When it comes to packaging solutions, rigid packaging and flexible packaging are two strong competitors, each with particular advantages and disadvantages. The decision made between the two can have a big influence on the packaged goods' freshness, safety, and sustainability. The article below will discuss the benefits and drawbacks of each material. Let’s follow along!
Read more: 5 types of plastic masterbatch are mainly used for packaging production
1. Understanding flexible packaging and rigid packaging
1.1. What are they?
1.1.1. Rigid packaging
Any type of packaging intended to maintain its shape even in adverse circumstances is considered rigid packaging. Rigid packaging materials include cardboard containers, metal, glass, and hard plastic, etc. Because it is difficult to destroy, this material is usually more expensive than any other kind. Pickle jars, hard plastic cannabis containers, wine bottles, hummus containers, and many more items are examples of rigid boxes.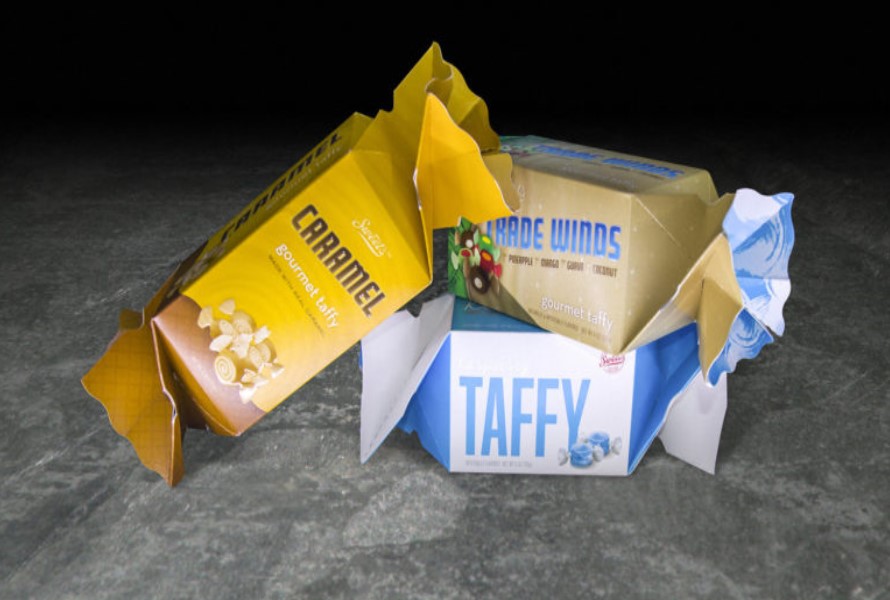
1.1.2. Flexible packaging
The type of material is designed to take on any shape, including bending and flattening. This packaging type is composed of plastic or polymers and is shaped to fit the item inside. It is a sturdy, lightweight, and portable material. High-density polyethylene is used to make flexible plastics, which are tear-and puncture-resistant and can be molded into any shape. Products like coffee, tea, candies, dried fruit, snacks, and many more are frequently made with it.
1.2. What are their differences?
1.2.1. Weight and size
Rigid packaging weighs more than flexible packaging. It’s because thicker, denser materials are frequently used to make rigid packaging. Tin cans, glass bottles, and paperboard boxes are a few examples. Conversely, flexible packaging, like sealed pouches, makes use of lighter materials like polypropylene or plastic.
The specifications determine the packaging's size. Since they can't be bundled together, rigid packages typically require more space. The purpose of rigid packaging is to keep the contents inside from deforming. On the other hand, flexible packages are flat, can be bent easily or bundled together to conserve space. Because of this, the preferred methods for shipping soft goods are poly mailers or flexible kraft paper.
1.2.2. Durability
The contents are better protected by rigid packaging. However, external deformation is a possibility. For instance, the surface is easily scratched or dented, which could harm the print or surface. Meanwhile, flexible packaging resists dents and deformations with ease. While a sharp object could puncture such packs during shipment, cosmetic abrasion is less likely to harm the flexible packaging.
Rigid packaging is typically used for the shipping of fragile goods. Electronic devices, including computer processors, cellphones, cameras, and televisions, are packaged rigidly and then placed inside protective packaging, such as air pillows or Styrofoam. The price of rigid packaging is frequently a very small portion of the total cost of the product in almost all cases. On the other hand, flexible packaging is frequently found in inexpensive goods from the food and cosmetics sectors. Foods that come in this type of package include chips, biscuits, bread, milk, frozen food, sauces, and creams.
