The technique of printing nylon has recently become popular thanks to its specific features and numerous opportunities to be utilized. Let’s view the top reasons why nylon is perfect for your 3D printing needs, the process of 3D printing nylon, and tips and tricks for optimal results from printing nylon.
Read more:
What is nylon? All about its properties and common uses
3D Printing With Nylon: What You Need To Know
What can you 3D print with plastics?
1. Why Choose Nylon for 3D Printing?
Nylon is also referred to as polyamide and adopted for 3D printing due to its fascinating physical and mechanical characteristics. Thus, nylon stands out against other 3D printing materials. They provide a blend of advantages that is highly desirable in various 3D printing nylon uses.
1.1. High strength-to-weight ratio
Nylon packing is a strong material but has a good balance of strength and weight, which is suitable for the formation of lightweight 3D printed components. This characteristic is highly advantageous for situations that require lighter vehicles such as automobiles, aircraft, and even home appliances.
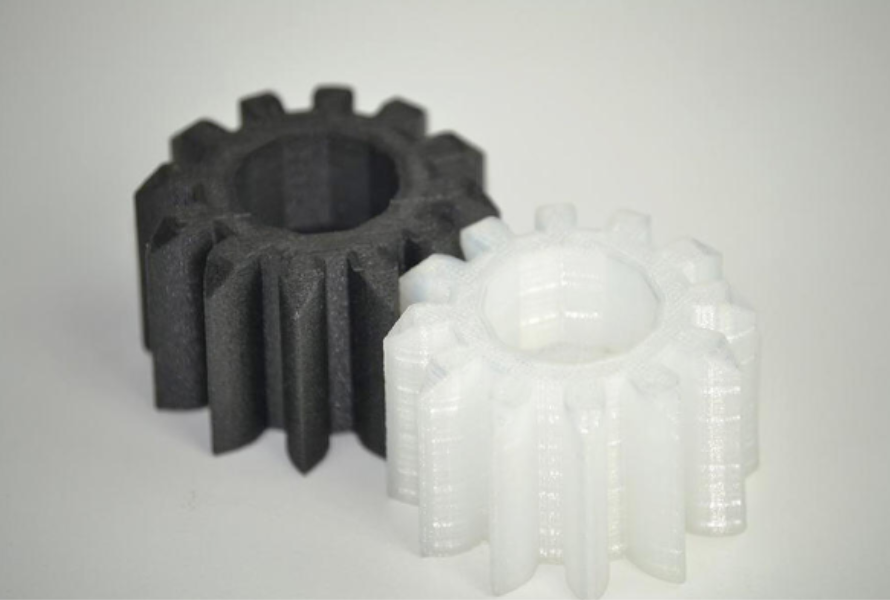
Nylon creates a high strength-to-weight ratio for 3D printed products.
1.2. Excellent impact resistance
Another noteworthy feature of nylon is its extremely high impact resistance. Consequently, parts made with nylon base in the 3D printing technology exhibit more acceptable tolerance on high levels of impacts, shocks and sudden loads without compromising the structural capacity of the component.
1.3. Tolerate wear and abrasion well
Nylon stands out in this respect because, among many materials that are printed in 3D, it possesses a significant level of abrasion and wear resistance. Hence, nylon parts are capable of maintaining the original appearance and size of their surface even when subject to cyclic stress or friction.
1.4. Dimensional stability
For nylon, dimensional accuracy is found to be highly acceptable; a Nylon 3D printed part has no significant change in size and shape irrespective of changes in temperature or humidity. It is ideal for sections that require strict tolerance and accurate dimensions.
