The plastic industry is constantly evolving, and at the forefront of this innovation is pultrusion. This cutting-edge manufacturing technique is producing high-quality, cost-effective composite materials that are pushing the boundaries of what's possible in the world of plastics.
By combining the strength of fibers with the versatility of resins, pultrusion is enabling manufacturers to create composite materials that are outperforming traditional counterparts.
1. Understanding pultrusion process
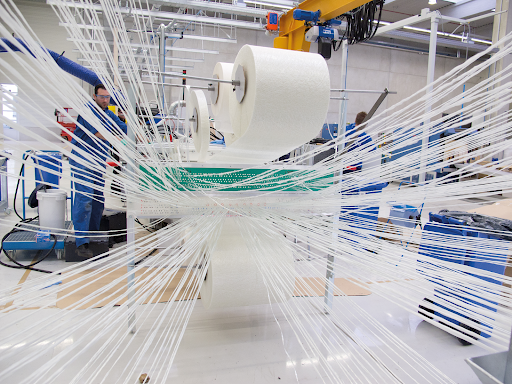
A pultrusion machine transforms raw materials into high-performance composite profiles
Early in the 1950s, a new manufacturing technique called pultrusion came onto the scene. It quickly changed the plastic industry by making high-quality, cost-effective composite materials. Pultrusion was made possible by new advances in fiber reinforcements and resin matrices, which led to the creation of lightweight, strong, and durable composite profiles.
The main tool for pultrusion is a machine that continuously turns raw materials into high-performance composites. This machine has several key components that work together to make sure the composite profiles have the right size and properties.
- Fiber creel: like a carousel that holds spools of fiber reinforcements. These fibers, usually fiberglass, carbon fiber, or aramid fiber, are like the backbone of the composite and give it strength and stiffness.
- Fiber delivery system: a carefully designed path that guides the fibers from the creel to a system that coats them in resin. This system makes sure the fibers are lined up correctly and are ready for the next step.
- Resin impregnation system: a crucial step that coats the fibers with a liquid resin matrix. The resin, usually made from polyester, epoxy, or vinyl ester, acts like glue and holds the fibers together to form the composite matrix.
- Pultrusion die: the heart of the machine. It's a heated mold that shapes the composite profile as the fiber-resin mixture passes through it. The shape of the die determines the shape and size of the profile, and the controlled heating triggers the resin to harden.
- Pulling gripper: a powerful tool that grabs the end of the emerging pultruded profile and pulls it through the die at a steady speed. This keeps the production process going and makes sure the profile hardens with the right dimensions.
- Curing system: often built into the die, provides the heat or radiation needed for the resin to harden. This change from a liquid to a solid state permanently binds the fibers together and creates a unified composite structure.
- Cut-off saw: located at the end of the pultrusion line and automatically cuts the pultruded profile to the desired length. This precise cutting makes sure the product dimensions are consistent and eliminates the need for manual work afterward.
Learn more about how some of them differ from one another: Aramid Fiber vs Carbon Fiber: What are the differences?
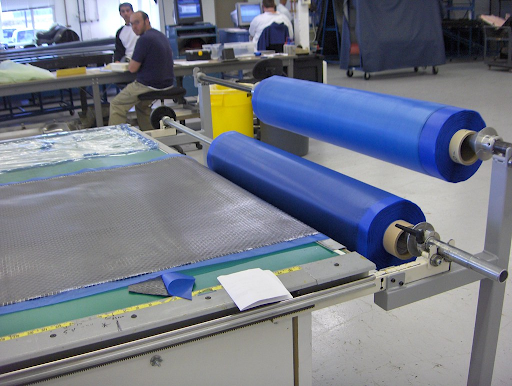
Pultrusion transforms raw carbon fibers into sleek sheets of composite
Pultrusion machines are versatile because they can work with a wide range of fiber reinforcements and resin matrices. Each type of fiber has different properties, such as strength, stiffness, and weight. Resin matrices also have specific characteristics, such as chemical resistance, flame retardancy, and electrical insulation.
