Plastic colors are considered an extremely important factor in determining the aesthetics and appeal of many products in human life. Color has long been an indispensable part of the commodity industry, helping to show the eye-catching branding of many businesses and expressing the individual personality of users. The following article will provide the most detailed look at plastic colors, the strong influence and wonderful effects they bring to applications. Let's find out right after this!
1. The Role of Colorants in Plastic Manufacturing
In the manufacturing process of plastics, plastic colors have a very important contribution to the appearance and some functions of the product in many ways. Here are their main roles:
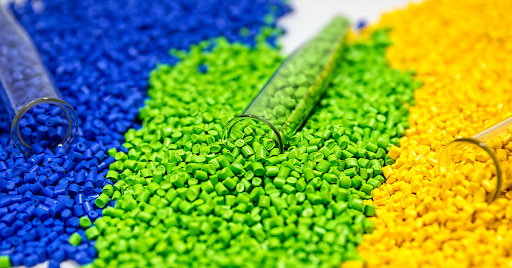
Color has long been an indispensable part of the commodity industry
1.1. Aesthetic value
Plastic colors can dramatically improve the look of the product. It can be easily seen that many shades are created by plastic colorants which improve the aesthetic of the product perfectly. Some brands can build brand recognition in this way.
With flexible and customizable colors, the product will have more charm, as they can meet the personality of the user. In addition, it's known that using bright vibrant colors catches the eyes of customers.
1.2. Product identification
Today, the colors of plastics are among those factors that help the product to be classified and identified hastily and effectively. In many industries, there is a crucial use of color coding as the prime basis for product classification and management. Some divisions highly acknowledge the application of color charts when it comes to classification, like medical devices, accessories, clothing, and even automotive body parts.
1.3. UV protection
In fact, plastic colors can enable products to perform better in environments exposed to direct sunlight over a longer period of time. More specifically, colorants that block UV will protect plastics from degradation by sunlight. This helps prolong the life of a product by preventing fading, brittleness, and damage resulting from exposure to ultraviolet rays.
1.4. Function marking
The other big role that plastic colors can definitely play is in defining the features and notes of a product. In this respect, many technical devices use plastic colors to mark areas of safety, activity levels, or separate functional parts. Such a role is helpful in improving the ability of recognition and proper use of products in compliance with the safety regulations. In particular, they are easy to recognize and suitable for all ages.
1.5. Thermal resistance
Most plastic colors are ideal for applications that require high durability. Some of these colorants are heat-resistant and thereby assist plastic products in withstanding higher temperatures, which make durability of products fulfilled in most operating environments. Thanks to plastic colors, the products help not only with aesthetic value but also with durability and function in many different industries.
2. Effects of Color Additives on Plastic Properties
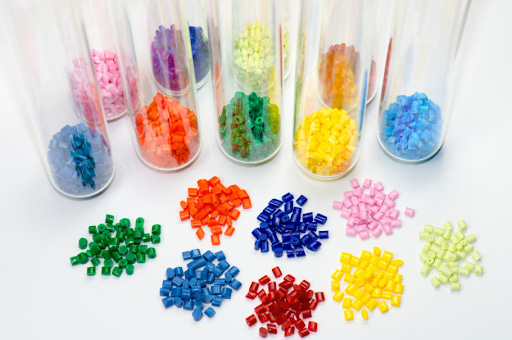
Plastic colors also have the ability to change the surface texture to improve the tactile and aesthetic qualities
2.1. Eye-catching appearance
Plastic colors provide colors that bring vibrant shades to the product. Because of this, plastic products can realize some of the aesthetic properties of the brand and design that the business desires. This makes the product stand out to attract consumers and increase the purchase rate.
2.2. Enhanced gloss and texture
Color additives in plastic colors can also enhance the gloss or opacity of the plastic. In addition, plastic colors also have the ability to change the surface texture to improve the tactile and aesthetic qualities that the product brings to the user. This is especially important for consumer goods, where feel and appearance are an integral part of the individual experience.
2.3. UV resistance
Some additives protect the plastic from ultraviolet rays, thereby minimizing fading or degradation over time. From this it can be seen that plastic colors provide the best performance for products exposed to outdoor environments.
2.4. Thermal stability
The heat-resistant additives in plastic colors help prevent color changes and warping at high temperatures. This effect from plastic colors helps maintain the perfect appearance and integrity during product use especially when the product operates in harsh environments for a long time.
2.5. Mechanical strength
In plastic colors, some colorants dramatically enhance the durability of the product. By providing structural integrity to the equipment parts, plastic colors have become important in many life and technical applications.
