Have you ever wondered about the materials that make up your smartphone, car, or everyday household items? Many of these products contain components made from PA plastics. PA, or Polyamide, has rapidly become a cornerstone in numerous industries due to its exceptional durability and resistance properties. With these outstanding qualities, PA plastics have become an indispensable material in modern life.
This article delves deep into the world of PA plastics, covering everything from their production process to their practical applications, empowering you to make informed decisions for your specific needs.
1. What is PA Plastic?
PA, also known as Polyamide, is a type of thermoplastic with a unique molecular structure featuring repeating amide linkages. It is one of the most widely used engineering plastics, renowned for its exceptional mechanical properties and versatility.
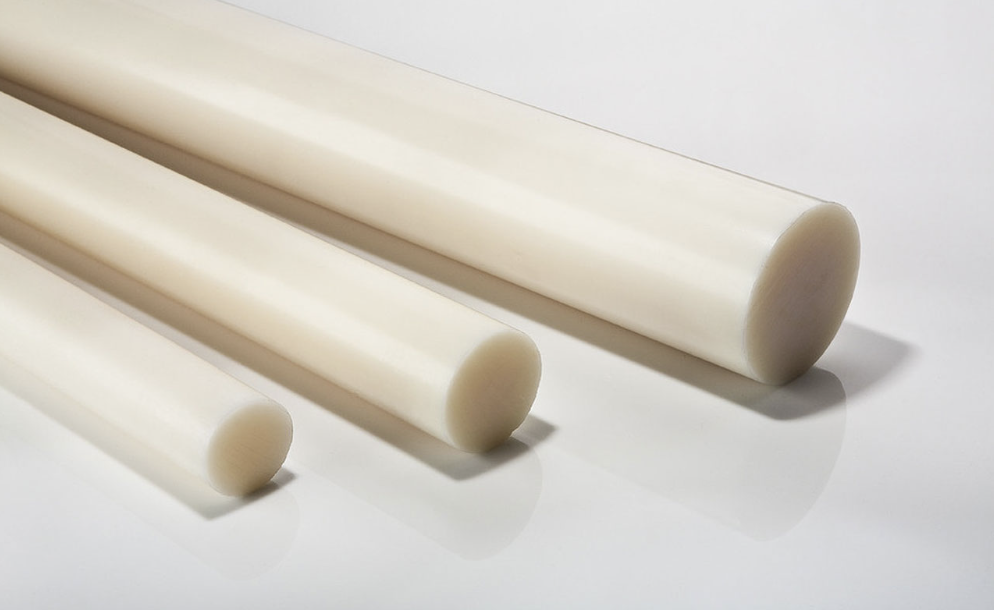
PA exhibits high strength, stiffness, and excellent abrasion resistance. Notably, it can operate reliably over a broad temperature range, from -40°C to 110°C, without compromising its structural integrity or performance. Additionally, PA is easy to process, boasts a high gloss finish, is non-toxic, and can be easily colored.
Chemically, PA consists of long polymer chains containing amide groups (N-H-C=O). PA is synthesized through a polymerization reaction between an acid and an amine. A prime example is PA66, formed from the reaction between adipic acid and hexamethylenediamine.
In terms of manufacturing, PA is commonly produced in the form of sheets or rods, facilitating easy processing and fabrication into custom products to meet specific user requirements.
1.1 PA Plastic Production Processes
There are two primary methods for synthesizing PA plastics:
Polycondensation: This involves a reaction between a dicarboxylic acid and a diamine, resulting in PA types with controllable chain lengths, such as PA66, PA69, and PA610. For instance, PA66 is synthesized from hexamethylenediamine and adipic acid.
Ring-opening Polymerization: This process involves the ring-opening of a lactam (a type of amino acid), producing PA types like PA6 and PA12. This method is simpler and more cost-effective, yielding a high-viscosity PA solution.
1.2 Molecular Structure of PA Plastics
The molecular structure of PA plastics directly influences the material's properties:
- Hydrogen bonding density: Affects crystallinity.
- Hydrogen bonding between amide groups: Contributes to high mechanical strength.
- Carbon chain length: Influences melting point and water absorption.