Flexible packaging is commonly seen in the food sector due to its protective qualities. For instance, because of the way they are made, retort pouches are growing in popularity. They consist of several polymer layers and frequently metalized sheets, like aluminum. This provides internal product shielding from chemicals and heat. To help keep its contents fresh, the pack provides an airtight barrier, shields them from light and heat, and can withstand a range of temperatures.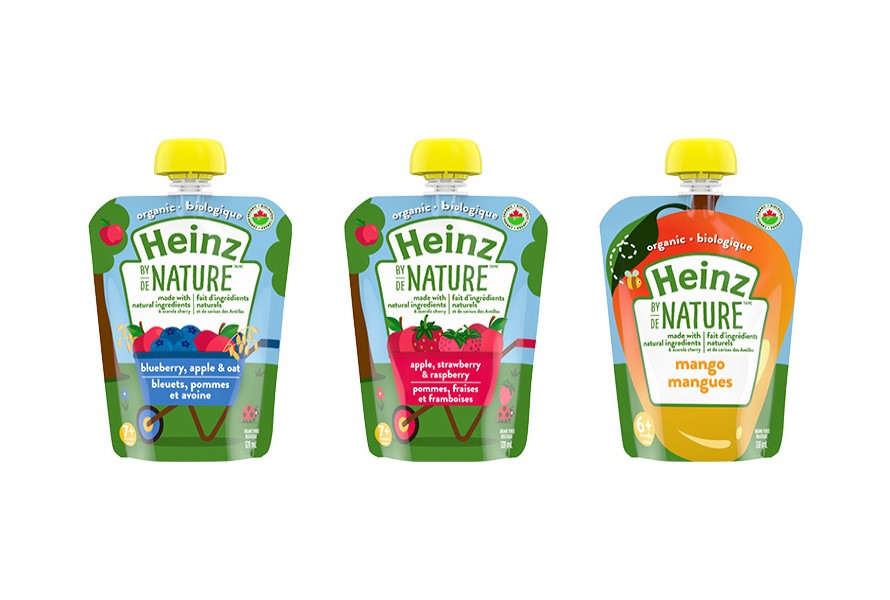
1.2.3. Customization
Flexible packaging allows easy customization. You can add any graphic or color that represents your brand by selecting from a variety of printing techniques. Furthermore, this type is easily customizable in terms of size and shape, enabling you to create a distinctive design that will help your products stand out on store shelves.Customizing rigid packaging is challenging and relatively costly. For instance, printing requires separate printing of the designs on paper, which adds to the cost, and then pasting the designs using adhesives. Rigid packaging shapes are also not very customizable in order for them to remain sturdy.
1.2.4. Impact on the environment
The materials used are the only factors that determine how packaging affects the environment. Recyclable packaging materials include flexible packaging made of polypropylene (PP) or low-density polyethylene (LDPE) and rigid cardboard or corrugated cardboard boxes. However, mixing materials makes recycling more challenging. Paperboard boxes, for instance, have plastic films or plastic pouches with metallic laminates inside of them.
2. Advantages and Disadvantages of Flexible Packaging and Rigid Packaging
2.1. Flexible packaging
2.1.1 Pros
Product protection: Delicate or fragile items are well-protected by rigid packaging. It works especially well for goods that must keep their structure or form while being stored and transported.
Biodegradability: Sustainable packaging practices are supported by the high degree of recyclable materials found in rigid packaging, such as metal and glass.
Elevated perceived value: Sturdy packaging frequently exudes durability and quality, raising the product's perceived value.
2.1.2. Cons
Bigger and heavier: Compared to flexible packaging, rigid packaging is typically heavier and more voluminous. Both the cost of transportation and the environmental impact may rise as a result.
Restricted flexibility in design: Compared to flexible packaging, rigid packaging offers less design flexibility, including size and shape. When it comes to product differentiation and customization, this limitation may be a disadvantage.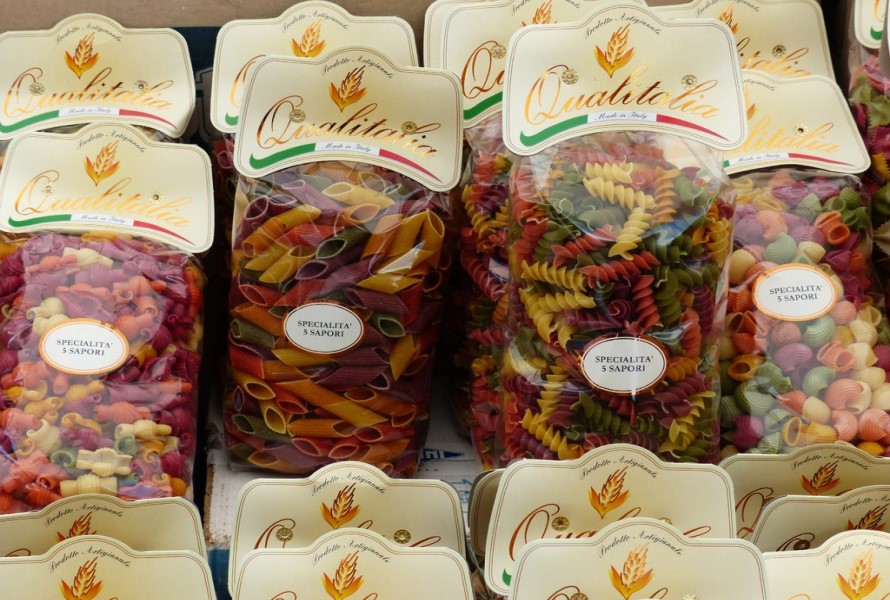
2.2. Rigid packaging
2.2.1. Pros
Convenience: Flexible packaging ensures consumer convenience by being lightweight, manageable, and frequently resealable. Product freshness is preserved after opening thanks to resealable zippers or seals, which also increase the product's usability and shelf life.
