Nylon is a remarkable material that finds application across various industries. It is cost-effective but also boasts a range of valuable properties, including softness, smoothness, and exceptional weather resistance. Because of these characteristics, nylon is widely used in various industries and sectors, from agriculture, industry, and transportation to construction. In this article, let's explore the importance of nylon material in the automotive industry!
1. Why Nylon Material Is Crucial In Automotive Applications?
1.1. Durability
Nylon material is highly valued in automotive applications due to its impressive strength-to-weight ratio. It is lightweight, which enhances fuel efficiency and overall vehicle performance. Despite its lightness, nylon offers remarkable tensile strength, making it ideal for parts that must withstand mechanical stress and wear. Components like engine covers, intake manifolds, and various under-the-hood parts are often made from nylon because they can endure harsh operating conditions without compromising structural integrity.
1.2. Heat Resistance
Automotive components are often exposed to high temperatures, especially those near the engine. Nylon material demonstrates excellent thermal stability, retaining its properties even when continuously exposed to high temperatures. This makes it suitable for engine-related components where heat resistance is critical to ensuring longevity and performance.
1.3. Chemical Resistance
In the automotive industry, materials are often exposed to various chemicals, including oils, fuels, and coolants. Nylon's chemical resistance is a significant advantage, as it can resist degradation when in contact with these substances. This property ensures that nylon components remain functional and reliable even in harsh chemical environments, reducing the risk of component failure and maintaining the safety and performance of the vehicle.
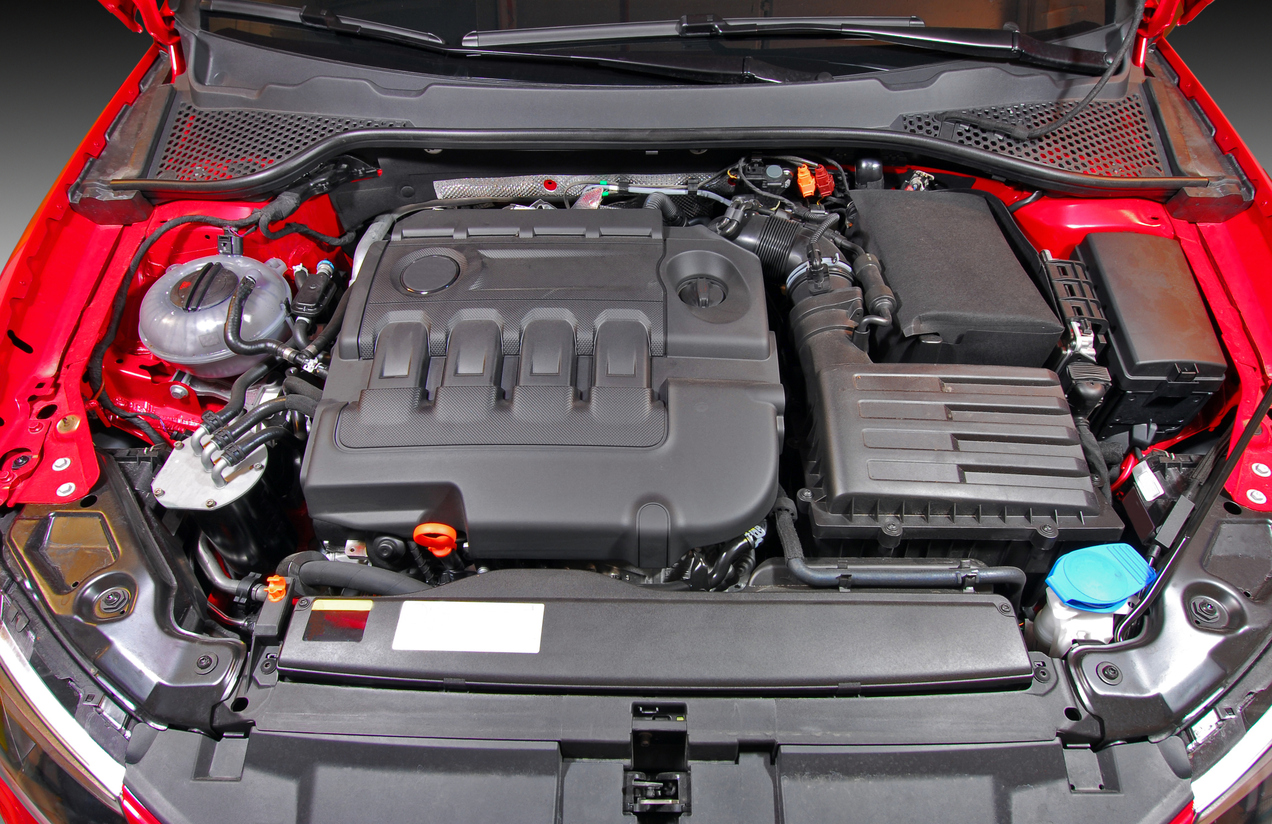
Plastic car parts made from nylon material
1.4. Flexibility and Impact Resistance
Nylon is a flexible material that effectively absorbs and distributes impact energy. This property is especially important for components that need to withstand sudden shocks or vibrations, such as those in suspension systems or impact-resistant panels. Nylon material can also flex without breaking, which helps protect vital vehicle systems and improve passenger safety.