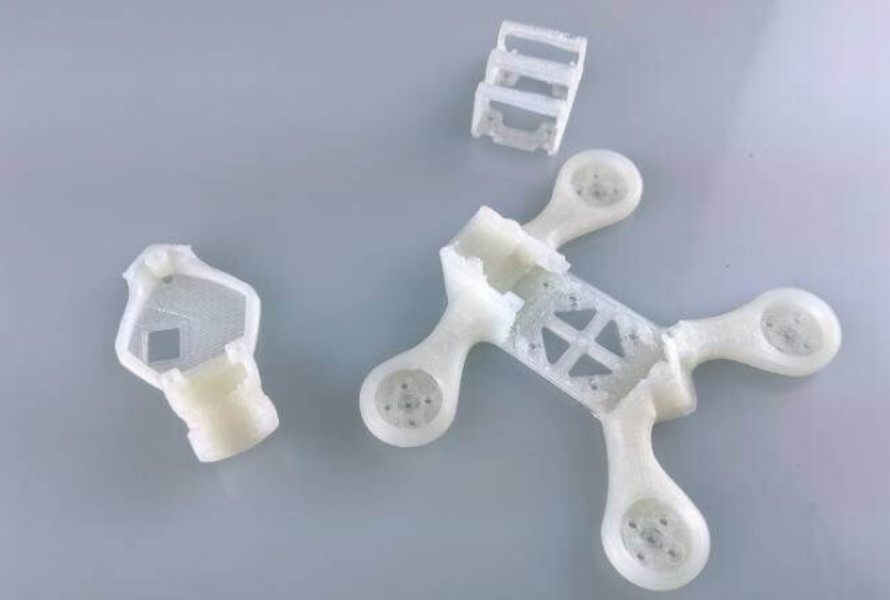
For items with precise dimensions and tight tolerances, printing nylon is essential.
2. Techniques for 3D Printing with Nylon
2.1. Fused Deposition Modeling (FDM)
A common 3D printing technique for printing nylon materials is Fused Deposition Modeling. In the process, a material such as nylon is threaded through a heated cylinder and extruded as a filament onto a substrate to create layers that eventually form a three-dimensional object.
While this process is affordable but very popular, it is mainly employed in home and micro 3D printing applications with nylon.
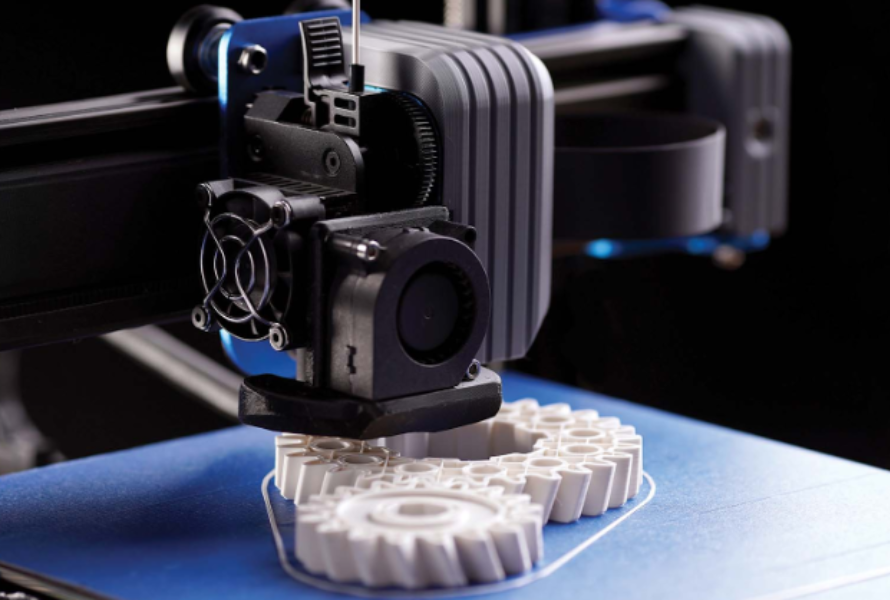
Among all the available methods, Fused Deposition Modeling (FDM) is widely used for printing nylon.
2.2. Selective Laser Sintering (SLS)
Overall SLS or Selective Laser Sintering is a suitable 3D printing nylon process that utilizes powder. In this process, a high power laser selectively melts the powder particles of nylon and fuses them to build different layers of the required 3D object.
SLS is also capable of producing dense, refined and durable nylon parts with high accuracy and stability without the need for reinforcement structures.