2. Types of PA Plastics on the Market
Various PA types are available on the market, including PA6, PA66, PA12, and specialized PA grades. Each type possesses distinct physical properties suitable for specific applications:
2.1. PA6 (Nylon 6)
Synthesized from caprolactam, PA6 exhibits:
- Tensile strength: 70-85 MPa
- High hardness: 78-80 Shore D
- Melting point: 220°C
PA6 is used in fiber production, gear manufacturing, bearings, and electrical equipment housings.
See more: PA6 vs. PA66: The Differences Between Two Engineering Giants
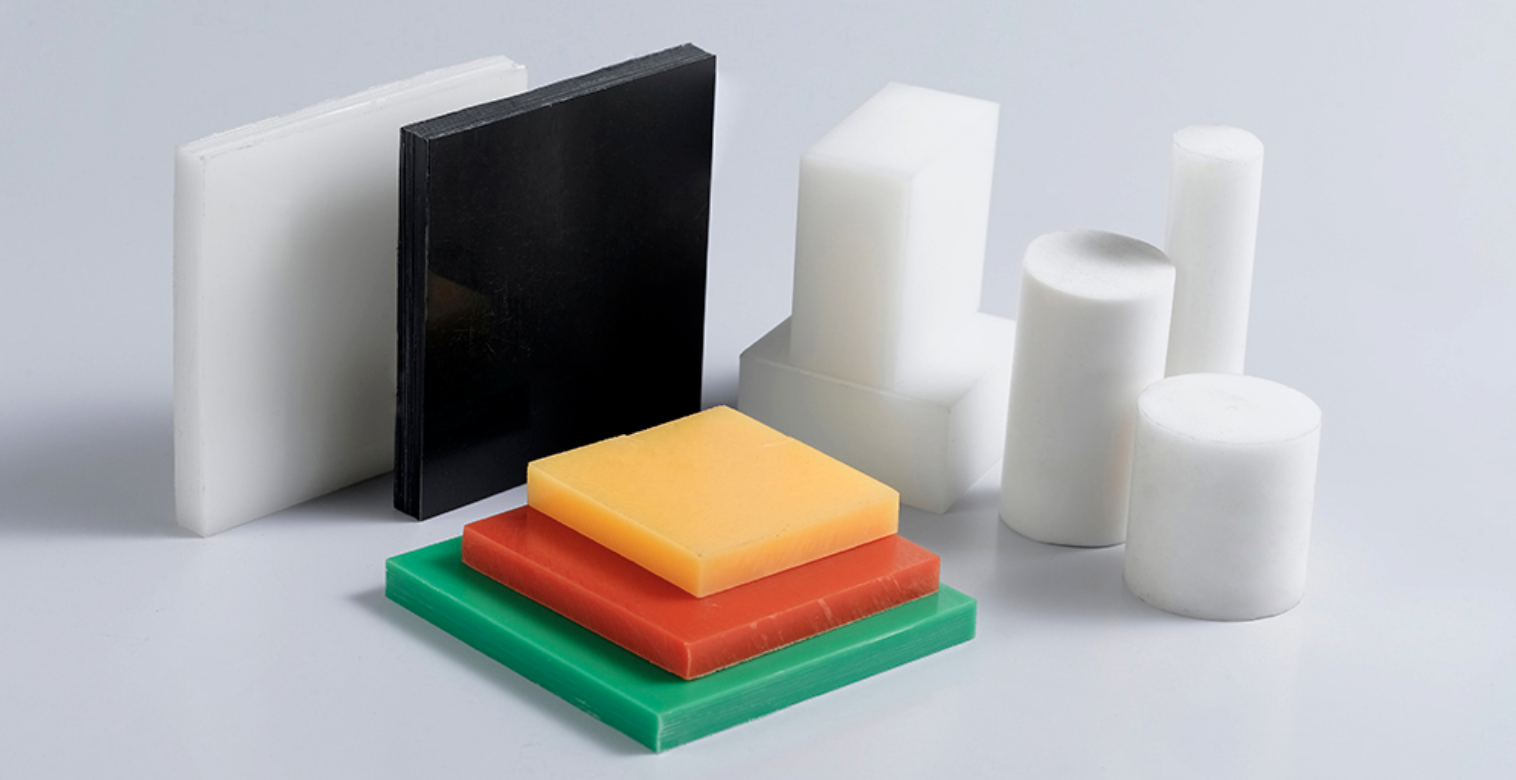
2.2. PA66 (Nylon 66)
Synthesized from hexamethylenediamine and adipic acid, PA66 exhibits:
- Tensile strength: 75-90 MPa
- Melting point: 260°C
- Higher hardness than PA6: 82-85 Shore D
PA66 is used in automotive components, electronic equipment housings, and industrial belts.
