versatile, inexpensive, time-saving, and consistent method that works well for small-scale product manufacture. It's frequently used in home goods, automotive, medical, and food packaging.
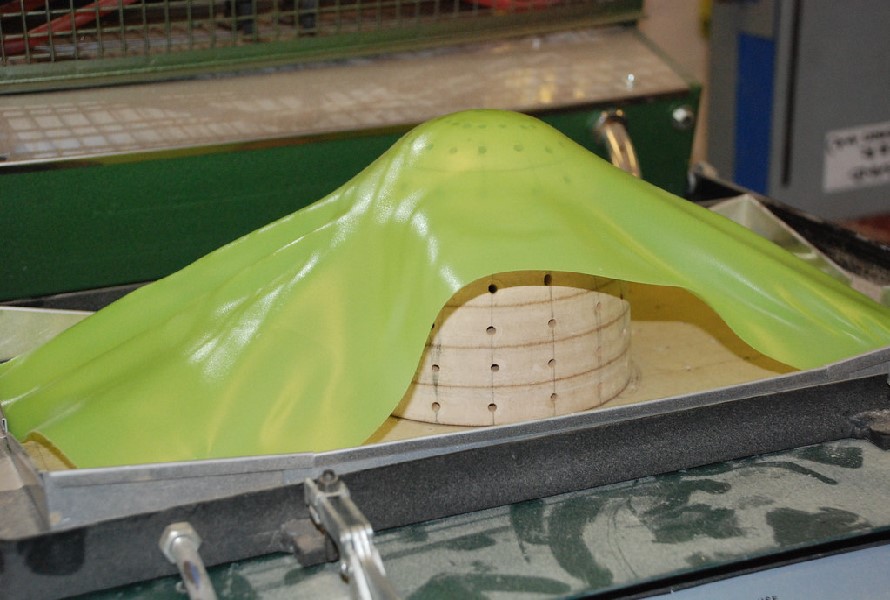
If you want to proceed with clear plastics, follow our tips above to ensure high-quality results for your products.
4. About EuroPlas
EuroPlas is a partner of thousands of factories in over 95 countries. As the world's No. 1 filler masterbatch manufacturer, we proudly bring customers unique plastic raw material solutions to help their factories optimize production costs and improve the competitiveness on the market.
Our company offers:
- Bioplastic compound
- Color masterbatch
- Plastic additives
- Engineering plastic compound
- Filler masterbatch
- Bio filler
Contact EuroPlas right now to get more information on our high-quality products!