Plastic additives are organic or non-organic substances added during the production process to modify and improve specific properties and efficiency of plastic end-products. It plays an indispensable role in many industries, including the toy industry. Plastic additives can enhance the quality and performance of toys, simultaneously making them safe for users. Let’s find out more details in this article!
1. Key types of plastic additives used in toys
Plastic additives are essential components in toy manufacturing, enhancing various properties to ensure safety, durability, and aesthetic appeal. Here are some key types of plastic additives used in toys:
- Antimicrobial additive
- Odor removing additive
- Anti-UV additive
- Flame retardant additive
Read more: What are plastic additives? 8 most common plastic additives in plastic industry
2. How additives enhance toy safety and performance
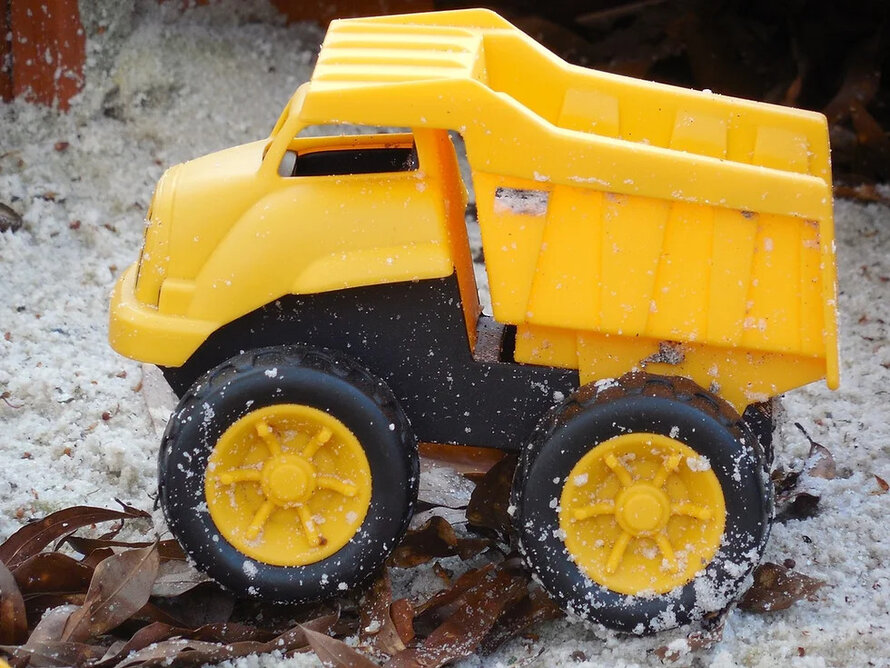
Using additives in the production process can improve toy safety and appearance
Plastic additives play a crucial role in enhancing both the safety and performance of toys. Here’s how they contribute:
2.1. Enhancing safety
- Flame retardants: These additives are essential in reducing the flammability of plastic toys, ensuring they meet stringent fire safety standards, and reducing the risk of fire-related accidents.
- Non-toxic stabilizers: Additives such as non-toxic stabilizers ensure that toys are safe for children by preventing the release of harmful chemicals during use.
- Antimicrobial additives: These help to inhibit the growth of bacteria, mold, and mildew on toys, ensuring they remain hygienic and safe for children to handle.
- Phthalate alternatives: Used to enhance flexibility without the health risks associated with traditional phthalates, making soft plastic toys safer for children.
2.2. Enhancing performance
- UV stabilizers: These additives protect toys from degradation due to exposure to sunlight, maintaining their integrity and appearance over time.
- Colorants: Additives such as pigments and dyes ensure toys have vibrant and appealing colors that are resistant to fading.
- Impact modifiers: These enhance the toughness and durability of plastic toys, ensuring they can withstand rough handling and play without breaking.
- Anti-static agents: These prevent the build-up of static electricity on plastic surfaces, which can attract dust and dirt, keeping toys cleaner and more appealing.
- Plasticizers: These improve the flexibility and pliability of plastics, making toys safer and more enjoyable to play with.
By integrating these additives, manufacturers can produce toys that are not only safer for children but also more durable, visually appealing, and resistant to various environmental factors.
