Plastics, while incredibly useful, often face limitations in terms of their inherent properties. To overcome these challenges and expand their applications, manufacturers integrated additives into polymer formulations to improve their characteristics. These additives can enhance various plastic properties, such as heat resistance, impact strength, and UV stability. This exploration sheds light on the various types of additives and their specific impacts on the mechanical and thermal properties of plastic materials.
1. Types of Additives and Their Purposes
1.1. What Are Additives?
Additives are substances added to polymers to enhance their properties, making plastics more adaptable to diverse applications. From plasticizers that soften materials to stabilizers that protect against heat and UV light, these additives allow plastics to perform in various environments.
Each type of additive serves a specific function, contributing to the safety, durability, and cost-efficiency of plastic products.
For instance, additives make plastics used in vehicles, electronics, and medical devices resilient and long-lasting. Some additives are even essential for certain manufacturing processes, such as heat stabilizers that allow safe molding. Without these compounds, plastics would lack the versatility required for their many critical applications.
Additives thus make plastics adaptable, ensuring they meet the demanding standards of modern industries.
Read more: What are plastic additives? 8 most common plastic additives in plastic industry
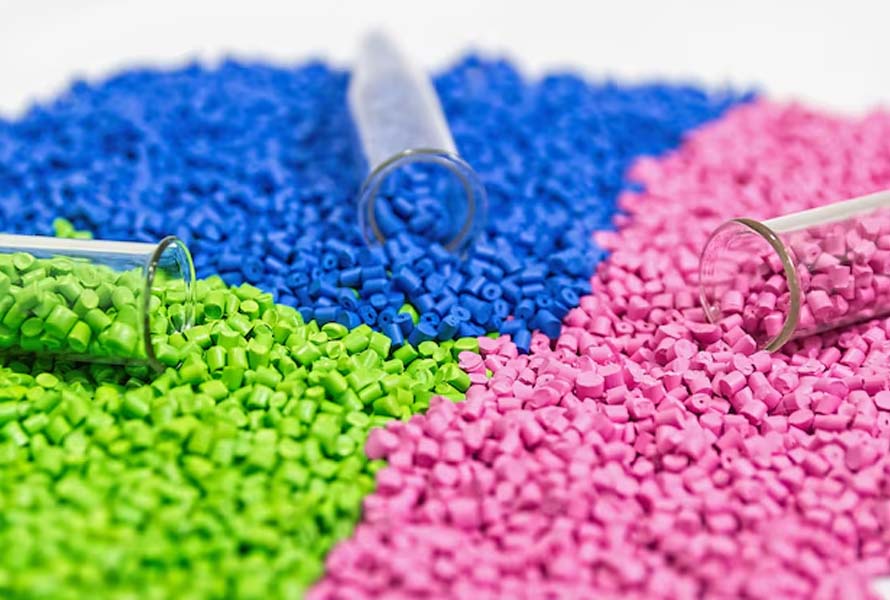
Additives are substances added to polymers to enhance their properties, making plastics more adaptable to diverse applications
1.2. The Main Types of Plastic Additives
Plastic additives come in various types, each designed to improve specific properties of plastic materials. Common types include:
These prevent film clumping by adding roughness to the surface, reducing vacuum effects that cause sticking. Commonly used in packaging, anti-stick agents ensure films remain separate without impacting quality or usability.
Used to improve clarity in films, especially with recycled content, they add gloss and reduce cloudiness without affecting adhesive or print properties, ideal for items like household plastics and packaging.
UV stabilizers protect plastics from sunlight-induced degradation by neutralizing free radicals, thus extending the product's life by preserving color, flexibility, and mechanical strength, commonly used in outdoor products.
Essential for fire safety in construction, electronics, and transportation plastics, they inhibit ignition and flame spread, aligning with regulatory standards.
Optical brightener additives mask plastic’s natural yellowness, creating a brighter appearance by enhancing blue light reflection. They also improve product gloss and smoothness to meet aesthetic standards.
These additives reduce static electricity in plastics, preventing dust accumulation and improving cleanliness and aesthetics, especially in items frequently handled or stored in dusty environments.
Odor-removing additives help reduce unpleasant odors in plastics, particularly in recycled materials. These additives don’t mask odors with fragrance but instead neutralize them, making them popular in items such as home appliances, toys, and packaging.
Added to inhibit bacterial growth, they prevent deterioration, discoloration, and odor, enhancing hygiene and maintaining the structural integrity of plastics used in healthcare and packaging.
These protect plastics from oxidation, which can cause cracks, discoloration, and brittleness, preserving mechanical properties under high heat or UV exposure, especially important in durable goods.