This combination of fiber reinforcements and resin matrices makes it possible to create customized composites for specific applications. For example, fiberglass-reinforced polyester composites are often used in construction because they are affordable and durable. Carbon fiber-reinforced epoxy composites, on the other hand, are preferred for aerospace applications because of their exceptional strength-to-weight ratio.
2. What the plastics industry may expect from pultrusion
2.1. Strength-to-weight ratio
Pultruded composites boast an impressive strength-to-weight ratio, enabling them to withstand significant loads without becoming bulky or heavy. This remarkable property, crucial for applications where weight is a critical factor, such as in the aerospace and automotive industries, stems from the high fiber volume fraction achieved through pultrusion.
Typically ranging from 50% to 70%, the high fiber volume fraction ensures that the majority of the composite material is composed of strong and stiff fibers, while the resin matrix occupies a relatively smaller volume. This strategic combination of materials maximizes the composite's strength and stiffness while minimizing its weight.
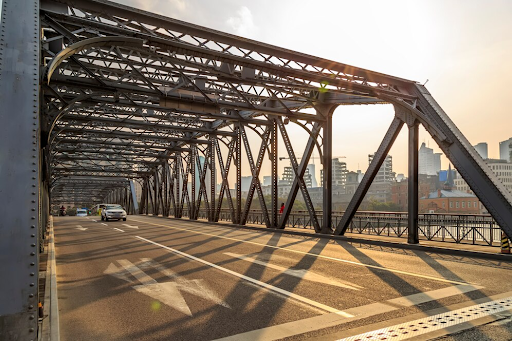
Pultruded composite profiles provide the strength, durability, and lightweight properties
2.2. Dimensional accuracy
Pultrusion ensures that the dimensions of your composite components remain consistent and precise throughout the manufacturing process. This eliminates the need for extensive post-processing and rework, saving you time and money. With pultrusion, you can be confident that your parts will fit perfectly and perform flawlessly.
2.3. Corrosion resistance
Pultruded composites are no slouches when it comes to corrosion resistance. They can withstand exposure to harsh environments, including salty air, chemicals, and extreme temperatures, without succumbing to degradation or loss of integrity. This makes them ideal for applications in marine, construction, and chemical processing industries.
2.4. Cost-effectiveness
When it comes to large-scale production runs, pultrusion emerges as a cost-effective manufacturing method. The continuous nature of the process allows for efficient production of long lengths of composite profiles, reducing material waste and minimizing labor costs. This makes pultrusion a compelling choice for manufacturers seeking to optimize their production costs.
To better understand the advantages of pultrusion, let's compare it to other common manufacturing methods for plastic composites:
Feature |
Pultrusion |
Injection molding |
Compression molding |
Extrusion |
Strength-to-weight ratio |
High |
Moderate |
Moderate |
Low to moderate |
Dimensional accuracy |
High |
High |
Moderate |
Moderate |
Continuous production |
Yes |
No |
No |
Yes |
Tailored properties |
Yes |
Yes |
Moderate |
Low |
Cost-effectiveness |
High |
Moderate |
Low to moderate |
Low to moderate |
Sustainability |
Recycled materials |
Limited |
Limited |
Recycled materials |
Versatility |
Wide range |
Limited |
Limited |
Wide range |
Durability |
High |
Moderate |
Moderate |
Moderate |
Electrical insulation |
Possible |
Limited |
Limited |
Limited |
Fire retardancy |
Possible |
Limited |
Limited |
Limited |
3. Applications of pultrusion
3.1. Construction
In the construction industry, pultruded composites play a crucial role in building resilient structures. Imagine towering skyscrapers with pultruded composite beams providing unwavering support, or stadiums with pultruded composite roofing panels shielding spectators from the elements. Pultruded composites also contribute to energy-efficient buildings by replacing heavier materials, reducing construction costs, and minimizing environmental impact.