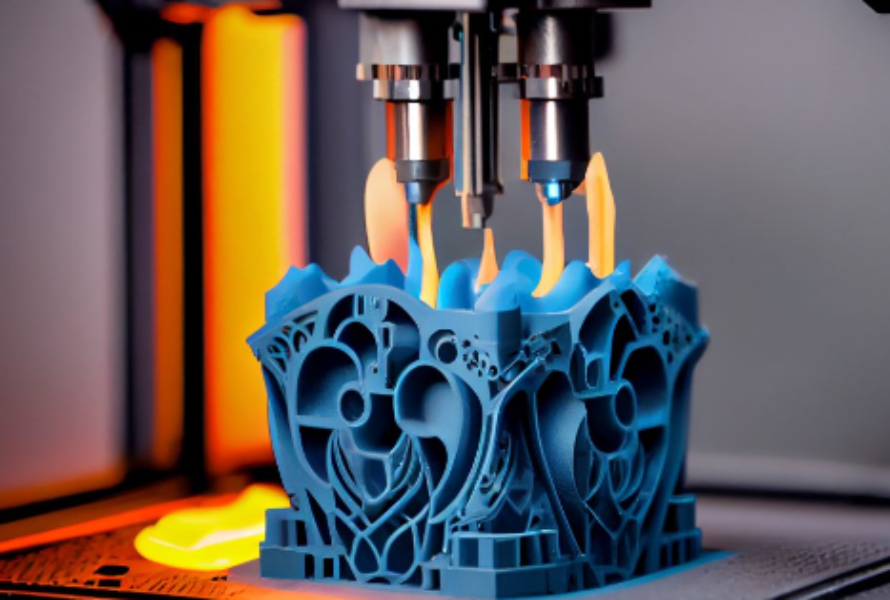
SLS is one of the best options in powder-based 3D printing nylon techniques.
2.3. Multi Jet Fusion (MJF)
Multi Jet Fusion, or MJF, is a relatively newer method of using nylon in 3D printing that has a good level of acceptance. In the MJF process, a nylon powder is selectively sintered and bonded to become solid by a combination of heat and chemicals to provide detailed and durable nylon parts.
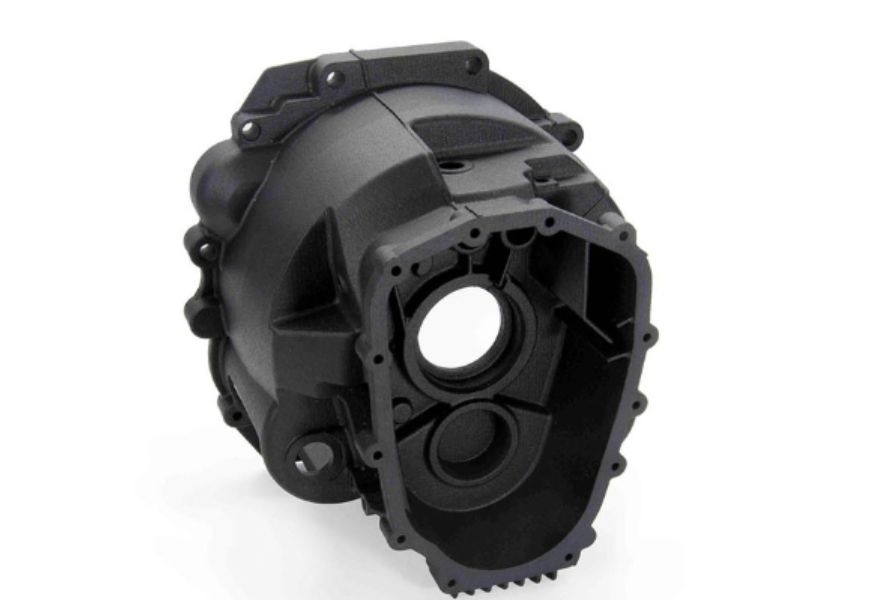
Multi Jet Fusion (MJF) is a new method of printing nylon.
2.4. Stereolithography (SLA)
Although less common for the production of 3D printing nylon compared to the other processes described below, Stereolithography, also known as SLA, can be used to create nylon parts.