1.5. Lightweight
Weight reduction is a critical factor in modern automotive design, as it directly impacts fuel efficiency and emissions. Nylon is a lightweight material, significantly lighter than metals traditionally used in automotive applications. This property makes it an attractive option for manufacturers looking to reduce the overall weight of vehicles without compromising on performance. By replacing heavier metal parts with nylon, manufacturers can achieve better fuel efficiency and lower emissions, contributing to more environmentally friendly vehicles.
Read more: 10 Unexpected Facts about Nylon
Read more: Nylon Melting Point: What Is Nylon's Temperature Ranges?
2. Common Applications Of Nylon Material In Automotive Industry
2.1. Application In Automotive Engine Peripheral Components
Since the peripheral parts of an engine primarily involve heat-generating and vibrating components, most of the materials used in these parts are glass fiber-reinforced nylon. This is because nylon offers superior comprehensive properties. The main characteristics of nylon have been modified with glass fibers and are greatly enhanced, such as strength, product precision, and dimensional stability. Additionally, nylon material comes in many varieties, is easier to recycle, and is relatively inexpensive. These factors make nylon an ideal material for engine peripheral components.
2.2. Application In Car Engine Parts
Engine covers, cylinder head covers, and other parts are often made from modified nylon. Compared to metal materials, using cylinder head covers reduces weight by 50% and cuts costs by 30%. Besides engine parts, other stress-bearing components of the car, like oil filters, wipers, and grilles, can also use reinforced nylon.
