Have you ever wondered how BOPP film is made and why it's something worth paying attention to? In this article, we will dive into the manufacturing process of BOPP film and explore the reasons why it holds significance.
1. The Manufacturing Process of BOPP Film
BOPP film is a type of plastic film made from polypropylene resin. It is produced through a process called biaxial orientation, where the film is stretched in both the machine direction (MD) and transverse direction (TD). This alignment of polymer chains gives the film its distinctive properties.
The manufacturing process of BOPP film involves several key steps:
Step 1. Raw material feeding system
The core of BOPP film is made from isotactic polypropylene, a semi-crystalline thermoplastic polymer. The outer layers may contain ethylene-propylene copolymers and/or ethylene-butane-propylene copolymers. These raw materials are introduced into the extruders using a hopper system.
.png)
Isotactic polypropylene, a semi-crystalline thermoplastic polyme, is used to make the core of BOPP film.
Step 2. Extrusion
The BOPP film raw materials are melted and heated to 200–230°C within the extruders before being fed into the extrusion head, where they are extruded as a foil.
Step 3. The foil cooling
The extruded BOPP film foil is then brought into direct contact with a chilled cylinder and submerged in a water bath to cool the melt.
Step 4. Machine direction orientation (MDO)
The BOPP film is subsequently passed over multiple rollers, which raise the temperature and prepare the film for longitudinal stretching (machine direction). By moving the film between the rollers that spin at increasing rates, the film is stretched up to five times its original length. This aligns the polymer chains, improving the mechanical properties of the film and reducing its thickness by up to five times.
The BOPP film is heated again after stretching to remove the tension created during stretching (annealing phase).
.png)
BOPP film is run through a number of rollers to increase its temperature and get it ready for longitudinal stretching (machine direction).
Step 5. Transverse direction orientation (TDO)
A quick-moving chain of metal jaws grabs the BOPP film on both edges once it exits the longitudinal stretching zone (tenter clips). The film is stretched transversely by the diverging rails after being heated up in an oven in the middle (i.e. stretching in the transverse direction up to 9 times its original width).
The macromolecules align at this point, but this time in a transverse orientation, improving the mechanical characteristics of the BOPP film and reducing its thickness by up to 9 times. After stretching, the chain and the film converge, allowing the film to balance off the tension that builds up during stretching (annealing phase).
Step 6. Thickness measurement and flame treatment
The BOPP film enters a new processing step at which point the thickness is automatically measured (along the entire width). After that, one of the faces is given a flame or corona treatment to prepare the BOPP film for the subsequent conversion processes, specifically to change the surface that will serve as an anchor for materials like ink (for printing), glue (for laminating), or metal (metallization process).
.png)
When the BOPP film reaches a new processing stage, the thickness (over the full width) is automatically measured.
Step 7. Reel winding
After being wound around a reel, the BOPP film is then sliced to the specific measurements.
Step 8. Film measurements
The final BOPP film product is subject to various measurements, including:
- Density, grammage, and thickness
- Elastic modulus, elongation at break, and tensile strength
- Haze (opacity) and Gloss (sparkling appearance)
- The friction coefficient between films and between films and metals
- Sealing strength and threshold °C
- Temperature stability (heat shrinkage)
The BOPP film has at least three layers and a thickness between 15 and 60 microns, with the center layer being the thickest and primarily responsible for the mechanical qualities, while the two outer layers provide the film with different characteristics. Additives may be added to the BOPP film to completely fulfill the application criteria, depending on the ultimate application the film is intended for.