Read more: Plastic additives and its role in the plastics industry
3. Conclusion
In conclusion, plastic additives have outstanding contributions to the toy industry by enhancing the safety, durability, and aesthetic appeal of toys. With a wide array of additives available, toy manufacturers can tailor the properties of plastics to meet stringent safety standards and consumer expectations. That guarantee will ensure that toys remain a source of joy and entertainment for children worldwide, while also giving peace of mind to parents and babysitters.
4. About EuroPlas’ additives
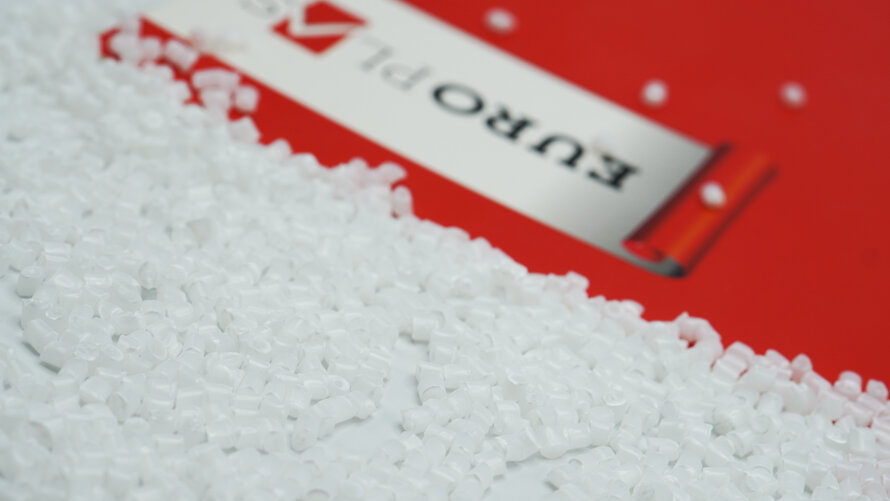
Plastic additive is supplied by EuroPlas
EuroPlas is a trusted supplier for many worldwide enterprises with a diversity of plastic additives being suitable for a range of projects. Our products combine lots of functions and feature all in one, bringing cost-saving solutions and improving end-products' durability and longevity.
Explore EuroPlas’s lists of plastic additives below and look for appropriate choices for your demand:
- Clarifying additive is an effective solution helping to enhance the transparency and glossiness of plastics. It is useful for improving the hardness and dimensional stability, as well as the smoothness of end products’ surfaces.
- Optical brightener additive is our prominent additive, which shows features that improve whiteness and brightness, as well as bring color and appearance to the finished plastic products. It is applied for blow-modded items, non-woven, raffia, etc.
- Odor-removing additive serves as a valuable solution that effectively neutralizes bad or unpleasant odors. It does not replace the original fragrance or perfume of your plastic products, instead, it prevents the absorption of unwanted smells and irritating chemicals.
- The desiccant additive is incorporated into formulations to absorb moisture that exists in plastic materials, especially technical resins, and causes fish eye and surface defects on final products, thus enhancing the overall efficiency of the production process and quality of end products.
- Flame retardant is popular in most plastic products because it can reduce flammability, smoke emission, and burning rate, which usually happens everywhere and results in much damage.
- Anti-fog additive can prevent the condensation of water, and stop water droplets from forming. This action contributes to significantly improving the plastic film's transparency and allows light to transmit more effectively.
- Anti-aging additive helps to decrease the degradative impacts of physical and chemical factors on the plastic surface, such as weight reduction, color fading, or cracking.
- The processing-aid additive is incorporated into the polymer to reduce the friction between plastics and machines during production. Without those additives, some plastic manufacturing processes ease worn-out machines, even giving bad-quality final products.
- Anti-static additive is applied to dissipate or promote the breakdown of static electricity. It also helps enhance machinability, lubrication, and mold release properties.
- Anti-UV additive is used to protect plastic products from the harmful effects of ultraviolet rays, particularly from sunlight.
- Anti-blocking additive (or anti-block agent) is combined with polyolefin films to reduce the coefficient of friction on the film surface. Polyolefin films make film processing and handling difficult because they tend to stick together.
For more detailed information, please look for it on our blog or contact us right now.