Moisture in polymer materials, especially technical resins, can lead to surface defects like fisheye in final products. Desiccant additives with Calcium Oxide absorb moisture, preventing issues in processes like extrusion and injection molding and improving end-product quality.
Anti-fog additives reduce water condensation on plastic film surfaces by lowering surface tension, which is crucial for applications like greenhouse films and food packaging. This prevents fog formation, keeps films transparent, and promotes effective light transmission, benefiting plant growth and product visibility.
Processing aids reduce friction between plastic and manufacturing equipment, enabling smoother production and enhancing final product quality. Used in processes like blown film and injection molding, these additives improve melt flow, reduce machine wear, and create glossy, transparent surfaces.
Used to make plastics softer and more flexible, these additives enhance degradability, supporting the production of environmentally friendly materials.
Applied to prevent mold damage during processing, these additives reduce friction and facilitate smoother processing, ensuring product consistency and quality.
These agents reduce warping and improve shape stability, particularly in polypropylene products, by accelerating cooling and increasing rigidity, allowing for faster production and enhanced structural integrity.
These create foam by forming gas bubbles within plastics, reducing material density and making products like insulation and cushioning more lightweight and shock-absorbent.
Added to absorb shock and prevent cracking, impact modifiers increase durability, especially in materials like PVC and polystyrene, ideal for high-stress applications.
- Anti-counterfeit Additives
These use optical brighteners and other technologies to authenticate products, making it easier to distinguish genuine items from counterfeits through distinct markings or characteristics.
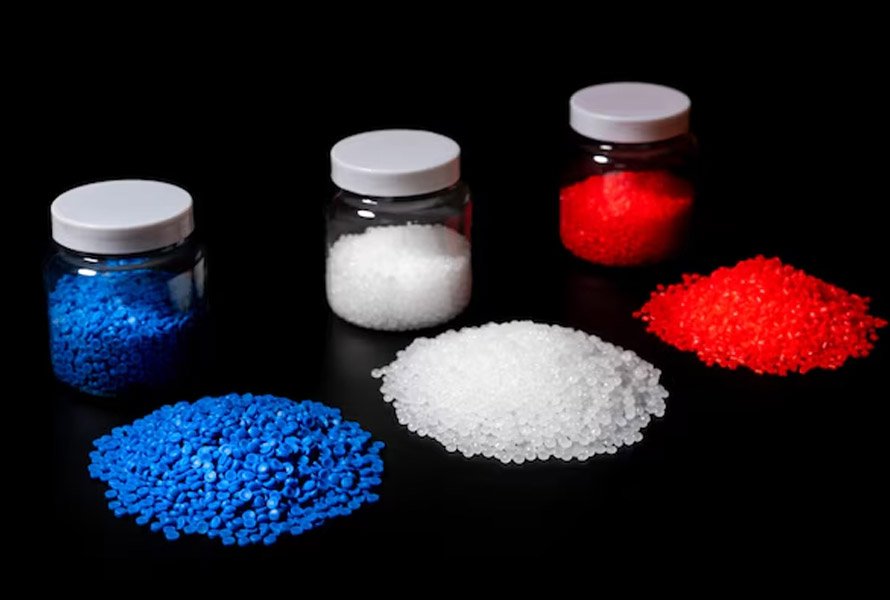
Plastic additives come in various types, each designed to improve specific properties of plastic materials.
1.3. Main Applications of Plastic Additives
Used to improve the performance of plastics, additives extend product life and increase functionality. Key sectors that benefit from plastic additives include:
Additives improve heat resistance, impact strength, and UV stability in car parts, such as dashboards, bumpers, and interiors, making them durable and safer.
Flame retardants and UV stabilizers are used in building materials like roofing, pipes, and insulation to enhance fire safety, durability, and weather resistance.
Conductive and flame-retardant additives ensure safety and functionality in electronic casings, circuit components, and electrostatic protection materials.
UV stabilizers and antioxidants in food packaging protect against UV rays and oxidation, preserving product freshness and extending shelf life.
Antimicrobial and stabilizing additives ensure the longevity and safety of medical plastics used in devices, tubes, and containers.
Plasticizers and colorants give flexibility and vibrant colors to synthetic fibers, enhancing comfort and appearance in clothing and upholstery.
- Outdoor and Recreational Goods
UV stabilizers and impact modifiers extend the life of products like furniture, playground equipment, and sports gear under sun exposure and rough use.
Wear-resistant and lubricating additives reduce friction and wear in machinery parts, such as gears, bearings, and conveyor belts, improving efficiency and longevity.