Read more: What is BOPP plastic film? BOPP film manufacturing process
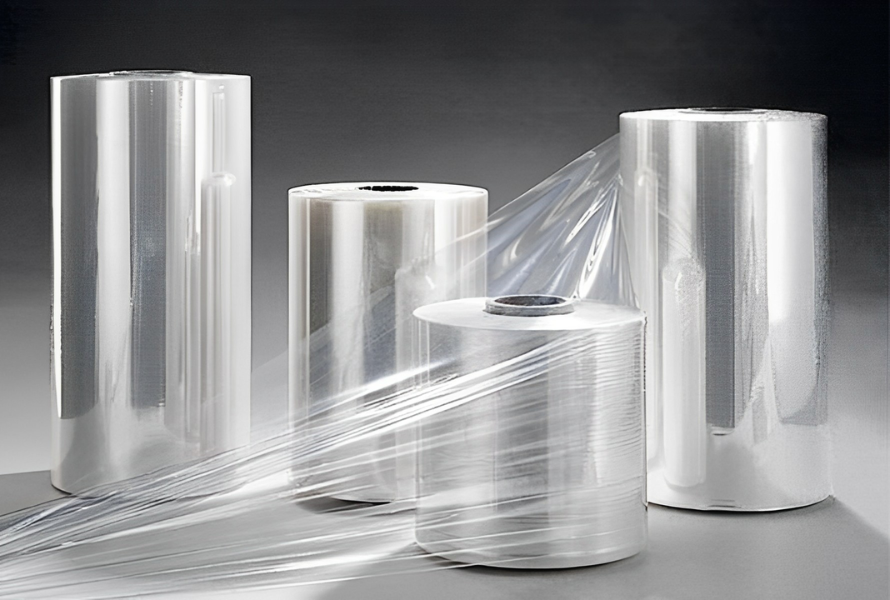
BOPP film is a plastic film made from PP resin, stretched in both the machine direction and transverse direction during production.
2. Properties of BOPP Film
BOPP film is a standout material in packaging, favored across industries for its exceptional properties. By understanding its remarkable qualities, we can unlock its true potential and see why it's an essential component of modern packaging solutions.
Here are some key properties of BOPP film:
- Clarity: BOPP film is transparent and offers excellent clarity, allowing for the visibility of products or printed content.
- High Tensile Strength: The biaxial orientation process imparts exceptional strength to BOPP film, making it resistant to tearing and punctures. It can withstand the rigors of handling and transportation.
- Dimensional Stability: BOPP film exhibits excellent dimensional stability, meaning it maintains its shape and dimensions even under varying temperature and humidity conditions. This property ensures consistent performance and reliability.
- Moisture Resistance: BOPP film has inherent moisture resistance, making it suitable for packaging applications where protection against moisture is crucial. It helps to maintain product freshness and extends shelf life.
- Chemical Resistance: BOPP film has good chemical resistance, making it resistant to various solvents and chemicals. This property enables its use in applications where exposure to chemicals is a concern.
- Printability: BOPP film provides a smooth and receptive surface for printing. It offers excellent ink adhesion, allowing for vibrant and high-quality graphics, text, and branding to be applied onto the film.
- Heat Sealability: BOPP film can be easily heat-sealed, enabling the production of airtight and tamper-evident packaging. It is commonly used in applications where secure sealing is required.
- Barrier Properties: While BOPP film is not inherently a high barrier material, it can be enhanced with coatings or laminations to improve its barrier properties. This allows for the protection of products against moisture, oxygen, and other environmental factors.
- Recyclability: BOPP film is recyclable and can be incorporated into the production of new plastic products. Its recyclability contributes to sustainability efforts and reduces environmental impact.