In this process, an SLA machine employs a UV-curable nylon resin and then it solidifies each layer by layer to develop the 3D object. In general, the components that are fabricated through SLA provide good surface finish and dimensional stability.
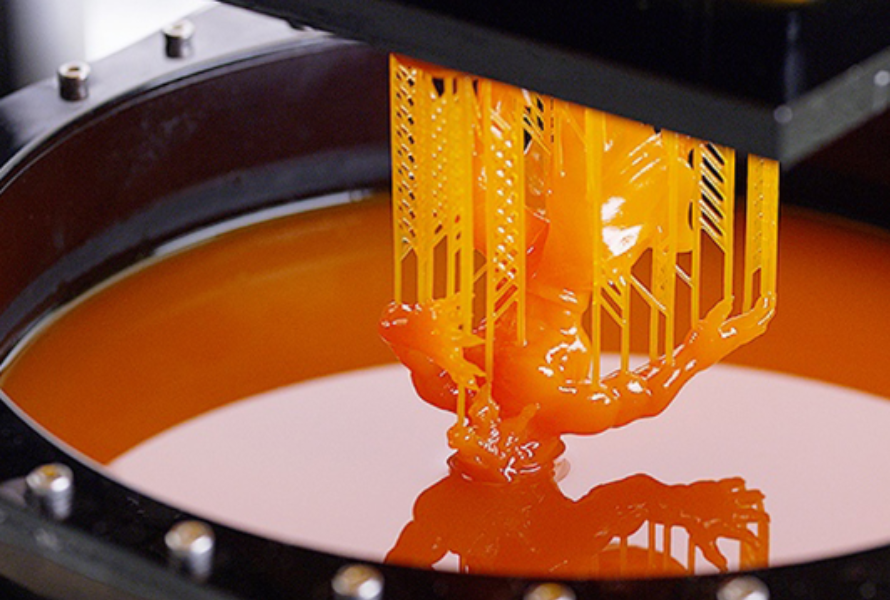
Another technique for 3D printing nylon is Stereolithography (SLA).
3. Best Practices for Successful Nylon 3D Printing
Experimentation with different settings and techniques may be necessary to achieve the best results for your specific application. Here are the best practices in 3D printing nylon that you can refer to:
1. Printer Preparation
- Make sure that the surface of the print bed is clean and there is no residue on it.
- Adjust the printer sizeable in order to attain a level print bed.
- The print bed temperature should be set at any value between 80–100 degree Celsius depending on the type of nylon filament.
2. Filament Selection
- Use good-quality nylon filament, atomically PA6 or PA12, from a reputable manufacturer.
- Ensure the filament is dry and, therefore, stored correctly to prevent absorbing moisture, which seems to be the main cause of print failure.
- Use a nylon filament with a low melting point since it is easy to print.
3. Print Settings
- Printing nylon at slower speeds, typically 20-40 mm/s, to allow the nylon time to adhere to both the print bed and the layer below. Increase the first
- layer height to 0.3-0.4 mm to achieve better initial layer adhesion.
- Increase top layers and bottom layers to increase part strength and surface finish.
4. Part Cooling
- It is important for nylon to be exposed to no or very little cooling. Talking about the part cooling fan, it is better to lower or even shut it down.
- Begin with it off for the first layer or two, then turn it on low at first.
5. Warping Prevention
- It is then recommended that an adhesion promoter be applied to the bed to ensure the adhesion of the part.
- The first few layers should be urged to print at slow speed so that the nylon sticks properly to the print bed.
6. Post-Processing
- Make sure that the printed part cools uniformly to prevent warping or cracking after the print has been completed.
- The part may be subjected to an annealing process in a heated furnace to enhance mechanical characteristics and stability of dimensions.
