Plastic additives for PVC are an important element to add to the production process of PVC applications. They are known to improve the process capabilities and strengthen the physical and mechanical properties of the end products. These additives include different types with specific usage. Let's dig into the details below to find out more about the topic!
Đọc thêm: What are plastic additives? 8 most common plastic additives in plastic industry
1. What are Plastic Additives for PVC?
PVC, or Polyvinyl chloride, is one of the most synthesized plastics used in a wide range of applications. Without additives, PVC would not be that useful and versatile. Thanks to these added elements, you can color it and make it softer, more processable, and longer its life span.
All polymers need stabilizers of one sort or another, and so does PVC. In order to meet the requirements of durability, plastic additives for PVC play an important role in achieving this goal.
2. Types of Plastic Additives for PVC
All types of plastic additives for PVC are useful in modifying processing properties, product characteristics, and quality. They include:
2.1. Stabilizers
Heating is one of the steps in PVC processing that often make the plastic degraded and create hydrochloric acid. Therefore, to avoid potential degradation, manufacturers usually add stabilizers. The heat stabilizers will work to neutralize hydrochloric acid and prevent oxidation.
Tin stabilizers are one of the stabilizing agents imparting heat stability and retaining color to rigid and plasticized PVC. In addition, it also allows the final products to tolerate oxygen, heat, and UV light.
2.2. Waxes
Waxes are commonly used in production and fabrication. They are in charge of internally and externally lubricating, enhancing processability, and improving the smoothness of the end products. Polyethylene, chloro-polyethylene, Fischer-Tropsch wax, and paraffin wax are some common names of PVC waxes.
2.3. Plasticizers
Plasticizers are added to make the PVC hot substance suitable for flexible products and more elastic without changing shape. Plasticizer additives improve flexibility by reducing the attraction between polymer chains.
2.4. Pigments
The original color of PVC is white, but it is possible to have other colors with additives. Many suppliers apply the pigments to PVC products to create diverse color, gloss or other functional properties. Some of the common pigments include zinc oxide (ZnO), zinc sulfide (ZnS), titanium dioxide, and naphthol red 210.
2.5. Flame Retardants
It is a common type of PVC additive to impart fire retardancy to plastic products. It not only helps slow and stop smoke and flames but also protects the structural integrity of PVC material. Popular kinds of flame additives are decabromodiphenyl ethane (DBDPE), zinc borate, ammonium polyphosphate phase II (APP-II), aluminum trihydrate, and antimony trioxide.
3. Application of Plastic Additives for PVC
Since PVC is combined with additives, its applications are even more varied. PVC products can be transparent, opaque or colored, rigid or flexible, conducting or insulating, making it suitable for a variety of needs Plus, the lifespan (from 10 to 100 years) of the majority of PVC applications is longer than other thermoplastics.
Some of the most common applications are car seals, flexible roof membranes, pipes, and window frames. In addition, it is also applied to medical services.
4. FAQs
4.1. Do Phthalate Plasticizers Used in Soft PVC Cause Cancer?
No, there is no evidence that Phthalate Plasticizers pose a significant health hazard to human beings. Much research and investigation have been conducted, but the general result is it may be the reason for liver tumors in rodents by a mechanism that does not occur in humans.
4.2. Are Potentially Toxic Metal Additives Included in PVC?
Metals that are immobilized in plastic products are in the same way as they are in traditional glass ones made from lead crystal. It means metals will not be released during the service life of the products. Plus, these materials need to meet strict requirements of the existing regulations where risk assessments play an important role. This process of assessing the risks of additives is fully acknowledged, supported, and involved by the PVC industry, and the removals are conducted when required.
5. Plastic Additives for PVC From EuroPlas
Since plastics are mostly inexpensive and easy to process, they are widely used in many industrial fields. However, not all the resins meet the requirements of the final products. Understanding this fact, EuroPlas introduces a wide selection of plastic additives to improve production efficiency and end-products functions.Plastic additives from EuroPlas are applied during the production process to guarantee the material is high-performance when molded and used. Since these substances decrease friction between materials and the machine wall, they allow more high-performance manufacturing. Plus, they improve the capability to be resistant to different environmental conditions, durability, and longevity of the plastics.