2.6. Chemical resistance
Additives that increase the chemical or moisture resistance of plastics are also one of the extremely popular topics when it comes to plastic colors. Thanks to this ability, the product can operate durably in environments exposed to abrasive chemicals such as acids, salts, grease and some other solvents.
3. Color Choices and Their Applications
For plastic colors, most colors serve aesthetic purposes, mark functions, and sometimes serve as safety warnings. Let's take a look at some of the color choices for plastics in some typical industries right below.
Plastic colors are very popular in the food and beverage industry
3.1. White and transparent
In medicine, white plastic colors are often used because of their clean, sterile appearance. In addition, transparent plastic devices will help users easily see the container inside. This allows users to check the contents of a syringe or IV bag almost immediately.
3.2. Black and gray
Black and gray plastic colors are widely used in automotive plastics because of their durability and opacity. These colors are used to make dashboards, trims, and other engine parts that require UV and heat resistance.
3.3. Transparent and color-coded
These plastic colors are very popular in the food and beverage industry. In fact, clear plastics are popular in bottles and containers to display the contents. A color-coded lid or label will help identify the product. The colors used must even be food-safe and non-toxic.
3.4. Dark plastic colors
This color tone is considered one of the anti-static colors for the electronics industry. Electronic devices often use dark colors, with additives that enhance anti-static properties to avoid dust accumulation and also avoid electrostatic discharge on highly sensitive components and packaging.
3.5. Green and black
Green and black plastics are often used in agriculture, such as in mulch films, greenhouse coatings and irrigation pipes. Green often indicates environmentally friendly or biodegradable products, while black blocks light from passing through, aiding in weed control.
3.6. Bright colors
In household products, bright colors such as red, blue and yellow are often used to enhance the aesthetics of the item. These colors make everyday items, like containers and kitchenware, more vibrant and easier to organize by color.
4. Conclusion
In conclusion, plastics colors play an important role in improving the quality and aesthetics of plastic products in many different industries. In particular, understanding color additives also helps manufacturers control the appearance, durability, UV resistance, heat resistance and antistatic properties of the manufactured products. In addition, some specific colors are also characteristic and meet the specific needs in the application of many different manufacturing industries. It can be seen that plastic colors are extremely essential for a progressive manufacturing industry and a sustainable development goal.
5. About EuroPlas’ Color Masterbatch
EuroPlas is proud to be a world-leading color masterbatch supplier with many years of experience. We bring high-quality products manufactured through the most advanced techniques and machinery.
EuroPlas's color masterbatch is meticulously designed to achieve the most accurate color in plastic products. In addition, EuroPlas's team of highly technical experts enthusiastically discuss and consult with customers to research and develop color masterbatch products that best suit each project's specific requirements.
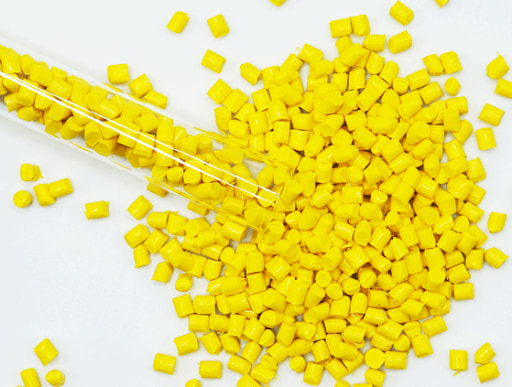
EuroPlas's color masterbatch is meticulously designed
EuroPlas has a variety of colors available and is confident that it can meet the diverse requirements of customers. Here are some basic colors:
- White masterbatch: Its ability significantly affects the final product in the way in which their durability, especially during weather conditions, is highly improved.
- Red masterbatch: It is made of red pigment, resin and suitable additives. It is used to create red color for end-products.
- Black masterbatch: This is a concentrated color granule, made of carbon black, primary resin, and appropriate additives.
- Green masterbatch: It is made of green pigment, resin and suitable additives. It is used to create green color for end-products
- Gray masterbatch: This color masterbatch adds vibrant gray color and advanced properties according to the additives to the initial raw material.
- Violet masterbatch: It offers excellent color dispersion. Besides, it has a molecular structure, which makes it more stable and heat resistant.
- Blue masterbatch: This masterbatch main usages are to create a blue color and enhance properties for the end products.
- Brown masterbatch: This color masterbatch is primarily used in the plastic industry to create brown color and improve the properties of plastic products.
- Orange masterbatch: It is highly compatible with various primary resins, providing a cost-effective solution to create orange color in various plastic products.
- Yellow masterbatch: It is commonly used in the production of packaging materials, automotive parts, and household appliances.
To receive useful advice and access high quality products, contact EuroPlas now!