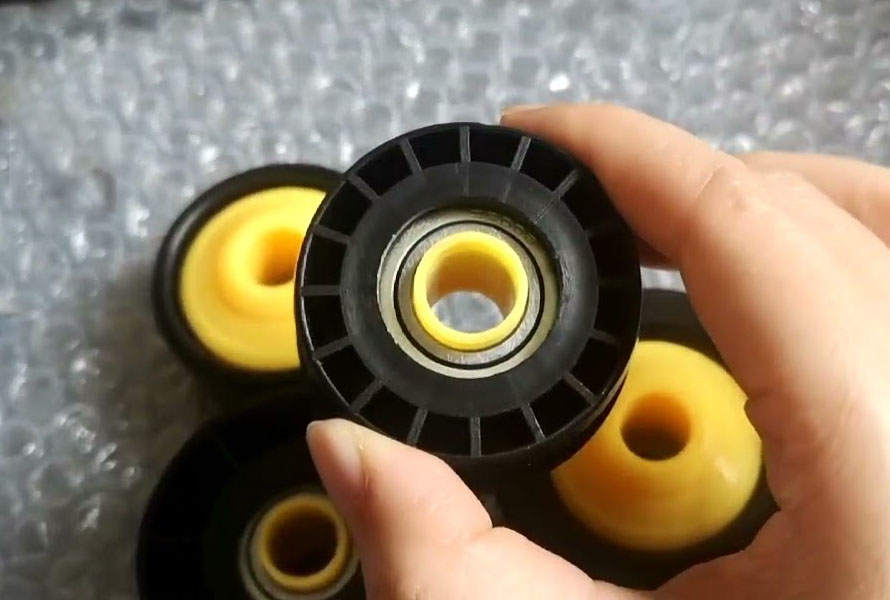
Plastic additives modify and strengthen plastics, enabling them to meet specific industries’ requirements.
2. Impact of Additives to Plastic Properties
The addition of specific additives can significantly improve plastic properties. These modifications allow plastics to perform better under different demanding environments.
2.1. Boosting Strength and Rigidity
Plastic additives play a key role in strengthening plastic materials. Reinforcing agents, such as glass fibers and carbon nanotubes, increase tensile strength and impact resistance. Furthermore, impact modifiers improve toughness and durability, making plastic products more resilient.
2.2. Additives Simplify Plastic Processing
Shaping plastic products involves carefully controlling molecular structure to prevent issues like discoloration, sticking to molds, or defects in the final product. Additives are crucial in tackling these challenges, making plastic processing manageable.
From bottles and bags to window frames and electronics, different plastic products require various shaping methods. Usually, polymer granules are melted and molded through techniques such as extrusion, injection, or blowing. Additives called process aids help improve flow and color mixing, while lubricants reduce viscosity, allowing intricate shapes and lower processing temperatures. Antioxidants, such as heat stabilizers protect plastics from heat-induced damage and decomposition.
2.3. Additives Enhance the Appearance of Plastics
What draws us to plastic objects? It could be their shape, utility, or color. Plastic coloring typically uses two methods: surface painting/printing post-molding or the addition of pigments during molding. When pigments are incorporated directly, colors become part of the plastic itself, ensuring they don’t fade or wear off, which provides designers with great creative flexibility.
Pigments, tiny particles that blend into molten polymers, allow plastics to match other materials like wood or metal for seamless design. These additives also give designers a wide color spectrum, serving functional roles like blocking light in medicine bottles, signaling danger, or providing opacity in items like dashboards and pipes. Pigments such as carbon black and titanium dioxide create solid, vivid colors; carbon black absorbs light, while titanium dioxide scatters it, producing a high-brightness white, often used in pastel shades when combined with other pigments.
2.4. Additives Enhance Safety in Plastics
Effective plastic design merges the safety of unbreakable materials with purposeful product features like rounded edges, child-resistant closures, and tamper-evident seals. Additives can further boost these safety aspects.
Most plastics, like natural polymers such as wood or cotton, are organic and can catch fire. This is a major risk in certain applications, such as building materials that legally must resist ignition and flame spread. Flame-retardant additives meet this need, as seen in PVC conveyor belts in coal mines, which reduced fires and saved lives.
Additives also improve the safety of plastic components in cars, where impact modifiers in dashboards and bumpers help absorb force during collisions.
2.5. Enhancing Flexibility
Plasticizers, a type of additive, enhance the flexibility of plastics by weakening the forces between polymer chains. This increased flexibility makes plastics suitable for a wider range of applications, including vinyl flooring, flexible pipes, and electrical cables.