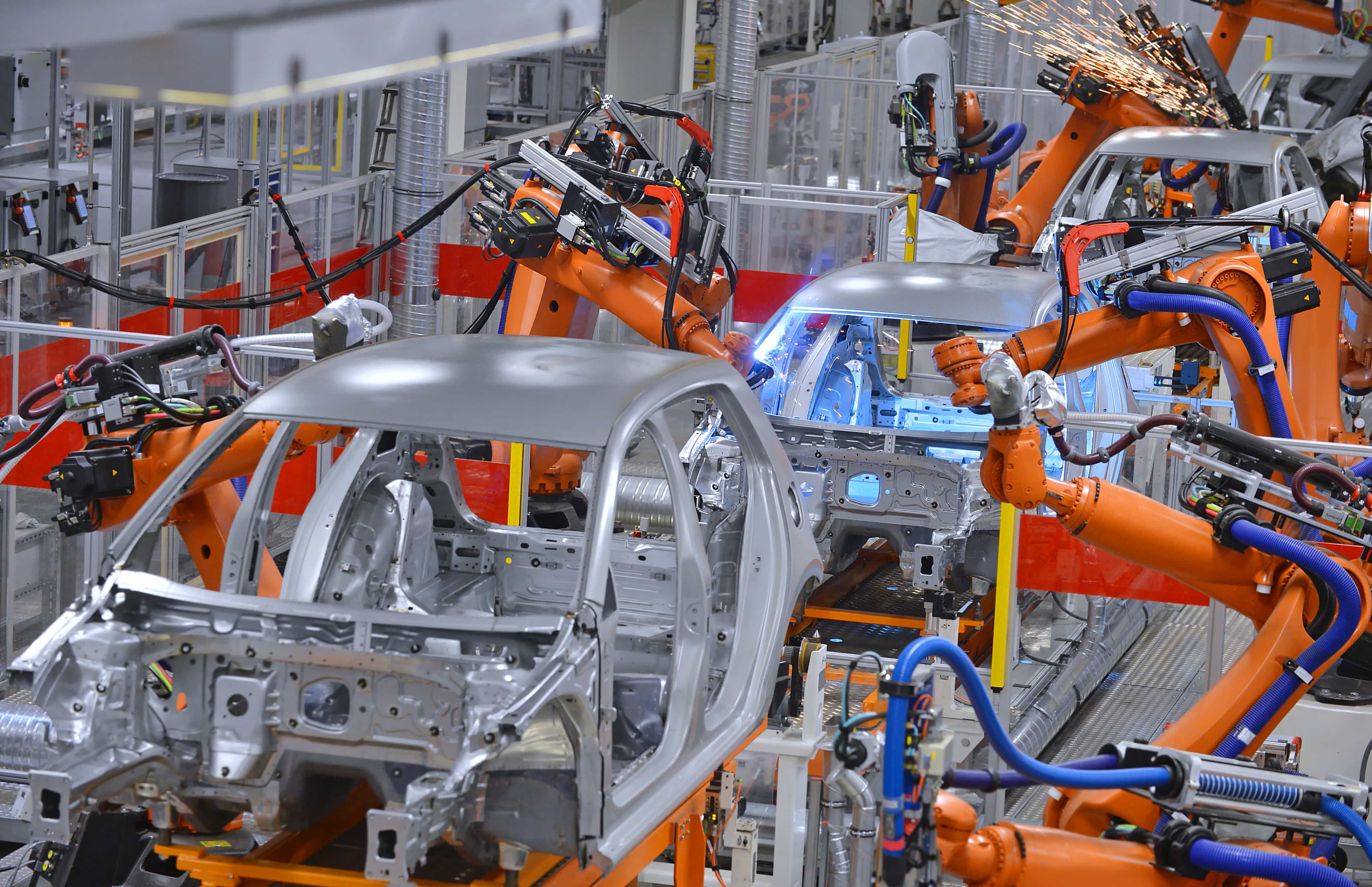
Engine covers made from nylon material
2.3. Application In Cooling System Components
Nylon material is also used in various components of the vehicle's cooling system, such as radiator end tanks, thermostat housings, and cooling fans. The material's resistance to heat and chemicals makes it ideal for parts that are constantly exposed to coolant fluids and high temperatures. Nylon components in the cooling system help ensure that the engine maintains an optimal operating temperature, preventing overheating and ensuring long-term engine performance.
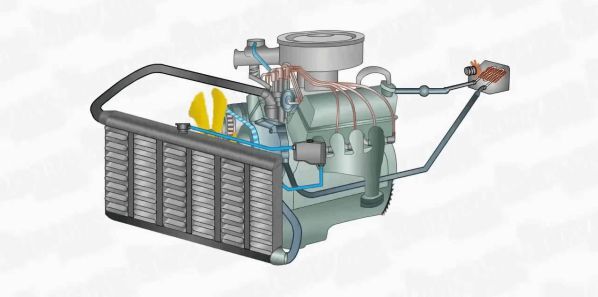
Some cooling system components in cars are made from nylon material
Read more: 3D Printing With Nylon: What You Need To Know
3. Advantages of Using Nylon Material in Automotive Manufacturing
Classified as one of the top 40 types of plastics, nylon material has now become widely used as a flexible plastic. In comparison to other heat-resistant plastics, it offers several outstanding advantages, including:
- Products made from PA plastic have high material hardness and durability. They can withstand strong impacts during use.
- Although it is a flexible plastic, the deformation temperature is quite high (from -40°C to 120°C), allowing it to be used in various fields. Additionally, products made from this type of plastic have good moisture resistance and low wear rates.
- PA plastic has a low friction coefficient, making it easy to dye and print information on the surface. It also has excellent durability in organic solvent environments.
- This material is highly regarded for its electrical insulation, noise reduction, and shock absorption properties when used in machinery components.
