Vertical injection molding is a method where plastic is injected into a mold from above, enabling easy part handling and minimizing material spillage. Before choosing a material for a vertical injection molding machine, manufacturers should consider various factors, such as plastic properties, material costs, and product requirements.
The article below will include a detailed selection guide. Follow along for more!
Read more:
Types Of Injection Molding Machines You Need To Know
7 Low Cost Plastics For Injection Molding
Different types of injection molding you need to know
1. Overall Of Vertical Injection Molding Machine
With the injection mechanism at the top, the vertical injection molding machine moves the mold halves vertically to open and close. When filling cavities, gravity and injection pressure are important factors that guarantee consistency and timing.
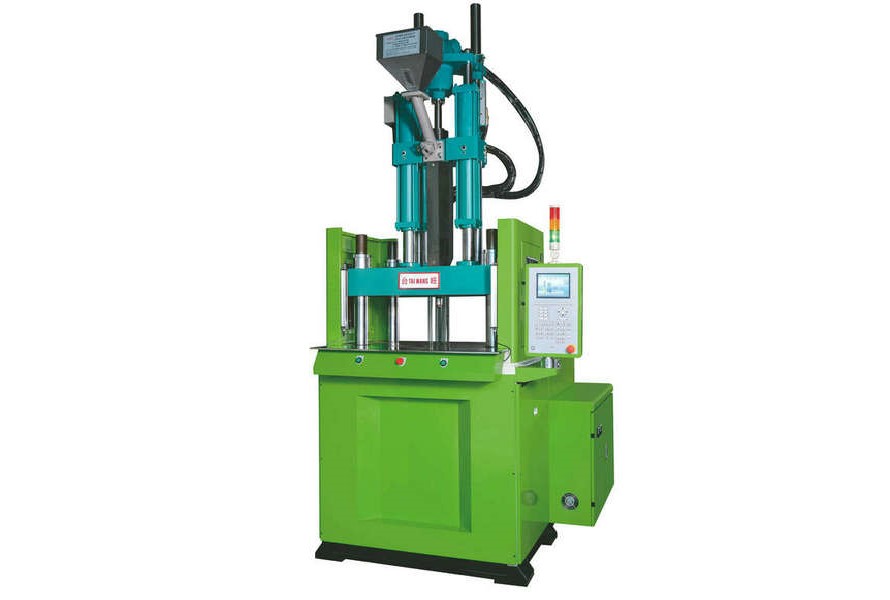
Multiple molds can be operated simultaneously using equipment featuring rotary tables and open clamps, which minimizes manual labor and intervention. Therefore, using a vertical injection molding machine can lead to higher productivity, lower costs, and better efficiency.
2. Criteria for Selecting Plastics for Vertical Injection Molding
Here are some criteria to look for when selecting a material suitable to use in a vertical injection molding machine.
2.1. Consider Material's Properties to Satisfy Product Functionality
The functioning of a product must satisfy the demands and aims of the user; therefore, choosing the right material is essential. Analyzing the product's use under varied conditions is required for this.
For instance, a food utensil needs to be made of a heat- and food-safe plastic like polypropylene, but a protective helmet needs to be made of a high-impact, impact-resistant substance like polycarbonate. Taking regulatory criteria into account also guarantees that the item satisfies all applicable requirements.
This alignment results in a successful injection molding project by optimizing the product's lifetime, safety, and performance.