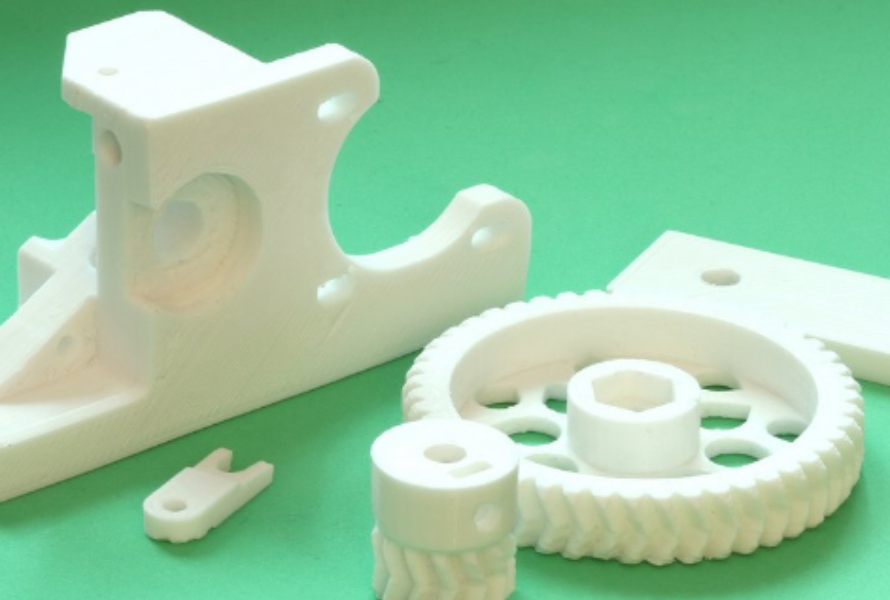
It can be required to experiment with various settings and procedures in order to achieve success in 3D printing nylon.
4. Troubleshooting Common Issues with Nylon Printing
Despite offering excellent mechanical properties and part durability, it is also prone to common issues in printing nylon such as:
Issue of printing nylon |
Causes |
Solutions |
Warping |
Rapid cooling, uneven cooling, poor bed adhesion, high print speeds |
- Increase bed temperature (80-100°C)
- Use a brim or raft to improve bed adhesion
- Reduce the speed of printing nylon (20-40 mm/s)
- Use an enclosure or print in a warm environment
- Apply adhesion promoters like hairspray or glue to the bed
|
Poor Layer Adhesion |
Insufficient interlayer bonding, low extrusion temperature, uneven extrusion |
- Increase nozzle temperature (240-270°C)
- Slow down the speed of printing nylon (20-40 mm/s)
- Increase extrusion multiplier (105-110%)
- Check for partial clogs or worn nozzle
|
Stringing/Oozing |
Overheating, retraction settings, high print speeds |
- Decrease nozzle temperature (240-260°C)
- Increase retraction distance and speed
- Reduce the speed of printing nylon (20-40 mm/s)
|
Brittleness/Low Strength |
Insufficient cooling, print orientation, layer height |
- Anneal the printed part in an oven (150-180°C for 2-4 hours)
- Print parts with the strongest orientation (e.g., along the length)
- Reduce layer height (0.1-0.2 mm)
|
Surface Roughness |
Uneven extrusion, nozzle size, layer height |
- Decrease layer height (0.1-0.2 mm)
- Use a smaller nozzle size (0.4 mm or less)
- Calibrate extruder steps and flow rate
|
Part Delamination |
Insufficient interlayer adhesion, moisture in filament, low bed adhesion. |
- Increase nozzle temperature (240-270°C)
- Dry the nylon filament thoroughly before printing
- Increase bed adhesion with promoters or a brim/raft
|
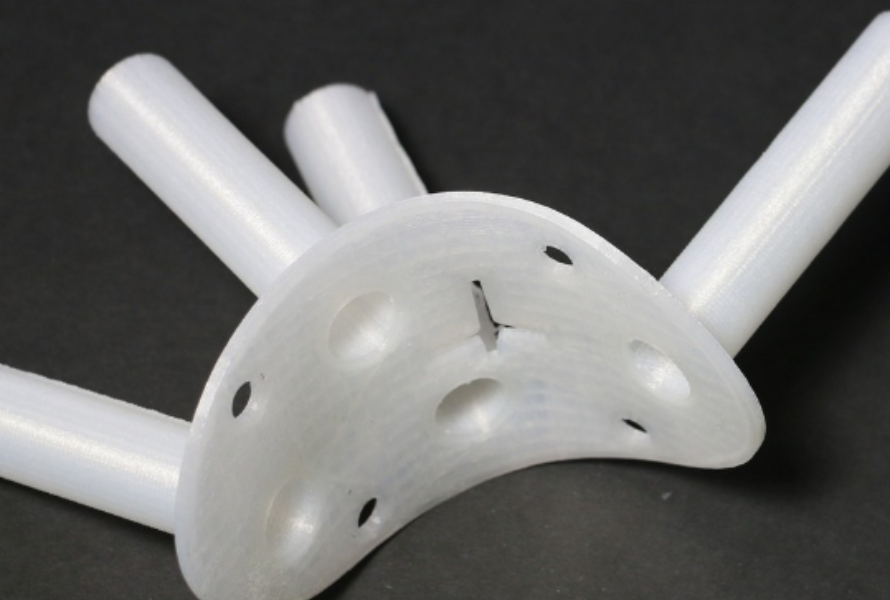
There are also some problems when printing nylon despite its good properties.
