In recent years, slip additives have been utilized in masterbatch and many manufacturing processes thanks to their amazing attributes.
Slip additives change the surface properties of the polyolefin film and reduce the friction between the film layers and other contact surfaces
In today’s post, we shall guide you through all the necessary information about these amazing products and how to choose the right one for your requirement!
Related:
- What are plastic additives? 8 most common plastic additives in plastic industry
- Slip additives and antiblock additives for extrusion industry
- Blocking in blown film: Main causes and solutions
- Anti-blocking: What you need to know
1. What are slip additives for plastic
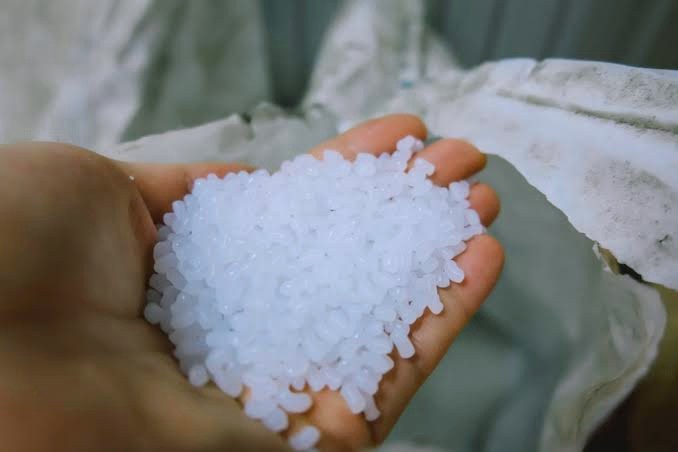
Source: El-Mostafa Masterbatch
1.1. Definitions
Slip additives, also known as slip agents, are compounds that are applied to polymers to control friction. They are introduced directly into the polymer during the manufacturing process and migrate to the surface when the polymer cools, allowing a solid lubricating layer to develop.
Slip additives modify the surface characteristics of polyolefin films by reducing friction between film layers, as well as friction between the film and other contact surfaces, since reduced friction allows the film to move more readily inside the film machining applications, where welding, charging, or forming equipment is used...
The interaction between two polymer surfaces or between the polymer surface and processing equipment is measured by slip, often known as surface friction and represented by the Coefficient of Friction (CoF). The formation of friction is influenced by a number of variables, such as:
- Type of polymer
- Temperature and type of process
- Measure and structure of the film
- Additionally existing ingredients
The winding of film rolls, the manufacture of bags, and packing activities might all experience difficulties as a result of high friction.
With the use of slip additives, a film's resistance to sliding over itself or other pieces of converting machinery may be decreased. The amides chemical family contains compounds that are crucial for the industry, and they are frequently referred to as "quick bloom" (oleamide) and "slow bloom" (erucamide) additives.
During the extrusion process, they are added directly into the polymer and move to the surface when the polymer cools, allowing a solid lubricating layer to develop. Other amides are utilized for particular operations (e.g. higher heat extrusion coating applications or customized mixtures where balancing slip and antiblock properties are critical.)