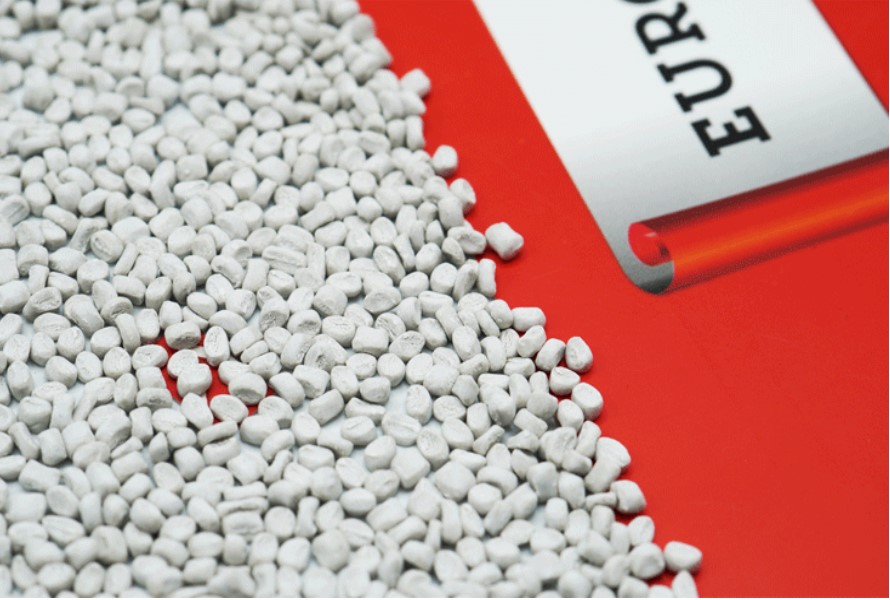
The list of plastic additives from EuroPlas includes Odor removing additives, Desiccants, Flame retardants, Anti-fog additives, Anti-aging additives, Processing-aid additives, Anti-static additives, Anti-UV additives, and Anti-blocking additives.
Types of additives |
Outstanding features |
Applications |
Odor removing additives |
- Limit the unpleasant smells of plastic, thus improving the quality of end-products
- High compatibility
- Tailor-made based on customer requirements
|
- Home appliances
- Toys
- Textile packaging
|
Desiccants |
- Absorb moisture in the raw materials, thereby limiting common errors in processing (bubbles, fisheyes, etc.)
- High level of compatibility
- Great dispersion
Improve the processing efficiency
|
- Blown films
- Raffia
- Injection molding
|
Flame retardants |
- Limit the spread of fire by working on the plastic surface
- Good dispersion with most standard resin
- No mechanical degradation caused to end-products
- Reasonable price
- No equipment corrosion
|
- Mobile charger
- Power socket
- Electronic components
|
Anti-fog additives |
- Prevent water condensation on the plastic surface and ensure the transparency of the plastic film
- Suitable for using conditions
- An appropriate amount of use (ensure travel speed)
- Long operating time
- It can be combined with other additives (such as anti-UV additives, anti-block, and slip)
- It does not affect the mechanical properties and color of the product
|
- Food wrap
- Mulch films
- Food packaging films
- Greenhouse films
|
Anti-aging additives |
- Prevent degradative impacts of physical and chemical factors on the plastic surface
- Great dispersion
- Stable products quality
|
- Plastic exterior
- Artificial grass
- Stadium chair
- Cars interiors and exteriors
- Agricultural films
|
Processing-aid additives |
- Reduce the friction between the surface of the polymer and the processing equipment.
- Eliminate cracking and improves surface during film blowing.
- Avoid plastic stains on the equipment.
- Thermal stability when handling at high temperature
- Eliminate gelation during the processing.
- Improve efficiency in processing recycled plastic.
- Reduce extrusion pressure thanks to the decrease of friction and resistance between plastic flow and extrusion equipment surface.
- Reduce the processing temperature, equipment capacity, and productivity.
- Easily combined with other additives without affecting the mechanical properties of end-products
|
- Blown films
- Raffia
- Extrusion
|
Anti-static additives |
- Prevent UV light's negative impacts on end-products
- Maintain end-products mechanical properties and improve end-products durability
- Great dispersion without spots
- Strongly absorb organic UV lights
- Permanent effectiveness
|
- Mobile charger
- Power socket
- Electronic components
- Blown films
- HDPE bottles
|
Anti-UV additives |
- Prevent UV light's negative impacts on end-products
- Maintain end-products' mechanical properties and improve end-products' durability
- Great dispersion without spots
- Strongly absorb organic UV lights
- Permanent effectiveness
|
- Plastic exterior
- Artificial grass
- Stadium chair
- Cars interiors and exteriors
|
Anti-blocking additives |
- Reduce the blocking on the film's surface, resulting in more efficient processing
- Ensure the level of transparency of the films
|
- Food wrap
- Textile packaging
- Food packaging film
|