Read more: Problems you might encounter in 3D printing
5. Advanced Tips for Mastering Nylon 3D Printing
5.1. Utilize print bed adhesion techniques
Achieving reliable bed adhesion is crucial when having 3D printing nylon. One effective method is to apply a thin, even layer of glue stick to the print bed before printing. The adhesive properties of the glue stick help the nylon part adhere securely to the surface.
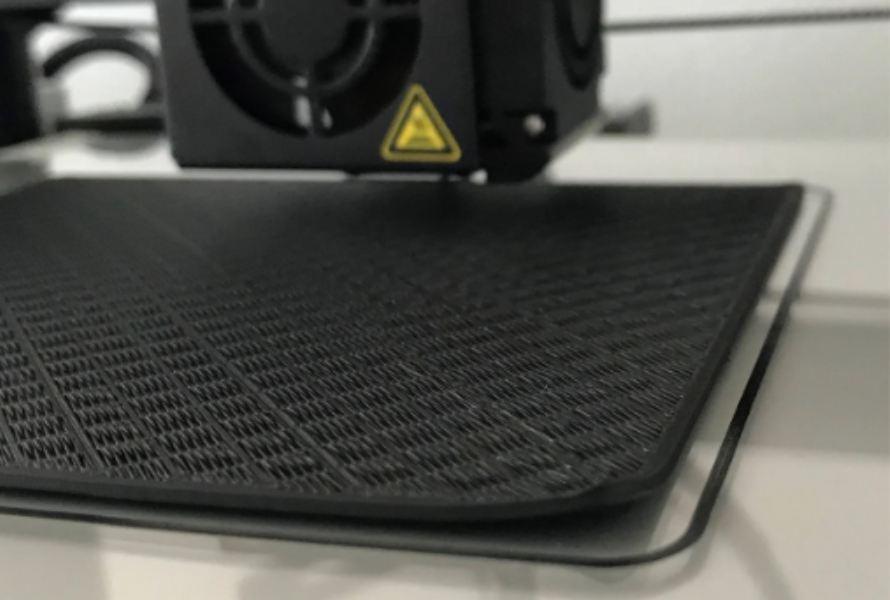
Applying a thin, even layer of glue stick to the print bed prior to printing nylon is one efficient technique.
5.2. Slow down print speeds
Nylon can be challenging to print at high speeds due to its tendency to warp and separate between layers. To mitigate these issues, it's recommended to slow down the speed of printing nylon significantly, typically between 20-40 mm/s.
5.3. Control bed and nozzle temperatures
Proper temperature management is essential for success when 3D printing nylon. The optimal bed temperature range for nylon is typically between 80-100°C. Higher bed temperatures help reduce warping and improve layer adhesion.