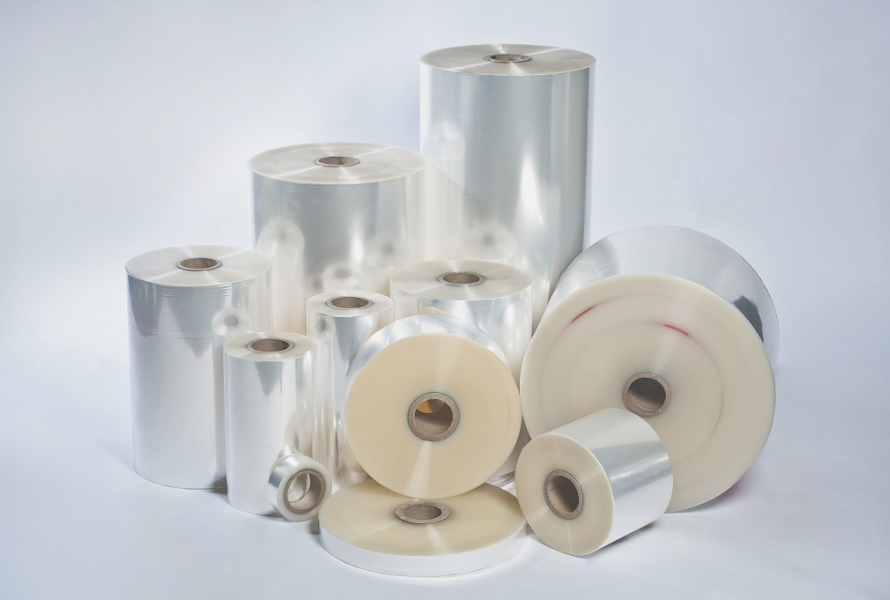
These properties combined make BOPP film a valuable component of contemporary packaging solutions.
3. Conclusion
BOPP film, derived from polypropylene resin, is a plastic film created through biaxial orientation, where it is stretched in both the machine and transverse directions. This stretching aligns the polymer chains and gives the film its unique properties.
These properties make BOPP film a popular choice for a wide range of packaging applications, including food packaging, consumer goods, industrial packaging, and more. The versatility and performance of BOPP film continue to drive its widespread adoption in the packaging industry.
4. About EuroPlas
BOPP film is produced from PP plastic resins. Currently, EuroPlas takes pride in offering exceptional plastic raw material solutions to optimize production costs and enhance market competitiveness. As a reliable source, we provide high-quality PP resins for BOPP film manufacturing:
At EuroPlas, our PP Filler Masterbatch offers the following features::
- Optimize production costs
- Improve some surface features of finished products: increasing hardness, reducing shrinkage,...
- Save fuel thanks to the good thermal conductivity of CaCO3
- Reduce mold cooling time, shorten the production cycle
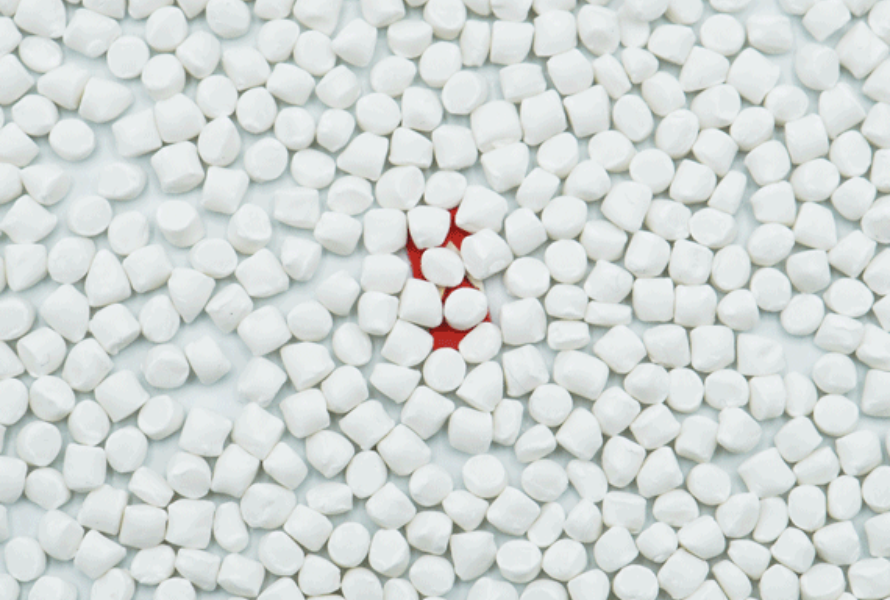
Contact us right now for prompt advice and support to meet your specific needs.