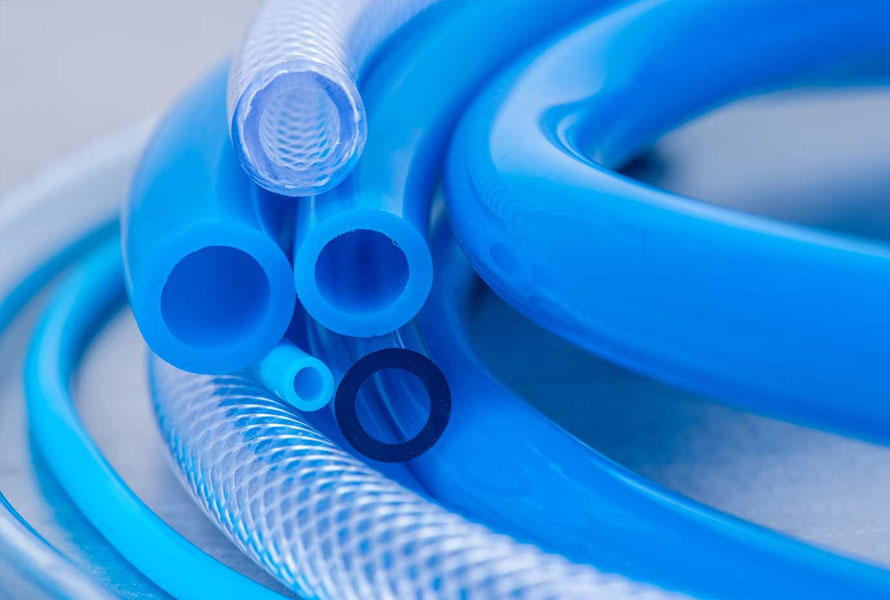
By softening polymer chains, plasticizers make plastics suitable for diverse applications
2.6. Improving Thermal Stability
Heat stabilizers are additives that protect plastics from high-temperature degradation, which can lead to discoloration, weakening, or melting. These additives ensure plastic’s longevity and performance, especially in applications like automotive components and electrical enclosures.
2.7. Enhanced Flame Resistance Ability
Flame retardants enhance the fire resistance of plastics, making them safer for various applications, including construction, electronics, and transportation. They work by inhibiting the combustion process, reducing the spread of flames and minimizing smoke generation.
2.8. Altering Surface Characteristics
Plastic additives can enhance the surface properties of plastics, improving their adhesion, hydrophobicity, or scratch resistance. This makes them suitable for a wide range of applications, from automotive parts to medical devices.
2.9. Decreasing Friction and Wear
To reduce friction and wear in plastic components, lubricants and wear-resistant additives are applied. These additives form a lubricating barrier between surfaces in contact, lowering friction and increasing the durability of plastics, especially in moving parts like gears, conveyor systems, and bearings.
2.10. Increasing Electrical Conduction Capability
Conductive plastic additives, like carbon black or metal particles, give plastics the ability to conduct electricity. This modification enables plastics to be applied in areas needing electrical conductivity, such as electronic parts, circuit boards, and protection against electrostatic discharge.
3. Innovations in Additives
Recent innovations in additives are transforming the capabilities of plastic materials. These breakthroughs aim to enhance performance while addressing environmental challenges.
3.1. Integrated Nanotechnology
The field of additive manufacturing has entered a new phase with the application of nanotechnology. Nano-additives, which have particle sizes smaller than 100 nanometers, enhance performance traits like strength, conductivity, and thermal stability. For example, incorporating nanoclay into plastics produces materials with better mechanical strength and barrier properties.
3.2. Smart Additives for Adaptive Materials
The introduction of smart additives has led to the creation of materials that react to external stimuli. These include additives that adjust to temperature, light, or pressure changes, resulting in applications ranging from self-healing materials to adaptive packaging solutions.
3.3. Biodegradable Additives Solutions
With increasing awareness of environmental issues, biodegradable additives have gained significance. These additives promote the breakdown of materials, addressing plastic pollution concerns. Polymers enriched with biodegradable additives decompose more effectively in natural settings, providing sustainable alternatives for multiple industries.
