Nylon vs. ABS: What Should You Choose?
When comparing Nylon vs ABS, it's essential to examine their distinct properties and performance in various applications. Both materials play a crucial role in manufacturing processes, each offering unique advantages and drawbacks. This discussion will provide a detailed analysis of their strengths and weaknesses, helping you make informed decisions for your projects.
1. Overview of Nylon and ABS
Before exploring the differences between Nylon vs ABS, we need to understand the definitions of these two materials, specifically as follows:
1.1 What is Nylon?
Nylon, scientifically classified as polyamide (PA), represents a category of synthetic polymers characterized by the absence of repeating amide groups in their molecular structure. Its journey began in 1935 when the American chemist Wallace Carothers successfully synthesized Nylon 66, marking a pivotal moment in the realm of synthetic fibers. This innovation led to the decline of natural fibers and ushered in a new era of materials with enhanced durability and versatility.
Over the years, various forms of Nylon have emerged, including PA6, PA11, and PA1010, each with unique properties suitable for a range of applications. Despite its relatively modest reputation, Nylon has found its place in diverse industries, including automotive, electronics, and power tools, owing to its strength, resilience, and resistance to wear. As a result, it continues to be an essential material in modern manufacturing, contributing to advancements across multiple sectors.
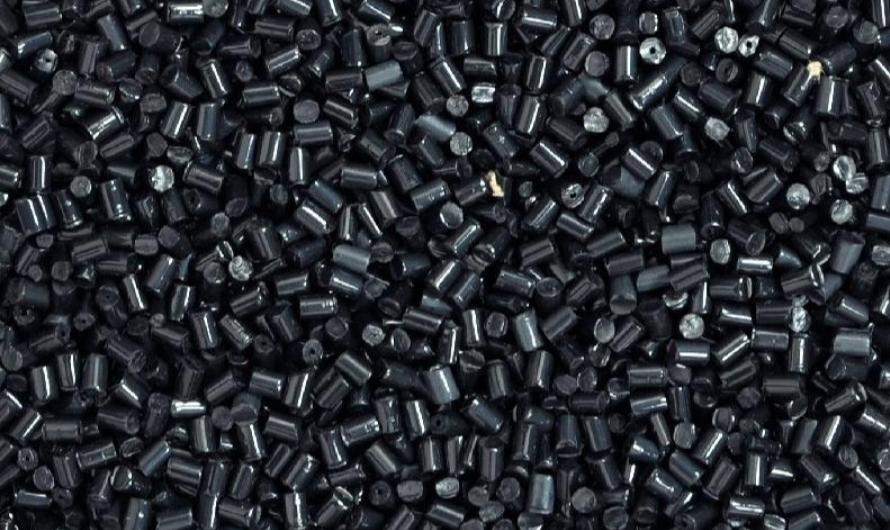
Read more: What is nylon? All about its properties and common uses
1.2 What is ABS?
Acrylonitrile-Butadiene-Styrene, commonly known as ABS, is a versatile thermoplastic polymer made from the combination of three key monomers: acrylonitrile (23–41%), butadiene (10–30%), and styrene (29–60%). This material typically appears as a light yellow or milky white granular resin, exhibiting a density ranging from 1.02 to 1.08 g/cm³. ABS is produced through two primary methods: the blending method, pioneered by the United States Rubber Company in 1945, and the grafting method, which was first developed by Marbon Company in 1954. ABS can be categorized into four distinct types based on impact resistance: medium impact, high impact, super high impact, and heat-resistant variants.
Due to its exceptional strength, toughness, and ease of processing, ABS has become one of the most widely produced polymers globally, finding applications in a broad spectrum of industries, including automotive components, consumer electronics, and various household products. Its adaptability and robust performance continue to make ABS a popular choice in modern manufacturing.