See more:
Common additives used in PA66 GF
PA66 GF30 - PA66 30% glass fiber: Outstanding benefits & applications
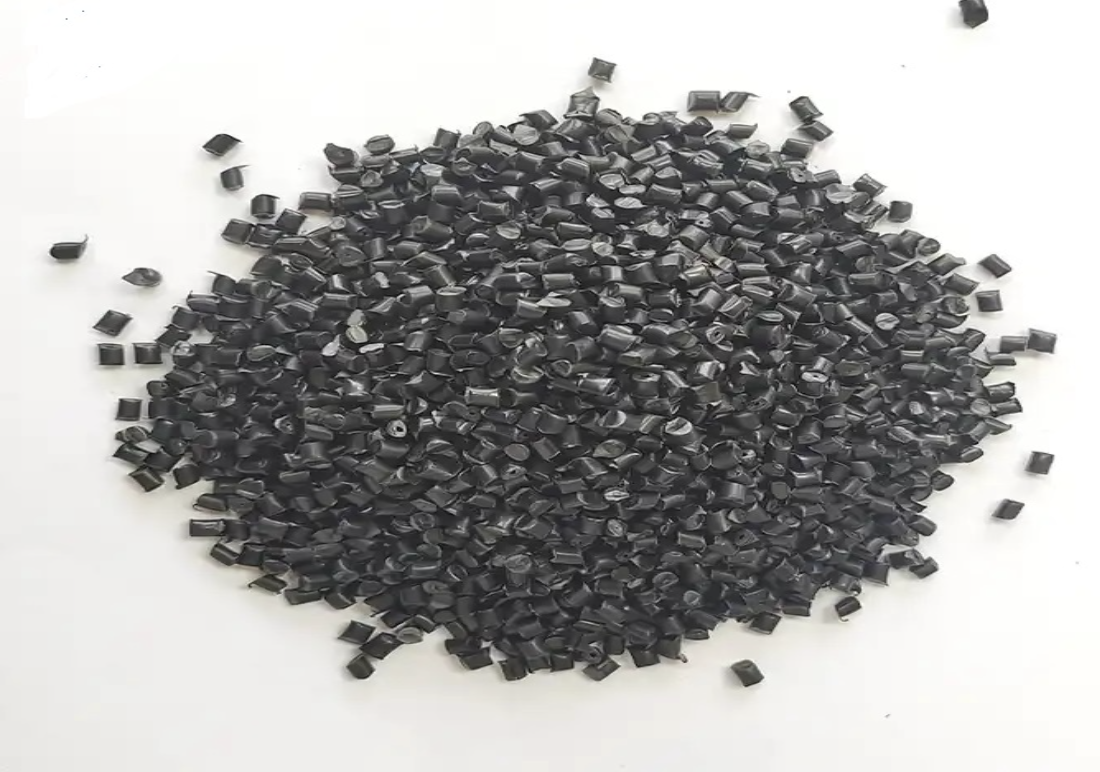
2.3. PA12 (Nylon 12)
Synthesized from laurolactam, PA12 exhibits:
- Excellent chemical resistance
- Good dimensional stability
- Lowest moisture absorption among PA types
PA12 is used in automotive fuel lines, fiber optic coatings, and components.