3.2. Automotive
The automotive industry has embraced pultruded composites for their exceptional strength, lightweight nature, and corrosion resistance. Pultruded composite bumpers and door panels enhance vehicle safety and fuel efficiency, while pultruded composite electrical components ensure reliable performance under demanding conditions. Interior trim made from pultruded composites offers durability, aesthetic appeal, and reduced weight, contributing to a more enjoyable driving experience.
3.3. Marine
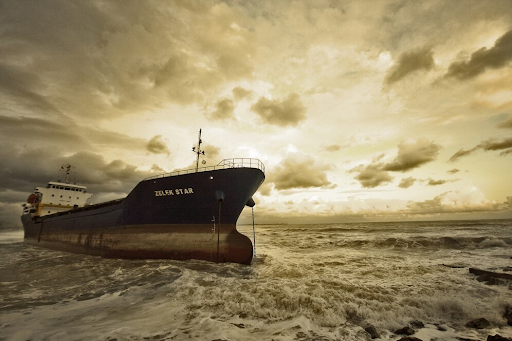
Pultruded composites withstand the harsh conditions of marine environments
Pultruded composites are the backbone of the marine industry, providing a winning combination of strength, corrosion resistance, and lightweight construction. Pultruded composite boat hulls effortlessly navigate the ocean's challenges, while pultruded composite decking materials offer durability and slip resistance. Anglers rely on pultruded composite fishing rods for their strength, sensitivity, and ability to withstand the harsh marine environment.
3.4. Aerospace
The aerospace industry demands materials that can withstand extreme conditions while maintaining exceptional performance. Pultruded composites meet these demands head-on, being utilized in aircraft components that are both strong and lightweight. Interior structures made from pultruded composites contribute to aircraft weight reduction, fuel efficiency, and passenger comfort. Pultruded composite antenna radomes provide essential protection for sensitive communication equipment, ensuring seamless operation even in the harshest aerospace environments.
3.5. Electrical and electronics
Pultruded composites serve as reliable insulators in the electrical and electronics fields, shielding sensitive components from electrical currents. They're utilized in everything from electrical insulators to connectors to ensure the safe and efficient flow of energy.
3.6. Medical
The medical industry has also discovered the value of pultrusion, utilizing pultruded composites in orthopedic implants and prosthetics. Their biocompatibility and strength make them ideal for replacing damaged bone and tissue, restoring mobility and improving quality of life.
4. Charting the future of pultrusion
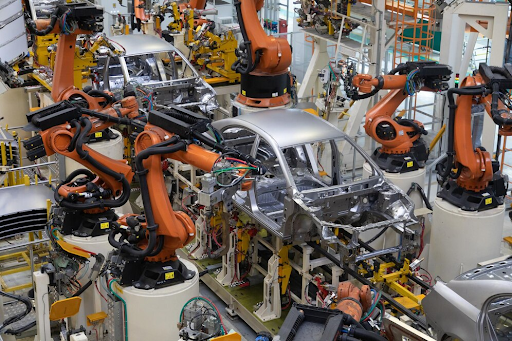
Pultrusion, a driving force in the plastics industry, is defining the future of high-performance composite materials
4.1. Novel fiber reinforcements and resin matrices
The quest for even stronger, lighter, and more durable composites is driving the development of novel fiber reinforcements and resin matrices. Researchers are exploring graphene, carbon nanotubes, and other advanced materials to create pultruded composites with exceptional properties.
4.2. Intelligent pultrusion
Pultrusion is embracing the Industry 4.0 revolution with the advent of intelligent pultrusion systems. These systems incorporate sensors and control mechanisms that continuously monitor and optimize the pultrusion process, ensuring consistent production of high-quality composites. Research shows that intelligent pultrusion is expected to reduce production waste by up to 20% and improve product quality by up to 30%.
5. Conclusion
Pultrusion's transformative impact extends far beyond its ability to create robust composite profiles. The versatility, coupled with its cost-effectiveness, has made pultrusion a game-changer in the plastic industry.
Learn about the EuroPlas blog to discover more potential and new plastic solutions that can increase your company's value in the eyes of customers.