Read more: ABS plastic - Everything you need to know
2. Nylon vs. ABS: Comparing Properties
To gain a deeper understanding of these two materials, we can compare the common physical properties of Nylon vs ABS:
Property |
Nylon |
ABS |
Apperance |
Transparent or semi-transparent crystalline resin |
Opaque ivory-colored particles |
Density (g/cm³) |
1.14-1.15 |
1.02-1.08 |
Shrink rate (%) |
1-2 |
0.4-0.9 |
Melting point (°C) |
250-265 |
170 |
Heat deflection temperature (°C) |
250 |
93-118 |
Nylon is a crystalline, transparent or semi-transparent thermoplastic known for its high strength, durability, and heat resistance. In contrast, ABS is an opaque, ivory-colored amorphous thermoplastic with good impact resistance and dimensional stability. These distinct physical properties make ABS plastic vs Nylon suitable for different applications in various industries.
3. Nylon vs. ABS: Comparing Applications
Nylon's versatility and desirable properties have made it a popular choice for a wide range of engineering and consumer applications. On the other hand, ABS's balance of strength, impact resistance, and affordability has led to its widespread use in prototyping, electronic housings, and various consumer goods.
Applications |
Nylon |
ABS |
Engineering Components |
Gears, bearings, bushings, valves, and other mechanical parts requiring high strength, wear resistance, and dimensional stability. Nylon's good chemical resistance makes it suitable for applications exposed to oils, lubricants, and some chemicals. |
- |
Automotive parts |
Engine components, fan shrouds, intake manifolds, and other parts requiring durability and heat resistance. Specific nylon formulations can offer additional benefits like flame retardancy or improved impact resistance for demanding applications. |
- |
Consumer Goods |
Brush bristles, zippers, fishing line, sporting goods components, and various household items benefit from nylon's strength, flexibility, and wear resistance. |
Toys, building blocks, luggage shells, power tool housings, and various household items. |
Prototyping |
- |
Its ease of 3D printing and machining makes ABS a popular choice for creating prototypes for functional testing and design iteration. The ability to be bonded and painted further enhances its usability for prototyping. |
Electric Housings |
- |
ABS offers a good balance of strength, impact resistance, and affordability, making it suitable for casings of electronic devices like computers, TVs, and appliances. It can be easily molded into complex shapes and is available in various colors. |
Pipes and Fitings |
- |
ABS exhibits good chemical resistance and can be used for non-critical plumbing applications like drain pipes, vent pipes, and waste disposal systems. |
4. What Plastic Should You Choose?
Selecting the right plastic material for your project involves careful consideration of several key factors. Each material, ABS plastic vs Nylon, offers distinct advantages that cater to specific applications. Here are some criteria to guide your decision-making process:
- Intended Use of the Product: Determine the primary function of your product. Nylon is particularly suited for high-stress applications, offering exceptional strength and resistance to wear, which is beneficial for components like gears and bearings. Conversely, ABS strikes a balance between durability and cost, making it ideal for a wide range of consumer products and protective housings.
- Performance Requirements: Beyond mere strength, assess the additional performance criteria needed. If flexibility is a significant factor, Nylon provides greater elasticity compared to ABS. Additionally, consider thermal exposure; Nylon can withstand higher temperatures, making it a better option for heat-sensitive applications.
- Durability and Lifespan: Reflect on the expected longevity of the product. While both materials are durable, Nylon’s superior wear resistance is crucial for components subjected to continuous friction, ensuring a longer operational life.
- Environmental Considerations: Explore the sustainability of your material choices. While neither Nylon nor ABS is biodegradable, some manufacturers now offer bio-based Nylon alternatives. Additionally, consider the environmental impact of production; Nylon tends to have a higher footprint compared to ABS, which may influence your decision based on eco-friendliness.
- Cost Analysis: Evaluate the financial implications of your choice. Generally, Nylon comes at a higher cost per unit weight than ABS. Moreover, ABS is often easier to machine and 3D print, potentially resulting in lower fabrication expenses. Consider the overall production efficiency, including scrap rates and processing complexity, as Nylon’s moisture sensitivity may necessitate additional drying steps.
- Availability and Compatibility: Ensure that you have a reliable supplier for the selected material in the necessary quantities. Supply chain issues can impact material availability. Furthermore, assess whether your existing manufacturing equipment can accommodate the chosen plastic. Nylon may require specialized machinery for effective high-temperature processing.
By carefully weighing these factors, you can make an informed decision that aligns with your project’s requirements and objectives.