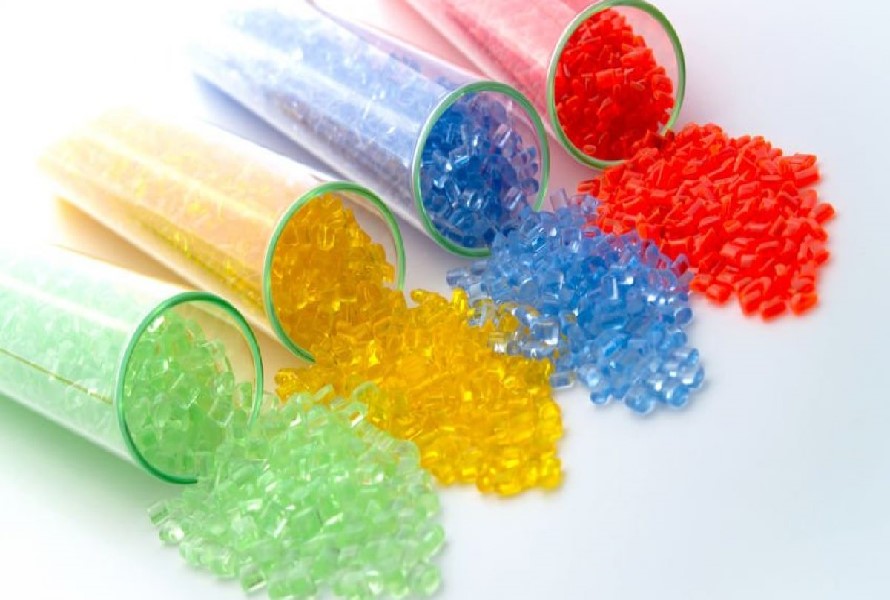
Thus, when choosing material for a vertical injection molding machine, manufacturers should consider the following:
- Thermal properties: For the material to survive injection molding and the conditions of its intended end-use, it must have the right thermal characteristics. For example, the product should have a high melting point and retain its strength and shape if it will be utilized in high temperatures.
- Chemical resistance: The material should be able to withstand any chemicals it may come into contact with during its intended usage, including corrosion and chemical degradation.
- Moldability: Plastics should be chosen for a vertical injection molding machine based on their filling qualities, flow characteristics, shrinkage rates, and moldability. Certain plastics may be more difficult to mold, which could increase production costs and decrease efficiency.
- Availability: Since a challenging or unpopular material could raise manufacturing costs and cause the project to be delayed, the material should be widely available and easily obtained.
2.2. Assess Material Costs
While choosing a material, manufacturers must take cost and technical characteristics into account. The cost of materials can vary, ranging from low-priced polymers like polyethylene to more expensive, specialized resins. It is important to realize that the least costly material could not end up being the most economical one over time.
A product may fail and incur additional expenditures if a material is not compatible with its durability and performance. However, a more costly material may compensate for its initial greater cost by providing better performance and durability.
2.3. Prioritize Aesthetics of the Products
The process of designing a product is intricate and requires careful consideration of both functionality and structural integrity. A product's visual appeal, which includes its color, texture, and gloss, is essential to its marketability.
Materials like polystyrene and acrylic provide easy color and treatment possibilities, while acrylic offers a high-gloss, transparent appearance. The ideal material for a vertical injection molding machine can be chosen by carefully weighing these variables, improving the product's attractiveness.
2.4. Consider the Environmental Impact of the Selected Material
When choosing material for a vertical injection molding machine, businesses should take into account its ecological impact over its whole life cycle, from extraction to disposal. While recyclable materials reduce waste and the demand for fresh raw materials, biodegradable polymers limit environmental harm.
Choosing materials with sustainability improves a business's standing for social responsibility. Environmental impact standards are becoming more stringent in many sectors. Therefore, selecting materials that can adapt to these changing needs is important.
3. Plastics Commonly Used in Vertical Injection Molding
These plastics can be suitable for a vertical injection molding machine:
- ABS: The plastic is tough, impact-chemical resistant, and cost-effective. It also features high dimensional stability and low shrinkage. Plus, its relatively low melting point makes it easy to process.
- PC (Polycarbonate): The material is strong and extremely impact-resistant. That's why it's suitable for applications requiring toughness and durability. Moreover, it can accept high cosmetic finishes well.
- PP (Polypropylene): PP is widely used in many applications due to its high melting point and excellent chemical resistance. It's the perfect material for parts that will be frequently used because it's lightweight and has good fatigue resistance.