Decreased material usage: Compared to rigid packaging, flexible packaging frequently uses less material. This lowers the packaging's overall weight and, by using fewer resources during production, has a less negative environmental impact.
Cost-effectiveness: Compared to rigid packaging, flexible packaging may be less expensive to produce, transport, and store because of its lighter weight and more efficient use of materials.
Longer shelf life: An efficient barrier against moisture, oxygen, light, and other external factors is provided by flexible packaging, especially when using advanced barrier materials. This barrier's ability to preserve freshness and stop spoiling contributes to the extended shelf life of food items.
2.2.2. Cons
Low rigidity: Although flexibility has its benefits, it can also be a drawback, particularly for products that require protection from the outside pressure t. Since the material is flexible, it can’t keep its shape and can’t be used for expensive items.
Environmental concerns: Because of problems with recycling and non-biodegradability, some flexible packaging materials, especially some plastics, may give rise to environmental concerns.
3. What should you choose?
Your decision should be based on the specific requirements, such as:
- Do you want to cut your packaging expenses? If yes, then go for flexible packaging.
- Is superior product protection required? If that’s the case, then rigid packaging is the better option (except the glass material).
- Is the goal of your brand to convey luxury or exceptionally high quality? If so, the ideal option for your requirements would be rigid packaging.
- Do you want to minimize the cost of shipping? Flexible packaging makes more sense if that's the case.
- Do you or your clients care about how your packaging affects the environment? You should think about flexible packaging if your response is yes. Even though most flexible packaging cannot be recycled, it still produces less pollution overall and has a significantly smaller carbon footprint.
4. EuroPlas - A manufacturer of filler masterbatch for your packaging
With more than 15 years of producing and exporting filler masterbatch to thousands of businesses around the world, EuroPlas is proud to offer a wide range of filler masterbatch to help manufacturers save cost, enhance productivity and produce high-quality plastic products.
EuroPlas filler masterbatch combines calcium carbonate CaCO3, primary resin, and other plastic additives based on the customers' requirements. The products have many advantages, such as reduced shrinkage, improved stiffness, and bend strength, the capability to enhance stability, printability, and surface quality of the final products, and energy savings. It's ideal for injection molding, blow molding, PVC pipe manufacturing, packaging, plastic frames, door production, etc.
Here are our highlighted filler masterbatch products:
Products |
Description |
Outstanding features |
PE filler masterbatch |
It is made of CaCO3 powder mixed with suitable additives in PE resin. |
- Save production cost
- Improve several properties of end-products: brightness, opacity, shrinkage reduction,...
- Save energy thanks to CaCO3's great thermal transmission ability
- Increase the stability in manufacturing process
|
PP filler masterbatch |
It is a mixture of CaCO3 powder, PP resin and appropriate additives |
- enhance the end product's mechanical characteristics, lessen shrinkage, increase hardness and clarity
- lower production costs for companies
|
Transparent filler masterbatch |
It is a mixture of inorganic powder such as Na2SO4 (or BaSO4), plastic resins: Polypropylene (PP) or Polyphenylene (PE), and other special additives. |
- Save production cost
- High transparency, dispersion, and light resistance
- Increase the physical durability and glossiness
- Good for colored plastic products
- Save energy thanks to CaCO3's great thermal transmission ability
|
EFPE 1001 filler masterbatch |
EFPE 1001 filler masterbatch is made of CaCO3 and appropriate additives on PE resin |
- Save production cost
- Improve several properties of end-products: brightness, opacity, shrinkage reduction,...
- Save energy thanks to CaCO3's great thermal transmission ability
- Increase the stability in manufacturing process
|
EFPP 1001 filler masterbatch |
EFPP 1001 filler masterbatch is a combination of CaCO3 powder, PP resin, and appropriate additives such as processing aid or dispersion additive... |
- improve several properties of end products, including hardness, strength endurance, and product elongation.
- reduce the cost
- increase the stability in the manufacturing process, hence shortening the production cycle
|
HIPS filler masterbatch |
HIPS (High Impact Polystyrene) filler masterbatch is made of CaCO3, HIPS resin and other additives. |
- Save production cost
- Great dispersion, which brings products higher whiteness, transparency, glossiness and smoothness
- High impact strength, which allows to be easily punched, sawed, and cut
- Save energy thanks to CaCO3's great thermal transmission ability
|
If you need help in finding material for your packaging, don’t hesitate to contact
EuroPlas for the best advice and price!