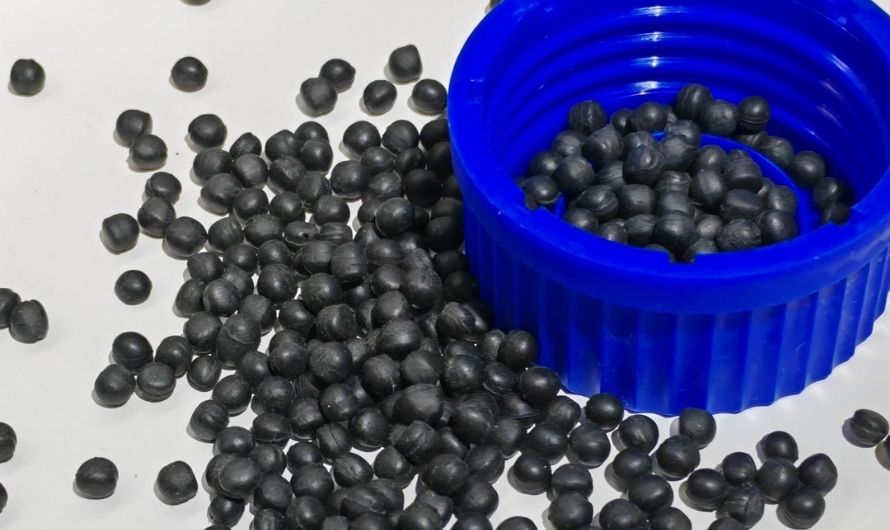
5. Conclusion
In conclusion, both Nylon vs ABS are outstanding thermoplastic materials, each with distinct advantages. Nylon is ideal for applications requiring high strength and temperature resistance, making it suitable for components facing significant wear. Conversely, ABS excels in processability and cost-effectiveness, making it perfect for mass production of consumer goods and complex designs. The selection between these materials should be based on the specific needs of your project to ensure optimal performance.
6. About EuroPlas’ PA and ABS Products
EuroPlas is proud to offer a superior range of PA and ABS products designed to meet the diverse needs of modern industries. Our PA6 and PA66 blend compounds deliver exceptional mechanical properties, making them ideal for demanding applications in the automotive and motorcycle sectors. With a perfect balance of resilience and strength, these materials are engineered to provide reliable performance in components such as roller bearings and fuel tank lids.
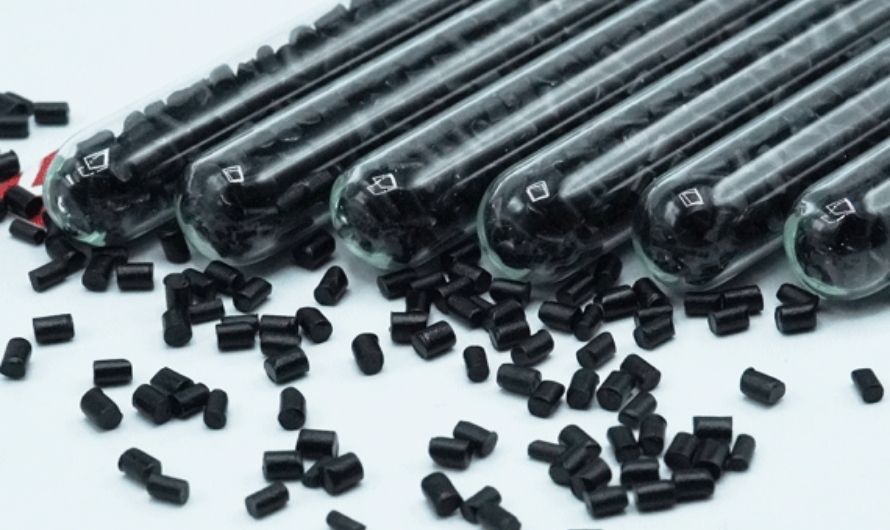
In contrast, our ABS flame retardant compounds combine outstanding processability with enhanced fire safety features. Modified with halogen-free additives, these materials are tailored for applications where fire resistance is paramount, such as electronic housings and mobile chargers.

Both product lines are crafted to ensure ease of processing and customization based on specific end-product requirements. To discover how EuroPlas can elevate your production capabilities with our advanced PA and ABS solutions, contact us today and let our expertise help you achieve your project goals.