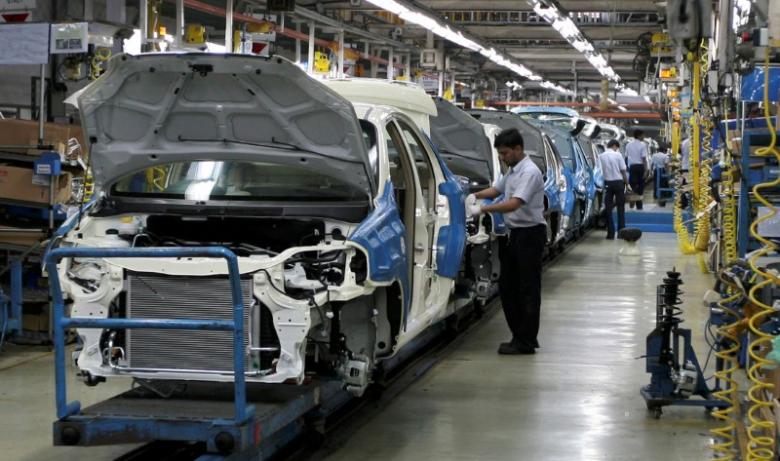
Using nylon material in automotive manufacturing
4. Conclusion
In short, nylon material offers several advantages that make it a valuable material in automotive manufacturing. Its durability, lightweight nature, and chemical and heat resistance all contribute to its widespread use in the industry. As automotive technology continues to advance, nylon's role is likely to expand, supporting innovations in vehicle design and performance.
5. About EuroPlas’ PA Products
Nylon material is one of EuroPlas' prides. Among the most notable are two types of engineering plastic compounds: PA6 and PA66. PA6 crystallizes at a high melting temperature, giving it excellent properties such as high surface hardness, good wear resistance, low friction coefficient, self-lubricating capability, and high noise reduction. PA66 has a lower water absorption rate than PA6 but offers higher heat resistance, hardness, and wear resistance.
PA6, PA66 blend compound
PA6, PA66 blend compound consists of PA6/PA66 resin, elastomers, and impact modifiers, giving it elasticity and strong mechanical properties. The most common applications of the PA6, PA66 blend compound are in the automotive a nd motorcycle industries. This material is often used in rolling bearings, gears in office equipment, carburetors, exhaust control valves, fuel tank caps, and other gear-related components.
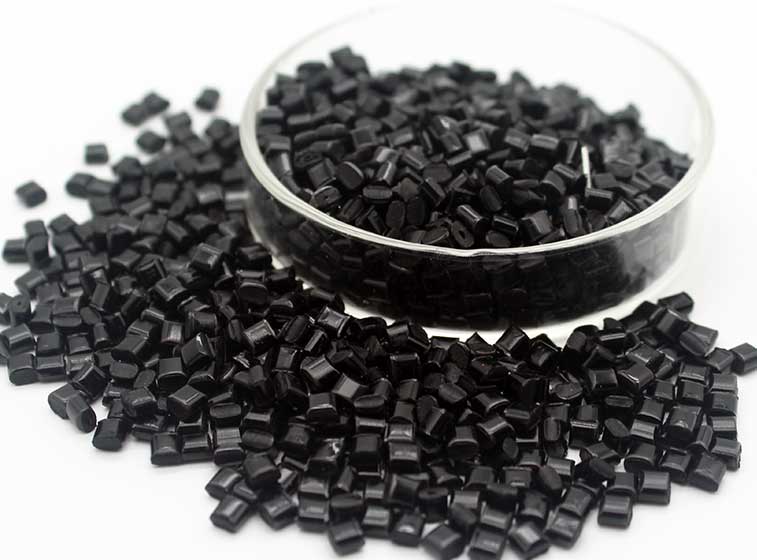
PA6, PA66 blend compound
PA66 & PA6 glass fiber compound
The PA66, PA6 glass fiber compound is a combination of PA resin and glass fiber reinforcement. It has high strength, abrasion resistance, chemical resistance, high heat deflection temperature, and excellent mechanical strength. The PA66, PA6 glass fiber compound from EuroPlas contains 30-50% glass fiber. It is widely used in the manufacturing of gears, bearings, drive belts, carburetor components, computer parts, and household electrical appliance components.
.jpg)
PA66 & PA6 glass fiber compound
With many years of experience in the industry, we are committed to providing the highest-quality PA products for customers. For more information and samples, please contact us HERE!
Read more: Suitable additives for nylon
Read more: Polyamide vs nylon: Are they the same? What are the differences?