See more:
PA 12 (Nylon 12) - Definition, key features and common uses
Pa12 GF20 - Pa12 20% glass fiber: Outstanding benefits & applications
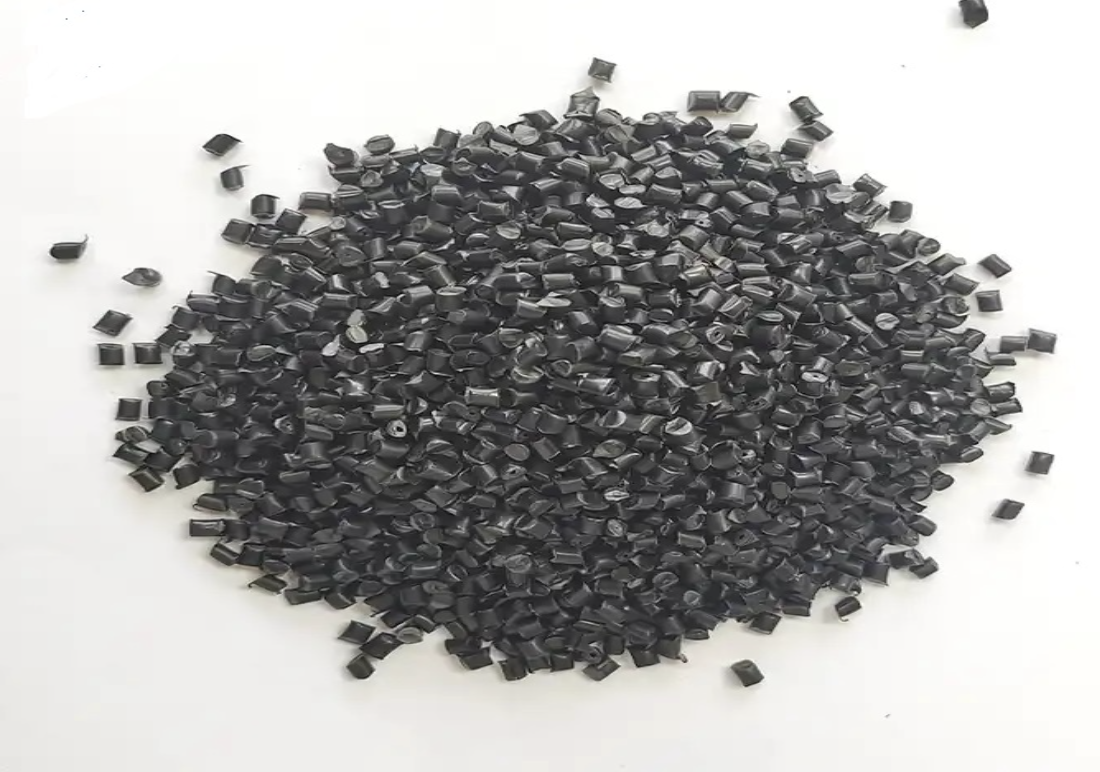
2.4 Specialized PA Types
- PA46: With a high melting point of 295°C, it is suitable for applications requiring extreme temperature resistance.
- PA612: A balance between PA6 and PA12, ideal for applications demanding both strength and dimensional stability.
3. Advantages of PA Plastics
PA plastics have earned significant trust from consumers due to their diverse advantages:
3.1. Mechanical Properties
- High surface hardness: Shore D hardness of 70-85
- Excellent abrasion resistance: Low coefficient of friction (0.2-0.3)
- High resistance to pressure and impact: Tensile strength of 70-90 MPa; elongation at break of 20-300%
3.2. Heat Resistance
- High melting point: PA6 220°C; PA66 260°C; PA46 295°C
- Stable operation over a wide temperature range: Continuous operating temperature from -40°C to 120°C; short-term operating temperature up to 180°C
3.3. Chemical Properties
- Food safety: Non-toxic; does not react with food
- Corrosion resistance: Resistant to various chemicals; less resistant to strong acids
- Organic solvent resistance: Resistant to oils, greases, and fuels; good resistance to hydrocarbons
Due to this combination of high strength, excellent electrical insulation, and stable chemical properties, PA plastics have become the preferred material for manufacturing components and mechanical structures in various devices.
4. Applications of PA Plastics
PA plastics find widespread applications in numerous industries:
- Automotive: Production of engine components, fuel systems, and cable coatings.
- Textiles: Production of fibers, garment accessories, and industrial belts.
- Electrical and Electronics: Production of equipment housings, electrical insulation components, and heat-resistant parts.
- Food Industry: Production of packaging, kitchen utensils, and food processing equipment.