1.2. Benefits
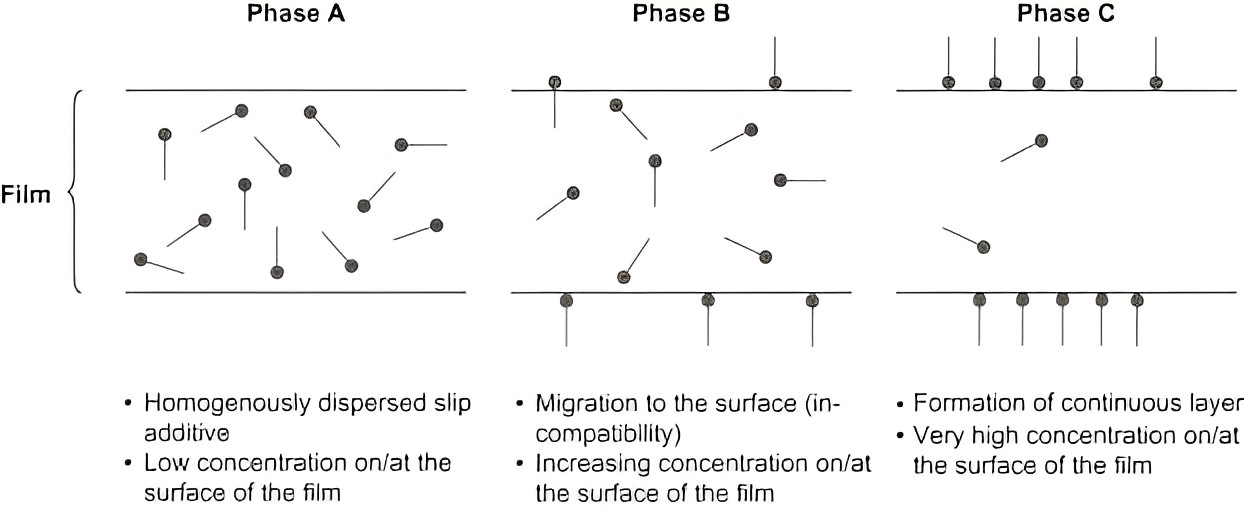
How a slip additive work
Source: Multilayer Flexible Packaging (Second Edition), 2016
The addition of an additive to the resin mixture creates an internal lubricant that moves to the resin's surface and dissolves into a molten solution. However when the mixture cools, it crystallizes and the slipper is discharged. When the slip agent reaches the surface, it generates a lubricating layer that separates the neighboring film layers.
Slip agents provide many benefits to the products:
- Reduce the friction coefficient to increase machine capacity.
- Create a process-regulating lubricant by increasing the line speed during milling.
- Increase the surface friction of plastic items.
- Increase the surface's safety.
- Increase your tolerance against UV radiation.
- Anti-scratching and flaking reduction in high-abrasion zones
1.3. Applications
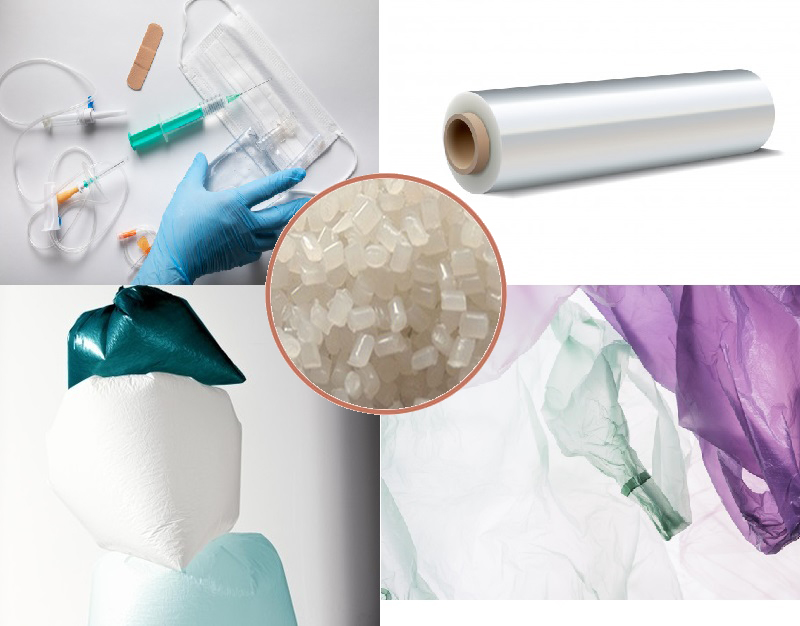
Some applications of slip additives
Source: Perfect Colourants and Plastic Pvt. Ltd.
Slip agents have been added to a wide range of products with the results being varied. In this context, slip refers to any movement between two surfaces without allowing the product to move laterally.
Slip additives can be employed in polymer film constructions and plastic packaging to enhance polymer manufacturing and in-use qualities, and they are a practical necessity for both the producer and the end-product user.