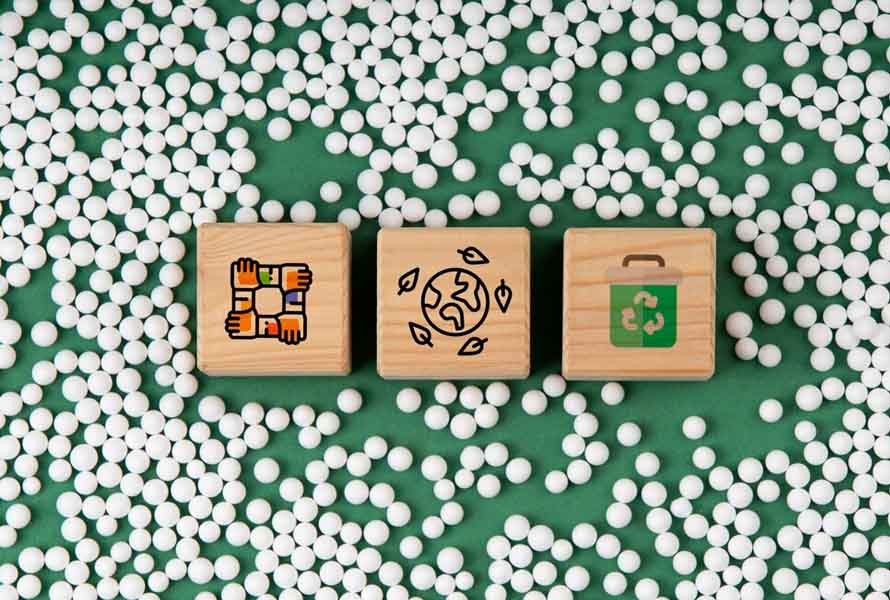
Incorporating specific additives can greatly enhance the properties of plastics
4. Conclusion
In summary, additives play a pivotal role in enhancing the properties of plastics, significantly influencing their performance and applications. By improving characteristics such as strength, flexibility, and resistance to environmental factors, additives enable the creation of materials suited for diverse industries, from automotive to electronics. Additionally, the ongoing innovations in additive technologies, including biodegradable and smart additives, point toward a more sustainable future for plastic materials. Understanding the impact of these additives is essential for manufacturers and consumers alike, as it shapes the way we approach plastic production and usage in an increasingly eco-conscious world.
5. About EuroPlas’ Additives
EuroPlas is a leading company in the production of high-quality plastic additives that enhance the performance and sustainability of plastic materials. With a commitment to innovation and excellence, EuroPlas offers a diverse range of products designed to meet the needs of various industries, including packaging, construction, automotive, and consumer goods. Their portfolio includes specialized additives like anti-blocking additives, flame retardant, anti-UV additives and other performance-enhancing agents that improve the mechanical, thermal, and aesthetic properties of plastics.
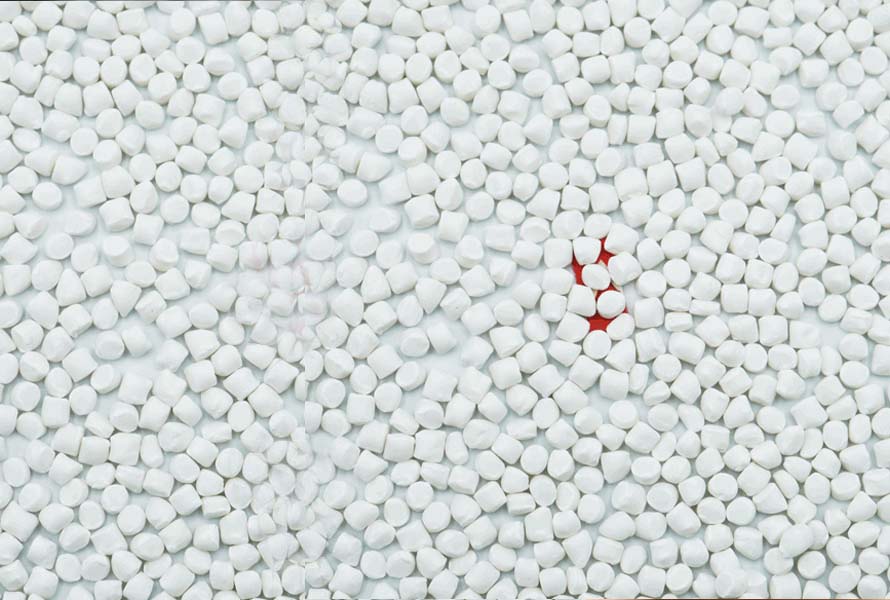
EuroPlas is a leading company in the production of high-quality plastic additives
By prioritizing research and development, EuroPlas stays at the forefront of industry trends and technological advancements, ensuring their additives are effective and compliant with international standards. Through their commitment to quality and sustainability, EuroPlas is not only enhancing the properties of plastics but also paving the way for a more sustainable future in plastic production and usage.
For more information about our products and how they can benefit your business, contact us today!