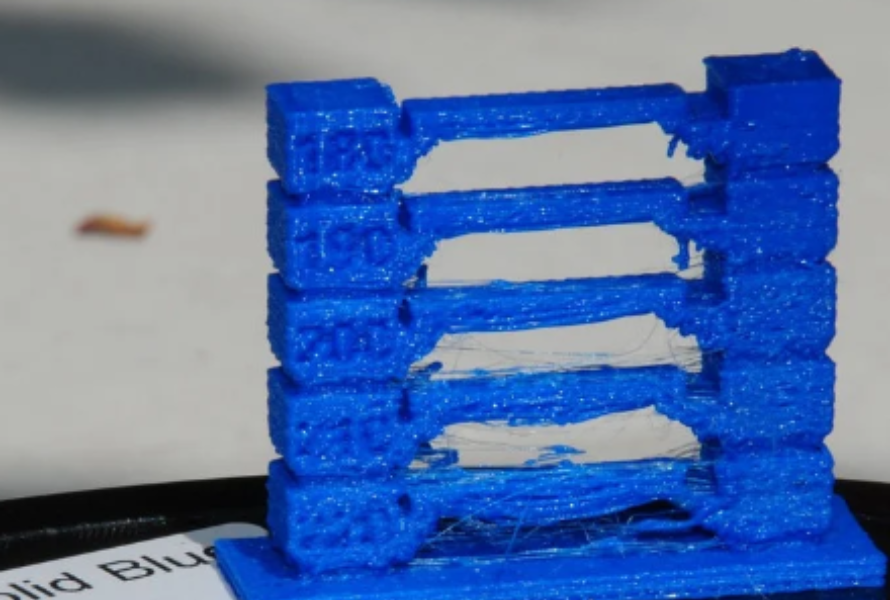
Carefully monitoring and adjusting both the bed and nozzle temperatures is good for printing nylon.
5.4. Enable retraction
Retraction is a crucial feature for 3D printing nylon, as it helps prevent oozing and stringing. Retraction works by pulling the filament back slightly when the nozzle moves between extrusion points, reducing the amount of material being deposited in unwanted areas.
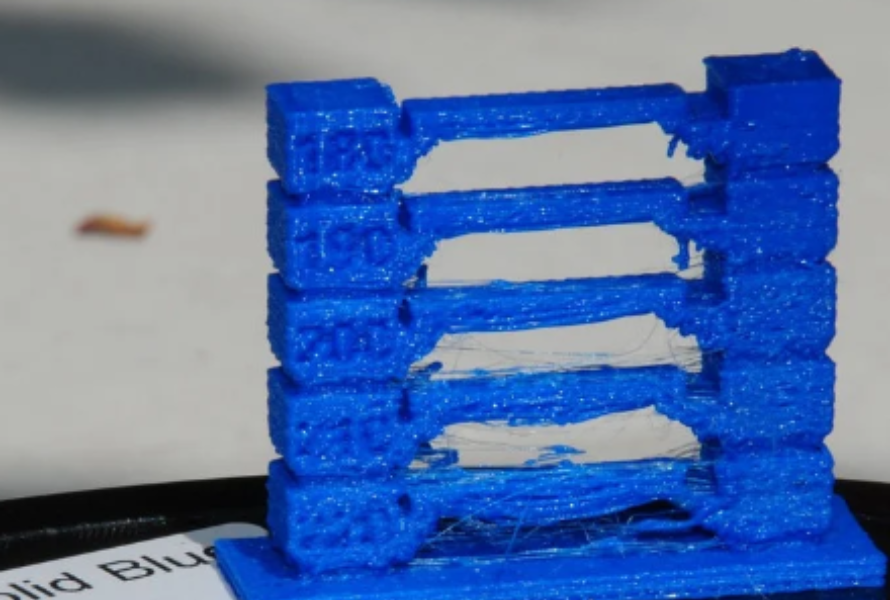
Retraction is a useful feature in nylon 3D printing.
6. Conclusion
There's no doubt that nylon has become an essential material in 3D printing. By implementing these best practices and continuously experimenting with your printing nylon process, you'll get success for your needs.
7. About EuroPlas’ Polyamide Products
EuroPlas is a leading supplier of high-performance engineering plastics, including a range of polyamide materials. Our polyamide product portfolio caters to a variety of industrial applications and 3D printing nylon needs.
EuroPlas’s Polyamide (PA) product includes:
Contact us right now for more information and support for your printing nylon needs.