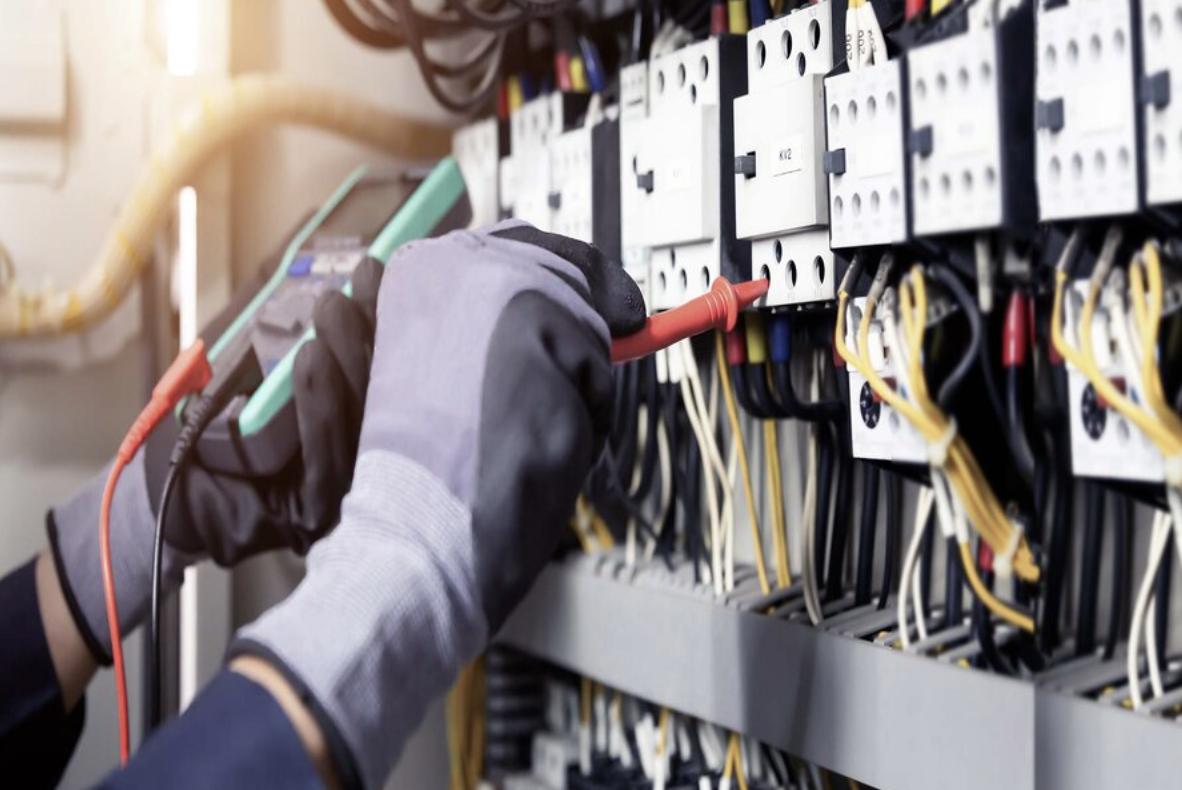
5. Conclusion
PA plastics have proven to be indispensable in many industrial sectors. With a wide variety of types, from PA6 to PA66 and specialized grades, along with exceptional properties such as high strength, heat resistance, and chemical resistance, PA plastics continue to be the first choice for many industrial and consumer applications.
However, selecting the right PA type for a specific application requires a deep understanding of the properties of each type and the application requirements. This is especially crucial in industries demanding high precision and reliability, such as automotive and electronics.
6. About EuroPlas PA Products
As a leading filler masterbatch manufacturer in Vietnam, EuroPlas has established itself as a top producer of high-quality PA compounds. With a team of experienced experts and advanced production processes, EuroPlas is committed to:
- Diverse product range: PA6 compounds for molding applications, PA66 compounds for engineering components, and specialized PA grades tailored to specific requirements.
- Advanced production processes: Strict quality control systems, modern production technologies, and well-equipped laboratories.
- Meeting diverse customer needs: In-depth technical consulting, product development support, and customized solutions.
If you are seeking a high-quality PA supplier, please contact EuroPlas's expert consultants for detailed advice and tailored solutions. As soon as we receive your inquiry, our expert team will promptly analyze your needs and provide optimal solutions, supporting you throughout the project implementation process. With extensive experience and in-depth knowledge of the plastics industry, EuroPlas is committed to delivering comprehensive solutions that enhance your competitiveness and optimize your production processes.