The most common applications for these additives are listed as follows:
- Blown film
- Cast film
- BOPP
- BOPET
- Sheet extrusion
- Profile extrusion
- Blow molding
- Injection molding
2. Types of slip additives
There are a few slip additives available on the market but the most common slip additives used in plastic production are Oleamide (C-18) and Erucamide (C-22).
2.1. Oleamide (C-18)
Oleamide is a main fatty acid amide produced from oleic acid. It is a colorless waxy solid that has been recommended for use as a slip additive in polyolefin applications. It frequently generates a thin lubricating coating to minimize friction and avoid undesired adhesion. It has a high slip, mold, and torque release, as well as composite lubrication and scuff- and scratch resistance.
2.2. Erucamide (C-22)
Erucamide is a wax with a non-polar straight chain and a polar amide functional group, making the molecule polypolar. Because erucamide has a low molecular weight and a flexible chain, it tends to migrate to the outside of the resin stream, causing a variety of effects such as decreasing the coefficient of friction (raising smoothness), lowering adhesion to the metal wall type, and so on.
2.3. Difference between Oleamide (C-18) and Erucamide (C-22)
There are a few things that differ between the two most common anti-slip additives. Surface bloom and COF decrease rates vary depending on the slide agent. As a result, a single slip agent may not operate in all of a customer's required applications.
- Oleamide is known as "rapid blooming" because it moves quicker than erucamide. After a certain period, the slower erucamide will produce films with a lower COF than oleamide.
- Erucamide is used in higher temperature handling applications due to its lower vapor weight and unpredictability, and it also stays at the surface longer, without venting off as smoke.
- Oleamide is used when a low COF is required in a short period of time, although erucamide's slower movement might be advantageous in move-stock applications and on-line crown treatment.
When film clarity is critical, this is frequently used in conjunction with erucamide or oleamide to provide an enemy of blocking effect. The centralization of slip present has an impact on execution. Initially, the COF is sensitive to minor variations in focus until a fundamental level of slip is reached, at which point slip has no effect on the COF. The amount of slip required is determined by the thickness of the film, the slip-added material used, and the proximity of other added substances, for example, enemies of squares.
3. Properties of slip additives
1. The slip agent migrates slowly, and the final COF may not be achieved until 7-10 days after extrusion (depending on the amide used.) The vast bulk of COF decrease typically occurs within 24-48 hours.
2. The processor must customize slip additives to the process and required end-properties. In certain circumstances, a fast-blooming oleamide is required, but in others, a slower-blooming amide is recommended.
3. High amounts of slip can disrupt the surface treatment of the film as well as its printability and sealability.
4. To maintain the same COF, the amount of slip agent must be lowered as the thickness of the film increases.
5. Small doses of slip additives improve not just the "hand" of the film but also its processability.
6. Slip additives can help improve mold release qualities in molding operations.
4. Top 3 slip additives suppliers
EuroPlas Vietnam is a top masterbatch manufacturer with more than 15 years of experience in the industry. EuroPlas is also one of the leading slip additive suppliers in Vietnam. We have a vast experience in manufacturing slip additives for various industries such as automotive industry, aerospace industry, medical equipment industry, and many more. We are specialized in producing high-quality slip additives as well as other additives for plastic masterbatch.
We are committed to delivering the highest quality products at competitive prices. Our products are regularly tested by our customers before they are shipped to ensure that they meet your exact specifications, no matter how difficult they may be.
Polyfill is a masterbatch manufacturer that has been making slip agents for many years. They have developed their own proprietary blend of polyester and other ingredients to create a perfect slip agent.
Polyfill's slip additive is very easy to use, it can be applied to parts using many different methods. The product has been tested and approved by so many people and companies. This means you can rest assured that your products will work as they should without any issues at all!
Ampacet is a masterbatch manufacturer that specializes in the production of polymer additives, such as anti-slip additives, anti-foam additives,... Ampacet has established itself as an innovative company with much production experience and expertise in the development of additives for specialist applications. The company's portfolio offers a wide range of products, from color to additive masterbatch.
Their primary focus is on supplying their customers with high-quality products at competitive prices and on time. The company also provides custom blends and formulations for their customers as well as technical support through a comprehensive service department.