- PA (Nylon, Polyamide): Nylon is well known for its strength, flexibility, and resilience to abrasion, heat, and chemicals. Because of its adaptability to many environments, nylon is used for various purposes.
- PE (Polyethylene): Because of its outstanding chemical and impact resistance, polyethylene is often used in applications where flexibility and moisture resistance are necessary.
4. Advantages of Using the Right Plastic in Vertical Injection Molding
When manufacturers know what materials are good for a vertical injection molding machine, they can gain lots of benefits, including:
- Product performance: Following the material selection guide guarantees that the finished product satisfies end-user needs and performs as intended. It's done by ensuring the material's strength, stiffness, and toughness meet design requirements.
- Production efficiency: Choosing the proper plastic means the injection molding process is appropriate for the material's flow characteristics, shrinkage rates, and filling qualities. Thus, factories can improve production efficiency and save time and money in the long run.
- Cost-effectiveness: The plastic material selection guide ensures the material is affordable and appropriate for the product design, lowering manufacturing costs and increasing the product's competitiveness in the market. It also ensures that the material is economical and within the project budget.
- Meeting standards: Choosing the right plastic for a vertical injection molding machine guarantees that the selected material satisfies all industry standards and regulations and the finished product is safe and appropriate for its intended use.
- Environmental impact: Manufacturers can lower the product's footprint, cut waste, preserve natural resources, and boost sustainability.
5. Conclusion
Choosing the material for a vertical injection molding machine includes consideration of its cost, chemical resistance, thermal stability, and intended mechanical qualities. Using the right plastic can help manufacturers reach the functional and aesthetic purposes of final products, save costs, and pursue sustainable development.
6. About EuroPlas
As the world's No. 1 filler masterbatch manufacturer, EuroPlas proudly brings customers tailor-made plastic material solutions to help them enhance their competitiveness. Our 7 factories all use advanced technology to ensure the highest quality products. Currently, we are strategic partners of thousands of factories in more than 95 countries worldwide.
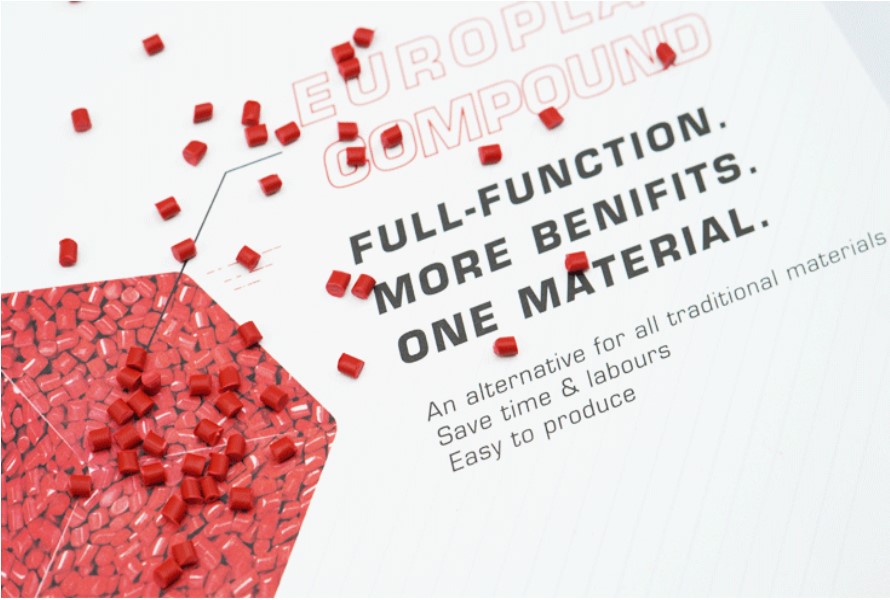
We offer a wide range of products, including engineering plastic compounds, plastic additives, color masterbatch, filler masterbatch, bioplastic compounds, and bio filler.
If you want to get further information, contact us right now!